Seamless vs Welded Pipe: When Each Makes Sense
Struggling to decide between seamless and welded pipes for your project? The wrong choice can lead to operational failures or budget overruns, creating significant headaches. This guide clarifies their differences, helping you select the optimal pipe type for your specific needs every time.
Seamless pipes, made from a solid steel billet, offer superior strength and corrosion resistance for high-pressure applications. Welded pipes, formed by rolling and welding steel sheets, are more cost-effective for lower-pressure, structural, and general-purpose uses, making each suitable for distinct scenarios.
Choosing the right pipe isn't just a technical detail; it's a critical decision that impacts your project's safety, longevity, and overall cost-effectiveness. As Global Business Director at MFY, I've seen firsthand how understanding these nuances can make or break an endeavor. Let's delve deeper into what sets these two pipe types apart and explore how to make the best choice for your requirements.
The debate between seamless and welded pipes isn't simply about a seam or no seam; it's a complex interplay of manufacturing methodologies, material science, and application-specific demands. While seamless pipes are often lauded for their inherent structural integrity, advancements in welding technology have significantly narrowed the performance gap for many applications. For instance, consider the petrochemical industry in the Middle East, where MFY has supplied stainless steel pipes for critical systems. While seamless was traditionally the default, high-frequency induction (HFI) welded pipes1 are now being considered for certain less critical lines due to improved weld quality and cost benefits. However, for hydrogen service or extremely high-pressure steam, the homogeneity of seamless pipes still provides an unparalleled safety margin. We must critically assess not just the "what" but the "why" behind each choice, factoring in long-term maintenance, inspection requirements, and the total cost of ownership rather than just initial purchase price.
What are the fundamental differences between seamless and welded pipes?
Confused by the basic distinctions between seamless and welded pipes? This uncertainty can lead to misapplication and performance issues. Understanding their core manufacturing differences is the first step to making an informed selection, ensuring your project's integrity from the start.
Seamless pipes are manufactured by piercing a solid steel billet, resulting in a homogenous structure without any seams. Welded pipes are formed by rolling a steel plate or strip and then welding the edges together, creating a longitudinal or spiral seam.
These fundamental manufacturing distinctions might seem straightforward, but they are the bedrock upon which all subsequent performance characteristics are built. At MFY, we often encounter clients, particularly new distributors in emerging markets like Southeast Asia, who are keen to understand these basics to better serve their local customers. It's not just about how they're made, but how those methods translate into real-world advantages or limitations. For example, the absence of a seam in seamless pipes inherently eliminates a potential weak point, which is a critical consideration for industries handling corrosive fluids or operating under high stress. Conversely, the versatility and cost-efficiency of welded pipe manufacturing open up a broader range of applications where such extreme conditions aren't a factor. As we explore these differences further, you'll see how these initial manufacturing choices cascade into significant implications for pressure ratings, corrosion resistance, and even the types of inspections required. Understanding this foundation is crucial before we can even begin to discuss specific applications or make informed recommendations. Let’s break down these differences in more detail to build a solid understanding. The journey from raw steel to finished pipe is fascinating and reveals much about its ultimate capabilities, a journey I've explained to many partners, from engineering contractors in India to equipment integrators looking for reliable components.
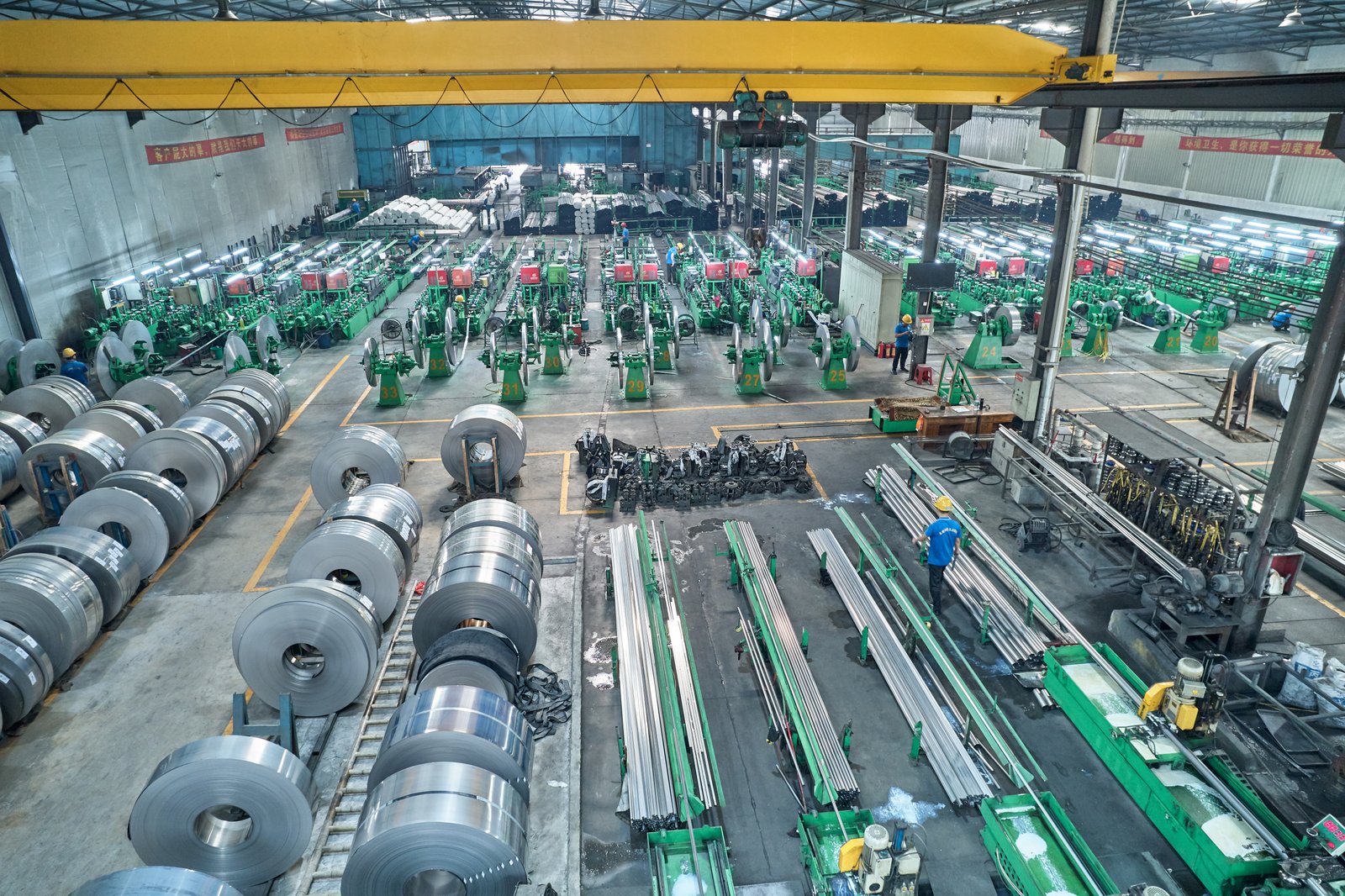
The distinction between seamless and welded pipes begins at the very genesis of their creation, influencing every aspect of their performance, from mechanical strength to corrosion resistance and cost. Understanding these fundamental differences is paramount for engineers, procurement specialists, and project managers alike. As we, at MFY, engage with clients across diverse sectors—from manufacturing companies in India to large-scale engineering contractors in Russia—the initial conversation often revolves around clarifying these core concepts to ensure the selected piping solution aligns perfectly with the application's demands. It’s not merely an academic exercise; it’s about ensuring safety, longevity, and economic viability. I've personally walked through our MFY production facilities with clients, showing them the billet piercing for seamless pipes versus the forming and welding lines for our welded products, and the "aha!" moment is always rewarding when they see the processes firsthand.
The Genesis: Raw Material and Initial Forming
The journey of a seamless pipe starts with a solid cylindrical piece of steel, known as a billet or a round. This billet is heated to a high temperature, making it malleable, and then pierced through its center with a hardened steel tool called a mandrel. The subsequent rolling and stretching processes elongate this hollow billet, refining its shape and achieving the desired wall thickness and diameter. This method inherently results in a pipe with a uniform, homogenous grain structure and consistent strength properties throughout its circumference, as there are no welded joints that could potentially act as stress concentrators or preferential sites for corrosion. For instance, in a recent project supplying a major chemical processing plant in the Middle East, the client specified MFY's seamless stainless steel pipes for handling highly corrosive acids at elevated temperatures. The inherent homogeneity of the seamless pipe provided the assurance against premature failure that a welded seam, however well-made, might not guarantee under such aggressive conditions. ASTM A312 for seamless austenitic stainless steel pipes is a common standard we adhere to for such applications, ensuring material integrity that our clients, like this one, depend on for critical infrastructure. This process, while more complex, guarantees a level of structural integrity that is non-negotiable in certain high-risk environments.
The manufacturing of welded pipes, conversely, typically begins with a flat steel plate or a continuous coil of steel strip (often called skelp). This skelp is progressively formed into a cylindrical shape by passing it through a series of precision rollers. Once the cylindrical shape is achieved, the longitudinal edges are brought together and joined using various welding techniques. Common methods include Electric Resistance Welding (ERW), High-Frequency Induction (HFI) welding, Submerged Arc Welding (SAW), or more advanced techniques like Laser Beam Welding (LBW) and Plasma Arc Welding (PAW). The quality and integrity of the weld seam are absolutely critical to the performance of a welded pipe. Modern welding technologies, many of which we employ at MFY, have advanced significantly, producing seams that are often nearly indistinguishable in strength and microstructure from the parent metal, especially after appropriate post-weld heat treatment and finishing. For example, MFY recently supplied HFI welded stainless steel pipes to a food processing facility in Southeast Asia. The precise control over the HFI welding process ensured a minimal, smooth internal bead, crucial for maintaining hygiene and preventing bacterial traps, while offering a more cost-effective solution than seamless pipes for their moderate pressure and temperature requirements. Industry data2 from sources like the SteelConstruction.info portal shows that for many applications, the burst pressure of high-quality ERW/HFI pipes can approach 80-95% of that of a comparable seamless pipe, demonstrating the reliability of modern welding.
The choice of raw material form – solid billet versus flat plate/coil – is the first major divergence and dictates much of the subsequent process. Seamless pipes inherently avoid the complexities and potential inconsistencies associated with creating and inspecting a weld seam. However, this also means the manufacturing process can be more energy-intensive and may have limitations on the achievable diameter-to-thickness ratios or very large diameters compared to some welded pipe manufacturing methods, especially for extremely large diameter pipes where processes like SAW (Submerged Arc Welding) become highly efficient. We often advise clients at MFY that while the "no seam" aspect of seamless pipes is a clear advantage in truly critical, high-stress applications, the advancements in non-destructive testing (NDT) for welded pipes, such as sophisticated ultrasonic testing (UT) arrays and eddy current testing, provide exceptionally high levels of assurance for seam integrity in a vast range of other scenarios. It's a balance of risk, requirement, and cost.
The Seam Factor: Presence vs. Absence and Its Implications
The most obvious and defining difference is the presence of a weld seam in welded pipes and its complete absence in seamless pipes. This seam, in a welded pipe, is by its very nature a zone of metallurgical discontinuity. Even with the most advanced welding techniques and meticulous post-weld heat treatment, the microstructure of the weld metal itself and the adjacent Heat-Affected Zone (HAZ) will inevitably differ to some extent from that of the base (parent) metal. This difference can influence mechanical properties such as tensile strength, ductility, toughness, and fatigue life. More critically for some applications, it can also make the seam area more susceptible to certain types of corrosion, like preferential weld corrosion or stress corrosion cracking, especially in aggressive chemical environments if not perfectly executed and treated. For example, a study published in the "Journal of Materials Engineering and Performance" highlighted that in chloride-rich environments, the HAZ in certain austenitic stainless steel welded pipes can be more prone to pitting corrosion if the welding process isn't optimized or if post-weld cleaning and passivation are inadequate.
Seamless pipes, lacking this metallurgical discontinuity, offer a more uniform resistance to corrosion and a more predictable, homogenous response to mechanical stresses and thermal cycling. This is precisely why for critical applications such as high-pressure steam lines in power plants, pipelines transporting sour gas (H2S-containing natural gas) in the oil and gas sector, or critical hydraulic systems, seamless pipes are often mandated by stringent industry codes and standards like ASME B31.3 for process piping or API 5L for line pipe. I recall a case with an engineering contractor in India working on a refinery upgrade; the specification for all high-pressure hydrogen service lines was unequivocally seamless, due to concerns about hydrogen embrittlement and high-temperature hydrogen attack, phenomena which can be significantly exacerbated at weld seams and their associated HAZs. MFY supplied the seamless alloy pipes for this project, understanding the critical safety implications.
However, it's crucial not to paint all welded pipes with the same broad brush of suspicion. The quality of the weld is paramount, and modern manufacturing has achieved remarkable consistency. Processes like ERW and HFI welding involve heating the edges of the steel to forging temperatures using high-frequency electrical current, then pressing them together under immense pressure. This often results in a very fine-grained, strong weld that, after proper heat treatment, can have properties very close to the parent metal. For many applications, particularly those involving lower pressures, less corrosive fluids—such as water distribution, general plumbing, structural supports, or many food and beverage applications—the performance of a high-quality welded pipe from a reputable manufacturer like MFY is more than adequate and offers significant cost advantages. Our quality control for welded pipes includes rigorous NDT protocols, such as hydrostatic testing, ultrasonic inspection of the seam, and eddy current testing, to ensure seam integrity, aligning with standards like ASTM A249 for welded austenitic steel boiler, superheater, heat-exchanger, and condenser tubes, or ASTM A269 for general service welded stainless steel tubing. The key is always matching the pipe type and its proven quality level to the specific service conditions, a philosophy we deeply ingrain in our MFY team.
Implications for Performance, Testing, and Cost
These fundamental manufacturing differences directly translate into variations in performance characteristics, required testing rigors, and, significantly, cost. Seamless pipes generally boast higher pressure ratings compared to welded pipes of the same material, grade, and dimensions, primarily because their structural integrity isn't reliant on a weld seam whose properties might deviate, however slightly, from the base material. Their uniform grain structure also contributes to better performance in high-temperature services (enhanced creep resistance) and under severe cyclic loading conditions. This superior performance assurance, however, comes at a premium. The manufacturing process for seamless pipes is typically more complex, involving more steps and often more energy, and can be less material-efficient (lower yield from billet to pipe) than for welded pipes, leading to higher production costs. The testing for seamless pipes, while rigorous, focuses on the homogeneity of the entire pipe body.
Welded pipes, especially ERW/HFI types, are generally more cost-effective to produce, particularly in common sizes and for large production runs. The raw material (steel coil or plate) is often less expensive per unit weight than the specially prepared billets for seamless production, and the forming and welding process can be highly automated and achieve very high throughput rates. This cost advantage makes welded pipes an extremely attractive option for a vast range of applications where the absolute highest pressure ratings or the most extreme corrosion resistance under unusual conditions are not overriding concerns. For instance, for a construction project requiring stainless steel handrails and architectural tubing in Southeast Asia, MFY would typically recommend our aesthetically pleasing and durable welded pipes. The aesthetic requirements and moderate structural loads are easily met by these welded pipes at a fraction of the cost of seamless alternatives. A comparative cost analysis we conducted for a client, a distributor in Russia, considering pipes for a low-pressure water treatment system showed that MFY's welded stainless steel pipes offered a saving of nearly 25-35% compared to seamless options, without any compromise on the required performance or lifespan for that specific application. Testing for welded pipes includes all the tests for seamless pipes plus specific tests focused on the integrity of the weld seam, such as ultrasonic or radiographic inspection of the weld.
The following table summarizes some key general differences stemming from their manufacturing:
Feature | Seamless Pipe | Welded Pipe (e.g., ERW/HFI/SAW) |
---|---|---|
Manufacturing | Pierced & rolled from solid billet | Formed from plate/coil, then edges welded |
Key Characteristic | Homogenous, no seam | Contains a longitudinal or spiral weld seam |
Structural Uniformity | High, consistent properties throughout | Parent metal properties + distinct weld/HAZ properties |
Typical Pressure Capability | Generally higher for same material/dimensions | Generally lower, but often sufficient; depends on weld quality & type |
Potential Weak Point | Material defects (e.g., inclusions, laminations) | Weld seam and Heat-Affected Zone (HAZ) |
Cost | Higher | Lower |
Common Use Focus | High integrity, extreme conditions, critical safety | General purpose, structural, cost-sensitive projects |
Ultimately, the choice is not about which pipe is "better" in an absolute sense, but which is more "fit for purpose." The fundamental differences in their creation dictate their suitability for diverse operational landscapes. As we move forward, we’ll see how these basics translate into specific application advantages and informed selection criteria, a journey I've helped many MFY clients navigate successfully.
Seamless pipes have no weld seamsTrue
Seamless pipes are manufactured from solid billets without any welding, resulting in a homogenous structure.
Welded pipes are weaker than seamlessFalse
Modern welding techniques can produce welded pipes with strength approaching 80-95% of seamless pipes for many applications.
How does the manufacturing process impact the properties of each pipe type?
Unsure how a pipe's origin story affects its strength and lifespan? This knowledge gap can lead to selecting a pipe that fails under pressure or corrodes too quickly. Understanding the manufacturing impact is crucial for ensuring reliability and avoiding costly replacements.
Seamless pipe manufacturing (billet piercing process in seamless pipes) results in uniform strength and high-pressure resistance. Welded pipe processes (electric resistance welding techniques) can introduce metallurgical differences at the seam but often offer better dimensional control and cost-effectiveness for many applications.
The journey from raw steel to a finished pipe is a tale of heat, pressure, and precision engineering. Each step, whether it's the meticulous piercing of a solid billet for a seamless pipe or the carefully controlled welding of a steel strip for its counterpart, imprints distinct characteristics onto the final product. These aren't just minor variations; they define the pipe's mechanical strength, its ability to withstand corrosive environments, its dimensional accuracy, and ultimately, its suitability for a specific job. At MFY, we often walk our clients, from large engineering contractors in Russia scrutinizing specs for a new chemical plant to specialized equipment integrators in India needing precision tubing, through these manufacturing nuances. It helps them appreciate why one MFY pipe might be ideal for a high-stakes petrochemical application, while another is perfectly suited for general industrial water lines. Understanding this "nature versus nurture" aspect of pipe properties is critical. The inherent qualities derived from the manufacturing process are fundamental to predicting performance and ensuring the longevity of any piping system. This understanding allows our clients to make informed decisions that impact not just upfront costs but also long-term operational reliability, a core value we champion at MFY.
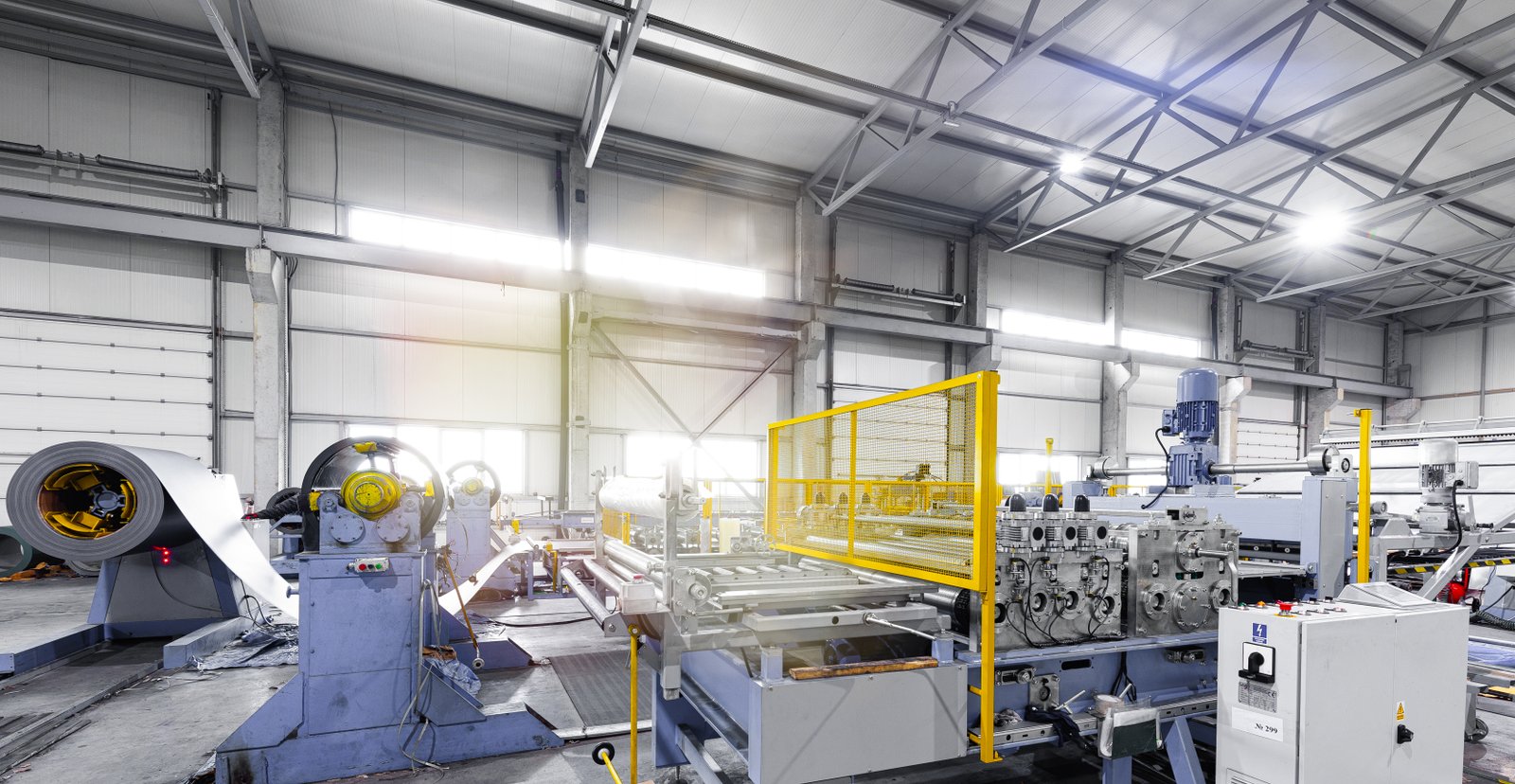
The manufacturing process is not merely a method of shaping steel; it is a critical determinant of a pipe's inherent properties, profoundly influencing its mechanical strength, corrosion resistance, dimensional tolerances, and even its surface finish. As a supplier of both seamless and welded stainless steel pipes at MFY, I’ve seen countless instances where a thorough understanding of these manufacturing impacts has guided clients towards the optimal choice, preventing future failures and optimizing costs. The journey from raw material to finished product imprints a unique signature on each pipe type, dictating its performance envelope. For example, I once worked with a manufacturing company in Southeast Asia that was experiencing unexpected corrosion in their piping system. A deep dive revealed they had used a welded pipe grade not ideally suited for the subtle cyclic temperature changes and minor chemical exposures in their process – a detail that understanding the HAZ's slightly different properties could have highlighted earlier.
Mechanical Strength and Structural Integrity: The Core of Performance
The manufacturing route has a direct and significant bearing on a pipe's mechanical strength. Seamless pipes, being forged from a single, solid billet through processes like Mannesmann piercing, pilgrim mill rolling, or extrusion, exhibit a homogenous grain structure throughout their cross-section. This uniformity means there are no inherent weaker zones like a weld seam or a heat-affected zone (HAZ) with potentially altered microstructures. Consequently, seamless pipes generally offer superior tensile strength, higher burst pressure ratings (often calculated with a joint efficiency factor of 1.0 in code calculations, like in ASME B31.3), and better performance under conditions of high stress, fatigue, and thermal cycling. For example, in power generation plants, main steam lines often operate at temperatures exceeding 500°C (932°F) and pressures well over 150 bar (2175 psi). ASTM A335 (for seamless ferritic alloy-steel pipe for high-temperature service) grades like P91 or P92 are commonly specified in seamless form precisely because this manufacturing process ensures the pipe can withstand these extreme conditions without the potential vulnerability of a weld. I recall a project with an equipment integrator in the Middle East designing a critical heat exchanger for a petrochemical application; the decision to use MFY's seamless stainless steel tubes was driven by the need for absolute reliability under fluctuating thermal loads and high internal pressures, where even a microscopic weld imperfection could propagate under stress and lead to a costly, or even dangerous, failure. The homogeneity ensures more predictable plastic deformation behavior and higher toughness in some cases.
Welded pipes, on the other hand, derive their strength characteristics from both the base metal (the steel strip or plate) and the integrity of the weld joint. Modern welding techniques, such as Electric Resistance Welding (ERW), High-Frequency Induction (HFI) welding, and Submerged Arc Welding (SAW), have made remarkable strides. High-quality welded pipes, especially those undergoing appropriate post-weld heat treatment (PWHT) like normalizing or stress relieving, and rigorous non-destructive testing (NDT), can exhibit mechanical properties very close to those of the parent material. However, the weld metal and the HAZ remain areas of metallurgical difference. The HAZ, for instance, undergoes a rapid thermal cycle that can alter its grain structure and mechanical properties, potentially making it slightly harder or softer, or having different toughness characteristics compared to the unaffected base metal, depending on the material composition and the specifics of the welding process. For instance, a study by The Welding Institute (TWI) indicated that while the tensile strength of a well-executed weld in carbon steel can readily match the base metal, the fatigue performance under cyclic loading can sometimes be lower due to geometric stress concentrations at the weld toe or cap, unless these are carefully controlled and smoothed. MFY ensures that our welded stainless steel pipes, like those conforming to ASTM A312 (welded condition), undergo meticulous quality control, including weld bead conditioning (e.g., rolling or planishing) and comprehensive NDT, to minimize these effects. This makes them perfectly suitable for a wide array of applications, including many pressure vessel components and structural uses where their cost-effectiveness is a major advantage. For example, our welded pipes are widely used by manufacturing companies in India for process lines where pressures are moderate and conditions are well-defined.
The debate often centers on the "weakest link" principle and the statistical probability of defects. In seamless pipes, any defect would likely be an inherent flaw within the base material itself, such as an inclusion or lamination originating from the steelmaking or billet casting process. In welded pipes, the weld seam, despite advances and rigorous testing, is statistically often considered the most probable site for the initiation of failure if manufacturing quality is not stringently controlled or if the pipe is unknowingly pushed beyond its designed operational limits. This is why critical service applications, where the consequence of failure is severe, often default to seamless, providing that extra margin of safety derived from complete material homogeneity. This is a common discussion point with engineering and construction contractors working on high-risk projects.
Corrosion Resistance and Material Purity: The Durability Factor
The manufacturing process also significantly influences a pipe's susceptibility to various forms of corrosion. Seamless pipes, with their uniform microstructure and complete absence of a weld seam, generally offer more consistent and predictable corrosion resistance across their entire surface. There are no crevices, flux residues, or metallurgical changes associated with welding that could become preferential sites for corrosive attack, such as pitting corrosion, crevice corrosion, or intergranular corrosion. This consistent behavior is particularly important when handling aggressive fluids or in environments where localized corrosion mechanisms are active. For example, MFY supplied seamless duplex stainless steel pipes (e.g., UNS S32205 conforming to ASTM A790) to a desalination plant in the Middle East. The high chloride content of seawater is extremely corrosive, and the uniform surface and microstructure of the seamless pipes provided superior resistance to chloride-induced stress corrosion cracking (SCC) compared to what might be expected from a welded counterpart if the weld quality, filler material choice (if used), or post-weld treatment was suboptimal. The absence of a sensitized HAZ is a key benefit here.
For welded pipes, the weld seam and HAZ can be areas of heightened concern for corrosion if not properly managed during manufacturing and subsequent treatment. During the welding process, especially in older types of austenitic stainless steels without low carbon content, sensitization can occur. This involves the precipitation of chromium carbides at grain boundaries in the HAZ, depleting the adjacent regions of chromium and reducing their passivity, thereby making these areas susceptible to intergranular corrosion. Modern best practices, which MFY strictly adheres to, include using low-carbon stainless steels (e.g., 304L, 316L, where 'L' denotes carbon content ≤ 0.03%), stabilized grades (e.g., 321, which contains titanium, or 347, which contains niobium), or implementing appropriate post-weld heat treatment (like solution annealing followed by rapid quenching for austenitic stainless steels) to redissolve any precipitated carbides and restore full corrosion resistance. Our manufacturing protocols for welded stainless steel pipes, such as those supplied to food and beverage applications in Southeast Asia under ASTM A270 (sanitary tubing), include processes that ensure a smooth, passive internal surface, minimizing any potential for corrosion that could compromise product purity. Research published in journals like "Corrosion Science" has often detailed how weld metallurgy, the surface finish of the weld bead (e.g., removal of slag or oxide, smoothing of the profile), and specific PWHT cycles can dramatically affect the corrosion performance of welded stainless steel in specific environments.
Furthermore, the initial raw material itself can play a subtle role. Seamless pipes are made from solid billets that are often produced with stricter controls on inclusions and tramp elements, as they are frequently destined for more critical applications. While high-quality, clean steel is also used for welded pipes, particularly by reputable manufacturers like MFY (we have stringent incoming material inspection for all our raw materials, whether billets for seamless or coils for welded), the sheer volume and varied applications of steel coil and plate production for the broader welded pipe market might statistically allow for a slightly wider tolerance in some non-critical commodity grades. The key takeaway is that while seamless pipes offer an inherent baseline advantage in corrosion resistance due to homogeneity, high-quality welded pipes manufactured with proper material selection, advanced welding techniques, and appropriate post-weld treatments can perform exceptionally well in a multitude of corrosive environments, often rivaling seamless performance for many practical purposes.
Dimensional Accuracy, Surface Finish, and Cost Implications: Practical Considerations
Dimensional tolerances and surface finish are also significantly influenced by the manufacturing method. Seamless pipes, particularly those that are hot-finished (produced at high temperatures without subsequent cold working), can sometimes exhibit greater variations in wall thickness around the circumference (eccentricity) and overall ovality compared to cold-drawn seamless pipes or many types of welded pipes. The nature of the piercing and rolling process at high temperatures can lead to these dimensional variations. Cold drawing, a secondary process where a hot-finished seamless tube is pulled through a die and over a mandrel at room temperature, greatly improves dimensional accuracy, tightens tolerances, and enhances the surface finish for seamless pipes, but it also adds to the cost and process time. For applications requiring very precise outside diameters, inside diameters, or wall thicknesses, such as in heat exchanger tubes where fit into tube sheets is critical, or for precision instrumentation tubing, cold-drawn seamless (CDS) tubes or high-quality welded and drawn/sized tubes are often preferred. A client of MFY, a manufacturer of precision scientific instruments in Europe, specifically orders our small-diameter, cold-drawn seamless stainless steel tubing (e.g., bright annealed to ASTM A269) for its tight tolerances (often +/- 0.05mm on OD) and exceptionally smooth internal finish, crucial for their sensitive fluid handling systems.
Welded pipes, especially those made using modern ERW/HFI processes from precision-rolled steel strip, can offer excellent dimensional control, particularly for wall thickness. The wall thickness of an ERW/HFI pipe is primarily determined by the thickness of the initial coil or plate, which can be controlled very tightly during the steel rolling process (often to within +/- 5% to +/- 10% of nominal, or even tighter for precision strip). The outside diameter consistency and roundness are also generally very good, as these are shaped by precision rolls. The surface finish of welded pipes can also be very well controlled, especially if the pipes are made from cold-rolled strip, which inherently has a smoother and brighter surface. This makes welded pipes highly suitable for applications where tight fit-up for subsequent welding is required, where components like O-rings need to seal effectively against the pipe OD, or where aesthetics are important, such as architectural applications. For example, MFY supplies polished welded stainless steel tubes for decorative handrails and building facades to construction projects in India and the Middle East, where consistent diameter and a flawless, reflective finish are paramount. Industry data, such as that found in mill test certificates, often indicates that the wall thickness tolerance for quality ERW pipes can be significantly tighter than for standard hot-finished seamless pipes, which might commonly be +/- 12.5% or even more according to some standards like ASTM A53 for commodity carbon steel pipe.
The impact on cost is undeniable and often a primary driver in selection. The multi-step, often more energy-intensive process of producing seamless pipes, coupled with potentially lower material yield from billet to finished pipe, usually results in a higher unit cost compared to welded pipes, especially for common carbon steel and standard stainless steel grades. This cost difference can be substantial. While a high-pressure, safety-critical application in an oil refinery might easily justify the premium for seamless pipes, a general-purpose water line in a factory or a structural support in a building would likely favor the more economical welded pipe, provided its properties comfortably meet all the design requirements. MFY always works with clients to perform a total cost of ownership (TCO) analysis. Sometimes a slightly more expensive upfront pipe choice (like a specific seamless alloy) can save significant money in the long run through reduced maintenance, longer life, or prevention of costly downtime, but very often, the initial cost saving of well-chosen welded pipes is a compelling and entirely justifiable factor for many target clients, including distributors and traders who need to remain competitive.
Property Affected | Seamless Pipe Manufacturing Impact | Welded Pipe Manufacturing Impact |
---|---|---|
Mechanical Strength & Integrity | Homogenous structure, generally higher inherent strength, no weld weakness. | Strength depends on base metal AND weld/HAZ quality. Potential for localized property variations. |
Pressure Rating | Typically higher due to uniform structure and no seam de-rating factor. | Generally lower than seamless for same size/material; weld efficiency factor may apply in codes. |
Corrosion Resistance | Uniform resistance across surface; no preferential weld/HAZ attack sites. | Weld/HAZ can be more susceptible if not optimally produced/treated (e.g., sensitization, crevice at weld bead). |
Dimensional Control | Hot-finished: wider tolerances on wall/ovality. Cold-drawn: much tighter. | ERW/HFI: Excellent wall thickness uniformity from strip; good OD/roundness control. |
Surface Finish | Hot-finished: can be rougher, may have scale. Cold-drawn: smoother. | Can be very smooth, especially if made from cold-rolled strip; internal/external weld bead can be conditioned. |
Cost Efficiency | Higher production cost due to complex process and often lower material yield. | Generally lower production cost due to efficient process from coil/plate and higher yield. |
Understanding these manufacturing-led property distinctions is absolutely crucial. It’s not about an inherent superiority of one type over the other in all cases, but rather an appreciation of how their specific "birth process" affects their lifelong capabilities and ultimate suitability for the diverse and demanding tasks we assign to them in modern industry.
Seamless pipes have uniform strengthTrue
Seamless pipes are made from a single billet without welds, resulting in consistent mechanical properties throughout.
Welded pipes always corrode fasterFalse
Properly manufactured welded pipes with appropriate post-weld treatments can match seamless pipe corrosion resistance in many applications.
What are the specific applications where seamless pipes excel?
Risking pipe failure in a critical system because you chose incorrectly? Such an oversight can lead to catastrophic consequences and severe financial losses. Knowing where seamless pipes are non-negotiable ensures safety, reliability, and operational integrity for your most demanding applications.
Seamless pipes excel in high-pressure, high-temperature applications like oil and gas transmission, chemical processing, power generation (steam lines), and critical hydraulic systems. Their homogenous structure ensures superior strength, corrosion resistance, and reliability under extreme conditions where failure is not an option.
When the stakes are exceptionally high, and the operational environment pushes materials to their absolute limits, seamless pipes often emerge as the undisputed champions. Their unique manufacturing process, commencing from a solid steel billet, imbues them with a level of structural integrity and material homogeneity that is paramount in applications where even the smallest flaw or inconsistency could lead to disastrous outcomes. At MFY, we've guided numerous clients, particularly in the energy and heavy industrial sectors3 across our key export markets in the Middle East and Russia, through the rigorous specifications that inherently demand seamless piping solutions. It's in these challenging arenas – characterized by extreme pressures, soaring temperatures, and aggressive or hazardous media – that the "no seam" advantage truly shines, providing an unparalleled level of safety and reliability. Understanding these specific scenarios isn't just about adhering to industry codes and standards; it's about a fundamental commitment to operational excellence and safeguarding critical infrastructure, personnel, and the environment. Let's explore the domains where seamless pipes are not just preferred but are often the only viable and responsible choice.
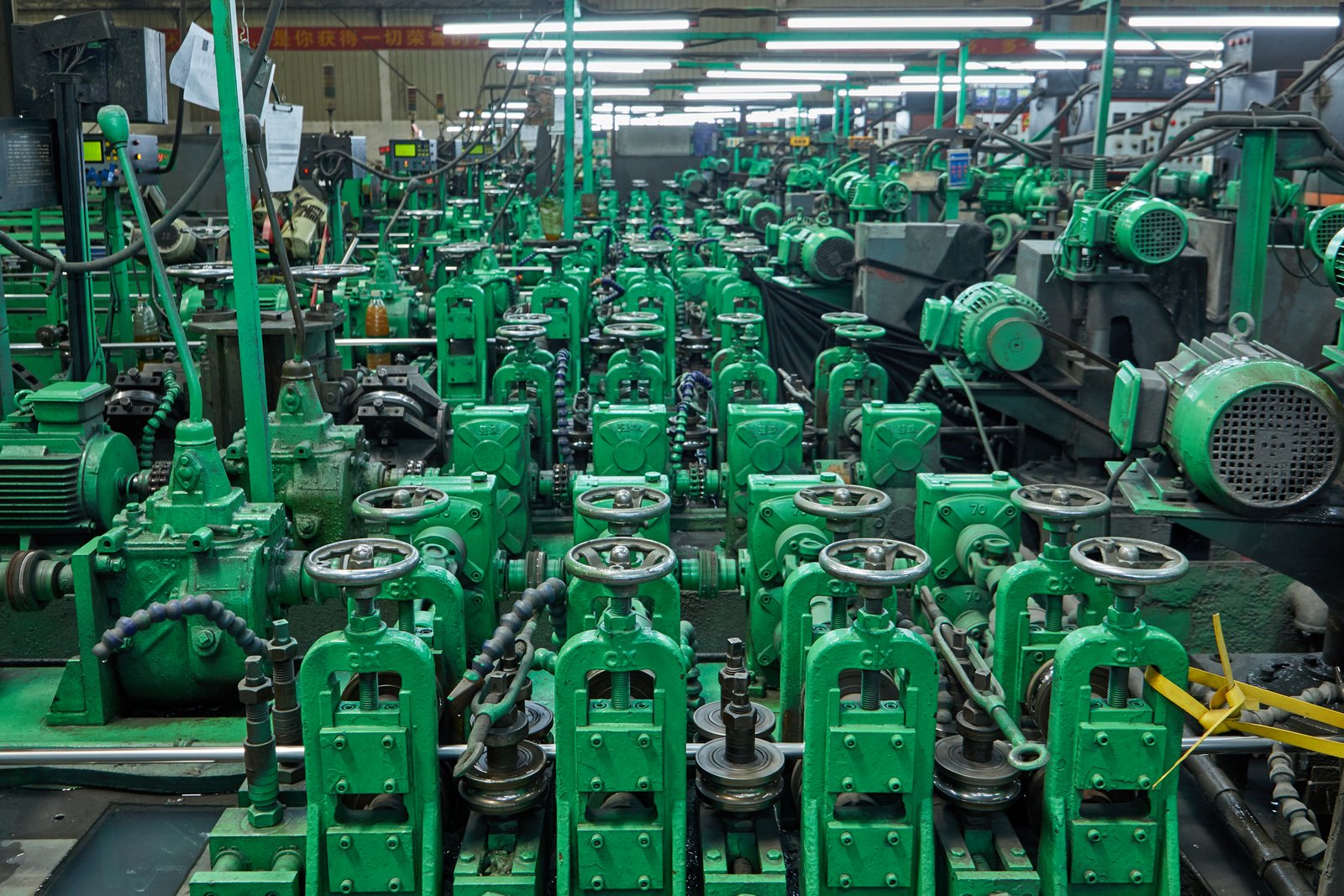
Seamless pipes, by virtue of their manufacturing process which results in a homogenous structure devoid of any weld seams, are inherently suited for applications where operational integrity, safety, and resistance to extreme conditions are paramount. Their ability to withstand high pressures, elevated temperatures, and aggressive corrosive environments makes them the preferred, and often mandated, choice in several critical industries. As we at MFY often discuss with engineering contractors and manufacturing clients planning high-stakes projects, the decision to specify seamless pipes in these contexts is driven by a non-negotiable need for unparalleled reliability and safety assurance. I've been involved in discussions for projects, for instance, in remote Siberian gas fields where the consequence of a pipeline failure would be environmentally and economically devastating, making seamless pipes the only considered option for certain segments.
High-Pressure and High-Temperature (HPHT) Environments: The Ultimate Test
One of the foremost domains where seamless pipes unequivocally excel is in high-pressure and high-temperature (HPHT) services4. The absence of a weld seam eliminates a potential metallurgical discontinuity that could act as a stress raiser or a preferential site for failure initiation under intense internal pressure or severe thermal stress and cycling. Power generation plants, for instance, rely heavily on seamless pipes for critical components like main steam lines, reheater tubes, and superheater tubes within boilers. Here, steam can reach temperatures exceeding 600°C (1112°F) and pressures significantly above 250 bar (3625 psi) in ultra-supercritical (USC) plants. Materials like ASTM A335 Grades P91, P92, or P911 (chrome-moly alloy steels) in seamless form are standard for these applications due to their exceptional creep strength, resistance to graphitization, and steam oxidation resistance at such elevated temperatures. I recall a consultation with an engineering firm designing a new USC power plant in India; the material specifications for the high-energy piping systems were rigidly non-negotiable – only seamless pipes could provide the required safety margins and operational lifespan under such demanding conditions. The uniform wall thickness and consistent material properties of seamless pipes ensure predictable performance and minimize the risk of catastrophic rupture, which could have dire consequences. The Electric Power Research Institute (EPRI) has extensive research highlighting the importance of material homogeneity for long-term HPHT performance.
Similarly, in the oil and gas industry, seamless pipes are indispensable for drilling operations (e.g., drill pipes, heavy weight drill pipes, drill collars), production tubing, casing, and the transportation of hydrocarbons, especially in challenging upstream and midstream sectors. Oil Country Tubular Goods (OCTG) are predominantly seamless due to the extreme downhole pressures (which can exceed 1000 bar or 15,000 psi in deep wells), high tensile loads experienced during drilling and completion, and often corrosive downhole environments (e.g., presence of H2S, CO2, and chlorides in sour gas or oil). API 5L (for line pipe), API 5CT (for casing and tubing), and API 5D (for drill pipe) are common standards governing these seamless pipes. MFY has supplied specialized seamless alloy pipes, including chrome and nickel-based alloys, to projects in challenging offshore environments in the Middle East and for onshore operations in Russia dealing with arctic conditions where material toughness at extremely low temperatures, combined with high operational pressures, made seamless the only reliable option. A failure in a high-pressure gas pipeline or a deep-well casing could have devastating environmental, safety, and economic consequences, making the inherent robustness of seamless pipes a critical safety feature. According to market reports from firms like Wood Mackenzie, the demand for high-grade seamless OCTG products is directly correlated with the increasing complexity, depth, and harshness of new oil and gas exploration and production projects.
The chemical and petrochemical industries also heavily rely on seamless pipes for critical equipment such as reactors, reformers, ethylene cracking furnace tubes, and critical process lines handling hazardous, flammable, or highly corrosive fluids at elevated temperatures and pressures. The metallurgical consistency of seamless pipes ensures better, more uniform resistance to various forms of corrosion, including stress corrosion cracking (SCC), pitting, and intergranular corrosion, which can be exacerbated by the residual stresses and microstructural changes potentially present in or near weld seams of less optimized welded pipes. For example, in processes involving highly corrosive acids (like sulfuric or nitric acid), lethal substances (like phosgene), or high-pressure synthesis reactions (like ammonia or methanol production), even a minor imperfection or inconsistency in a weld could lead to rapid localized corrosion, leakage, and potentially catastrophic failure. MFY often supplies seamless stainless steel grades like 304H, 316H, 310S, 347H, or various duplex and super duplex stainless steels for such critical applications where the combination of pressure, temperature, and corrosivity demands the absolute highest level of material integrity and predictability.
Critical Applications Requiring Uniformity, Reliability, and Precision
Beyond just HPHT conditions, seamless pipes are favored in a multitude of applications where material uniformity, predictable behavior under stress, dimensional precision, and absolute reliability are critical. Hydraulic systems, for example, often operate at very high pressures (commonly 200-700 bar, or 3000-10000 psi, and even higher in specialized systems) and require tubing with precise dimensions (especially OD and ID for fitting integrity and cylinder performance) and a smooth internal finish to ensure efficient fluid flow, minimize pressure drops, and prevent leaks. Seamless hydraulic tubes, manufactured to standards like DIN 2391 St37.4 NBK (Normalized, Bright, Annealed, Cold-drawn) or stainless steel grades under ASTM A269/A213, provide the necessary burst strength, fatigue resistance for high-cycle operations, and dimensional accuracy for demanding hydraulic cylinders, high-pressure fluid power lines, and fuel injection systems. I remember a case with an equipment integrator specializing in heavy-duty mining machinery; they switched to MFY’s cold-drawn seamless hydraulic tubing after experiencing premature fatigue failures with a lower-specification welded alternative in their high-cycle hydraulic excavators. The superior fatigue life and consistency of our seamless tubes significantly improved the reliability and operational uptime of their equipment.
Another significant area is in the manufacturing of bearings, axles, and other precision mechanical components. Seamless mechanical tubing (e.g., manufactured to ASTM A519 for carbon and alloy steel, or ASTM A511 for stainless steel) is often used as the raw material or near-net shape precursor because its uniform structure, consistent machinability, and tight dimensional tolerances (especially after cold drawing) are essential for subsequent machining operations and for ensuring the performance, load-bearing capacity, and longevity of the final component. The automotive industry, for instance, uses seamless tubes for critical components like drive shafts, axles, steering columns, and suspension components where high torsional strength, fatigue resistance, and predictable failure modes (if overloaded) are crucial for safety. The absence of a weld seam ensures that the material properties are consistent around the entire circumference and along the length, which is vital for components subjected to complex dynamic loads and stresses. One of our MFY clients, a Tier 1 automotive supplier, relies on our precision seamless tubes for producing airbag inflator bodies, where burst strength consistency is a life-critical parameter.
Furthermore, in nuclear applications, the exceptionally stringent safety and quality requirements almost exclusively dictate the use of seamless pipes and tubes for primary coolant systems, secondary steam systems, fuel element cladding, and other critical functions within the nuclear island. The need to reliably contain radioactive materials and withstand demanding operational conditions (including radiation exposure, high temperatures, and pressures) leaves virtually no room for the potential vulnerabilities or increased inspection complexities associated with welds in such critical zones, however high their quality might be. The documentation, traceability, and quality assurance requirements for materials in the nuclear industry (e.g., ASME Section III N-Stamp) are among the most rigorous globally, and seamless pipes, with their inherently simpler material pedigree, often have a more straightforward path to meeting these comprehensive quality assurance standards. Data from nuclear regulatory bodies like the NRC (U.S. Nuclear Regulatory Commission) consistently emphasizes the importance of material homogeneity and proven integrity in preventing failures in critical systems.
Applications Demanding Specific Metallurgical Purity or Specialized Performance
Certain specialized applications require the unique metallurgical characteristics or performance attributes best achieved, or most reliably guaranteed, through the seamless manufacturing route. For instance, pipes intended for high-pressure hydrogen service at elevated temperatures and pressures, commonly found in refineries (hydrocrackers, hydrotreaters) and ammonia plants, often need to be seamless and made from specific chrome-moly alloys (like 1.25Cr-0.5Mo, 2.25Cr-1Mo, up to 9Cr-1Mo-V) to resist hydrogen attack (Nelson curves provide guidance) and hydrogen-induced cracking (HIC). While welded options exist with extremely stringent controls on welding consumables, procedures, and post-weld heat treatment, seamless pipes provide an additional layer of confidence due to their inherent homogeneity, minimizing potential pathways for hydrogen diffusion, accumulation, and subsequent embrittlement or blistering, which could be more prevalent at microstructural discontinuities associated with welds. A comprehensive study by the Materials Technology Institute (MTI) on hydrogen attack mechanisms often points to non-metallic inclusions and microstructural discontinuities as potential initiation sites, risks that are inherently lower or more uniformly distributed in high-quality seamless products.
Moreover, for applications requiring exceptionally smooth internal surfaces to minimize friction (e.g., in pneumatic conveying), prevent deposit buildup (e.g., in pharmaceutical or bioprocessing), or ensure ultra-high purity conditions (e.g., in semiconductor manufacturing gas delivery systems), cold-drawn seamless (CDS) stainless steel tubes, often followed by electropolishing, are frequently preferred. While electropolished welded tubes can also achieve very smooth surfaces, the base seamless tube provides a more uniform substrate for such demanding finishing processes, without any concern about the internal weld bead profile, however minimal it might be. MFY has worked with clients in the semiconductor industry in Southeast Asia where the purity of specialty gases conveyed through our electropolished seamless stainless steel tubes (often 316L grade, with surface roughness Ra < 0.25 µm) was absolutely critical to their microchip manufacturing yields. The absence of any internal weld bead or associated HAZ meant fewer potential sites for particle entrapment, moisture adsorption, or outgassing, ensuring the highest level of process integrity.
The following table highlights key sectors and compelling reasons for choosing seamless pipes:
Industry/Application Sector | Key Drivers & Reasons for Seamless Pipe Choice | Common Materials/Standards Examples |
---|---|---|
Power Generation (HPHT Steam) | Extreme pressure/temperature, creep resistance, long-term safety, thermal fatigue | ASTM A335 (P11, P22, P91, P92), A213 (Boiler Tubes) |
Oil & Gas (Upstream/Midstream) | Extreme downhole/pipeline pressures, H2S/corrosive environments, OCTG integrity | API 5L (X-grades), API 5CT (J55, N80, P110+), API 5D |
Chemical/Petrochemical (Critical) | Aggressive/hazardous media, HPHT reactions, safety, uniform corrosion resistance | ASTM A312/A376 (SS 304H, 316H, 310S, 347H), Duplex/Super Duplex SS |
Hydraulic & Pneumatic Systems | Very high operating pressures, fatigue resistance, dimensional precision, reliability | DIN 2391 (CS), EN 10305-1/4, ASTM A269/A213 (SS) |
Mechanical Engineering (Precision) | Strength, machinability, dimensional accuracy for bearings, shafts, gears, etc. | ASTM A519 (CS/Alloy), ASTM A511 (SS) |
Nuclear Industry (Critical Safety) | Extreme safety standards, reliability, radiation resistance, QA traceability | ASME Section III (NCA, NB, NC, ND), specific proprietary alloys |
Specialized (e.g., Hydrogen Service) | Resistance to specific attack mechanisms (hydrogen embrittlement), ultra-purity | Cr-Mo alloys (ASTM A335 P5, P9, P22), EP Grade SS (ASTM A270 S2, A632) |
In summary, seamless pipes carve out their essential niche in applications where the cost of failure (in terms of safety, environmental impact, or economic loss) is unacceptably high, and where the operational conditions demand the utmost in material integrity, uniformity, predictable performance, and long-term reliability. While they may represent a higher initial investment, their proven performance and robustness in these critical scenarios often translate to lower life-cycle costs, enhanced safety, and peace of mind for operators and engineers alike – a value proposition MFY consistently delivers to its clients in these demanding sectors.
Seamless pipes resist hydrogen attackTrue
Special chrome-moly alloy seamless pipes are preferred for high-pressure hydrogen service due to their homogeneous structure that minimizes hydrogen diffusion pathways.
Welded pipes equal seamless in HPHTFalse
Seamless pipes' weld-free structure provides superior performance in high-pressure high-temperature applications by eliminating potential weak points at weld seams.
In what scenarios are welded pipes the preferable choice?
Overspending on over-specified seamless pipes for applications where welded pipes suffice? This common mistake drains budgets without adding real value. Identifying when welded pipes are the smarter, cost-effective choice can optimize project resources and enhance competitiveness.
Welded pipes are preferable for lower-pressure applications, structural uses, general fluid conveyance (water, air), and situations where cost-effectiveness is crucial. Their good dimensional accuracy, wide availability, and lower price make them ideal for many industrial and construction projects.
While seamless pipes undoubtedly hold the crown in high-stakes, extreme environments, it's crucial to recognize that for a vast array of common industrial and commercial applications, welded pipes offer an optimal blend of reliable performance, manufacturing versatility, and significant economic advantage. Dismissing modern welded pipes based on outdated perceptions of seam quality or limited capability would be a disservice to the remarkable advancements in welding technology5 and stringent quality control processes employed by reputable manufacturers like MFY. We frequently advise our diverse clients – from distributors in Southeast Asia looking for cost-effective stock solutions to manufacturing companies in India needing dependable general-purpose piping for their plant utilities – on the substantial benefits of choosing high-quality welded pipes6. The advancements in Electric Resistance Welding (ERW), High-Frequency Induction (HFI) welding, and Submerged Arc Welding (SAW), coupled with rigorous non-destructive testing, have produced welded pipes that are not only highly reliable but also offer distinct advantages in terms of dimensional consistency, surface finish, and availability for many standard applications. Let's delve into the specific scenarios where welded pipes are not just a viable alternative, but often the most intelligent, practical, and economically sound solution.
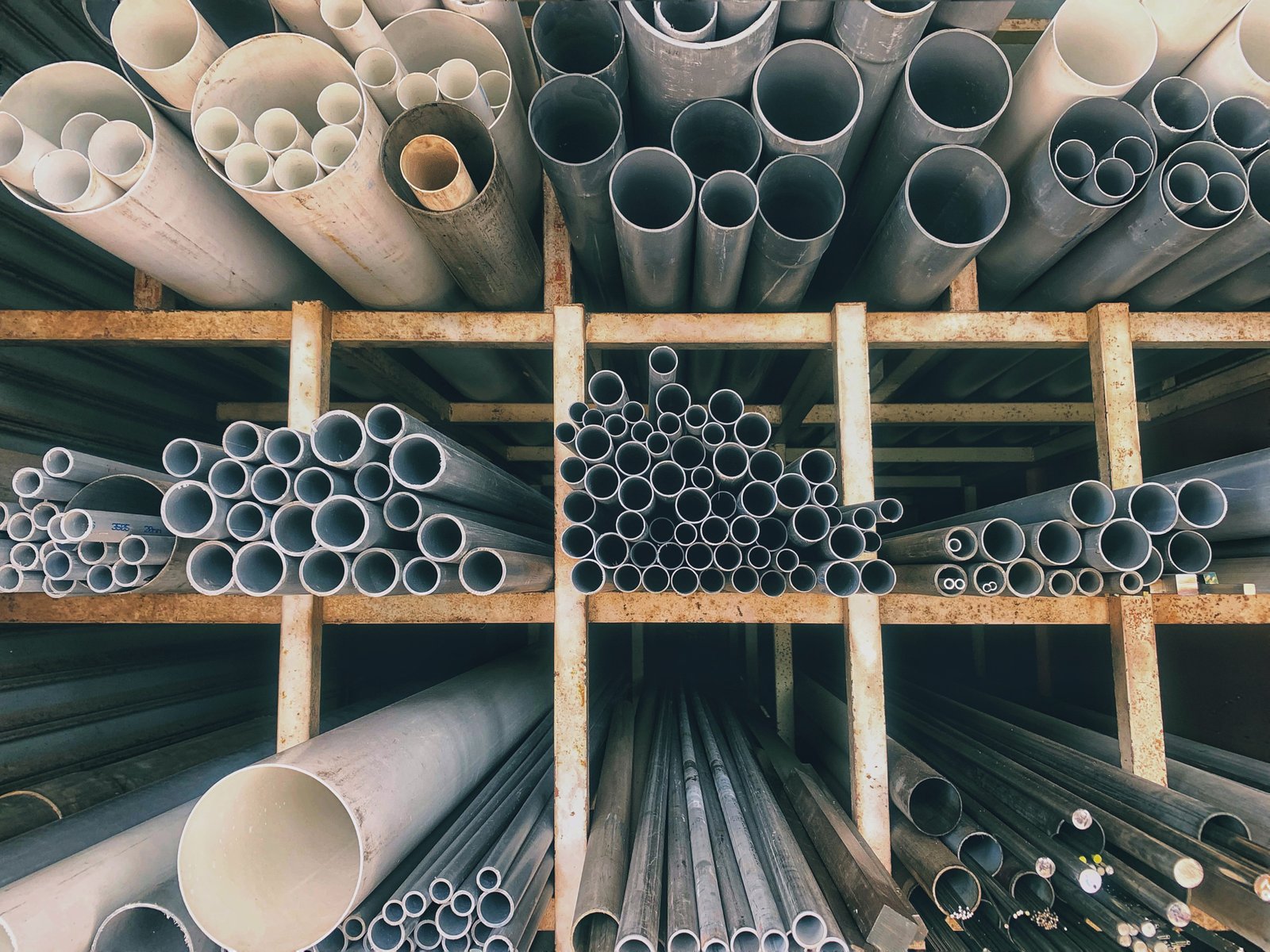
Welded pipes, manufactured by forming steel strip or plate into a cylindrical shape and then joining the edges through various highly controlled welding processes, represent a versatile and economically sound choice for a multitude of applications across countless industries. While they might not always be suitable for the most extreme pressure or temperature conditions where the inherent homogeneity of seamless pipes is paramount, modern welded pipes, produced with advanced technologies like Electric Resistance Welding (ERW), High-Frequency Induction (HFI) welding, Laser Welding, or Submerged Arc Welding (SAW), offer excellent and predictable performance characteristics for a broad spectrum of industrial, commercial, and structural uses. As a major global supplier of stainless steel piping solutions, MFY often highlights the strategic advantages of welded pipes, especially when meticulously balancing performance requirements with budgetary constraints and project timelines. I've personally seen many projects, for instance, with equipment integrators where switching from an over-specified seamless tube to an appropriate MFY welded tube7 for a less critical component saved them significant costs without any compromise on the component's function or lifespan.
Cost-Effectiveness and Availability for General and Large-Scale Applications
One of the most compelling and frequently decisive reasons to choose welded pipes is their inherent cost-effectiveness. The manufacturing process for welded pipes is generally more efficient, faster, and less material-intensive than that for seamless pipes. Starting with steel coils or plates, which are readily available in vast quantities and often less expensive per unit weight than the specially prepared solid billets required for seamless production, allows for higher production speeds and better material yield (less scrap). This efficiency translates directly into lower per-unit costs, making welded pipes an extremely attractive option for projects with tight budgets or where very large quantities of piping are required. For example, MFY regularly supplies ERW stainless steel pipes (e.g., conforming to ASTM A312 welded condition, ASTM A269 for general purpose tubing, or ASTM A778 for larger diameter unannealed austenitic products) to construction contractors and manufacturing companies across our export markets in Southeast Asia and India for applications like plant utility water systems, drainage networks, general plumbing, and low-pressure process lines. In these numerous scenarios, the operating pressures and temperatures are well within the established capabilities of quality welded pipes, and the significant cost savings compared to seamless alternatives (often ranging from 15% to 40% or more, depending on size, material, and quantity) allow for much better resource allocation across the entire project. Industry benchmarks consistently show that for common grades of carbon steel and standard austenitic stainless steels, welded pipes offer a substantial economic advantage for a large percentage of piping footage installed globally.
Furthermore, welded pipes are often available in a wider range of diameters and potentially longer continuous lengths, particularly for very large diameters which can be exceptionally challenging or prohibitively expensive to produce seamlessly. Processes like longitudinal submerged arc welding (LSAW) or spiral submerged arc welding (SSAW) are well-suited for manufacturing large-diameter pipes (e.g., from 20 inches up to 100 inches or even more) used in major water transmission mains, large-scale industrial ducting, penstocks for hydroelectric plants, or as structural pilings for bridges and marine structures. I recall a significant project in the Middle East requiring extensive large-bore (e.g., 36-inch and 48-inch) stainless steel piping for a new industrial water treatment and distribution facility8; MFY's LSAW pipes provided the necessary scale, required corrosion resistance, and performance characteristics at a competitive price point that would have been unachievable with seamless technology for those dimensions. The general availability from stockists and distributors is also typically better for common sizes and grades of welded pipes due to higher overall production volumes and broader demand in general service applications. This is a key factor for our MFY distributor clients who need to maintain responsive inventory levels.
The speed of production for many types of welded pipes can also be a critical advantage for projects with tight schedules or urgent requirements. Continuous ERW/HFI mills can produce standard-sized pipes at a much faster linear rate than most seamless mills, facilitating quicker order fulfillment for standard items and larger project quantities. This manufacturing agility is something our clients, particularly engineering and construction contractors facing pressing deadlines, highly value when sourcing materials.
Applications Requiring Excellent Dimensional Tolerances and Specific Surface Finishes
Modern welded pipe manufacturing processes, especially those utilizing precision cold-formed steel strip and advanced welding techniques like HFI or laser welding, can produce pipes with exceptionally good dimensional accuracy. This is particularly notable in terms of wall thickness uniformity and concentricity. The wall thickness of an ERW/HFI welded pipe is primarily determined by the precision-rolled strip from which it is formed, and modern steel mills can control strip thickness very tightly (e.g., within +/- 0.1 mm for thinner gauges). This uniformity can be highly advantageous in applications where precise flow characteristics are needed, where weight is a critical design parameter (e.g., in transportation or aerospace, though those are specialized niches), or where consistent fit-up for automated welding is required. For example, MFY supplies welded stainless steel tubes conforming to standards like ASTM A249 (for boiler, superheater, heat exchanger, and condenser tubes) or ASTM A269 for less critical heat exchanger and condenser applications. While seamless tubes are the default for high-pressure/temperature exchangers, many moderate-duty units in various industries can effectively and economically utilize welded tubes, which often offer superior wall thickness control compared to standard hot-finished seamless tubes, potentially leading to more predictable heat transfer performance and lighter overall unit weight.
The surface finish of welded pipes, especially those made from cold-rolled stainless steel strip, can also be inherently superior (smoother and brighter) to that of typical hot-finished seamless pipes, often requiring less subsequent polishing for aesthetic or functional purposes. This makes them highly suitable for applications where aesthetics are important or where a specific level of hygiene is required. For instance, MFY provides large quantities of polished welded stainless steel pipes (e.g., with a #4 brushed finish, or a #8 mirror polish) for architectural applications like handrails, balustrades, column cladding, and decorative elements in commercial buildings, airports, and public spaces across our export markets. Similarly, in the food and beverage industry, and increasingly in pharmaceuticals for less critical applications, welded stainless steel pipes (often manufactured to ASTM A270 for sanitary tubing) are widely used. The internal weld bead, a key consideration for hygiene, can be cold-worked (hammered or rolled down) and then ground and polished to create a smooth, crevice-free internal surface that meets stringent hygienic standards (e.g., 3-A Sanitary Standards in the US). We worked closely with a major dairy processing plant in India to supply such sanitary welded tubes, where ease of cleaning (CIP/SIP compatibility) and the prevention of bacterial adhesion and growth were paramount. The consistent surface finish achieved on our MFY welded tubes was a critical factor in their selection.
Moreover, the excellent consistency of shape (roundness) and outside diameter in high-quality welded pipes facilitates easier and more efficient fabrication and assembly. Automatic orbital welding machines, commonly used in constructing high-purity piping systems or in mass production of piped assemblies, often perform better and yield more consistent weld quality with pipes that have highly consistent outside diameters and roundness – attributes commonly found in top-tier ERW/HFI pipes. This can lead to reduced fabrication time and lower overall installed costs.
Structural and Low-to-Medium Pressure Conveyance Applications: The Workhorse of Industry
A vast majority of structural applications across construction and manufacturing utilize welded pipes and, more specifically, Hollow Structural Sections (HSS), which are predominantly produced by welding. Their favorable strength-to-weight ratio, combined with lower cost, good formability into various shapes (round, square, rectangular), and excellent weldability for creating complex connections, makes them ideal for building frames, bridges, trusses, support structures for equipment, and mechanical frameworks. Standards like ASTM A500 (for cold-formed welded and seamless carbon steel structural tubing in rounds and shapes) and EN 10219 (for cold-formed welded structural hollow sections of non-alloy and fine grain steels) are prevalent in this domain. MFY has supplied such structural tubes, including stainless steel variants for corrosive environments or architectural appeal, to numerous construction projects where engineers leverage the predictable mechanical properties and wide range of available profiles of welded HSS to create efficient and durable structures. The presence of a weld seam in these applications is generally not a limiting factor for structural integrity when the design appropriately considers its properties and the connection details are correctly executed as per structural welding codes (e.g., AWS D1.1).
For low to medium-pressure fluid conveyance, welded pipes are truly the workhorse of many industries. This includes extensive systems for water (potable water, industrial process water, cooling water, wastewater), compressed air lines, low-pressure steam and condensate return, various oils and lubricants, and a multitude of general process fluids where the operating conditions do not necessitate the premium performance (and associated cost) of seamless pipes. For instance, manufacturing companies of all sizes often use welded carbon steel pipes (e.g., conforming to ASTM A53 Type E [ERW] or Type F [Furnace-butt weld], or EN 10255) or, for better corrosion resistance, welded stainless steel pipes (e.g., ASTM A312 welded, Schedule 10S or 40S) for their plant utility lines. The cost savings are substantial, and the performance is entirely adequate and reliable for these services. I've seen countless MFY clients, from small factories in Southeast Asia to large industrial complexes in Russia, successfully implement extensive networks of welded piping for these general services, achieving reliable long-term operation without over-engineering the solution and thereby optimizing their capital expenditure. Data from global piping industry associations consistently indicates that welded pipes constitute a significant majority (often estimated at 70-80% or more) of the total tonnage of pipes used globally, underscoring their widespread suitability and economic importance for these common but essential applications.
The table below offers a snapshot of common scenarios where welded pipes are often the preferable and more sensible choice:
Scenario / Application Type | Key Reasons for Preferring Welded Pipe | Common Materials/Standards Examples |
---|---|---|
General Fluid Conveyance (Low/Med Pressure) | Cost-effective, good availability, adequate pressure rating for water, air, mild chemicals | ASTM A53 (CS), EN 10255 (CS), ASTM A312 (SS, welded), ASTM A778 (Large Dia SS) |
Structural Applications (HSS/Pipes) | Excellent strength-to-weight ratio, lower cost, formability (shapes), good weldability for connections | ASTM A500 (CS HSS), EN 10219 (CS HSS), SS structural tubes (e.g., ASTM A554) |
Architectural/Decorative Uses | Superior surface finish (from cold-rolled strip), dimensional consistency, cost, polishability | Polished SS (e.g., 304, 316, conforming to ASTM A554 for ornamental tubing) |
Low-Pressure Heat Exchangers/Condensers | Good wall thickness control (from strip), better cost for moderate duties | ASTM A249/A269 (SS), ASTM A178/A214 (CS for heat exchangers) |
Food & Beverage (Sanitary Tubing) | Hygienic surface finish (polished internal weld), cost-effective for sanitary lines | ASTM A270 (SS Sanitary Tubing), EN 10357 |
Automotive Exhaust Systems | Formability, lower cost for moderate temperature and corrosion resistance requirements | Aluminized steel, ferritic SS (e.g., Type 409, 439) |
Large Diameter Water Mains/Ducting | Manufacturability in very large sizes (SAW/SSAW), significant cost advantage per meter | AWWA C200 (CS for water), ASTM A134/A139 (CS EFSW/ERW), Large SS welded options |
General Industrial Piping (Non-critical) | Balance of performance and economy for utilities, drains, less demanding process lines | Various CS and SS welded pipe standards applicable to specific industry needs |
In essence, welded pipes emerge as the pragmatic, versatile, and often economically superior choice when extreme performance under severe conditions is not the primary design driver, and factors like initial cost, specific dimensional accuracy needs (like wall uniformity), surface finish requirements, or the necessity for very large diameters take precedence. The key, as always, is a proper and thorough engineering assessment of the specific service conditions to ensure that a high-quality welded pipe from a reputable manufacturer like MFY can meet all the design demands safely, reliably, and for the intended service life of the system.
Welded pipes are cost-effective for low-pressure applicationsTrue
Welded pipes offer significant cost savings (15-40%) compared to seamless pipes for applications like water systems and drainage networks where extreme pressure resistance isn't required.
Seamless pipes always have better dimensional accuracyFalse
Modern welded pipes often achieve superior wall thickness uniformity and concentricity compared to standard hot-finished seamless pipes, especially when made from precision-rolled strip.
What are the recommendations for choosing between seamless and welded pipes?
Overwhelmed by pipe choices and afraid of making a costly error? Incorrect selection leads to project delays, budget overruns, or even safety hazards. Clear, actionable recommendations can guide you to the optimal pipe, ensuring both performance and economic efficiency.
Choose seamless pipes for high-pressure, high-temperature, critical safety, or highly corrosive applications demanding maximum integrity. Opt for welded pipes for lower-pressure, structural, general fluid conveyance, or cost-sensitive projects where their good dimensional control and lower price offer better overall value. Always verify against governing industry standards and codes.
Navigating the crucial decision between seamless and welded pipes requires more than just a cursory glance at technical specifications or price lists; it demands a holistic and meticulous understanding of your project's unique operational demands, the surrounding environmental conditions, long-term performance objectives, and inherent safety implications. As someone who has consistently guided countless MFY clients through this very selection process – from large, sophisticated engineering contractors in Russia meticulously planning complex petrochemical plants to dynamic distributors in India stocking for diverse local industrial needs, and manufacturing companies across Southeast Asia optimizing their plant designs – I can attest that the "right" choice is rarely a simple black and white determination. It's almost always about achieving a careful, well-informed balance, judiciously weighing critical factors like maximum operating pressure, design temperature ranges, the precise nature and corrosivity of the fluid being conveyed, potential safety ramifications of a failure, mandatory regulatory compliance (codes and standards), and, of course, the ever-present budgetary constraints. The ultimate goal is to arrive at a piping solution that is not only technically sound and demonstrably safe but also economically prudent and sustainable over the project's lifecycle. Let's explore a systematic, multi-faceted approach to making this critical decision, ensuring you select the pipe type that truly makes the most sense for your specific scenario, backed by established industry best practices, sound engineering principles, and practical field experience from MFY's global operations.
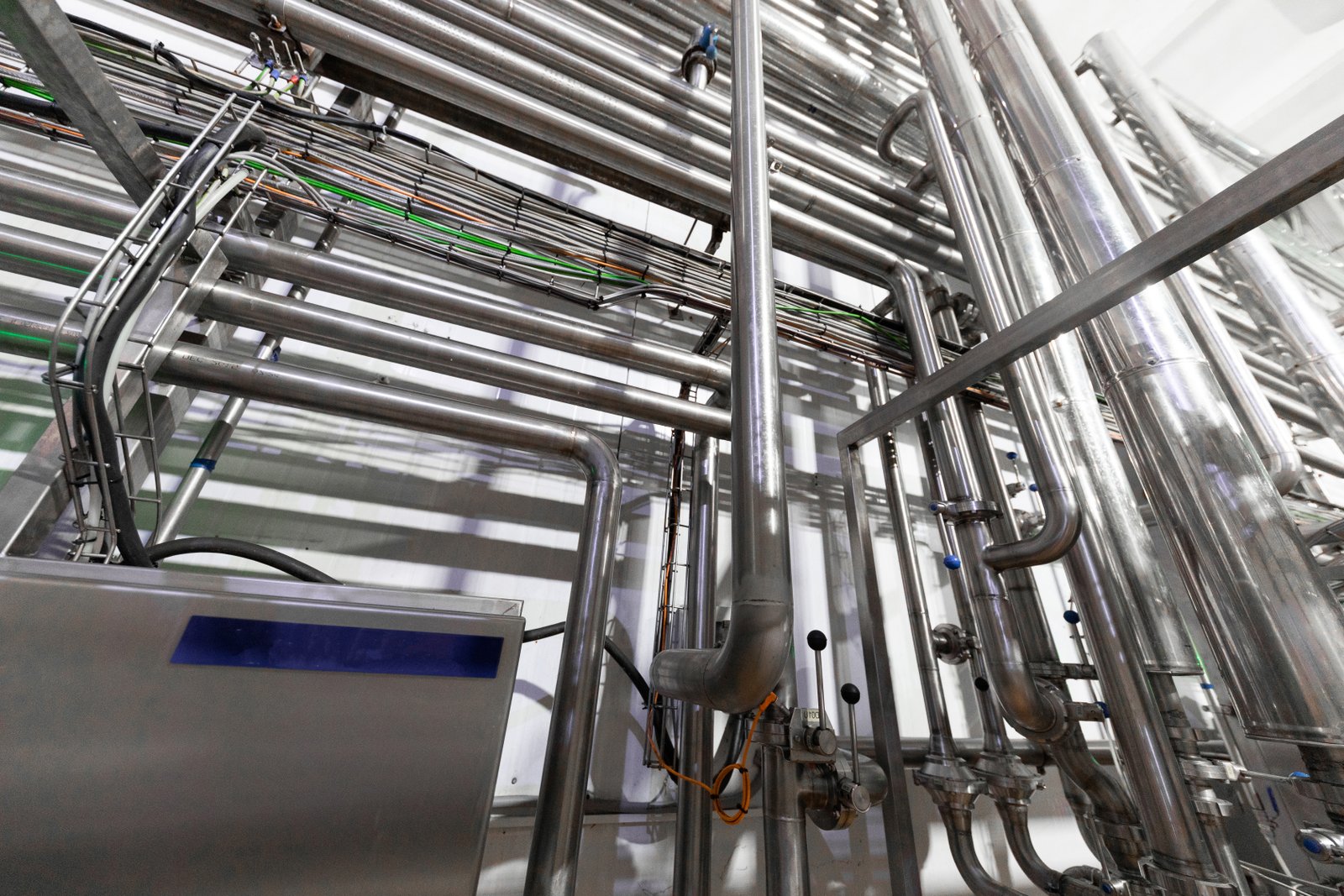
Choosing between seamless and welded pipes is a critical engineering and procurement decision that can significantly impact a project's safety, operational reliability, longevity, and overall lifecycle cost. There's no universal "better" option; the optimal choice is always context-dependent9, hinging on a detailed evaluation of specific application requirements. At MFY, our collaborative approach with clients involves a thorough assessment of various interdependent factors to guide them towards the most suitable and cost-effective stainless steel piping solution. Here are key recommendations, structured as a decision-making framework, to consider when making this selection, drawing from internationally recognized industry best practices (like those embedded in ASME, API, and EN standards) and our extensive practical experience in the global stainless steel pipe market10. I've often seen clients, for example, an equipment integrator, initially lean towards seamless for all components, but after a joint review, we identified areas where MFY's high-quality welded tubes could be safely and more economically applied, freeing up budget for other critical areas of their design.
Step 1: Rigorously Assess Operating Conditions and Crucial Safety Implications
The first and most fundamentally crucial step is to meticulously evaluate the intended service conditions of the piping system. This involves accurately quantifying the maximum (and minimum) operating pressure, the full design temperature range (including considerations for thermal cycling, start-up/shutdown transients, and potential upset conditions), and the precise nature and properties of the fluid or gas being transported (its viscosity, density, phase, and any hazardous characteristics).
For high-pressure applications (e.g., generally considered above 100 bar / 1500 psi, though this threshold varies significantly by industry, standard, and material) and high-temperature services (e.g., above 400-450°C / 750-840°F for carbon steel, or when operating within the creep range for alloy or stainless steels), seamless pipes are typically the safer, more conservative, and often mandated choice. Their homogenous, monolithic structure, entirely devoid of a weld seam, provides superior resistance to rupture, creep deformation, and fatigue under these demanding conditions. As an illustrative example, for a steam reforming process in a modern petrochemical plant, where hydrogen-rich syngas is present at temperatures often exceeding 800°C (1470°F) and significant pressures, MFY would almost invariably recommend and supply seamless heat-resistant alloy steel pipes (such as those made from HK40, HP Mod, or similar cast/wrought alloys, or specialized wrought grades like Incoloy 800HT) due to the extremely severe operating environment and the critical risks associated with hydrogen embrittlement and high-temperature hydrogen attack (HTHA), which could be significantly exacerbated at any weld discontinuity. A formal Process Hazard Analysis (PHA) or risk assessment should always be conducted for critical systems; if pipe failure could lead to catastrophic consequences (e.g., release of toxic or flammable substances, explosion, major environmental damage, or prolonged, costly shutdowns), the inherent, proven integrity of seamless pipes often justifies their higher initial cost. Codes like ASME B31.3 Process Piping explicitly address design considerations for severe cyclic conditions or very high-pressure designs, which might inherently favor or even mandate seamless construction, or apply more stringent limitations or examination requirements for welded pipes.
Conversely, for low to moderate pressure and temperature applications, such as general industrial water lines, plant air systems, HVAC chilled/hot water circuits, low-pressure process streams, or structural supports, high-quality welded pipes (ERW, HFI, or SAW depending on size, material, and specific need) often provide perfectly adequate, reliable performance at a significantly lower installed cost. For instance, a food processing client in Southeast Asia requiring stainless steel piping for product transfer lines operating at ambient temperature and pressures below 10 bar (145 psi) found MFY’s ASTM A270 sanitary welded tubes to be an ideal and compliant solution, offering the necessary hygiene, corrosion resistance, and cleanability without the premium price associated with seamless alternatives for such a duty. The key is always to ensure that the selected welded pipe's design pressure rating, as determined according to relevant standards (e.g., calculations based on allowable stress values from ASME B31.3 or other applicable codes, considering dimensional standards like ASME B36.10M/B36.19M, and material-specific ASTM/EN standards for properties), provides a sufficient and clearly defined safety margin for the maximum anticipated operating conditions. MFY provides all necessary documentation to support these calculations.
Don't forget to consider external pressures or mechanical loads. For buried pipelines subject to significant soil loads, traffic loads, or differential settlement, or for subsea pipelines under substantial external hydrostatic pressure, the structural integrity and resistance to buckling and collapse are key design parameters. While both seamless and welded pipes can be used effectively, the specific design calculations, accounting for factors like D/t ratio (diameter to thickness) and material yield strength, will guide the choice, and sometimes the thicker, more uniform walls achievable with certain seamless products or specialized welded pipes (like UOE-formed LSAW) might be advantageous.
Step 2: Evaluate Corrosion Concerns, Material Compatibility, and Product Purity
The corrosivity of the fluid being conveyed (internal corrosion) and the external environment (external corrosion) is a major determinant in material selection, which in turn influences the seamless vs. welded decision. While both seamless and welded pipes can be manufactured from a wide range of corrosion-resistant alloys, including numerous grades of stainless steel (austenitic, ferritic, duplex, super duplex), nickel alloys, and titanium, the presence of a weld seam in welded pipes can sometimes introduce a preferential site for certain types of localized corrosion if the welding process, filler material (if used), or post-weld treatment is not perfectly optimized for the specific service environment.
For highly corrosive environments or fluids known to cause issues like preferential weld attack, intergranular corrosion (IGC) in sensitized zones, or stress corrosion cracking (SCC) – particularly where weld-related residual stresses or microstructural alterations (like sigma phase formation in some duplex stainless steels if cooling is too slow post-weld) could be problematic – seamless pipes generally offer a more uniform and predictable resistance profile. For example, handling wet chlorine gas, certain concentrated strong acids (like hot sulfuric acid), or specific organic chloride solutions might favor seamless construction, especially in higher nickel alloys or reactive metals where achieving perfect weld immunity across a range of conditions can be challenging. I recall a client in the specialty chemical industry who experienced premature failures in a welded pipeline carrying a specific acidic slurry; switching to seamless pipes of the same alloy grade, as recommended by MFY after a detailed failure analysis and corrosion testing, resolved the persistent issue by eliminating the weld zone as the primary corrosion initiation point. Authoritative resources like the NACE International (now AMPP) Corrosion Engineer's Reference Book provide extensive data on material performance in various corrosive media, often highlighting potential differential behavior at weldments versus base metal.
However, for a vast range of moderately corrosive services, modern, high-quality welded stainless steel pipes (e.g., made from common grades like 304L, 316L, or duplex grade 2205) with proper, certified welding procedures and appropriate post-weld treatment (such as solution annealing and quenching for full austenitic restoration, if required by the application or standard, followed by thorough cleaning and passivation) can perform excellently and provide a service life equivalent to seamless pipes. The low carbon content ('L' grades, with C ≤ 0.030%) in austenitic stainless steels significantly minimizes the risk of sensitization and subsequent intergranular corrosion in the HAZ during welding. MFY ensures that our welded stainless steel pipes meet stringent quality controls, including proper welding procedures (WPS/PQR), qualified welders, correct filler metal selection (if applicable), and, where specified, appropriate post-weld heat treatment and surface passivation. This makes them highly suitable for a wide range of applications, including many chemical processing lines, food and beverage contact surfaces, pharmaceutical utility systems, and pulp and paper industry processes. For instance, for brewery applications requiring hygienic conditions and resistance to cleaning solutions (CIP/SIP), MFY routinely supplies welded 304L or 316L stainless steel pipes that provide excellent corrosion resistance and a smooth internal finish, often at a better price point than seamless.
Always ensure the chosen pipe material itself (e.g., 316L SS vs. Alloy C276 vs. Carbon Steel) is fundamentally compatible with the service environment and product purity requirements. This material selection decision precedes the seamless vs. welded choice but strongly influences it. For some exotic alloys that are notoriously difficult to weld perfectly without altering their corrosion properties or mechanical integrity, seamless might be the only practical or reliable option to ensure consistent, as-specified performance. Conversely, some materials are readily weldable with excellent results.
Step 3: Consider Total Cost of Ownership, Availability, Project Timelines, and Specific Fabrication Needs
Budgetary constraints and overall project economics are practical realities in every project. As has been discussed, seamless pipes are generally more expensive on a per-unit basis than welded pipes of the same material, size, and nominal wall thickness. This cost premium can range significantly, from as little as 10-20% for some common items to over 100% or much more for very large diameters, heavy walls, or specialized alloys where seamless production is particularly complex or has lower yields. Therefore, a thorough Total Cost of Ownership (TCO) analysis is essential, not just an initial price comparison. TCO should consider initial purchase cost, installation costs (which can be affected by dimensional consistency and weldability), inspection requirements (welded pipes may require more extensive NDT of the seam), anticipated maintenance, expected lifespan, and the cost/consequence of potential failure. If a high-quality welded pipe can safely and reliably meet all the design, operational, and lifespan requirements of a system, then opting for a more expensive seamless pipe would represent an unnecessary expenditure of capital. MFY often helps clients, especially Engineering, Procurement, and Construction (EPC) contractors and end-users working on competitive bids or budget-constrained projects, to identify areas where MFY's certified welded pipes can be confidently used without compromising safety or long-term quality, thereby optimizing overall project costs. A typical scenario is a large industrial plant construction project (e.g., in India or Southeast Asia), where using cost-effective welded stainless steel for general utilities, firewater systems, and moderate process lines, while reserving the premium seamless pipes for the truly critical high-pressure/high-temperature or severely corrosive circuits, offers the best economic and engineering balance.
Availability and manufacturing lead times can also be significant influencing factors in the decision-making process. Common sizes and standard grades of welded pipes are often more readily available from MFY's inventory or from general stockists, or they typically have shorter manufacturing lead times compared to seamless pipes. This is especially true for very large diameters or non-standard wall thicknesses in seamless, which might require special mill rollings with long lead times. If a project has an urgent timeline or if a quick replacement is needed for an existing line, the quicker availability of a suitable and certified welded pipe might make it the preferred practical choice, provided it meets all the non-negotiable technical and safety requirements. MFY leverages its integrated supply chain, flexible production capacity, and strategic inventory management to offer competitive lead times for both seamless and welded stainless steel pipes, but market dynamics and specific order complexities can sometimes favor one over the other in terms of delivery speed.
Finally, consider specific project requirements such as the need for extremely tight dimensional tolerances, particular surface finish characteristics (internal or external), ease of fabrication, or specific end preparations. If exceptionally tight wall thickness control or OD/ID precision is paramount, a cold-drawn seamless (CDS) tube or a high-quality ERW/HFI welded and sized/drawn tube might be superior to a standard hot-finished seamless pipe. If a very smooth internal surface (low Ra value) is required for hygienic reasons, to minimize friction losses, or to prevent particle adhesion in high-purity systems, then either electropolished seamless tubes or specially finished welded tubes (with meticulously ground and polished internal welds) can be considered. The choice here would depend on the absolute level of smoothness required, the diameter, and the relative costs. For example, for pneumatic conveying systems where smooth, uninterrupted flow is essential to prevent blockages, MFY might discuss the technical merits and cost implications of both CDS stainless steel tubes and high-quality welded stainless steel tubes with a controlled and smoothed internal weld bead profile. Ease of on-site welding for tie-ins and spool fabrication can also be a factor; some find the consistent OD and wall of quality ERW pipes easier for automated orbital welding.
A simplified decision matrix can be a helpful tool to summarize these considerations:
Factor Considered | Strongly Favor Seamless Pipe When... | Strongly Favor Welded Pipe When... |
---|---|---|
Operating Pressure | Very High (e.g., >150 bar / 2200 psi, critical systems, per code limits) | Low to Moderate (e.g., <70 bar / 1000 psi, general service) |
Operating Temperature | Very High (e.g., in creep range for material, >450°C for CS/low alloy) | Low to Moderate (e.g., <400°C, outside significant creep effects) |
Fluid/Environment Corrosivity | Highly aggressive, known to preferentially attack welds, high SCC/HIC risk | Mild to Moderate, or when weld/HAZ properties are proven suitable for media |
Safety / Consequence of Failure | Potential for catastrophic outcomes (toxic release, explosion, critical system loss) | Consequences are manageable, low direct risk, non-critical systems |
Cyclic Service Conditions | Severe thermal or pressure cycling, high fatigue duty, vibration is high | Mild to moderate cyclic loads, low fatigue concerns |
Initial Cost Sensitivity | Performance/Safety/Reliability far outweighs initial cost premium | High, budget constraints are a primary driver, good value needed |
Dimensional Precision Needs | Extreme precision needed (CDS option often best); or if HF seamless allows | Good general tolerances suffice; ERW/HFI often offers excellent wall uniformity |
Availability / Lead Time | Project can accommodate potentially longer lead times for special items | Urgent need for standard items, shorter lead times are critical |
Governing Codes/Standards | Specifically mandated or strongly preferred by applicable design codes | Permitted and demonstrably suitable as per applicable codes and standards |
Product Purity / Contamination | Ultra-high purity, no risk of weld-related contamination acceptable | Standard industrial purity, properly finished weld is acceptable |
Ultimately, the best and most robust recommendation is to always consult the relevant and current industry standards (ASME, API, ASTM, EN, ISO, etc.), perform a thorough engineering assessment based on sound principles, and engage transparently with experienced and reputable suppliers like MFY. We can provide valuable insights based on our broad product knowledge, manufacturing capabilities, quality certifications, and extensive application experience across diverse industrial sectors and global geographies. This collaborative approach will help you make a well-informed decision that optimally balances all critical aspects: performance, safety, regulatory compliance, and overall project economics.
Seamless pipes handle higher pressuresTrue
Seamless pipes are recommended for high-pressure applications (typically above 100 bar) due to their homogeneous structure without weld seams, which provides superior strength and resistance to rupture.
Welded pipes are always cheaperFalse
While welded pipes are generally more cost-effective, specialized welded pipes with high-quality finishes or made from exotic alloys can sometimes be more expensive than standard seamless pipes.
Conclusion
Choosing between seamless and welded pipes hinges on application specifics. Seamless excels in high-stress, critical environments demanding utmost integrity, while welded pipes offer a cost-effective, reliable solution for general-purpose, lower-pressure duties. A thorough assessment ensures optimal selection, balancing performance with project economics.
-
Learn about benefits of HFI welding technology in reducing cost and improving weld quality ↩
-
Explore industry data on pressure capacity and reliability of modern welded pipes ↩
-
Learn about industries where seamless pipe usage is essential ↩
-
Discover the benefits of seamless pipes in HPHT settings ↩
-
Discover modern welding technologies that enhance pipe strength and seam quality. ↩
-
Learn the advantages of welded pipes for industrial and construction uses. ↩
-
Understand MFY's welded tube reliability for cost-effective solutions in less demanding services. ↩
-
Explore the cost and performance benefits of LSAW pipes for large infrastructure projects. ↩
-
Understanding how specific project contexts affect piping decisions can help optimize choices. ↩
-
Gain insights into market dynamics affecting pipe availability and pricing. ↩
Have Questions or Need More Information?
Get in touch with us for personalized assistance and expert advice.