ASTM, ASME & EN Pipe Standards Explained
Are you struggling to navigate the complex world of pipe standards, unsure which one applies to your project or how they differ? This confusion can lead to costly errors and project delays. As Global Business Director at MFY, I understand these challenges intimately, and this guide will demystify ASTM, ASME, and EN standards.
ASTM, ASME, and EN pipe standards are sets of technical specifications defining material properties, manufacturing processes, dimensions, and testing requirements for pipes. They ensure safety, quality, and interoperability in various industries, with ASTM and ASME prevalent in North America and EN standards primarily used in Europe.
Navigating these standards can feel like a maze, especially when projects span international borders or involve diverse applications. At MFY, we've guided countless clients through this landscape. This article will not only explain these critical standards but also provide practical insights to help you select and apply them effectively, ensuring your stainless steel pipe projects meet all necessary requirements.
The world of industrial piping relies heavily on standardization, yet the co-existence of multiple prominent standards like ASTM, ASME, and EN can initially seem counterintuitive. Why not a single, universal standard? The answer lies in historical development, regional industrial priorities, and specific application focuses. ASTM International1 (formerly American Society for Testing and Materials) provides a vast array of consensus standards for materials, products, systems, and services. ASME (American Society of Mechanical Engineers) focuses heavily on mechanical engineering, with its Boiler and Pressure Vessel Code (BPVC) being a cornerstone for safety in pressure applications, often referencing ASTM material standards. Meanwhile, EN (European Standards or Euronorm) standards are developed by CEN (European Committee for Standardization2) to harmonize technical specifications across Europe, facilitating trade and ensuring consistent quality. As MFY expanded its stainless steel pipe exports to markets like India, Southeast Asia, and the Middle East, we quickly recognized that a deep understanding of all three was crucial. Different regions and industries often have historical allegiances or specific regulatory mandates for one over the others, making a one-size-fits-all approach impractical. For instance, a project in the Middle East might specify ASME for pressure piping, while a similar application within a European manufacturing plant would mandate EN compliance. This diversity, while complex, also allows for tailored solutions optimized for specific performance criteria, and we at MFY pride ourselves on navigating this complexity for our clients.
What is the historical background of ASTM, ASME, and EN pipe standards?
Ever wondered how these intricate pipe standards came into being and why they matter so much today? Their origins are rooted in the industrial revolutions and the growing need for safety and reliability. Understanding this history helps us appreciate their current significance in global trade and engineering.
ASTM, ASME, and EN pipe standards evolved from distinct industrial needs: ASTM from late 19th-century US rail industry material concerns, ASME from early 20th-century boiler safety imperatives, and EN standards from late 20th-century European efforts to harmonize technical specifications across member states.
The journey of these standards is a fascinating reflection of industrial progress and the relentless pursuit of quality and safety. As we delve into their individual histories, you'll see how events like boiler explosions or the need for consistent material quality in rapidly expanding industries shaped them. At MFY, we often share these historical contexts with our clients, especially those in engineering and construction, because it underscores why adherence to specific codes isn't just a regulatory hurdle but a legacy of lessons learned. For instance, when supplying stainless steel pipes for a critical application in an Indian power plant, referencing the historical development of ASME's B31.1 Power Piping code can emphasize the stringent safety requirements embedded within. This historical perspective allows for a richer understanding and a more committed approach to compliance, moving beyond mere box-ticking to a genuine appreciation for the engineering principles at play. This deeper understanding is what we aim to foster, ensuring our clients not only receive compliant products but also grasp the foundational importance of the standards governing them.
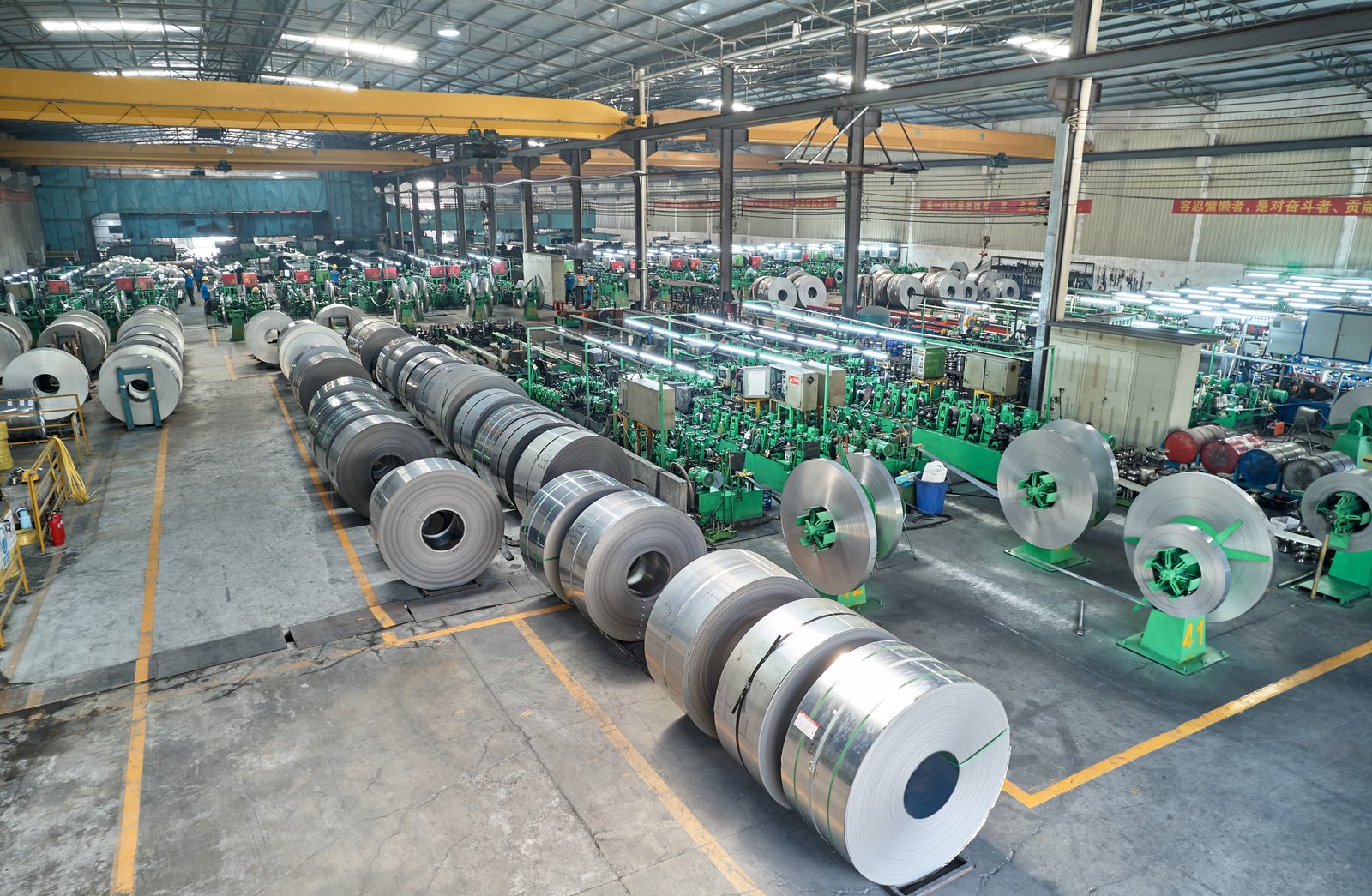
The evolution of pipe standards is a story of industrial advancement, safety imperatives, and the quest for interoperability. Each standard—ASTM, ASME, and EN—has its own unique genesis, shaped by the specific challenges and technological advancements of its time and region. Understanding this historical context is not merely an academic exercise; it provides crucial insights into their current structure, scope, and application in industries worldwide, including the stainless steel sector where MFY operates. For instance, when we at MFY discuss a particular ASTM A312 stainless steel pipe grade with a client in Southeast Asia, knowing that ASTM's roots lie in ensuring material reliability helps convey the assurance that comes with this standard. Similarly, explaining to a Middle Eastern contractor why an ASME B31.3 specification for a process plant includes certain safety factors becomes more impactful when you trace ASME's origins to preventing catastrophic failures. The European EN standards, born from a desire for economic and technical harmonization, tell another important story about facilitating trade and ensuring a common baseline of quality across diverse nations—a principle we at MFY deeply respect as we serve a global clientele. This historical awareness allows us to better anticipate client needs, explain regulatory requirements, and ultimately provide stainless steel solutions that are not just compliant but also perfectly suited to their intended purpose.
The Genesis of ASTM Standards: Responding to Industrial Demands
ASTM International, originally known as the American Society for Testing Materials, was established in 1898. Its formation was driven by the urgent need for standardized specifications for materials used in the rapidly expanding railroad industry in the United States. Scientists and engineers recognized that inconsistent material quality, particularly for steel rails, was leading to frequent failures and accidents. The initial focus was on developing standard test methods and specifications to ensure reliability and safety. As I recall from my early days in the industry, even a slight deviation in material composition could have significant consequences, a lesson learned the hard way by many pioneering companies.
Over the decades, ASTM's scope broadened dramatically beyond just steel for railroads. It now covers a vast array of materials, products, systems, and services across numerous industries, from construction and petroleum to consumer products and, of course, stainless steel pipes. Standards like ASTM A312 (Standard Specification for Seamless, Welded, and Heavily Cold Worked Austenitic Stainless Steel Pipes) and ASTM A269 (Standard Specification for Seamless and Welded Austenitic Stainless Steel Tubing for General Service) are fundamental in our daily operations at MFY. We've seen firsthand how adherence to these detailed specifications—covering chemical composition, mechanical properties, dimensions, and testing procedures—provides a common language for producers, purchasers, and users, ensuring that the stainless steel pipes we export to India or Russia meet globally recognized quality benchmarks. For example, a manufacturing client in India recently required ASTM A312 TP316L pipes for a new chemical processing line. The clarity of the ASTM standard meant that both our production team and the client’s engineers had a precise understanding of the material’s corrosion resistance, weldability, and strength characteristics, eliminating ambiguity and ensuring project success.
The development process for ASTM standards is a consensus-based one, involving input from producers, users, consumers, academics, and government representatives. This collaborative approach ensures that the standards are practical, relevant, and reflect the latest technological advancements and industry best practices. This iterative and inclusive process is why ASTM standards are so widely respected and adopted globally. At MFY, our internal quality control systems are deeply intertwined with ASTM requirements, from raw material procurement to final product inspection, providing a robust framework for delivering excellence.
ASME's Emergence: A Focus on Pressure Integrity and Safety
The American Society of Mechanical Engineers (ASME) was founded in 1880, but its most significant contribution to piping and pressure vessel standards came in the early 20th century, largely in response to a series of catastrophic boiler explosions. These incidents highlighted the critical need for robust design, construction, inspection, and testing standards for pressure-retaining equipment to protect lives and property. The first edition of the ASME Boiler and Pressure Vessel Code3 (BPVC) was published in 1914-1915, and it has since become a cornerstone of industrial safety worldwide. I often tell my team that understanding ASME's historical commitment to safety is key to appreciating the rigor of its codes.
While ASTM focuses primarily on material specifications, ASME codes often adopt or reference these ASTM material standards (e.g., an SA-312 pipe in an ASME code is based on ASTM A312, with the "S" indicating it's an ASME adopted specification) and then build upon them by providing rules for design, fabrication, installation, examination, and testing of systems. For example, ASME B31.1 and ASME B31.34 for Process Piping are indispensable guides for engineers designing and constructing industrial plants. When MFY supplies stainless steel pipes for a refinery project in the Middle East, it's almost certain that ASME B31.3 will govern the piping systems. Our clients, typically engineering and construction contractors, rely on us to provide materials that fully comply with the stringent requirements of these codes, including specific heat treatment conditions, non-destructive examination (NDE) protocols, and pressure testing capabilities. A recent project involved supplying high-pressure stainless steel tubing to an equipment integrator for a system destined for a Russian petrochemical plant; adherence to the relevant ASME code sections was paramount for regulatory approval and operational safety.
The continuous evolution of ASME codes, incorporating new research, technological advancements, and lessons learned from incidents, ensures their ongoing relevance. MFY stays abreast of these updates through continuous training and investment in our technical libraries. This diligence allows us to advise clients like manufacturing companies looking to upgrade their facilities or distributors needing to stock compliant materials for their respective markets, ensuring that the stainless steel pipes they procure from us are fit for purpose and meet the highest safety standards.
The European Harmonization: The Birth of EN Standards
The development of EN (European Standards, or Euronorm) standards represents a more recent, yet equally significant, chapter in the history of standardization. Driven by the formation and expansion of the European Union (EU), EN standards aim to harmonize technical specifications across member states, thereby removing technical barriers to trade and fostering a single European market. CEN (European Committee for Standardization), CENELEC (European Committee for Electrotechnical Standardization), and ETSI (European Telecommunications Standards Institute) are the primary bodies responsible for developing and maintaining5 these standards. My experience working with European clients has shown me how deeply embedded these harmonized standards are in their procurement and regulatory frameworks.
For stainless steel pipes, key EN standards include EN 10216 (for seamless steel tubes for pressure purposes), EN 10217 (for welded steel tubes for pressure purposes), and EN 10296 (for welded circular steel tubes for mechanical and general engineering purposes), with specific parts detailing requirements for stainless steels (e.g., EN 10217-7 for welded stainless steel tubes for pressure purposes). These standards cover aspects like chemical composition, mechanical properties, dimensions, tolerances, and testing procedures, much like their ASTM/ASME counterparts, but with nomenclature, specific requirements, and testing regimes tailored to European practices and regulations. For instance, material designations (e.g., 1.4404 for 316L) and inspection document types (e.g., EN 10204 3.1 certificate) are distinctly European. When MFY exports stainless steel pipes to a client in Germany or Italy, compliance with the relevant EN standards is non-negotiable. We recently supplied EN 10217-7 Grade 1.4404 pipes to a food processing equipment manufacturer in Southeast Asia who was building machinery for export to the EU. Our ability to produce and certify to this EN standard was critical for their market access.
The process of developing EN standards involves national standards bodies from all EU/EFTA member countries, ensuring broad consensus and facilitating their adoption as national standards (e.g., DIN EN in Germany, BS EN in the UK). This harmonization has greatly simplified trade within Europe and for companies like MFY exporting to the region. It provides a clear, unified set of requirements, reducing the complexity of navigating multiple national standards that existed previously. Our commitment at MFY is to maintain the capability to produce stainless steel pipes conforming to all three major standard families—ASTM, ASME, and EN—to serve our diverse global clientele effectively.
ASTM originated from US railroad needsTrue
ASTM was established in 1898 primarily to address material quality issues in the rapidly expanding US railroad industry.
EN standards predate ASME codesFalse
EN standards emerged in the late 20th century for European harmonization, while ASME's pressure vessel codes date back to 1914-1915.
How are ASTM, ASME, and EN pipe standards currently applied in the industry?
Are you unsure which standard applies to your specific stainless steel pipe application? The choice between ASTM, ASME, and EN often depends on project location, industry, and specific functional requirements. Getting this right is crucial for compliance, safety, and operational efficiency, something we at MFY assist with daily.
Currently, ASTM standards are foundational for material specifications globally. ASME codes (often referencing ASTM materials) govern design and construction of pressure systems, especially in North America and regions adopting US practices. EN standards are mandatory for products in the European Economic Area.
The interplay between these standards is key. For example, a pressure vessel built to ASME code might use pipes specified by ASTM material standards, but if that vessel is for the European market, EN equivalencies or direct EN compliance might be needed. At MFY, we recently worked with an engineering contractor in India building a chemical plant with US technology (requiring ASME compliance) but also sourcing some components from Europe (requiring EN). Our role was to supply stainless steel pipes that met the primary ASME design codes, often using ASTM grades, while also providing necessary documentation to demonstrate EN equivalency where requested for certain auxiliary systems. This involves careful review of specifications, understanding the nuances of testing requirements, and meticulous documentation – all part of our commitment to delivering one-stop solutions. We'll explore these application scenarios in more detail, showing how MFY’s integrated supply chain and technical expertise help clients navigate these complexities effectively.
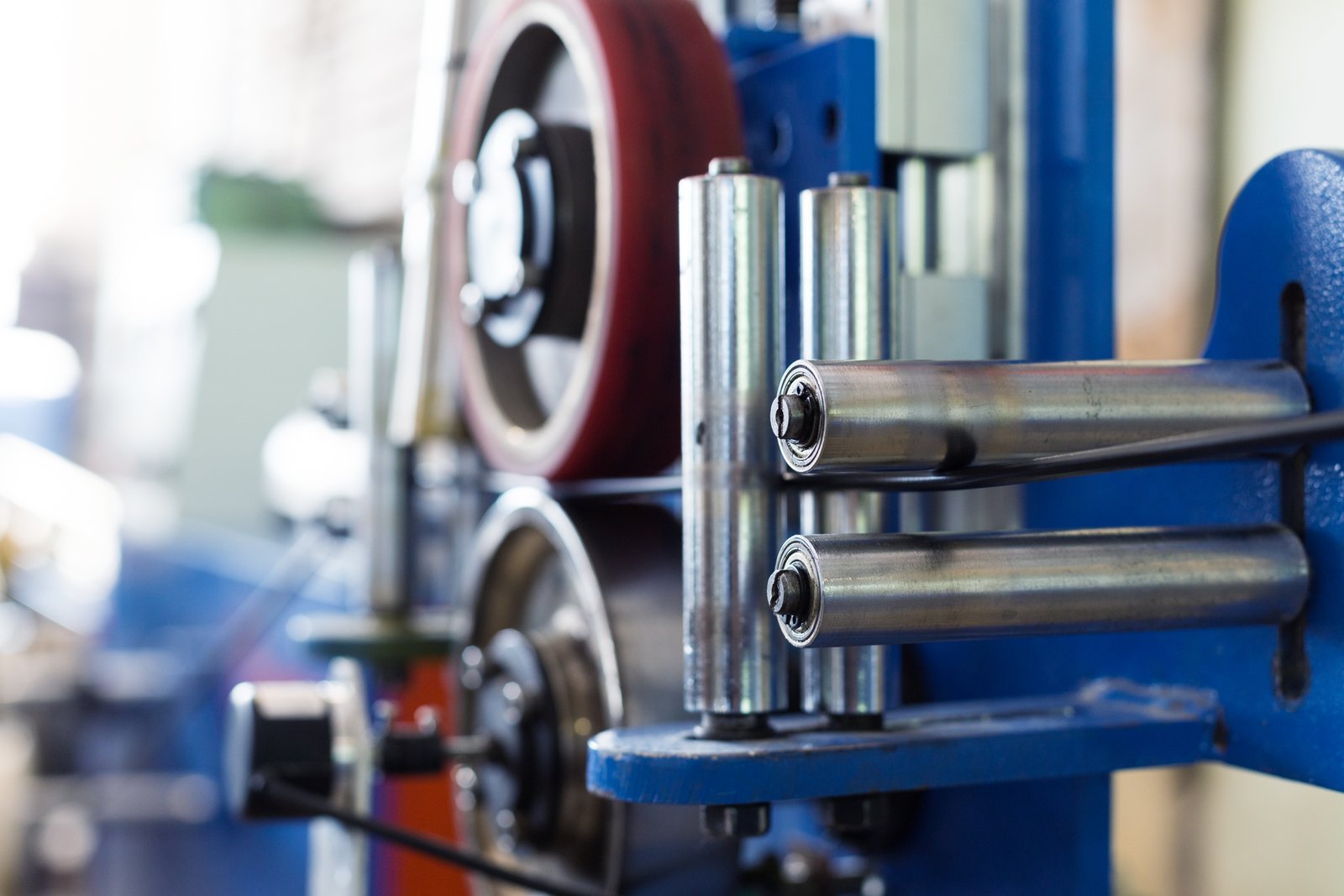
The current application of ASTM, ASME, and EN pipe standards in the global industry is a multifaceted landscape, shaped by regulatory mandates, contractual specifications, historical precedents, and industry-specific best practices. As a Global Business Director at MFY, I've seen firsthand how these standards act as the backbone for countless projects involving stainless steel pipes, from massive industrial complexes to specialized equipment. For our clients, whether they are manufacturing companies, engineering and construction contractors, distributors, or equipment integrators, understanding the specific domain of each standard is paramount. ASTM standards6 are frequently the starting point, providing the detailed material DNA – the chemical composition, mechanical properties, and manufacturing methods for grades like 304L or 316L stainless steel. ASME then often takes these ASTM material specifications and integrates them into a broader framework for the design, fabrication, inspection, and testing of pressure-retaining systems. This is particularly true for projects in North America, the Middle East, and parts of Asia that have adopted ASME codes like B31.3 for process piping or Section VIII for pressure vessels. EN standards, on the other hand, hold sway in Europe and are increasingly influential in regions trading heavily with the EU. They offer a comprehensive suite of specifications that are often required for CE marking, a mandatory conformity mark for products sold within the European Economic Area. Navigating this requires a supplier like MFY to be agile and knowledgeable, capable of producing and certifying stainless steel pipes to any of these standards, sometimes even requiring dual certification or meticulous equivalency assessments for projects with mixed international stakeholder requirements.
ASTM: The Backbone of Material Specification
ASTM International standards for pipes, particularly stainless steel pipes, are globally recognized and widely utilized as the primary reference for material characteristics. When an engineer specifies "ASTM A312 TP316L," they are invoking a detailed document that dictates the chemical composition, tensile strength, yield strength, elongation, heat treatment procedures, and permissible manufacturing methods (seamless or welded) for that specific austenitic stainless steel pipe. This level of detail ensures consistency and predictability in material performance. At MFY, our production processes for stainless steel pipes, from melting and casting to rolling, welding, and finishing, are meticulously aligned with ASTM specifications. For example, a client in Southeast Asia, a large-scale manufacturing company, recently placed an order for ASTM A249 welded austenitic steel boiler, superheater, heat-exchanger, and condenser tubes. Their entire quality assurance program relied on the strict adherence to this ASTM standard, which we ensure through rigorous in-process checks and final testing protocols, including hydrostatic testing and non-destructive electric tests as mandated.
The application of ASTM standards extends beyond just the end-user. Distributors and traders, who form a significant part of our client base, rely on ASTM designations to manage their inventory and assure their customers of material quality. When we export stainless steel pipes to India or Russia, the ASTM marking on the pipe, along with the accompanying Mill Test Certificate (MTC) detailing conformity to the specific ASTM standard, is a crucial piece of documentation. This ensures traceability and provides the end-user with the confidence that the material they are receiving meets the required engineering properties. I've seen projects where a lack of clear ASTM specification led to confusion and delays. For instance, a contractor might request "stainless steel pipe" without specifying the grade or the relevant ASTM standard, leading to potential mismatches in corrosion resistance or mechanical strength for the intended application. This is why we at MFY always work closely with our clients to clarify these requirements upfront.
Furthermore, ASTM standards are dynamic. They are regularly reviewed and updated by technical committees comprising experts from various fields. This ensures that the standards reflect the latest advancements in materials science, manufacturing technology, and testing methods. For MFY, staying current with these revisions is part of our commitment to innovation and quality. Our R&D team actively monitors changes to key ASTM standards like A312, A269, A270 (for sanitary tubing), and A790 (for duplex stainless steel pipes), ensuring our production and quality control practices evolve accordingly. This proactive approach allows us to consistently deliver stainless steel pipes that meet the most up-to-date global benchmarks.
ASME: Ensuring Safety in Pressure Applications
ASME standards, particularly the Boiler and Pressure Vessel Code (BPVC) and the B31 codes for pressure piping (e.g., B31.1 for Power Piping, B31.3 for Process Piping, B31.4 for Pipeline Transportation Systems for Liquids and Slurries), are paramount in industries where system integrity under pressure is critical. These codes provide a comprehensive set of rules for the design, fabrication, installation, examination, inspection, testing, and certification of pressure-containing components and systems. While ASTM specifies what a material is, ASME often dictates how that material should be used safely in a pressure application. Many ASME material specifications (SA-grades, like SA-312) are directly adopted from ASTM specifications (A-grades, like A312), with ASME sometimes imposing additional requirements or limitations. I recall a project with an engineering contractor in the Middle East designing a new oil and gas processing facility. The entire piping system was governed by ASME B31.3, which meticulously detailed everything from pipe wall thickness calculations based on design pressure and temperature, to allowable stresses, flange ratings, welding procedures, and examination requirements.
MFY's role in such projects is to supply stainless steel pipes that not only meet the base ASTM material standard (e.g., ASTM A312 TP316L) but also satisfy any additional stipulations imposed by the relevant ASME code adopted by the project. This might include specific heat treatment conditions, supplementary non-destructive testing (NDT) like ultrasonic or radiographic testing beyond standard ASTM requirements, or particular marking and documentation protocols. For instance, ASME codes often require materials to be sourced from manufacturers holding specific ASME quality system certificates (e.g., ASME U-stamp for pressure vessels), or at least demonstrate robust quality control aligned with ASME principles. Our strong production capacity and inventory, coupled with a fully integrated supply chain, enable us to meet these demanding requirements. We recently supplied SA-790 duplex stainless steel pipes for a high-pressure application in a chemical plant in India, where the design was strictly according to ASME B31.3. The enhanced corrosion resistance and strength of duplex stainless steel were critical, and our ability to certify the material to both ASTM A790 and ASME SA-790, along with providing comprehensive test reports, was key to securing the order.
The global reach of ASME standards is significant. While originating in the US, they are widely adopted or serve as a reference in many countries, particularly for critical infrastructure projects like power plants, refineries, and chemical facilities. For MFY, this means our stainless steel pipes destined for such applications in our export markets—India, Southeast Asia, Middle East, Russia—must often demonstrate compliance with ASME codes. Our rapid export delivery and innovation-driven development allow us to adapt to these complex project specifications efficiently.
EN Standards: Gateways to the European Market and Beyond
EN (European Standards) are technical standards drafted and maintained by CEN, CENELEC, or ETSI, recognized by the European Union and EFTA. They are crucial for accessing the European market, as compliance with relevant EN standards is often a prerequisite for affixing the CE marking to products, indicating conformity with EU health, safety, and environmental protection directives. For stainless steel pipes, key EN standards include series like EN 10216-5 (Seamless steel tubes for pressure purposes - Technical delivery conditions - Part 5: Stainless steel tubes) and EN 10217-7 (Welded steel tubes for pressure purposes - Technical delivery conditions - Part 7: Stainless steel tubes). These standards meticulously define material grades (e.g., 1.4307 for 304L, 1.4404 for 316L), chemical compositions, mechanical properties, dimensions and tolerances, inspection procedures, and marking requirements. I've found that European clients, and increasingly clients in other regions adopting EN standards, are very particular about the specifics of EN compliance, including the type of inspection certificate (e.g., EN 10204 3.1 or 3.2).
MFY has invested significantly in ensuring our production capabilities and quality management systems can meet the stringent demands of EN standards. This is vital for our business, as many of our target clients—manufacturing companies, equipment integrators, and distributors—either operate within Europe or supply to projects that require EN-compliant components. For example, we recently supplied a batch of EN 10217-7 TC1 grade 1.4404 welded stainless steel pipes to an equipment integrator in Southeast Asia. This integrator was building a water treatment system for a municipality in a European country, and the project specifications explicitly mandated EN standards for all wetted parts. Our ability to provide pipes fully certified to EN 10217-7, complete with EN 10204 3.1 inspection certificates, was a critical factor in their decision to partner with MFY.
The influence of EN standards is also growing beyond Europe, as they are often seen as high-quality, comprehensive benchmarks. Some countries in the Middle East and Asia are harmonizing their national standards with EN standards or accepting them as an alternative to ASTM/ASME in certain contexts. This trend underscores the importance for a global supplier like MFY to maintain proficiency across all major international standard systems. Our integrated supply chain allows us to source raw materials and manage production processes to meet the specific nuances of EN standards, such as particular testing frequencies or marking conventions, which can differ from ASTM or ASME requirements.
Below is a table illustrating typical applications and key features:
Feature | ASTM | ASME | EN (European Norm) |
---|---|---|---|
Primary Focus | Material Specifications | Design, Fabrication & Safety of Pressure Systems | Harmonized Technical Standards for European Market |
Scope Example | A312 (Stainless Steel Pipe) | B31.3 (Process Piping), BPVC Section VIII (Pressure Vessels) | EN 10217-7 (Welded Stainless Steel Tubes for Pressure) |
Material ID | Grade (e.g., TP304L, TP316L) | SA-Grade (e.g., SA-312 TP304L, often references ASTM) | Numerical/Symbolic (e.g., 1.4307, X2CrNi18-9) |
Typical Use | General industry, material procurement | Power, Oil & Gas, Chemical plants (Pressure applications) | EU projects, CE Marking, European industry |
Key Document | Mill Test Certificate (MTC) to ASTM spec | Often requires MTC + compliance to specific ASME code sections | Inspection Certificate (e.g., EN 10204 3.1/3.2) |
MFY Example | Supplying A269 tubing to a food processor in India | Supplying SA-312 pipes for a refinery in the Middle East | Supplying EN 10217-7 pipes to an equipment OEM exporting to EU |
This comparative overview highlights how each standard, while comprehensive, carves out its specific area of emphasis, guiding engineers and procurement specialists in their selection of stainless steel pipes for diverse global applications. At MFY, our expertise lies in understanding these nuances and ensuring our products meet the precise standard required by our clients' projects.
ASTM defines material propertiesTrue
ASTM standards specify chemical composition, mechanical properties and manufacturing methods for materials like stainless steel pipes.
ASME replaces ASTM standardsFalse
ASME builds upon ASTM material specifications by adding design and safety requirements for pressure applications, but doesn't replace them.
What challenges arise from using ASTM, ASME, and EN pipe standards?
Are you finding it difficult to reconcile the differences between ASTM, ASME, and EN standards for your stainless steel pipe needs? This can lead to compliance issues, project delays, and unexpected costs. As someone who has helped many clients navigate this, I know these challenges are very real.
Key challenges include interpreting nuanced differences in chemical compositions and mechanical properties, ensuring material equivalency across standards, managing complex documentation and certification requirements (e.g., EN 10204 vs. standard MTCs), and the cost implications of dual testing or certifications for global projects.
Imagine an engineering contractor in India working on a project with European end-users. They might be comfortable with ASME standards, but the client insists on EN compliance for all stainless steel piping. This immediately brings up questions of equivalency: Is ASTM TP316L7 truly interchangeable with EN 1.4404 in this specific application? What are the differences in required testing or tolerances? At MFY, we often act as a bridge in these situations. Our technical team can help analyze the specific requirements of each standard, identify potential discrepancies, and advise on the best path forward, whether it’s sourcing dual-certified material or conducting supplementary tests. The complexities don't end there; keeping up with amendments and revisions to each standard also requires constant vigilance. These hurdles, while significant, are manageable with the right expertise and a proactive approach, which we'll explore further.
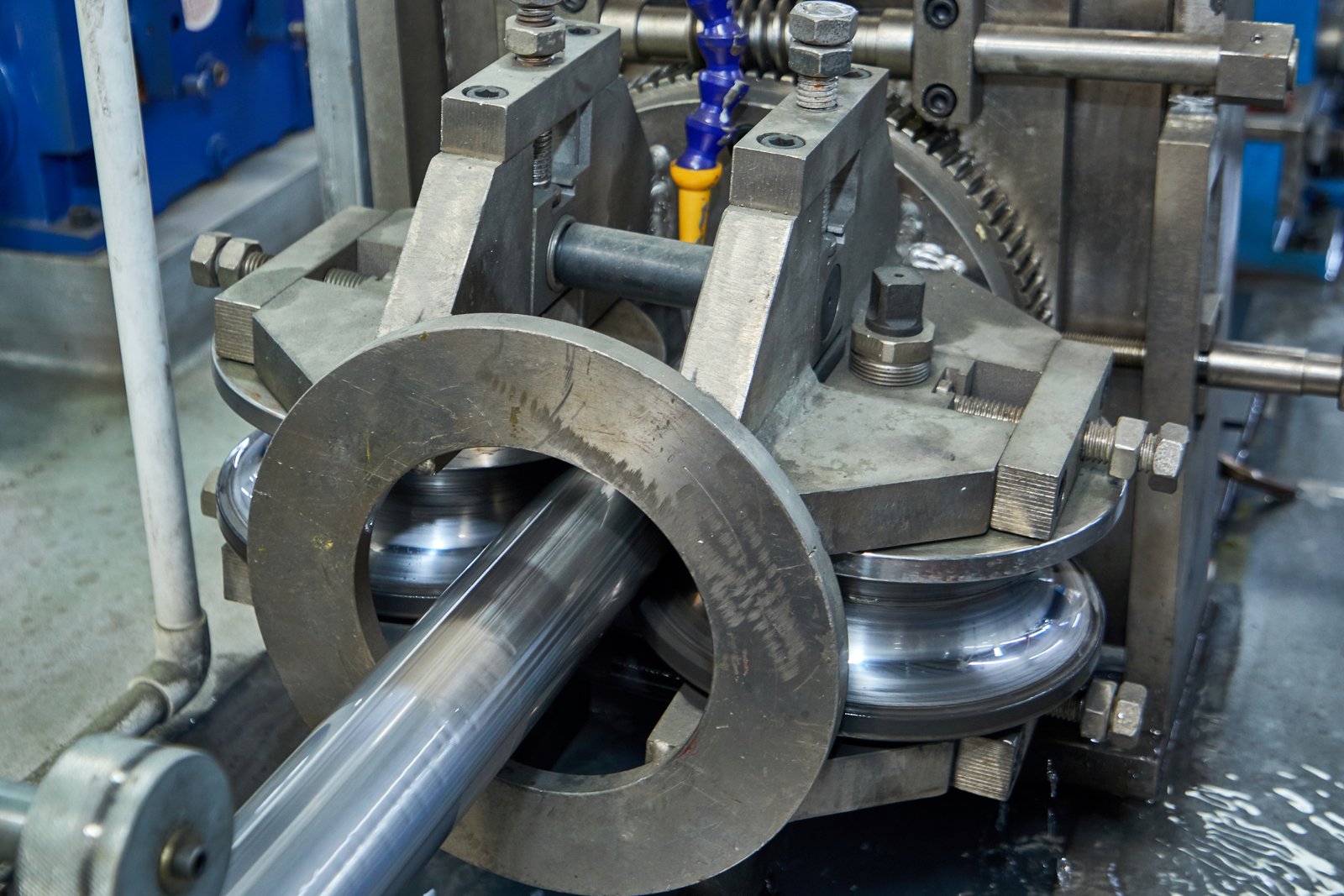
While ASTM, ASME, and EN standards are indispensable for ensuring quality, safety, and interoperability in the stainless steel pipe industry, their co-existence and inherent complexities present a unique set of challenges for manufacturers, suppliers, and end-users alike. At MFY, we encounter these challenges regularly as we cater to a diverse global clientele with varied project requirements. One of the most common hurdles is the sheer volume and intricacy of the standards themselves. Each code is a lengthy document filled with technical jargon, detailed tables, and specific testing protocols that require expert interpretation. For a company sourcing stainless steel pipes for a project that might involve components from North America, machinery from Europe, and final assembly in Asia, navigating the interplay of ASTM, ASME, and EN requirements can be a daunting task. This complexity is compounded by the fact that standards are not static; they are periodically reviewed and updated, meaning that what was compliant last year might need re-evaluation this year. Furthermore, the perceived or actual equivalence between grades specified under different standards (e.g., an ASTM grade versus an EN grade) is a frequent point of contention and requires careful technical assessment to avoid costly mistakes in material selection. These are not just theoretical problems; they have real-world implications for project timelines, budgets, and the ultimate performance and safety of the installed systems.
The Labyrinth of Cross-Referencing and Equivalency
One of the most significant challenges I've observed in my years at MFY is navigating the intricate web of cross-referencing between standards and determining true material equivalency. For instance, an engineering firm might design a system using ASME B31.3, which in turn references an SA- (ASME) material specification, which is often based on an ASTM A- specification. If the end client or local regulation then requires EN compliance, the task becomes identifying an EN material grade that is functionally equivalent to the specified ASTM/ASME grade. This isn't always a straightforward one-to-one match. While grades like ASTM TP316L and EN 1.4404 are often considered equivalent for many applications due to similar chemical compositions (chromium, nickel, molybdenum content) and corrosion resistance, there can be subtle but critical differences in specified minimum/maximum elemental percentages, allowable impurities, mechanical properties (yield strength, tensile strength, elongation), or required heat treatment conditions. For example, a slight variation in the minimum molybdenum content between an ASTM and an EN grade could impact pitting corrosion resistance in a specific chloride-rich environment. I recall a case with a manufacturing client in Southeast Asia who had a bill of materials specifying ASTM A312 TP304L. However, due to a specific European end-user requirement, they needed to demonstrate equivalency to EN 1.4307. While generally accepted, the project's stringent quality assurance demanded a detailed comparison of chemical analysis ranges and mechanical property minimums as per the latest revisions of both standards. MFY's technical team prepared a comparative analysis, highlighting the overlaps and minor differences, which helped the client satisfy their end-user's scrutiny.
This challenge is further compounded when dealing with less common alloys or more specialized applications. Data supporting equivalency claims must be robust and often requires more than just looking at a comparison table. It might involve reviewing the original standard documents, consulting material databases, and sometimes, if the application is critical enough, conducting specific tests to confirm performance characteristics. The responsibility for ensuring true equivalency often falls on the supplier or the contractor, adding a layer of risk and due diligence. For instance, a distributor in Russia might receive a request for an EN-specified stainless steel pipe but has stock of an ASTM-specified pipe. Without thorough verification, supplying the ASTM material could lead to non-compliance if the end application has specific EN-derived requirements not fully covered by the ASTM standard, such as specific impact testing temperatures or different pressure rating calculations. At MFY, our strong production capacity and inventory allow us to stock materials certified to multiple standards or produce specifically to the required standard, minimizing these risks for our clients.
The interpretation of "equivalent" can also be subjective or context-dependent. What is considered equivalent for a low-pressure water line might not be for a high-temperature, high-pressure chemical processing line. The project specifications, governing codes, and regulatory environment ultimately dictate the level of scrutiny applied to equivalency claims. This necessitates a deep understanding of not just the material standards themselves, but also the application context and the relevant design codes.
Cost and Time Implications of Multi-Standard Compliance
Achieving compliance with multiple standards, or even ensuring stringent adherence to one complex standard, invariably has cost and time implications. These can arise from several factors. Firstly, there's the cost of acquiring and maintaining up-to-date copies of the standards themselves, which can be substantial, especially for organizations needing access to a broad range of ASTM, ASME, and EN documents. At MFY, we invest significantly in digital libraries and subscriptions to ensure our teams always reference the latest revisions. Secondly, the testing and certification requirements can differ significantly. For example, EN 10204 specifies different types of inspection documents (e.g., 2.2 Test Report, 3.1 Inspection Certificate, 3.2 Inspection Certificate validated by an independent third party). Achieving a 3.1 or particularly a 3.2 certificate typically involves more rigorous inspection, testing, and documentation, and potentially third-party witness costs, compared to a standard manufacturer's MTC often sufficient for some ASTM-based requirements. If a project requires stainless steel pipes to be dual-certified to both ASTM and EN standards, it might necessitate additional tests to cover the specific requirements of both, or at least a more comprehensive testing regime that satisfies the superset of requirements. I've seen situations where an equipment integrator needed pipes for a project with global deployment. Some components were destined for North America (ASME) and others for Europe (EN). While the base material (e.g., 316L) was the same, the certification package had to be tailored for each, sometimes requiring separate production runs or specific marking to maintain traceability and compliance for each destination. This adds complexity to production planning and inventory management.
Furthermore, the time taken for these additional tests, inspections, and documentation processes can impact project timelines. For instance, if specific non-destructive examinations (NDE) like ultrasonic testing or positive material identification (PMI) are mandated by one standard but not routinely performed for another, scheduling and conducting these tests adds to the lead time. MFY's rapid export delivery capability is partly built on our efficient internal processes for managing these varied testing and certification requirements. We work with our clients, like engineering and construction contractors, to understand their project schedules and ensure that all necessary compliance activities are planned and executed without causing undue delays. A recent example involved a time-sensitive project for a manufacturing company in India requiring stainless steel tubes with EN 10204 3.1 certification. By having pre-approved testing procedures and a streamlined documentation process aligned with EN requirements, we were able to meet their tight deadline, which might have been a challenge if we only operated to a singular standard's certification protocol.
The administrative overhead of managing compliance across different standards is also a non-trivial cost. This includes training personnel, maintaining quality management systems that can accommodate various requirements, and handling the extensive paperwork involved. For distributors and traders, ensuring that the materials they stock and sell have the correct and complete documentation for their target markets is a continuous effort. Any lapse can lead to rejected shipments, contractual penalties, or damage to their reputation. MFY’s commitment to a fully integrated supply chain and innovation-driven development includes robust digital systems for managing this documentation, providing our clients with accurate and timely compliance information.
Keeping Pace with Evolving Standards and Amendments
ASTM, ASME, and EN standards are not static documents; they are living standards, regularly reviewed, updated, and amended by their respective technical committees. These revisions can include changes to chemical composition limits, mechanical property requirements, testing procedures, acceptance criteria, or even the introduction of new material grades or product forms. For any organization involved in the specification, manufacture, supply, or use of stainless steel pipes, keeping abreast of these changes is a constant challenge. Failure to adhere to the latest version of a standard can lead to non-compliance, even if the material met the requirements of an older version. I remember a case where a long-standing ASTM specification for a particular stainless steel alloy had a minor but critical update to its chromium range. A supplier who wasn't aware of this amendment continued to produce to the older specification, leading to a batch of material being rejected by a client whose project mandated adherence to the latest revision.
The frequency of updates varies. Some standards might see minor revisions annually, while others might undergo more significant overhauls every few years. Tracking these changes across multiple standards bodies (ASTM, ASME, EN) requires a dedicated effort. At MFY, our technical and quality assurance teams are tasked with monitoring announcements from these organizations, participating in industry forums, and regularly reviewing the standards relevant to our stainless steel pipe products. This proactive approach is part of our commitment to continuous evolution. For example, when ASME BPVC is updated every two years, our engineers study the changes relevant to materials (Section II) and piping codes (e.g., B31.3) to ensure our products and advisory services remain current. Similarly, amendments to EN standards, often published through official journals or databases, are carefully reviewed for their impact on our CE marking procedures or specifications for pipes supplied to European markets.
This challenge is particularly acute for smaller companies or those with limited resources dedicated to standards management. It's not just about having the latest document; it's about understanding the implications of the changes. Sometimes, an amendment might necessitate adjustments in manufacturing processes, recalibration of testing equipment, or retraining of personnel. For our clients, such as distributors or smaller manufacturing firms, MFY often serves as a resource, providing information on relevant standard updates or explaining how a change might affect their procurement choices. Our vision to become a leading international trade and service brand in China’s stainless steel industry is underpinned by this commitment to technical excellence and staying at the forefront of industry knowledge, ensuring that the stainless steel pipes we deliver to India, Southeast Asia, or the Middle East always conform to the most current and applicable standards.
ASTM TP316L and EN 1.4404 are often considered equivalentTrue
These grades share similar chemical compositions and corrosion resistance properties, making them generally interchangeable for many applications.
EN standards never require additional testingFalse
EN standards like EN 10204 often require more rigorous testing and certification compared to standard ASTM MTCs, especially for 3.1 and 3.2 certificates.
What strategies can be employed to address challenges in applying these pipe standards?
Feeling overwhelmed by the complexities of ASTM, ASME, and EN pipe standards? You're not alone. Many face hurdles in interpretation and application. The good news is, effective strategies exist to navigate these challenges, ensuring your projects stay on track and compliant.
Strategies include investing in continuous team training, developing robust internal quality management systems (QMS), leveraging supplier expertise (like MFY's), utilizing specialized standards management software, and fostering clear communication with all project stakeholders regarding standard requirements from the outset.
At MFY, we often advise clients, particularly engineering and construction contractors, to establish a "standards champion" within their team—someone responsible for staying updated and disseminating knowledge. For one project in the Middle East, a client was struggling with conflicting requirements from different international partners. We helped them by facilitating a workshop to map out all applicable standards and identify a clear compliance path, leveraging our deep understanding of ASTM, ASME, and EN pipe standards8. This collaborative approach, combined with a commitment to internal capability building, transformed their ability to manage complex specifications. We'll delve into these and other practical strategies, demonstrating how a proactive and informed approach can turn standardization challenges into a competitive advantage.

Addressing the challenges posed by the diverse and intricate landscape of ASTM, ASME, and EN pipe standards requires a proactive, multi-faceted approach. It's not enough to simply acknowledge the difficulties; organizations must implement concrete strategies to manage them effectively. As someone deeply involved in MFY's global operations, I've seen how a well-thought-out strategy can transform potential pitfalls into opportunities for demonstrating competence and reliability. The core of such a strategy revolves around building knowledge, establishing robust processes, fostering strong partnerships, and leveraging technology. For our clients, ranging from large manufacturing companies undertaking complex plant constructions to distributors needing to ensure their inventory meets diverse market demands, the ability to confidently navigate these standards is a critical success factor. This involves more than just technical know-how; it also requires excellent communication skills and meticulous record-keeping9. For instance, when MFY works with an equipment integrator designing a system with components subject to different standards (e.g., some parts for the US market under ASME, others for European deployment under EN), our strategy involves early engagement to clarify all requirements, meticulous segregation of materials and documentation, and leveraging our integrated supply chain to source or produce precisely what's needed for each segment. This comprehensive approach minimizes errors, reduces delays, and ultimately delivers value to our clients across markets like India, Southeast Asia, and Russia.
Developing In-House Expertise and Continuous Learning
One of the most fundamental strategies for any organization dealing regularly with ASTM, ASME, and EN standards is to invest in developing in-house expertise. This means ensuring that key personnel—engineers, quality assurance teams, procurement specialists, and even sales staff who interact with clients on technical matters—have a solid understanding of the relevant standards applicable to their work. At MFY, we prioritize continuous learning through regular training sessions, workshops, and access to technical resources. I often encourage my team members to delve into the specifics of standards like ASTM A312 for stainless steel pipes or ASME B31.3 for process piping, not just to understand the letter of the standard but also the intent behind it. This deeper understanding allows for more informed decision-making and problem-solving. For example, when a client, perhaps an engineering contractor in India, presents a complex specification that seems to draw from multiple standards, an MFY team member with strong in-house expertise can quickly identify potential conflicts or areas needing clarification, rather than simply passing on a confusing request to production.
This in-house expertise should not be static. Given that standards evolve, a commitment to continuous learning is crucial. This can involve subscribing to updates from standards-developing organizations (SDOs) like ASTM, ASME, and CEN, participating in industry seminars and conferences, and encouraging professional certifications where relevant. We've found that creating internal "subject matter experts" for different standard families or specific product lines can be highly effective. These experts can then serve as go-to resources for the rest of the team and can also lead internal training initiatives. For instance, one of our senior engineers at MFY specializes in the nuances of EN pressure equipment standards, which is invaluable when we are working on projects for the European market or for clients who are adopting EN specifications. This internal capability reduces reliance on external consultants for routine interpretations and allows us to respond more agilely to client inquiries.
Furthermore, fostering a culture where questioning and seeking clarity on standards is encouraged is vital. Employees should feel comfortable raising concerns if they believe a specification is ambiguous or if they are unsure about the correct application of a standard. This proactive approach can help catch potential errors early in the process, saving significant time and resources down the line. We have seen this pay dividends when a junior engineer questioned a seemingly straightforward pipe specification for a project, only for further investigation to reveal a subtle but critical requirement hidden in a referenced sub-standard, preventing a potential non-conformance.
Leveraging Supplier Knowledge and Partnerships (like MFY)
For many companies, especially small to medium-sized enterprises (SMEs) or those whose core business is not materials engineering, developing comprehensive in-house expertise across all relevant standards can be a significant challenge and expense. In such cases, leveraging the knowledge and experience of trusted suppliers becomes a critical strategy. As a specialized manufacturer and exporter of stainless steel pipes, MFY positions itself not just as a supplier but as a technical partner to its clients. We understand that our clients—be they manufacturing companies, E&C contractors, distributors, or equipment integrators—rely on us for more than just delivering a product; they often seek our guidance on standard selection, material equivalency, and compliance documentation. I recall a situation with a distributor in the Middle East who was expanding their stainless steel pipe inventory to cater to new industrial segments. They were unsure about the specific ASTM and ASME grades most in demand and the associated certification requirements. Our MFY sales and technical team worked closely with them, providing market insights, explaining the applications of different grades like ASTM A312 TP304/304L and TP316/316L, detailing typical ASME B31.3 requirements for process plants in the region, and clarifying the importance of proper Mill Test Certificates (MTCs). This partnership approach helped them optimize their stock and better serve their customers.
A good supplier should be able to provide clear, accurate, and up-to-date information about the standards their products conform to. This includes providing comprehensive MTCs that clearly state the specific standard (including year of revision), material grade, chemical analysis, mechanical test results, and any other information required by the standard. At MFY, our fully integrated supply chain and robust quality management system are designed to ensure this level of traceability and documentation accuracy. We also proactively communicate any significant changes in standards that might affect the products we supply. For projects involving complex or multiple standard requirements, we engage in early discussions with our clients to understand their needs thoroughly and to offer solutions, such as providing dual-certified materials or conducting specific supplementary tests to meet all applicable codes. For example, for an equipment integrator building a system for a global market, we might supply stainless steel tubes that meet both ASTM A269 and certain EN 10217-7 requirements, complete with the necessary distinct certifications for each batch destined for different regions.
Building long-term relationships with knowledgeable suppliers like MFY can significantly reduce the burden of standards compliance for the client. It allows them to tap into a reservoir of specialized expertise without having to build it all internally. This collaborative approach, based on trust and transparency, is a cornerstone of MFY’s business philosophy as we aim to support the global expansion of China’s stainless steel supply chain.
Implementing Robust Quality Management Systems (QMS)
A robust Quality Management System (QMS), ideally certified to a recognized standard like ISO 9001, provides the framework and processes necessary to consistently meet customer and regulatory requirements, including those related to pipe standards. A well-implemented QMS ensures that procedures are in place for understanding customer specifications, translating them into production requirements, controlling manufacturing processes, conducting necessary inspections and tests, managing documentation, and handling any non-conformances. At MFY, our QMS is integral to our ability to comply with diverse standards like ASTM, ASME, and EN. It dictates how we review contracts to ensure we fully understand the specified standards, how we control the procurement of raw materials to meet those standards, how our production lines are set up and monitored to maintain consistency, and how final products are inspected and certified before dispatch. For instance, if an order specifies stainless steel pipes to EN 10217-7 with an EN 10204 3.1 certificate, our QMS has defined procedures for the specific inspection steps, the authorized personnel to sign off on the certificate, and the records to be maintained.
A key aspect of an effective QMS in the context of standards compliance is document control. This ensures that all personnel are working with the latest versions of standards, specifications, and internal procedures. It also governs the creation, approval, distribution, and retention of compliance documentation, such as MTCs, test reports, and certificates of conformity. I've seen firsthand how poor document control can lead to serious compliance issues. For example, using an outdated internal checklist for final inspection that doesn't reflect a recent amendment to an ASTM standard could result in a non-compliant product being shipped. Our QMS at MFY incorporates rigorous document control processes, increasingly managed through digital systems, to mitigate such risks.
Furthermore, a QMS promotes a culture of continuous improvement through mechanisms like internal audits, corrective and preventive actions (CAPA), and management reviews. These processes help identify weaknesses in compliance procedures and implement improvements. For example, if an internal audit reveals inconsistencies in how different shifts interpret a particular testing requirement of an EN standard, a corrective action might involve retraining and standardizing the interpretation. This commitment to continuous improvement, embedded within our QMS, strengthens MFY’s ability to reliably deliver high-quality stainless steel pipes that meet the exacting requirements of our clients in India, Southeast Asia, the Middle East, Russia, and beyond. It also supports our vision of becoming a leading international trade and service brand in China’s stainless steel industry.
Supplier partnerships aid standards complianceTrue
Knowledgeable suppliers like MFY provide technical guidance and dual-certified materials to help clients navigate complex standard requirements.
QMS only requires annual updatesFalse
Effective QMS requires continuous document control and real-time updates to reflect standard amendments, not just annual reviews.
What technical recommendations can enhance the use of ASTM, ASME, and EN pipe standards?
Looking for ways to improve how your organization works with ASTM, ASME, and EN pipe standards? Beyond general strategies, specific technical actions can greatly enhance efficiency and compliance. Adopting these can transform standards from mere obligations into tools for quality assurance.
Technical recommendations include rigorous material traceability from melt to final product, utilizing Positive Material Identification (PMI) extensively, performing gap analyses between differing standards for specific project needs, and maintaining meticulous, digitally managed records of all tests and certifications.
Consider an equipment integrator building complex systems for various international markets. They might receive stainless steel pipes from multiple suppliers, all claiming compliance. By implementing a strict PMI protocol10 upon receipt, they can instantly verify the alloy composition against the MTC and the specified standard (ASTM, ASME, or EN). At MFY, we encourage such practices and ensure our own traceability is impeccable. For one client, a manufacturing company, we helped implement a system where QR codes on pipe bundles linked directly to their digital MTCs, streamlining their incoming inspection and inventory management. These kinds_of technical enhancements are crucial for robust standards application.
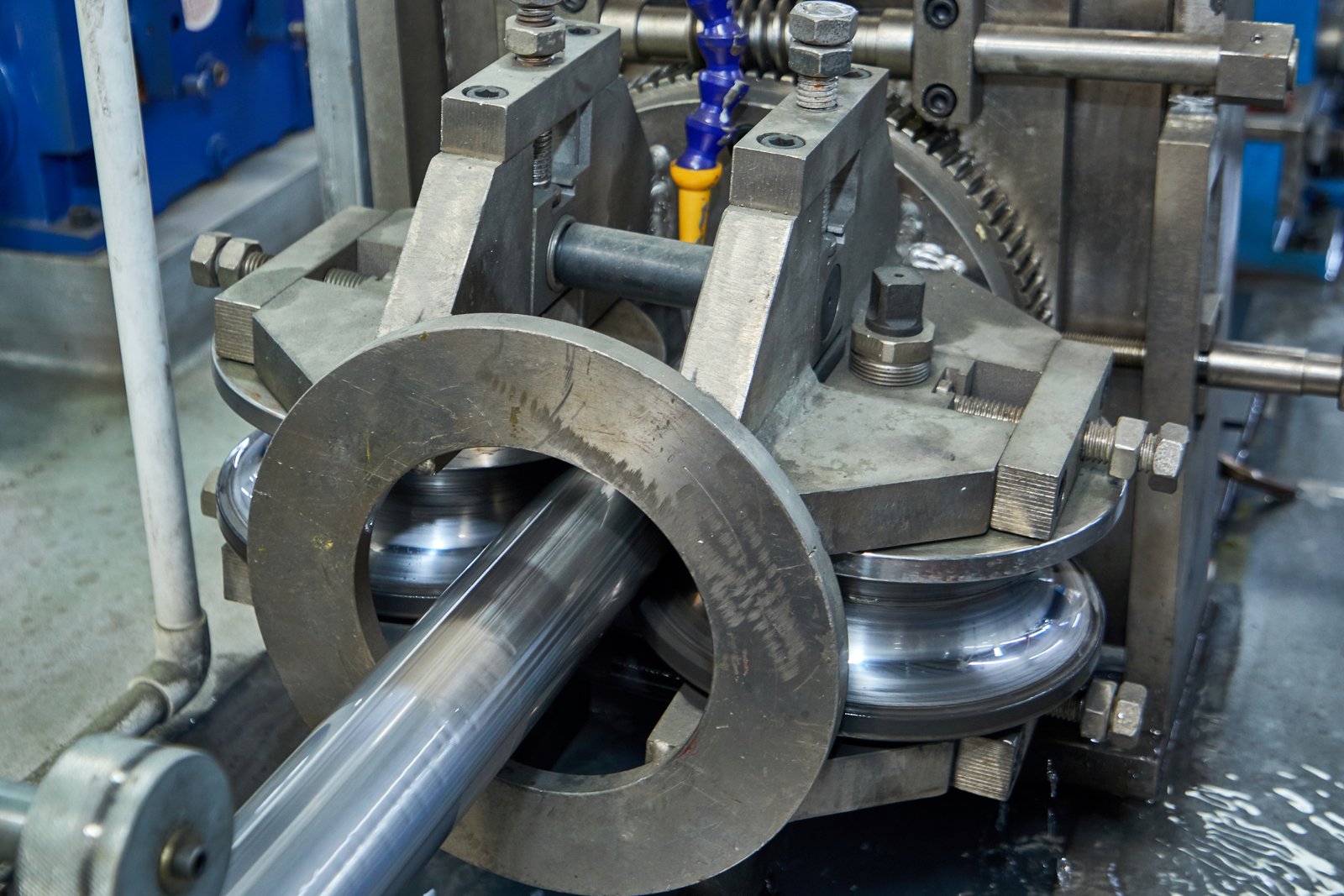
Enhancing the practical application of ASTM, ASME, and EN pipe standards goes beyond mere understanding; it involves the adoption of specific technical methodologies and tools that can improve accuracy, efficiency, and overall compliance. As Global Business Director at MFY, I've seen how integrating certain technical practices11 into daily operations can significantly reduce errors, streamline workflows, and provide greater assurance to clients. These recommendations are particularly pertinent in the stainless steel industry, where material integrity and adherence to precise specifications are paramount for performance and safety. For our diverse clientele—from manufacturing companies requiring precise material inputs to engineering and construction contractors building critical infrastructure, and distributors needing reliable stock—these technical enhancements can translate into tangible benefits. They help bridge the gap between the theoretical requirements of a standard and the practical realities of sourcing, fabricating, and installing stainless steel pipes. For instance, when MFY exports stainless steel pipes to demanding markets like those in the Middle East for oil and gas applications, or to Southeast Asia for advanced manufacturing, the technical rigor we apply in interpreting and meeting standards like ASME B31.3 or specific ASTM grades is a key differentiator. It's about embedding quality and precision into every step, from raw material selection through to final inspection and documentation.
Adopting Digital Tools for Standards Management and Comparison
In today's digital age, relying solely on paper copies of standards or manual comparison methods is inefficient and prone to error. Adopting digital tools for standards management and comparison is a crucial technical recommendation. There are specialized software platforms and online subscription services that provide access to vast libraries of ASTM, ASME, EN, and other international standards. These tools often feature powerful search functionalities, allow for side-by-side comparison of different standards or revisions, and provide alerts for updates and amendments. At MFY, we utilize such digital resources to ensure our engineering and quality teams always have access to the latest versions and can quickly analyze requirements. For example, if a client, say an engineering contractor in India, queries about the differences between an older version of an ASTM standard referenced in their legacy drawings and the current version, our team can use digital tools to quickly generate a comparison report highlighting the changes in chemical composition, mechanical properties, or testing protocols. This capability not only saves time but also enhances the accuracy of our technical advice.
Furthermore, some digital tools can assist in managing internal compliance documentation, linking specific project requirements to the relevant clauses in the standards, and tracking compliance status. For equipment integrators or manufacturing companies dealing with complex bills of materials that cite various standards, such systems can be invaluable. Imagine an equipment integrator building a skid-mounted processing unit that uses stainless steel pipes compliant with ASTM for some parts, and EN for others (due to specific component sourcing or end-user requirements). A digital system can help manage the distinct documentation packages, ensure traceability, and flag any discrepancies. We've also seen the benefit in our own operations; our digital innovation efforts at MFY include developing internal systems that integrate order processing with quality control and standards compliance, ensuring that every batch of stainless steel pipe produced aligns perfectly with the specified standard, whether it's for a client in Russia requiring GOST-harmonized EN standards or a project in Southeast Asia strictly following ASME codes.
The ability to digitally search and cross-reference within standards also aids in understanding complex interdependencies. For example, an ASME piping code might reference dozens of ASTM material specifications and other ASME standards for welding or NDE. Digital tools make navigating this "standards web" far more manageable than flipping through multiple voluminous hardcopy books. This efficiency translates into faster response times to client queries and more robust internal processes.
Ensuring Comprehensive Material Testing and Certification
While standards dictate minimum testing requirements, a proactive technical approach involves ensuring comprehensive material testing that not only meets but sometimes exceeds these baseline requirements, especially for critical applications. This includes meticulous attention to both destructive testing (like tensile tests, bend tests, impact tests) and non-destructive testing (NDT) such as hydrostatic testing, eddy current testing, ultrasonic testing (UT), or radiographic testing (RT), as specified by the relevant ASTM, ASME, or EN standard. At MFY, our integrated production facility is equipped with advanced testing laboratories to perform a wide array of these tests in-house. This capability allows us to maintain tight control over quality and to provide clients with reliable test results. For example, for stainless steel pipes intended for high-pressure applications under ASME B31.3, such as those supplied to petrochemical plants in the Middle East, we ensure that NDT protocols are stringently followed and often provide supplementary test data if requested by the client to give them extra assurance.
A crucial aspect of this is Positive Material Identification (PMI). PMI testing is a non-destructive method to verify the chemical composition of alloys, ensuring that the supplied material matches the specified grade. While not always mandatory for all standards or all pipe types, implementing PMI at various stages—incoming raw material, in-process, and final product—is a best practice that MFY strongly advocates and employs. It helps prevent material mix-ups, which can have catastrophic consequences. I recall an instance where an MFY client, a manufacturing company, implemented mandatory PMI for all incoming stainless steel components after a costly incident caused by an incorrect alloy grade from a previous supplier. Our ability to provide pipes with reliable PMI reports became a key factor in their decision to switch to MFY.
The certification accompanying the pipes is equally critical. Mill Test Certificates (MTCs) or Inspection Certificates (e.g., EN 10204 3.1 or 3.2) must be accurate, complete, and fully traceable to the supplied material. This documentation should clearly state the standard complied with (including the year of revision), the exact chemical composition from the heat analysis, the results of all specified mechanical tests, heat treatment details, and NDT results. At MFY, we have robust digital systems for generating and managing these certificates, ensuring their accuracy and timely availability to our clients, whether they are distributors in India needing clear documentation for their stock or engineering contractors in Southeast Asia requiring detailed certification for project handover. Our commitment to innovation-driven development extends to continually improving these certification processes.
Proactive Gap Analysis and Risk Assessment
When projects involve multiple standards, or when transitioning from one standard to another (e.g., a design based on ASTM but needing to procure EN-compliant materials), conducting a proactive gap analysis is an essential technical recommendation. This involves a detailed, side-by-side comparison of the requirements of the different standards in question, specifically as they apply to the project's unique needs. The goal is to identify any differences ("gaps") in material specifications (chemical, mechanical), testing requirements, dimensional tolerances, or acceptance criteria. For example, if a project designed to ASME B31.3 using ASTM A312 TP316L pipes needs to consider an EN 10217-7 Grade 1.4404 alternative due to availability or client preference, a gap analysis would compare aspects like:
- Chemical Composition: Are the allowable ranges for Cr, Ni, Mo, C, etc., fully overlapping or are there tighter restrictions in one standard?
- Mechanical Properties: Are minimum yield/tensile strengths and elongation values comparable? Are impact testing requirements different, especially at low temperatures?
- Testing & Inspection: Does one standard mandate specific NDT methods or frequencies not required by the other? Are certification requirements (e.g., EN 10204 3.1 vs. standard MTC) different?
- Tolerances: Are dimensional and out-of-roundness tolerances equivalent?
At MFY, our technical team often performs such gap analyses for clients. For an E&C contractor working on an international project, this analysis can inform material selection, identify needs for supplementary testing, or highlight areas where clarification from the end-user or engineering authority is required. This proactive approach helps mitigate risks associated with assuming equivalency where it might not fully exist for the specific application. A table illustrating a simplified gap analysis for a common scenario could be structured as follows:
Parameter | ASTM A312 TP316L (Example) | EN 10217-7 Gr. 1.4404 (Example) | Gap/Difference & Potential Impact |
---|---|---|---|
Carbon (C) max % | 0.035 | 0.030 | EN is slightly stricter; generally interchangeable for weldability. |
Molybdenum (Mo) % | 2.00-3.00 | 2.00-2.50 | EN has a tighter upper limit; check if >2.5% Mo is critical for project. |
Min. Yield Strength | 205 MPa (30 ksi) | 220 MPa (for <3mm thk) | EN may specify higher yield for thinner walls; check design calc. |
Impact Test Req. | Not generally required | May be required by spec/order | If EN mandates impact tests, ASTM material needs supplementary testing. |
NDT (Weld Seam) | Hydro/NDE as per A999 | Specific EN NDT options | Ensure selected NDT method satisfies the governing project code. |
Once gaps are identified, a risk assessment should follow. What is the consequence of a particular difference? Is it a minor administrative point, or does it impact safety, performance, or regulatory compliance? This assessment will guide decisions on whether an alternative material is acceptable, if additional testing is needed, or if the original specification must be strictly adhered to. This systematic, technical approach is key to MFY's ability to provide reliable one-stop solutions and help global clients build efficient and compliant supply chains.
PMI verifies alloy compositionTrue
Positive Material Identification (PMI) is a non-destructive testing method that confirms the chemical composition of alloys against specified standards.
Paper copies are sufficient for standardsFalse
Digital tools for standards management are essential for efficient comparison, updates, and compliance tracking, making paper copies inadequate for modern operations.
Conclusion
Understanding ASTM, ASME, and EN standards is vital for project success in the stainless steel pipe industry. By recognizing their historical context, current applications, challenges, and employing smart strategies with technical diligence, your organization can navigate this complex landscape effectively, ensuring quality and compliance.
-
Discover ASTM’s consensus standards shaping global material reliability ↩
-
Explore how CEN harmonizes technical specs across Europe for seamless trade ↩
-
Understand the BPVC’s role in ensuring safety for pressure-retaining equipment ↩
-
Uncover the design and construction rules for industrial piping systems ↩
-
Learn about European harmonization efforts impacting technical standards ↩
-
Discover how ASTM standards specify detailed materials characteristics ↩
-
Understand the equivalency or differences between ASTM and EN standards for stainless steel ↩
-
Gain insights into the distinct applicability of each standard in the industry ↩
-
Learn effective project management techniques for standard compliance ↩
-
Learn the benefits of PMI in ensuring material compliance and traceability ↩
-
Discover how technical practices enhance accuracy and efficiency in standards application ↩
Have Questions or Need More Information?
Get in touch with us for personalized assistance and expert advice.