MFY’s Pipe Manufacturing Process: Quality from Raw Material to Shipment
Are you tired of inconsistent stainless steel pipe quality jeopardizing your projects and reputation? It's frustrating when material defects cause unexpected failures or delays. At MFY, we understand these challenges, which is why our meticulous manufacturing process ensures quality from the very first step to final shipment.
MFY’s pipe manufacturing process is a comprehensive system designed to deliver superior quality. It encompasses stringent raw material selection, precise manufacturing steps including forming and welding, multi-stage quality control checks, protective packaging, and efficient logistics management, all ensuring products meet the highest standards upon delivery.
As the Global Business Director at MFY, I've seen firsthand how a commitment to excellence at every stage translates into tangible benefits for our clients. We don't just sell pipes; we provide a promise of reliability and performance. This deep dive will illuminate how our integrated approach, from sourcing pristine raw materials to ensuring your order arrives safely and on time, truly sets us apart.
The stainless steel pipe industry is often perceived as a straightforward commodity market, but the reality is far more nuanced. While many suppliers might focus solely on price or basic specifications, a truly reliable partner understands that consistent quality and dependable delivery1 are paramount for complex projects and long-term success. At MFY, our diversified group structure, integrating everything from raw material trading to advanced digital innovation in our processes, allows us a unique vantage point. We're not just assembling components; we're orchestrating a symphony of precision, backed by decades of expertise and a relentless drive for improvement. This holistic view enables us to anticipate challenges, innovate proactively, and ultimately, deliver value that goes far beyond the physical product.
How does MFY select high-quality raw materials for pipe manufacturing?
Sourcing subpar raw materials can lead to catastrophic failures in final applications, causing costly rework and damaging your credibility. Imagine the frustration of discovering defects only after installation. MFY mitigates this risk by implementing an exceptionally rigorous selection process for all stainless steel coils and plates2.
MFY ensures high-quality raw materials by partnering with reputable, certified mills, conducting thorough chemical composition and mechanical property testing upon arrival, and maintaining strict traceability. This multi-faceted approach guarantees that only materials meeting our exacting standards enter the production line, forming the foundation for superior pipes.
The old adage "garbage in, garbage out" is particularly true in stainless steel manufacturing. As Global Business Director, I've seen projects falter due to poor material choices made upstream. At MFY, our deep roots in stainless steel raw material trading give us a distinct advantage. We don't just buy what's available; we strategically source from a network of trusted suppliers we've cultivated over years. This isn't just about getting a good price; it's about ensuring consistency, understanding the metallurgical properties3, and securing supply chains that are resilient. We often work with clients, like a large manufacturing firm in India, who previously faced issues with inconsistent material grades from other suppliers. By switching to MFY, they gained access to materials with verified pedigrees, directly impacting their product's lifespan and performance. Our initial assessment of raw materials goes beyond simple certifications; we conduct our own verification tests because we know that the integrity of the final pipe begins here. This commitment to foundational quality is non-negotiable for us and a cornerstone of the trust our clients place in MFY.
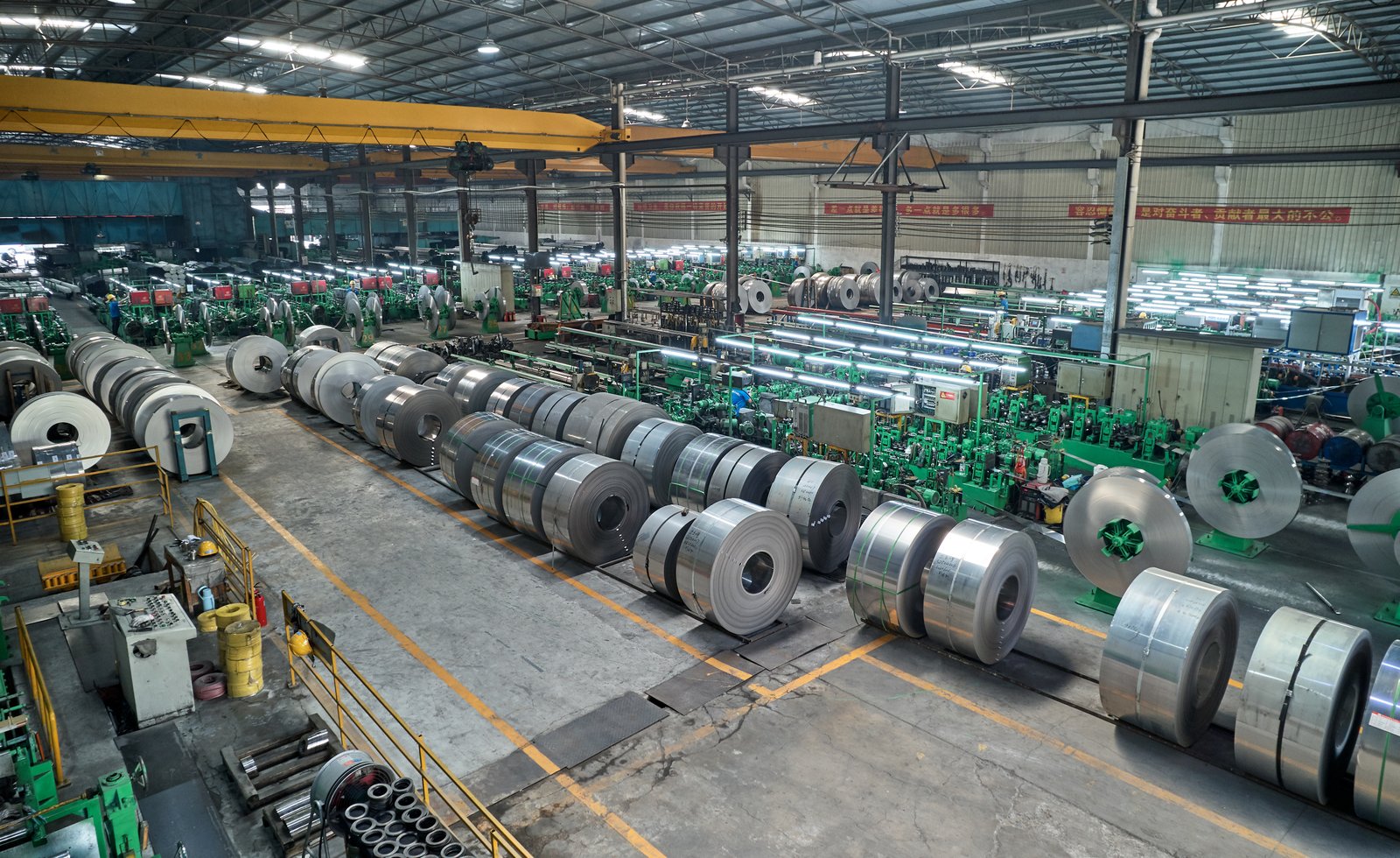
Our approach to raw material selection is not just a procedural step; it's a core philosophy embedded in MFY's operational DNA. We understand that the characteristics of the raw material directly influence every subsequent manufacturing stage and, ultimately, the performance and longevity of the finished stainless steel pipes. This understanding drives our meticulous processes, ensuring that we lay the strongest possible foundation for the products that our clients rely on for critical applications. From construction projects in bustling Southeast Asian cities to demanding industrial applications in the Middle East, the quality of the initial steel coil is paramount.
The Foundation: Establishing Rigorous Supplier Qualification Protocols
The first line of defense in ensuring raw material quality is a robust supplier qualification process. At MFY, we don't simply look for the lowest-cost provider. Instead, we engage in a multi-stage vetting process that assesses potential suppliers on a range of criteria, including their production capabilities, quality management systems (like ISO 9001 certification), historical performance, and ethical sourcing practices. I recall a specific instance where a prominent engineering contractor in India, one of our target clients, was facing premature corrosion issues in pipes sourced from a previous local supplier. The root cause was traced back to inconsistent alloying elements in the raw material. When they approached MFY, we were able to demonstrate our stringent supplier audits and material traceability, giving them the confidence that such issues would be a thing of the past. Our internal metrics for supplier approval are demanding, often exceeding general industry standards. For example, we might require a supplier to demonstrate a defect rate below a certain threshold for a consistent period before they are added to our approved vendor list. Industry reports consistently highlight that material failure, often originating from substandard raw materials, accounts for a significant percentage of project cost overruns and failures. A study by a leading metallurgical institute indicated that up to 40% of failures in certain industrial applications could be traced back to material defects or incorrect material selection. MFY’s proactive stance on supplier qualification directly mitigates these risks for our clients.
Beyond Certifications: Comprehensive Material Testing and Analysis
While mill test certificates (MTCs) provide a baseline of information, we at MFY believe in a "trust but verify" approach. Upon arrival at our facilities, raw materials undergo a battery of tests to confirm their compliance with required specifications and our internal quality benchmarks. This includes spectral analysis using advanced PMI (Positive Material Identification) guns to verify the chemical composition and ensure the correct grade of stainless steel. We also perform mechanical tests, such as tensile, hardness, and sometimes impact tests, depending on the intended application of the pipes. For instance, for a client in Southeast Asia's burgeoning oil and gas sector, who required pipes for a high-pressure, corrosive environment, we didn't just rely on the MTC. We conducted additional Charpy impact tests at specific temperatures and more detailed microstructural analysis to ensure the material's suitability. Many competitors might solely rely on the supplier's MTC, which, while generally reliable from reputable mills, doesn't preclude the rare possibility of errors or variations. Our in-house testing, often supplemented by third-party laboratory verification for particularly critical orders, provides an added layer of assurance. This was crucial for an equipment integrator client who needed absolute certainty about the material properties for components going into medical devices.
Strategic Sourcing and Long-Term Partnerships
MFY’s position as a diversified group company, with a significant arm in stainless steel raw material trading, provides us with unparalleled advantages in strategic sourcing. We aren't just buying coils for our pipe production; we are active participants in the raw material market. This allows us to secure prime materials, often directly from top-tier mills, and maintain a more stable and predictable supply. Building long-term partnerships with these mills means we often get priority access and better consistency. I remember a situation where a global shortage of a specific nickel alloy was impacting the market. Because of our established relationships and purchasing volume, MFY was able to secure the necessary raw materials for a large distributor client in Russia, who was struggling to find supply elsewhere for their committed orders. This stability is critical for our clients who rely on us for consistent, on-time delivery. Data on supply chain resilience consistently shows that companies with diversified and strong supplier relationships weather market volatility much better. MFY also conducts continuous supplier performance reviews, tracking metrics like on-time delivery, material conformity, and responsiveness, ensuring our partners consistently meet our high standards. This dynamic evaluation process ensures that our raw material sourcing remains robust and reliable.
Common Raw Material Defect | MFY's Prevention/Detection Method | Impact if Undetected |
---|---|---|
Incorrect Chemical Composition | PMI Spectral Analysis, Independent Lab Verification | Reduced corrosion resistance, poor weldability |
Surface Imperfections (cracks, pits) | Visual Inspection, Incoming Material Surface Quality Checks | Potential leak paths, stress concentrators |
Lamination or Inclusions | Ultrasonic Testing (on select critical materials), Microscopic Exam | Reduced strength, delamination |
Incorrect Mechanical Properties | Tensile, Hardness, Impact Testing | Unexpected failure under load |
Dimensional Inaccuracies (thickness) | Micrometer checks, Gauge measurements | Issues in forming, inconsistent wall thickness |
MFY conducts independent material testingTrue
MFY performs its own verification tests beyond mill certificates, including spectral analysis and mechanical testing.
Supplier price is MFY's primary selection criterionFalse
MFY evaluates suppliers on multiple criteria including quality systems and ethical practices, not just cost.
What are the key steps in MFY's pipe manufacturing process?
Navigating a complex manufacturing process without clarity can be daunting, leading to uncertainty about quality and consistency. You might worry if every crucial step is handled with the necessary precision. MFY addresses this by employing a clearly defined, optimized, and transparent pipe manufacturing sequence.
MFY's key pipe manufacturing steps include: precision slitting of stainless steel coils, meticulous forming and shaping, advanced welding (TIG, Laser, or Plasma), accurate sizing and straightening, controlled heat treatment (annealing), thorough cleaning and pickling, and precise cutting to length, followed by various finishing options.
As someone who has walked our production floors countless times, I can attest to the intricate dance of machinery and human expertise at MFY. Each step in our pipe manufacturing process is not an isolated task but part of an integrated system designed for excellence. Our R&D team works closely with production to continuously refine these processes, leveraging our capabilities in both cold-rolled processing and specialized tube manufacturing. For example, a client, a leading equipment integrator, required pipes with exceptionally tight tolerances for a new product line. Our engineers were able to fine-tune the forming and sizing stages, drawing on data from our digital innovation initiatives, to meet their exact specifications. This seamless integration ensures that from the moment a coil enters our line to when a finished pipe is ready for inspection, every action is deliberate and contributes to the final quality. We understand that our clients, whether they are large manufacturing companies or specialized engineering contractors, depend on this precision for their own operations.
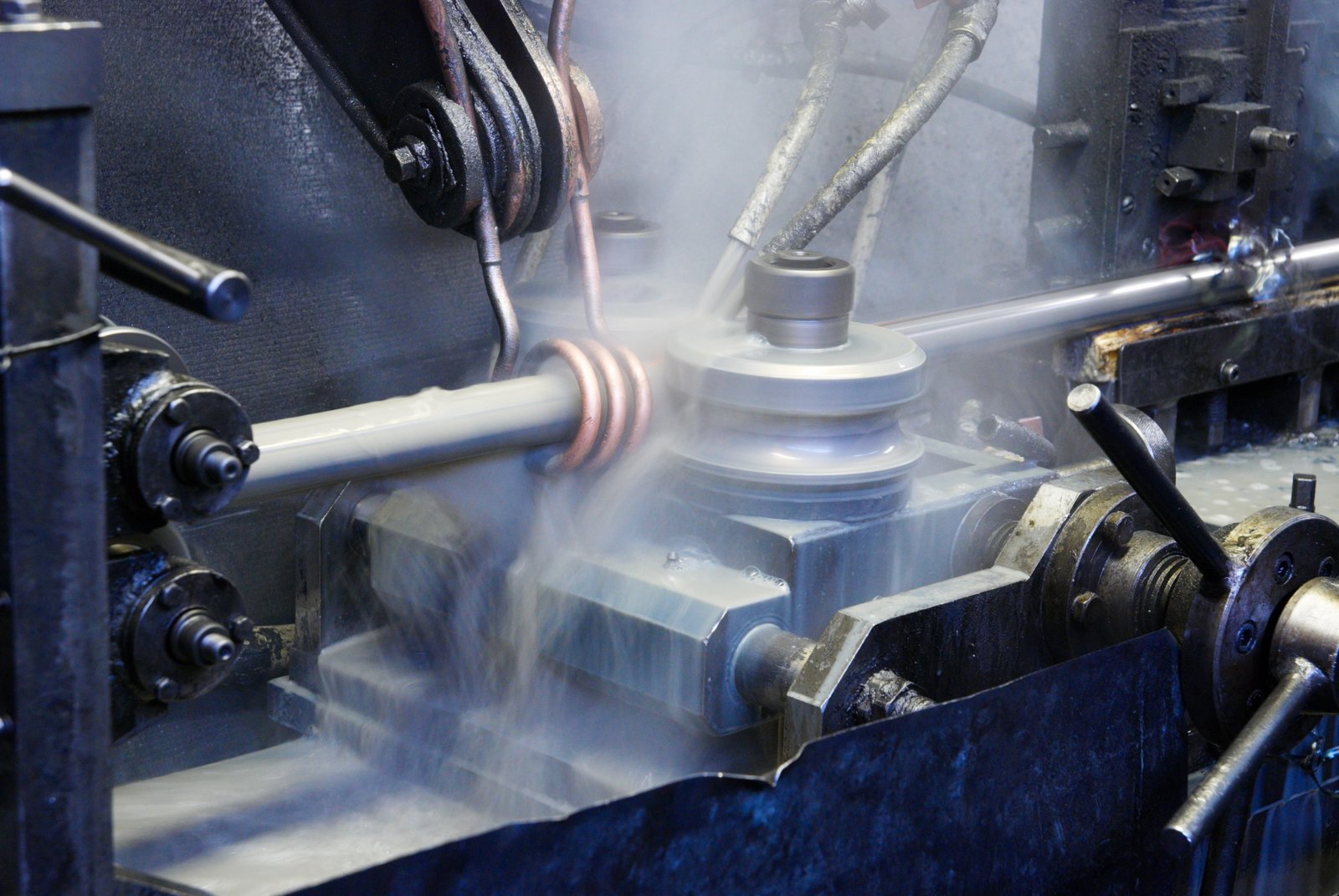
The journey of transforming a raw stainless steel coil into a high-performance pipe is a testament to engineering precision and meticulous control. At MFY, we view each step not just as a mechanical operation but as an opportunity to embed quality. Our state-of-the-art facilities and skilled workforce are aligned to execute these steps flawlessly, ensuring that the final product not only meets but often exceeds the demanding requirements of our clients across diverse industries and export markets like India, Southeast Asia, and the Middle East.
Precision Slitting and Edge Preparation: The Unseen Hero
The very first manufacturing step after raw material approval is often overlooked in its importance: precision slitting and edge preparation4. The stainless steel master coils are slit into narrower strips corresponding to the circumference of the pipe to be produced. The accuracy of this slitting process is paramount; any variation in width can lead to inconsistencies in pipe diameter and difficulties in the subsequent welding process. Furthermore, the quality of the slit edge – ensuring it is clean, burr-free, and properly conditioned – directly impacts weld integrity. At MFY, we utilize advanced slitting lines with high-precision rotary shear blades and sophisticated control systems to maintain tight width tolerances, often tighter than industry standards. I recall visiting a manufacturing company, one of our key clients, who previously sourced pipes from another supplier and consistently struggled with inconsistent outside diameters. This was causing significant downtime on their automated assembly lines. After switching to MFY pipes, they reported a marked improvement in their production efficiency, directly attributable to the dimensional consistency originating from our precision slitting. Industry standards like ASTM A554 or A269 specify dimensional tolerances, but our internal targets for slit width can be as tight as ±0.05mm for certain applications, ensuring a better fit-up for welding.
Forming, Welding, and Sizing: Engineering Meets Artistry
Once the steel strips are prepared, they enter the forming section of the pipe mill. Here, a series of rollers gradually shape the flat strip into a cylindrical tube. This is a critical stage where improper forming can induce stresses or result in an out-of-round shape. Following forming, the edges of the tube are brought together and welded. MFY employs various advanced welding technologies, including Tungsten Inert Gas (TIG) welding5 for superior weld quality and aesthetics, Plasma welding for thicker walls, and sometimes Laser welding for specific applications requiring minimal heat input. For instance, for a high-pressure application requested by an engineering contractor in the Middle East, destined for a desalination plant, we utilized a specialized multi-torch TIG welding process combined with inline non-destructive testing (NDT) like eddy current testing immediately post-weld to ensure absolute seam integrity. After welding, the pipe undergoes sizing and straightening operations to achieve the final precise diameter, roundness, and straightness. Data on weld failure rates in the industry can vary, but MFY’s internal target for first-pass yield in welding is consistently above 99%, a testament to our skilled operators, well-maintained equipment, and stringent process controls. The role of skilled welders and machine operators here cannot be overstated; it's where engineering design meets practical execution.
Heat Treatment and Finishing: Optimizing Properties and Appearance
For many stainless steel grades, particularly austenitic types like 304 or 316, heat treatment (typically bright annealing or open annealing followed by pickling) is a crucial step after welding and sizing. Annealing recrystallizes the grain structure in the weld zone and heat-affected zone, relieving internal stresses induced during forming and welding, and restoring the material’s optimal corrosion resistance and mechanical properties. MFY utilizes controlled atmosphere furnaces for bright annealing, which results in a clean, bright surface finish, or open annealing followed by meticulous pickling and passivation to remove any surface scale and restore the chromium oxide passive layer. We also offer various finishing options, from standard mill finish to polished surfaces for aesthetic or hygienic applications. An equipment integrator client developing components for the food processing industry required pipes with a specific internal surface roughness (Ra value) to prevent bacterial adhesion and ensure easy cleaning. We achieved this through a specialized polishing process post-annealing. Research data from bodies like the Nickel Institute extensively documents the impact of proper annealing on the intergranular corrosion resistance of austenitic stainless steels; our processes are designed in strict accordance with these principles.
Welding Technique | MFY Application Context | Key Advantages for MFY Pipes | Typical Materials |
---|---|---|---|
TIG Welding | Standard for high-quality aesthetic & structural pipes | Excellent weld quality, good control, clean weld | Austenitic SS (304, 316) |
Laser Beam Welding | Thin-walled precision tubes, minimal heat distortion | High speed, low heat input, narrow weld bead | All SS grades |
Plasma Arc Welding | Thicker wall pipes, high-speed applications | Deeper penetration, higher welding speeds | Austenitic, Duplex SS |
ERW (HF Welding) | (Less common for MFY's typical high-spec SS pipes) | High production speed for certain grades | Carbon steel, some SS |
Precision slitting impacts weld qualityTrue
Accurate slitting ensures proper pipe diameter and clean edges for better welding integrity.
Annealing is only for appearanceFalse
Annealing restores material properties and corrosion resistance, not just surface finish.
How does MFY ensure quality control at each stage of production?
Receiving a batch of stainless steel pipes only to find defects can derail your project timelines and inflate costs significantly. This uncertainty is a major concern for any buyer. MFY alleviates this by embedding rigorous quality control checkpoints throughout the entire production lifecycle, not just at the end.
MFY ensures quality control by implementing in-process checks at every critical manufacturing stage, utilizing advanced non-destructive testing (NDT) methods, conducting meticulous dimensional and visual verifications, and performing comprehensive final inspections, all supported by a robust traceability system from raw material to dispatch.
Quality, in my experience as Global Business Director at MFY, is not an act, it's a habit – a culture that permeates our entire organization. It's not about a single inspector at the end of the line; it's about every operator, every supervisor, and every manager taking ownership of quality at their respective stages. This philosophy is fundamental to our operations. We integrate quality checks from the moment raw materials arrive until the pipes are packaged for shipment. For instance, a distributor in Russia, who handles large volumes for diverse applications, relies on our consistent quality to minimize their own inspection overhead and ensure customer satisfaction. Our continuous evolution in QC practices6, driven by our digital innovation and feedback from clients and our internal teams, means we are always seeking ways to improve, to catch potential issues earlier, and to refine our processes for even greater reliability. This proactive and embedded approach to quality is what gives our clients peace of mind.
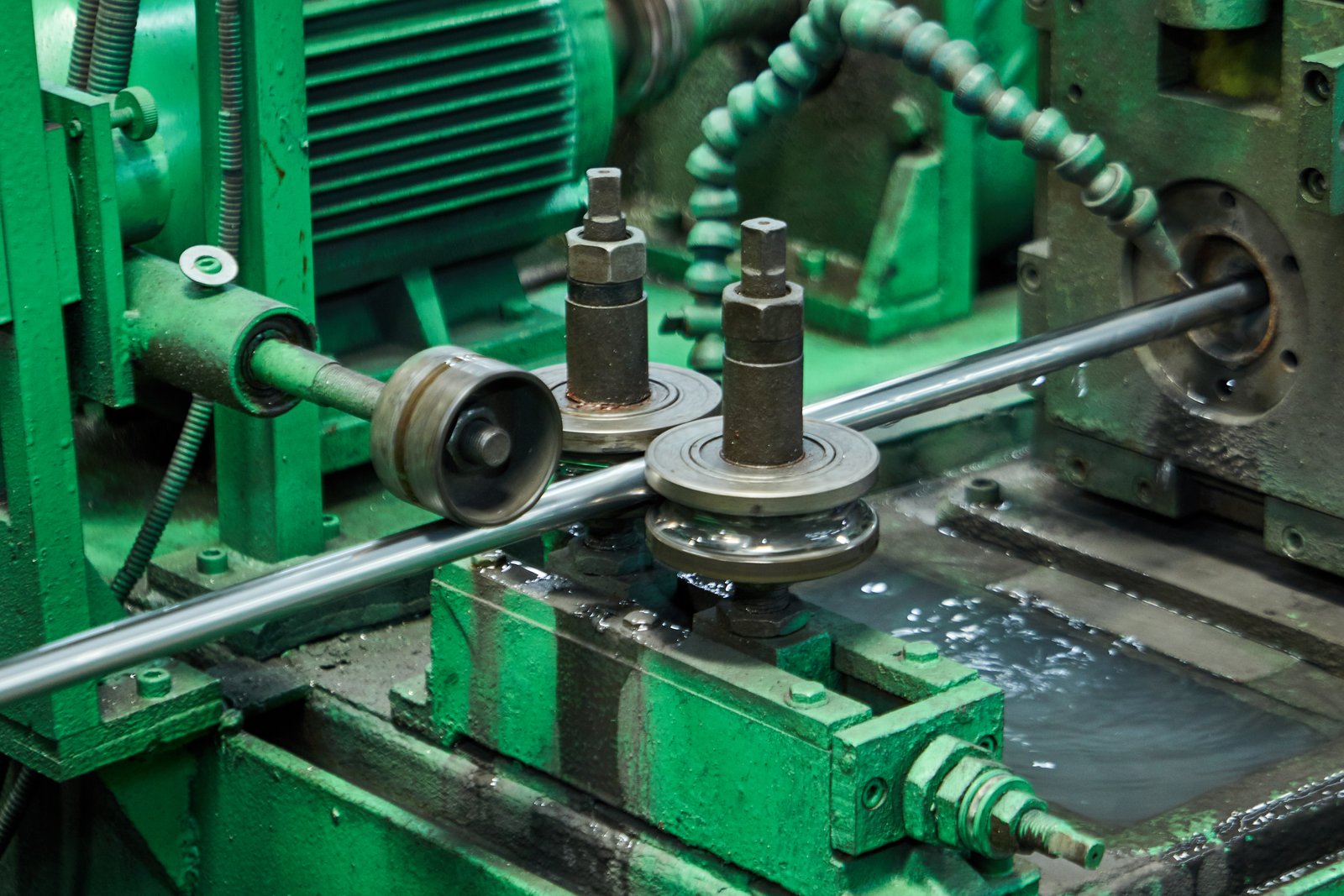
At MFY, quality control is not a department; it's a systemic commitment woven into the fabric of our manufacturing process. We understand that for our target clients—be it manufacturing companies integrating our pipes into their products, engineering and construction contractors relying on them for structural integrity, or distributors supplying critical industries—consistent quality is non-negotiable. Our multi-layered QC strategy is designed to detect and rectify any deviations early, ensuring that every pipe leaving our facility adheres to the strictest standards.
Proactive In-Process Quality Gates
The core of MFY’s quality assurance lies in establishing proactive "quality gates"7 at critical junctures within the manufacturing flow. This means that instead of waiting until the end to inspect for defects, we perform checks continuously. For example, immediately after slitting, strip width and edge condition are verified. Post-forming, the roundness and seam alignment are checked before welding. After welding, inline NDT such as eddy current testing often scans 100% of the weld seam. Dimensional checks for outside diameter, wall thickness, and straightness are performed frequently by operators and QC personnel using calibrated instruments. I once toured our facility with a delegation from a major distributor in Russia, one of our key export markets. They were particularly impressed by our real-time SPC (Statistical Process Control) charts displayed at various workstations, which allow operators to monitor process stability and make adjustments before any parameters drift out of specification. This approach significantly reduces internal scrap and rework rates. Industry data8 shows that implementing robust in-process QC can reduce defect rates by as much as 25-50% compared to relying solely on final inspection. MFY's internal metrics confirm this, with a consistent reduction in non-conformities at final inspection stages due to effective upstream controls.
Advanced Non-Destructive Testing (NDT) and Destructive Testing Protocols
Beyond visual and dimensional checks, MFY employs a suite of advanced Non-Destructive Testing (NDT) methods to ensure the integrity of our stainless steel pipes, especially the weld seam. Common NDT methods include Eddy Current Testing (ECT) for detecting surface and near-surface flaws in the weld, Ultrasonic Testing (UT) for detecting internal weld defects, and Hydrostatic Testing to verify pressure-holding capability and leak tightness. The choice of NDT method and the extent of testing (e.g., 100% of pipes or statistical sampling) often depends on the client's specifications, applicable industry standards (like ASTM, ASME, EN), and the criticality of the application. For instance, a manufacturing company in India producing heat exchangers for the chemical industry required 100% hydrostatic testing at 1.5 times the design pressure for all pipes supplied by MFY. We readily accommodated this, and our internal processes ensured seamless integration of this requirement. In addition to NDT, we also conduct destructive tests on samples taken from production batches. These include tensile tests, flaring tests, flattening tests, and bend tests to verify mechanical properties and weld ductility, ensuring they meet the specified standards. Comparing MFY's approach, we often apply more stringent NDT protocols than mandated by basic standards, especially for pipes intended for demanding export markets like the Middle East's oil and gas sector.
Comprehensive Final Inspection and Traceability Systems
The final inspection is the last critical quality gate before pipes are packaged and dispatched. At MFY, this is a comprehensive process conducted by dedicated QC inspectors. The checklist includes verification of dimensions (length, diameter, wall thickness, straightness), visual inspection for surface finish and defects, checking of markings (grade, size, heat number, MFY logo), and confirmation of correct packaging. Our digital systems play a crucial role here, linking each pipe or bundle back to its production records and, importantly, to the specific raw material heat number used. This robust traceability is vital for quality assurance and for our clients' compliance needs. I recall an instance where an equipment integrator client, supplying to a highly regulated industry, needed to provide full material traceability for an audit. Our system allowed us to quickly retrieve all relevant MTCs and production quality records for the specific batches they had purchased. MFY’s quality management system is certified to ISO 9001, which provides a framework for these processes, but our commitment goes beyond just certification. Customer satisfaction surveys consistently rate MFY highly on product quality, a direct result of these thorough final inspection and traceability measures. Data from our CRM indicates that quality-related complaints are exceptionally low, well below industry averages for similar products.
Production Stage | Key MFY QC Check | Testing Method/Tool Used | Purpose |
---|---|---|---|
Raw Material Receipt | Chemical Composition, Mechanical Properties | PMI Analyzer, Tensile Tester, Hardness Tester | Verify Grade & Properties |
Slitting | Strip Width, Edge Condition | Calipers, Visual Inspection | Ensure correct input for forming/welding |
Forming & Welding | Seam Alignment, Weld Bead Profile, Inline NDT | Visual, Eddy Current/Ultrasonic Testing | Ensure weld integrity and correct form |
Sizing & Straightening | OD, Wall Thickness, Roundness, Straightness | Micrometers, Calipers, Straight Edge, Laser | Meet dimensional specifications |
Heat Treatment | Furnace Temperature, Atmosphere, Hardness | Pyrometers, Gas Analyzers, Hardness Tester | Ensure proper annealing, restore properties |
Finishing (Pickling/Polishing) | Surface Cleanliness, Surface Roughness | Visual, Surface Roughness Tester | Meet aesthetic/functional surface requirements |
Final Inspection | All Dimensions, Visual, Marking, Quantity | Full suite of measuring tools, Visual | Overall compliance to order specifications |
MFY uses in-process quality checksTrue
MFY implements quality control at every critical manufacturing stage, not just at final inspection, to catch issues early.
Quality is only checked at final inspectionFalse
MFY's quality control is embedded throughout the entire production process, with checks at multiple stages before final inspection.
What packaging processes does MFY use to protect pipes during shipment?
Receiving perfectly manufactured pipes only to find them damaged during transit is incredibly frustrating and can lead to costly project delays and disputes. The effort put into quality production is nullified if the goods don't arrive intact. MFY recognizes this critical final step and employs robust packaging processes.
MFY utilizes tailored packaging processes including secure bundling with steel straps, protective end caps for pipe openings, wrapping with waterproof materials like plastic film or woven bags, and sturdy wooden crates or boxes, especially for international shipments, to ensure pipes are well-protected during transit.
The journey of a stainless steel pipe doesn't conclude when it rolls off the production line; it ends when it arrives at our client's doorstep in perfect condition. As Global Business Director, I’ve learned that overlooking the significance of packaging is a common pitfall that can negate all previous quality efforts. A scratch, dent, or contamination during transit can render a high-quality pipe unusable9 for its intended application. At MFY, we consider various factors when determining the optimal packaging: the pipe's dimensions and weight, its surface finish (e.g., highly polished pipes require extra care), the mode of transport (sea, road, rail), the duration of transit, and the environmental conditions it might encounter, especially for our export markets like humid Southeast Asia or the long voyages to the Middle East. Our aim is to provide packaging that is not just adequate, but optimal for ensuring product integrity.
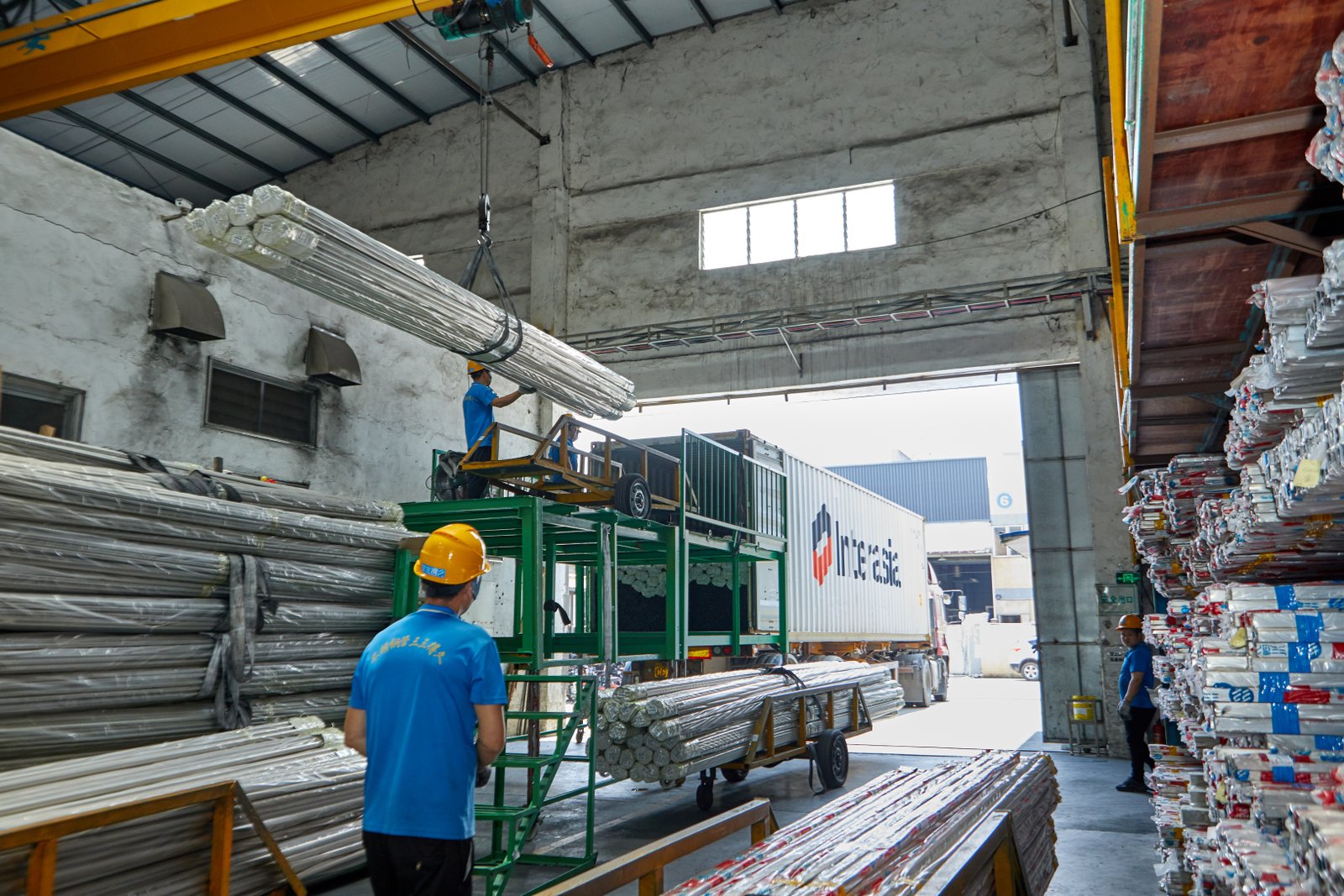
At MFY, we understand that the final impression of our quality commitment is often made when the client receives their shipment. Therefore, our packaging processes are designed with the same meticulous attention to detail10 as our manufacturing. We aim to ensure that the high-quality stainless steel pipes, crafted with precision in our facilities, maintain their integrity and finish throughout the often arduous journey to our diverse clientele, from local manufacturing companies to international engineering contractors across continents.
Tailoring Packaging to Product Specifications and Transit Risks
A one-size-fits-all approach to packaging is simply ineffective in the diverse world of stainless steel pipes. MFY’s packaging strategy begins with a thorough assessment of the product itself and the anticipated transit risks. Factors such as pipe diameter, length, wall thickness, overall weight of the bundle, and especially the surface finish, dictate the primary packaging considerations. For instance, standard mill-finish pipes might be bundled securely with steel straps and plastic end caps. However, for pipes with a polished or mirror finish, often required by architectural projects led by engineering contractors in the Middle East or for sanitary applications, we employ much more delicate handling. This includes individual soft wrapping or plastic sleeving for each pipe within the bundle to prevent abrasion, followed by robust outer protection. We also consider the mode of transport – sea freight to India or Southeast Asia presents different challenges (e.g., moisture, handling at multiple ports) compared to road transport for domestic clients. For long sea voyages, additional measures like VCI (Volatile Corrosion Inhibitor) paper or film might be incorporated within the wrapping to protect against surface oxidation, especially if the pipes are not of a highly corrosion-resistant grade or if the destination has high humidity. Industry best practices, such as those outlined by the Steel Shipping and Packaging Institute (SSPI), often form our baseline, but we frequently enhance these based on our experience and specific client needs.
Material Selection for Optimal Protection
The choice of packaging materials is critical for ensuring the pipes are shielded from mechanical damage, environmental factors, and contamination. MFY invests in high-quality, durable packaging materials. Standard bundles are typically secured with steel strapping. Plastic end caps are used to protect the pipe ends from impact damage and to prevent ingress of dirt or moisture during handling and storage. For waterproof wrapping, we use heavy-gauge plastic film or durable woven polypropylene bags, which provide excellent protection against rain, sea spray, and dust. For more robust protection, especially for export orders or delicate pipes, we construct custom wooden crates or boxes. These are built from sturdy timber, often heat-treated to comply with ISPM 15 international phytosanitary standards, crucial for smooth customs clearance in markets like Europe or Russia. I remember a specific shipment to a client in Southeast Asia for an offshore platform project. The sea journey was notoriously rough. Our team designed reinforced wooden crates with internal cushioning. Upon arrival, despite some external wear on the crates, the client confirmed the pipes were in pristine condition, preventing costly delays for their critical project. A cost-benefit analysis consistently shows that the slightly higher investment in robust packaging materials significantly reduces the much larger costs associated with transit damage, claims, and project disruptions. Data from our logistics department indicates a year-on-year reduction in transit damage claims since implementing more tailored and material-focused packaging protocols.
Standardization and Customization: Finding the Right Balance
While customization is key for specific needs, standardization of packaging protocols for common order types brings efficiency, consistency, and cost-effectiveness. MFY has developed standard packaging specifications for various pipe categories based on size, grade, and finish. This allows our packaging teams to work efficiently and ensures a consistent level of protection for routine orders. However, we maintain the flexibility to offer fully customized packaging solutions. This might be requested by a distributor client who needs bundles of a specific maximum weight or dimension to suit their warehousing systems, or an equipment integrator who requires pipes to be delivered in a particular orientation or kitted with other components. For example, a large distributor in India requested that their pipe bundles be color-coded based on grade and size for easier inventory management in their busy warehouse. We happily incorporated this into their packaging plan. We also collaborate closely with our logistics partners to understand any specific handling constraints or risks associated with certain routes or destinations, allowing us to proactively adjust our packaging. This blend of standardized efficiency and customized attention ensures we meet diverse client requirements effectively.
Packaging Method | MFY Application Context | Key Protection Offered | Typical Use Case |
---|---|---|---|
Bare Bundling (Strapped) | Standard for robust, larger diameter pipes with mill finish | Basic consolidation, prevents scattering | Domestic, short transit, durable pipes |
End Caps | Applied to almost all pipes | Protects pipe ends from damage, keeps clean | Universal application |
Plastic Film/Woven Bag Wrap | Standard for most bundles, especially for export | Waterproofing, dust protection, minor abrasion | Most export/domestic shipments |
Individual Sleeving | Polished or sensitive surface finish pipes | Prevents scratching between pipes | Architectural, sanitary pipes |
Wooden Crates/Boxes | High-value, delicate pipes, long/rough transit, specific client req. | Maximum protection against impact, stacking | Export, sensitive/valuable pipes |
VCI Paper/Film | Added layer for long sea transit or high humidity areas | Corrosion inhibition | Sea freight, long storage |
MFY uses wooden crates for export shipmentsTrue
The text specifically mentions that MFY uses sturdy wooden crates or boxes, especially for international shipments, to ensure maximum protection during transit.
All pipes receive identical packagingFalse
MFY tailors packaging based on multiple factors including pipe specifications and transit risks, with different methods used for mill-finish versus polished pipes.
How does MFY manage logistics to ensure timely delivery of pipes?
Project schedules are tight, and a delayed shipment of critical materials like stainless steel pipes can cause significant disruptions, cost overruns, and damage to your reputation. The anxiety of uncertain delivery times is a common pain point. MFY addresses this directly with a proactive and efficient logistics management system.
MFY manages logistics by maintaining strong finished goods inventory for common items, utilizing integrated production and shipment planning systems, partnering with reliable and vetted freight forwarders, ensuring efficient export documentation, and providing proactive communication to clients regarding shipment status for timely delivery.
Timely delivery is a promise we take as seriously as product quality. As Global Business Director, I’ve seen countless projects where the critical path hinges on the arrival of materials. That’s why "rapid export delivery" isn't just a marketing phrase for MFY; it’s a core component of our operational strength, particularly vital for our clients in India, Southeast Asia, the Middle East, and Russia. Our approach leverages our strong production capacity and inventory management, ensuring we can often ship standard items quickly. Furthermore, our investment in digital innovation extends to our logistics, allowing for better tracking, streamlined documentation, and improved communication with both our logistics partners and our clients. We understand the pressures our clients, from manufacturing companies with just-in-time production lines to engineering contractors on tight project deadlines, face, and our logistics are designed to support their success.
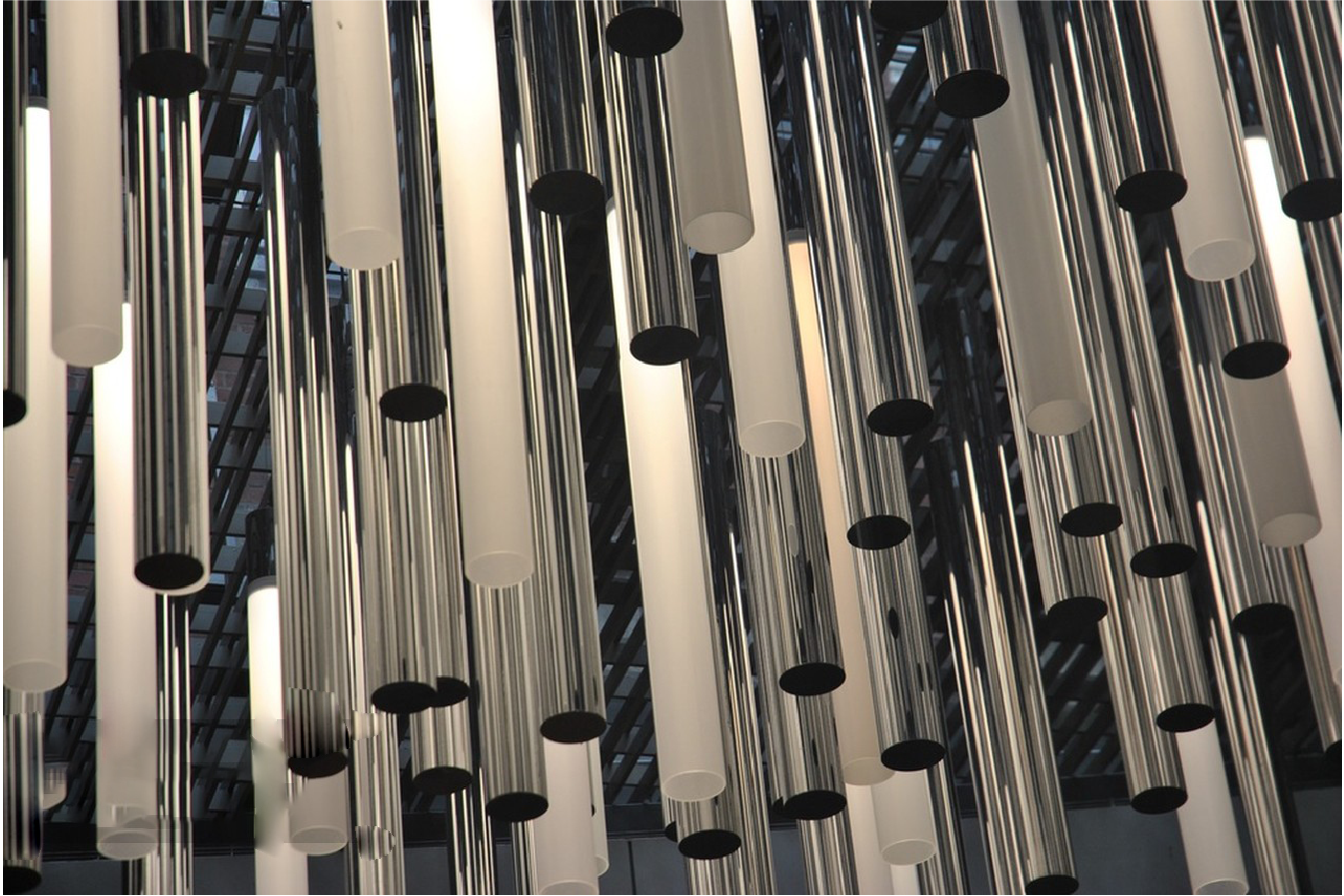
In today's fast-paced global business environment, efficient logistics management is as crucial as the quality of the product itself. At MFY, we recognize that our clients—manufacturing companies, engineering contractors, distributors, and equipment integrators—depend on predictable and timely deliveries to keep their operations running smoothly and their projects on schedule. Our logistics strategy is built on integration, strong partnerships, and proactive communication, ensuring that MFY pipes reach their destinations across our key export markets and beyond, efficiently and reliably.
Integrated Planning: From Production Scheduling to Shipment Coordination
Effective logistics begin long before a product is ready to ship; it starts with integrated planning. At MFY, our sales, production planning, and logistics teams work in close coordination, often facilitated by our robust Enterprise Resource Planning (ERP) system. This system provides real-time visibility into order status, production schedules, and finished goods inventory. When an order is confirmed, it’s not just entered into a queue; it’s assessed against current production capacity and lead times for any non-stock items. This allows us to provide realistic delivery estimates to our clients from the outset. I worked closely with an equipment integrator in Southeast Asia who required a phased delivery of various pipe sizes for a large-scale assembly project with a very tight just-in-time (JIT) schedule. Our integrated planning allowed us to synchronize our production runs and shipment batches precisely with their assembly line needs, preventing both material shortages and excess inventory at their site. Our internal data on on-time delivery performance, which consistently exceeds 95% for confirmed ship dates, is a direct result of this meticulous upstream planning. We also have contingency plans to manage potential disruptions, such as alternative production routing or expedited shipping options, should unforeseen delays occur in manufacturing.
Strategic Partnerships with Freight Forwarders and Carriers
The physical movement of goods, especially for international trade to markets like India, the Middle East, or Russia, relies heavily on the capabilities and reliability of freight forwarders and shipping lines. MFY has a rigorous process for selecting its logistics partners. We evaluate them based on their network coverage in our key export markets, their track record for reliability, their expertise in handling steel products, their financial stability, and, of course, competitive pricing. We don’t just choose the cheapest option; we seek partners who offer the best value and dependability. For example, securing priority booking and container availability during peak shipping seasons can be challenging. However, because of the significant volume MFY ships and our long-term relationships, we often have an advantage. I recall a situation where a large order for a distributor in India needed to be shipped just before a major holiday season when space on vessels was extremely scarce. Our primary freight forwarder was able to secure the necessary bookings, ensuring the client received their materials as planned. We conduct regular performance reviews with our key logistics partners, tracking metrics such as on-time performance, cargo care, and communication responsiveness, ensuring they continuously meet MFY’s high standards.
Proactive Communication and Documentation Management
Keeping clients informed about the status of their shipment is a cornerstone of good logistics service. At MFY, we have dedicated logistics coordinators who proactively communicate with clients, providing updates from the moment the goods are dispatched until they arrive at the destination. This includes sharing shipping details, vessel tracking information, and estimated times of arrival (ETAs). Equally important is the efficient and accurate management of all necessary export documentation. Incorrect or delayed documents (like the Bill of Lading, Commercial Invoice, Packing List, Certificate of Origin, or MTCs) can lead to significant delays at customs, incurring demurrage and detention charges for the client. Our team is well-versed in the specific documentation requirements for our diverse export markets. I once assisted a manufacturing company, a new client exporting to a less common destination, by meticulously preparing and cross-checking all their shipping documents. Our proactive approach ensured a smooth customs clearance process for them, which they greatly appreciated. MFY is increasingly investing in digital tools to streamline document sharing and customer communication, allowing clients to access shipment information and relevant documents through a secure portal, further enhancing transparency and efficiency. The impact of smooth documentation on reducing customs clearance times can be substantial, often saving days in the overall delivery timeline.
Shipping Mode | MFY Primary Use Case & Considerations for Export Markets (India, SE Asia, Middle East, Russia) | Advantages | Disadvantages |
---|---|---|---|
Sea Freight (FCL/LCL) | Standard for most export orders due to volume and cost-effectiveness for pipes. | Cost-effective for bulk, global reach | Longer transit times, potential port congestion |
Air Freight | Urgent, small, high-value orders or critical spare parts. Less common for bulk pipes. | Fastest transit time | Very expensive, weight/size limitations |
Road Transport | Domestic deliveries within China, or to some neighboring countries in SE Asia. | Flexible, door-to-door, good for shorter distances | Can be slower for long distances, traffic dependent |
Rail Transport | Viable for some routes to Russia or Central Asia, depending on infrastructure. | Good for bulk over land, potentially faster than sea for some inland destinations | Limited network, requires intermodal transfer |
MFY ensures quality at every stepTrue
The text explicitly states MFY's process includes stringent material selection, precision manufacturing, and multi-stage quality checks.
Stainless steel pipes are simple commoditiesFalse
The text clarifies the industry is nuanced, requiring consistent quality and dependable delivery beyond basic specifications.
Conclusion
MFY’s dedication to quality is unwavering, from meticulous raw material sourcing and precision manufacturing to robust packaging and agile logistics. This integrated approach ensures we consistently deliver superior stainless steel pipes and reliable service to our global clients, empowering their success.
-
Understanding protective packaging enhances pipe integrity during shipping ↩
-
Discover the certification process for stainless steel coils and plates used in manufacturing. ↩
-
Understand metallurgical properties crucial for stainless steel pipe performance and durability. ↩
-
Understand the importance of proper edge preparation for quality welding outcomes ↩
-
Learn why TIG welding is ideal for aesthetically pleasing and structurally sound welds ↩
-
Discover MFY's continuous improvements in QC for enhanced reliability ↩
-
Understand how proactive quality gates ensure defect prevention ↩
-
Explore data on defect rate reduction through robust QC processes ↩
-
Learn about common types of damage affecting the usability of stainless steel pipes ↩
-
Discover how effective packaging can preserve product quality during shipment ↩
Have Questions or Need More Information?
Get in touch with us for personalized assistance and expert advice.