Maximizing Corrosion Resistance in Stainless Steel Pipes
Corrosion in stainless steel pipes can lead to costly failures, operational downtime, and safety hazards if not properly addressed. Imagine critical systems compromised or production halted due to unexpected pipe degradation. Understanding and implementing strategies to maximize corrosion resistance is crucial for long-term operational integrity and peace of mind.
Maximizing corrosion resistance in stainless steel pipes involves selecting appropriate grades, understanding environmental factors, applying protective measures, and implementing regular maintenance. These steps ensure durability and prevent premature failures in various industrial applications, safeguarding investments and operational efficiency across sectors.
Corrosion is a silent enemy, often working unseen until significant damage occurs. As someone deeply involved in the stainless steel industry with MFY, I've seen firsthand how a proactive approach to corrosion can save businesses substantial costs and headaches. Let's delve deeper into why this is such a critical aspect of material selection and system design for long-term success.
The challenge with stainless steel, despite its name, is that it's not "stainless" under all conditions; it's "stain-less." The magic lies in its passive chromium oxide layer, but this protective shield can be compromised. From my perspective as Global Business Director at MFY, dealing with diverse markets like India, Southeast Asia, and the Middle East, I've seen how varying environmental aggressors—be it high salinity near coastal areas or industrial pollutants in manufacturing zones—demand meticulous grade selection. For example, a food processing plant in Southeast Asia might grapple with corrosion from cleaning agents, a vastly different challenge than a petrochemical facility in the Middle East facing high-temperature chloride environments. Industry data consistently shows that material failure due to corrosion accounts for a significant portion of maintenance budgets. Research, such as studies by AMPP (formerly NACE International)1, often highlights the billions lost annually worldwide due to corrosion, underscoring the economic imperative of getting material selection and protection right. It's not just about the pipe itself; it's about the integrity of the entire system, the safety of operations, and the overall efficiency of your business.
What are the common corrosion issues in stainless steel pipes?
Unaware of the diverse corrosion types, businesses risk unexpected pipe failures and operational disruptions. These failures can halt operations, cause safety hazards, and lead to costly repairs, ultimately undermining your project's success and financial stability. Identifying common corrosion issues is the first step toward effective prevention and maintaining system integrity.
Common corrosion issues in stainless steel pipes include pitting, crevice corrosion, stress corrosion cracking (SCC), intergranular corrosion, and general corrosion. Each type has distinct mechanisms and visual indicators, requiring specific preventative measures for optimal pipe longevity and performance in various industrial settings.
Understanding these common corrosion types is more than just an academic exercise; it's a practical necessity for anyone specifying or using stainless steel pipes. At MFY, we frequently encounter situations where a lack of awareness about these specific failure modes has led to significant problems for our clients. For instance, a manufacturing company in India might experience pitting corrosion due to localized chloride exposure from their process water, while an engineering contractor in the Middle East could battle stress corrosion cracking in a high-temperature, chloride-rich environment within a refinery. It's not enough to simply know that stainless steel can corrode; you need to understand how it corrodes in your specific application. This nuanced understanding allows for better material selection, improved design considerations, and more effective maintenance strategies. We believe in empowering our clients with this knowledge, moving beyond just supplying pipes to providing comprehensive solutions. The implications of ignoring these issues are far-reaching, impacting not only the immediate cost of replacement but also operational efficiency, safety, and even brand reputation if product contamination occurs. Therefore, taking a moment to familiarize yourself with these potential pitfalls is a crucial investment in the long-term success of your projects. Let's explore these corrosion types in more detail to equip you with the insights needed to protect your stainless steel assets effectively. This knowledge forms the foundation for building resilient and durable piping systems.
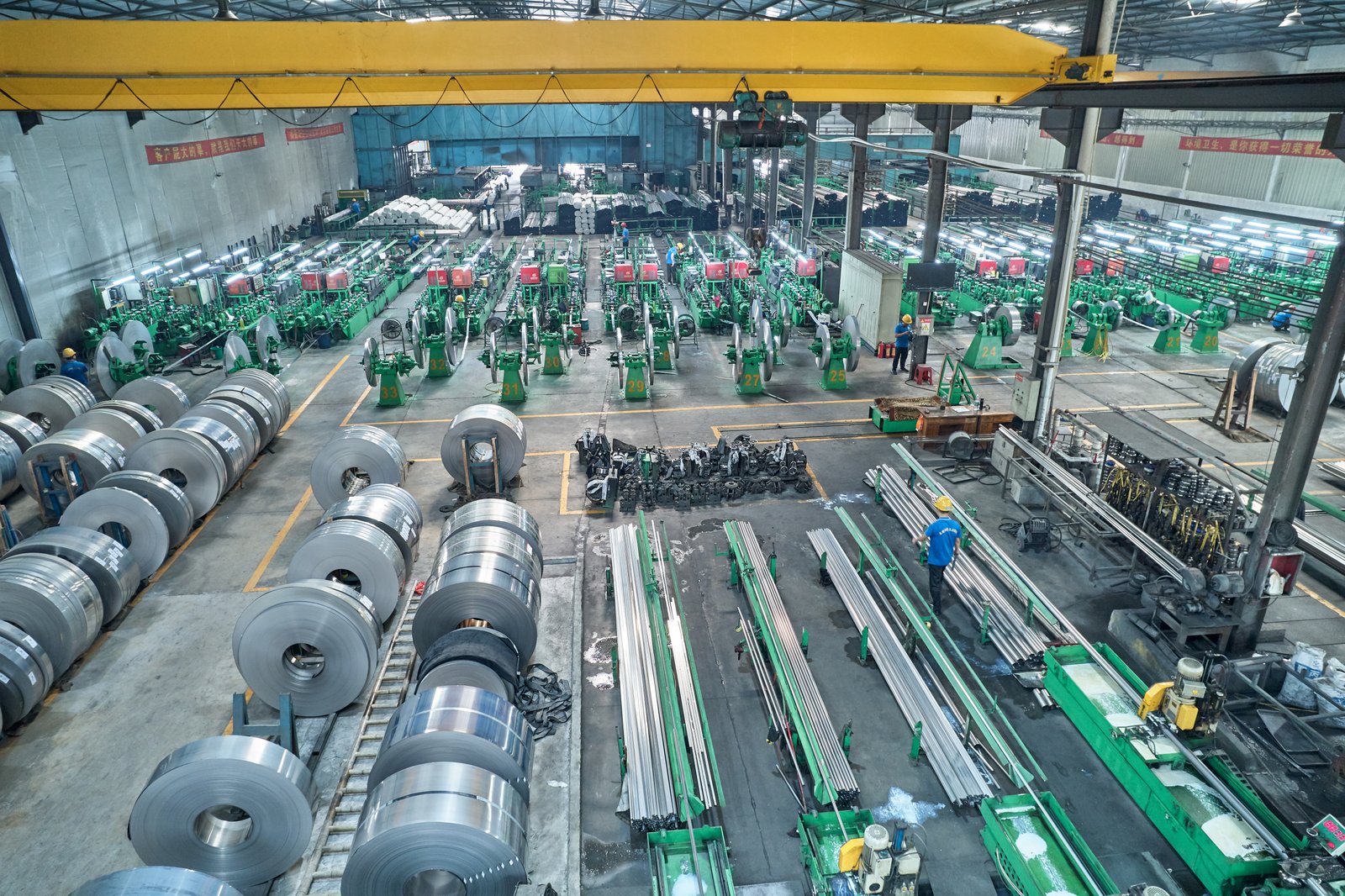
The world of stainless steel corrosion is multifaceted, with each type presenting unique challenges and requiring specific understanding for effective mitigation. As we delve deeper, it's essential to recognize that these aren't isolated laboratory phenomena; they are real-world issues that impact industries daily. At MFY, our experience across various sectors, from manufacturing companies relying on process integrity to engineering and construction contractors building critical infrastructure, has shown that a detailed comprehension of these corrosion mechanisms is invaluable. It enables us to guide our clients, whether they are distributors needing to advise their customers or equipment integrators designing complex systems, towards the most durable and cost-effective solutions. The subsequent sections will break down some of the most prevalent corrosion types, providing insights into their characteristics, common scenarios, and the foundational knowledge needed to combat them. This journey into the specifics of corrosion will not only enhance your technical understanding but also equip you with the foresight to prevent costly failures and ensure the longevity of your stainless steel investments. We'll examine how localized attacks differ from more uniform degradation and why factors like stress or grain boundary conditions can turn a seemingly robust material into a vulnerable component.
Understanding Pitting and Crevice Corrosion
Pitting corrosion is a localized form of attack that results in small holes or "pits" in the metal surface. It's particularly insidious because it can lead to through-wall penetration and failure with very little overall metal loss, making it difficult to detect with general wall thickness measurements. The initiation of pits is often associated with the breakdown of the passive film by aggressive anions, most notably chlorides. Even in environments considered mildly corrosive, the presence of concentrated chlorides, perhaps from seawater spray, certain industrial chemicals, or even food products like ketchup or brines, can rapidly initiate pitting in common austenitic grades like 304 (UNS S30400). A study in the Journal of Materials Engineering and Performance highlighted that stagnant conditions exacerbate this, as they allow corrodents to concentrate locally.
At MFY, we've advised numerous clients, particularly those in coastal regions of Southeast Asia or those in the food processing industry, who were experiencing premature failures in their Type 304L stainless steel piping systems. In one instance, a seafood processing plant was using 304L pipes for waste brine discharge lines. Despite the "L" grade indicating low carbon content (beneficial for weldability and resisting sensitization), the high chloride concentration in the brine, coupled with intermittent flow leading to stagnant conditions in certain sections, led to severe pitting within just two years of operation. Our recommendation, after a thorough site analysis and review of their process fluids, was to upgrade to a higher-molybdenum grade like Type 316L (UNS S31603)2 or, for even greater security, a duplex stainless steel such as 2205 (UNS S32205). These materials offer significantly better pitting resistance, which can be quantified by the Pitting Resistance Equivalent Number (PREN). Typically, PREN is calculated as %Cr + 3.3 %Mo + 16 %N. A 304 grade has a PREN around 18-20, while 316L is around 23-28, and duplex grades like 2205 can exceed 35, offering superior protection.
Crevice corrosion is mechanistically similar to pitting but occurs in confined spaces or crevices where stagnant solutions can accumulate and create differential aeration cells. Common sites include areas under gaskets, seals, bolt heads, lap joints, or even beneath surface deposits. Within the crevice, oxygen depletion occurs, making the crevice area anodic relative to the boldly exposed surface. This leads to an influx of aggressive anions like chlorides into the crevice to maintain charge neutrality, a drop in pH, and accelerated local corrosion. A classic industry example is often seen in flanged connections where an inappropriate gasket material is used or where the design allows for a very tight, unsealed metal-to-metal or metal-to-gasket interface. We had a case with an equipment integrator building water purification skids. They found corrosion occurring under pipe clamps used to secure 304 stainless steel tubing. The stagnant water, combined with trace minerals and occasional sanitizing cycles, created an aggressive microenvironment in these crevices. The solution involved selecting clamps with a more open design to allow flushing and drying, ensuring smoother tube surfaces, and considering an upgrade to 316L for critical components.
The Threat of Stress Corrosion Cracking (SCC)
Stress Corrosion Cracking (SCC) is a particularly dangerous form of corrosion because it can lead to sudden, brittle-like failure of normally ductile materials under tensile stress in a specific corrosive environment. Austenitic stainless steels, such as the widely used 300 series (e.g., 304, 316), are particularly susceptible to chloride-induced SCC at elevated temperatures, typically above 60°C (140°F), although it can sometimes occur at lower temperatures with very high chloride concentrations or specific pH conditions. The cracks are often fine and branched, and can propagate rapidly, leading to catastrophic failure without significant visual warning or overall metal loss. Research published in journals like Corrosion Science frequently details the synergistic effect of tensile stress (which can be applied operational stress or residual stress from fabrication), chloride concentration, and temperature. Even environments with seemingly low bulk chloride levels can become problematic if mechanisms exist for chlorides to concentrate, such as through evaporation on heated surfaces in areas of intermittent wetting and drying.
A manufacturing client of MFY in the petrochemical sector, located in a coastal region of India, faced a challenging SCC problem. They were using Type 304 stainless steel pipes to carry hot process fluids containing trace chlorides, with operating temperatures around 80-90°C. Residual stresses from welding, combined with operational stresses, led to multiple instances of SCC initiating near weld zones and propagating through the pipe wall. The cost of downtime for emergency repairs and lost production was substantial. Our team, in collaboration with their engineers and a corrosion consultant, analyzed the failed components and the operating conditions. The recommendation was a strategic upgrade to duplex stainless steels (like 2205 duplex stainless steel3) for critical sections known to experience the combination of high temperature, chloride exposure, and tensile stress. Duplex grades offer a much higher intrinsic resistance to chloride SCC due to their balanced austenite-ferrite microstructure and higher chromium and molybdenum content. Industry data consistently shows that while Type 304L might crack in a few hundred hours in a standard boiling magnesium chloride test (a very aggressive SCC test), a 2205 duplex can last tens of thousands of hours under similar, or even more aggressive, conditions.
It's crucial to recognize that the "stress" component for SCC isn't always from obvious operational loads. Residual stresses from fabrication processes like welding (due to differential cooling), cold bending, grinding, or even aggressive machining can be sufficient to initiate SCC if the specific environmental conditions (corrodent and temperature) are met. A study by The Welding Institute (TWI) has shown that improper welding procedures or joint designs can introduce very high localized residual tensile stresses, often exceeding the material's yield strength, making the heat-affected zone (HAZ) particularly vulnerable. Therefore, sometimes post-weld heat treatment (stress relieving) can be beneficial for mitigating SCC in certain alloys, though for austenitic stainless steels, this needs extremely careful control to avoid the detrimental effects of sensitization, which can lead to intergranular corrosion. More often, the solution lies in selecting more SCC-resistant alloys from the outset, like duplex or ferritic stainless steels, or rigorously controlling the environment to eliminate one of the key factors (e.g., reducing chloride levels, lowering temperature, or applying corrosion inhibitors if feasible).
Intergranular and General Corrosion Concerns
Intergranular corrosion (IGC), sometimes called intergranular attack (IGA), is a localized form of corrosion where the grain boundaries of the stainless steel become preferentially attacked, while the bulk of the grains themselves remains largely unaffected. In austenitic stainless steels, the most common cause of IGC is "sensitization." This occurs when the material is heated in the temperature range of approximately 450-850°C (842-1562°F), for example, during welding or certain heat treatments. In this range, chromium combines with carbon to form chromium carbides (Cr23C6) which precipitate primarily at the grain boundaries. This process depletes the chromium content in the regions immediately adjacent to the grain boundaries to below the level required for passivity (typically <12% Cr), making these depleted zones anodic relative to the grain interiors and thus susceptible to corrosion in many environments.
We once worked with an engineering and construction contractor building a chemical processing plant that involved extensive on-site welding of Type 304 stainless steel pipes. Several months after the plant was commissioned, leaks started appearing adjacent to some of the welds in lines carrying mildly acidic process fluids. Metallographic analysis of failed sections revealed classic intergranular corrosion, with cracks following the grain boundaries in the heat-affected zones (HAZs) of the welds. The issue was traced back to the standard carbon content of the 304 grade (up to 0.08% C) and potentially slow cooling rates after welding, which allowed sufficient time for chromium carbide precipitation. The primary solution involved replacing the affected sections with Type 304L ("L" for low carbon, typically <0.03% C) stainless steel. The lower carbon content significantly reduces the amount of chromium carbides that can form, thus minimizing sensitization. Alternatively, stabilized grades like Type 321 (titanium-stabilized)4 or Type 347 (niobium/columbium-stabilized) could have been used. These grades contain elements that have a stronger affinity for carbon than chromium, so they form carbides with Ti or Nb instead, leaving chromium in solution to maintain passivity. Data from suppliers like MFY and major producers like Outokumpu or Aperam clearly shows time-temperature-sensitization (TTS) curves, illustrating how low-carbon or stabilized grades offer a much wider safety margin during welding and high-temperature exposure.
General corrosion, also known as uniform corrosion, involves a more or less even attack across the entire exposed surface of the metal. While stainless steels are specifically chosen for their excellent resistance to this form of attack in many environments (thanks to their passive film), they are not immune, especially when exposed to highly aggressive chemicals outside their optimal passivity range. For example, most stainless steels will exhibit significant general corrosion in hot, concentrated non-oxidizing acids like sulfuric acid or hydrochloric acid. The corrosion rate in such cases is often predictable and can be expressed in terms of metal loss per unit time, such as mils per year (mpy) or millimeters per year (mm/yr). Corrosion rate data, often presented in iso-corrosion diagrams (plotting lines of constant corrosion rate on a graph of temperature versus acid concentration), is crucial for selecting the right grade for a specific chemical service. For instance, a distributor partner of MFY in Russia needed to supply pipes for a facility handling moderately concentrated nitric acid at elevated temperatures. While Type 304 stainless steel is generally quite good in nitric acid (which is an oxidizing acid that helps maintain passivity), at higher temperatures and concentrations, a grade with higher chromium content or specific alloying additions (like silicon in some proprietary grades) might be necessary to keep general corrosion rates below an acceptable threshold, typically defined by the end-user (e.g., <0.1 mm/yr for a long design life).
Corrosion Type | Primary Cause(s) | Common Affected Grades | Key Prevention Strategies |
---|---|---|---|
Pitting Corrosion | Localized chloride attack, stagnant conditions | 304, 316 (in severe cases) | Higher Mo grades (316L, Duplex), smooth surface, avoid stagnation, PREN > 30 for chlorides |
Crevice Corrosion | Stagnant solution in confined spaces, O2 depletion, low pH in crevice | 304, 316 | Eliminate crevices, proper gasket design, regular cleaning, crevice-resistant alloys |
Stress Corrosion Cracking (SCC) | Tensile stress + specific environment (e.g., chlorides, high temp >60°C) | 300-series austenitic | Duplex SS, Ferritic SS, reduce stress (applied & residual), control environment (temp, Cl-) |
Intergranular Corrosion | Sensitization (Cr-carbide precipitation at grain boundaries due to heat 450-850°C) | Standard 304, 316 | Low carbon (304L, 316L), stabilized grades (321, 347), solution annealing post-weld |
General Corrosion | Strong acids/alkalis outside passivity range of the alloy | All grades (varies by environment) | Proper grade selection based on chemical environment (concentration, temp), iso-corrosion data |
Stainless steel can corrodeTrue
Despite its name, stainless steel is only "stain-less" and can corrode when its passive chromium oxide layer is compromised by environmental factors.
304L resists all corrosionFalse
304L stainless steel has limitations and can suffer from pitting, crevice corrosion, and SCC in chloride-rich or high-temperature environments despite its low carbon content.
What causes corrosion in stainless steel pipes?
Stainless steel pipes, though renowned for their robustness, can corrode unexpectedly, leading to system failures and costly downtime. This corrosion, often misunderstood, results from specific environmental and material interactions, jeopardizing your operational integrity and safety. Understanding the root causes is absolutely key to preventing such damage and ensuring long-term pipe reliability.
Corrosion in stainless steel pipes is primarily caused by the breakdown of their protective passive chromium oxide layer. Key triggers include exposure to aggressive chemical species like chlorides, acidic or alkaline solutions, elevated temperatures, mechanical stresses, the presence of crevices, and even microbial activity.
Identifying the specific agents and conditions that trigger corrosion is fundamental to selecting the right stainless steel grade and implementing effective mitigation strategies. As a Global Business Director at MFY, I've seen countless instances where a superficial understanding of "stainless" led to costly misapplications and premature failures. It's crucial to remember that it's not just about the material itself, but how it interacts with its unique operational environment. For example, a client with a facility near the coast in India might find their standard Type 304 grade pipes[^5] corroding due to airborne salt deposition, while another client operating an industrial plant in a region of Southeast Asia might face issues from acidic process streams or chemical fumes. Even something as seemingly innocuous as a tiny crevice formed by a pipe support or a residual stress imparted during fabrication can become a focal point for corrosive attack under the right (or, rather, wrong!) conditions. This intricate interplay between the material, its service environment, and various operational factors is complex. At MFY, we aim to help our clients navigate this complexity, ensuring they understand that "stainless" implies superior resistance, not absolute immunity. By exploring the common culprits behind corrosion, we can better equip ourselves to design, specify, and maintain systems that truly last, optimizing both performance and overall cost-effectiveness for our diverse clientele including manufacturing companies, engineering contractors, and distributors.
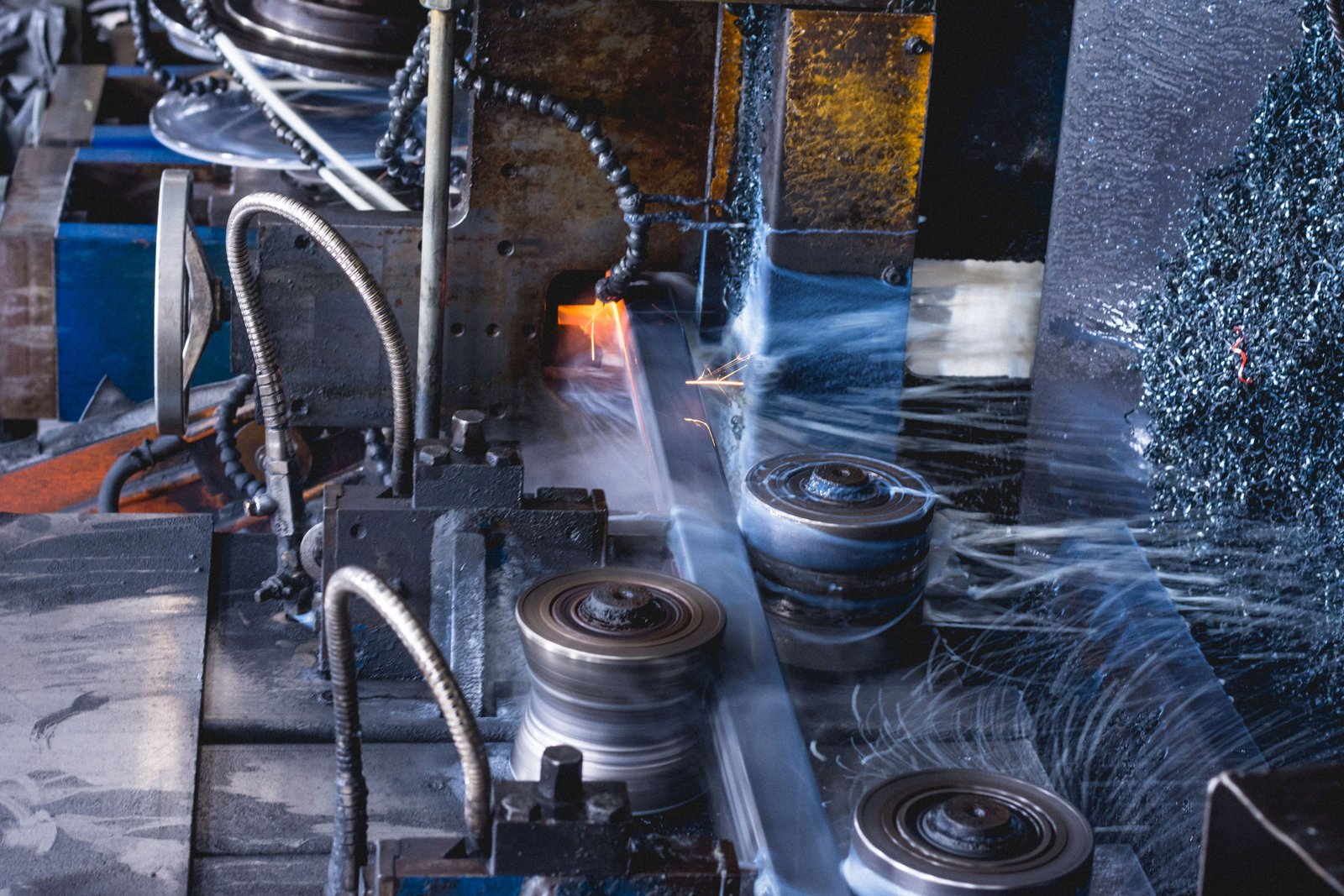
The resilience of stainless steel pipes hinges on the stability of their passive layer, a thin, tenacious film rich in chromium oxide. However, various factors can compromise this protective barrier, initiating the corrosion process. It's a combination of the environment the pipe is in, the inherent characteristics of the specific stainless steel grade chosen, and the conditions it's subjected to during fabrication and operation. As we delve deeper, we'll explore these categories of causes. From my experience at MFY, successfully navigating these challenges requires a holistic view. For instance, a manufacturing company might meticulously select a high-grade stainless steel pipe but overlook the impact of incompatible cleaning chemicals, leading to unexpected corrosion. Similarly, an engineering contractor might design a system with appropriate materials but inadvertently introduce crevices or high residual stresses during installation, creating localized corrosion sites. Understanding these root causes is not just about preventing failures; it's about optimizing the lifecycle performance of the asset. For our clients, whether they are distributors aiming to provide the best advice or equipment integrators striving for system reliability, this knowledge is power. Let's break down the primary factors that can lead to the unwelcome degradation of stainless steel pipes.
Environmental Aggressors: The Chemical Attack
The most notorious environmental aggressor for stainless steels, particularly the common austenitic grades5, is the chloride ion (Cl-). Chlorides are exceptionally effective at locally breaking down the passive chromium oxide (Cr2O3) layer that gives stainless steel its corrosion resistance. This localized breakdown leads to pitting and crevice corrosion. Sources of chlorides are ubiquitous in industrial and natural environments, including seawater (a major concern for our clients in coastal Middle Eastern and Southeast Asian markets), de-icing salts, many industrial process fluids, food products (e.g., sauces, brines), and even some cleaning and sanitizing agents. The aggressiveness of chloride attack is influenced by several factors: chloride concentration, temperature (higher temperatures significantly accelerate attack), pH (low pH can exacerbate it), and the presence of oxidizers. For instance, data from the Nickel Institute and various alloy manufacturers clearly shows that while Type 304 stainless steel might perform adequately in low-chloride water at ambient temperatures, increasing either the chloride concentration or the temperature can dramatically elevate the risk of pitting. This is why for MFY's clients involved in desalination or offshore applications, 304 is rarely sufficient, and we typically start recommendations at 316L or duplex grades.
At MFY, we frequently advise clients in the food and beverage industry across Asia. One client manufacturing various sauces and condiments experienced persistent pitting corrosion in their Type 304L stainless steel transfer pipes and mixing tanks. Analysis revealed that several of their products contained significant levels of salt (NaCl), and their cleaning-in-place (CIP) cycles occasionally used chlorinated sanitizers. The combined effect, especially in areas with slight product stagnation or within crevices around fittings, proved too aggressive for the 304L. We assisted them in evaluating material upgrades, focusing on Type 316L (which contains 2-3% molybdenum) for its enhanced resistance to chloride pitting and crevice corrosion. The Pitting Resistance Equivalent Number (PREN = %Cr + 3.3x%Mo + 16x%N) serves as a practical guide: 304L typically has a PREN around 18-20, whereas 316L is in the 23-28 range. For more demanding chloride environments, super austenitic stainless steels (e.g., 6% Mo alloys with PREN > 40) or duplex stainless steels (e.g., 2205 with PREN ~35, or superduplex with PREN > 40) offer substantially better performance.
Beyond chlorides, other chemical species can also initiate or accelerate corrosion in stainless steel pipes. Strong reducing acids, such as hydrochloric acid (HCl) and sulfuric acid (H2SO4), can readily attack most stainless steels, leading to general corrosion, especially at higher concentrations and temperatures. Oxidizing acids like nitric acid (HNO3) are generally well-tolerated by many stainless steel grades because they help maintain the passive film; however, at very high concentrations, elevated temperatures, or if contaminated with species like chlorides, even nitric acid can become corrosive. We had a challenging case with a distributor supplying pipes for a chemical plant in Russia where complex mixed acid streams were present. Iso-corrosion diagrams, which plot corrosion rates (e.g., in mm/year) as a function of acid concentration and temperature for various alloys, became indispensable tools. These diagrams, available from MFY and other alloy producers, helped identify that for certain highly aggressive streams, even robust austenitic grades were insufficient, pointing towards the need for higher alloyed stainless steels, nickel-based alloys, or even non-metallic alternatives for specific sections of the plant. Furthermore, highly alkaline solutions, especially at elevated temperatures, can also cause corrosion, including caustic stress corrosion cracking in some austenitic grades.
Material Condition and Manufacturing Influences
The inherent condition of the stainless steel material itself, along with how it's processed and fabricated, plays a significant role in its ultimate corrosion susceptibility in service. One of the most critical factors is the risk of sensitization in austenitic stainless steels. As previously discussed, heating standard grades like Type 304 or 316 (with nominal carbon content around 0.04-0.08%) into the range of approximately 450-850°C (842-1562°F) – a common occurrence during welding or improper heat treatment – can lead to the precipitation of chromium carbides at the grain boundaries. This depletes chromium in the adjacent regions, reducing local passivity and making these grain boundary areas highly susceptible to intergranular corrosion (IGC) in many corrosive environments. This is why the development of low-carbon "L" grades (e.g., 304L, 316L, with carbon <0.03%) was a major advancement, as they drastically reduce the amount of carbon available to form deleterious carbides, thereby minimizing sensitization risk during typical welding operations.
I recall a project with an engineering contractor in India who was experiencing premature failures in a newly installed piping system fabricated from standard Type 304 stainless steel. The failures were manifesting as leaks and cracks in the heat-affected zones (HAZs) of many welds. Our investigation, which included on-site visual inspection and laboratory metallographic analysis of failed samples, confirmed sensitization followed by intergranular corrosion. The welding procedures used hadn't fully accounted for the carbon content of the standard 304 grade, and perhaps slower than ideal cooling rates after welding exacerbated the problem. The remedial action involved replacing the most critically affected sections with Type 304L pipe. Industry standards such as ASME B31.3 (Process Piping) and various API standards provide extensive guidance on material selection and fabrication controls to avoid such issues, often recommending the use of 'L' grades or stabilized grades (like Type 321, stabilized with titanium, or Type 347, stabilized with niobium) for welded constructions intended for corrosive service where post-weld solution annealing is not feasible.
Surface finish and cleanliness are also critical manufacturing-related factors influencing corrosion resistance. A rough surface, or one contaminated with exogenous matter like free iron particles from carbon steel fabrication tools or grinding debris, can be a prime site for corrosion initiation. Free iron contamination is a common issue if stainless steel is fabricated in mixed-metal workshops without proper segregation and cleaning protocols. These iron particles can rust (form iron oxide) on the stainless steel surface, not only causing unsightly staining but also potentially creating local galvanic cells that can disrupt the passive layer and initiate pitting. Similarly, surface defects such as deep scratches, scores, weld spatter, or arc strikes can act as initiation sites for pitting or crevice corrosion by mechanically disrupting the passive film and creating local geometries that trap corrodents and hinder repassivation. Best practices, which MFY champions both in its own production of stainless steel products and in advice to clients, include maintaining dedicated stainless steel fabrication areas, using appropriate tools (e.g., stainless steel brushes, grinding wheels designated for stainless steel only), and implementing thorough post-fabrication cleaning and passivation treatments (e.g., according to ASTM A380/A967). Passivation, typically involving nitric or citric acid solutions, removes free iron and other contaminants and helps to chemically enhance the uniformity and robustness of the protective passive layer. Studies have consistently shown that smoother, cleaner surfaces, such as those achieved by electropolishing, can offer superior corrosion resistance compared to mechanically polished or as-welded surfaces, especially in aggressive environments.
Operational Factors and Mechanical Damage
The operational conditions a stainless steel pipe experiences during its service life significantly influence its corrosion behavior. Temperature is a major accelerator for most chemical and electrochemical corrosion reactions; a widely cited rule of thumb is that corrosion rates can approximately double for every 10°C (18°F) increase in temperature. This is particularly true for localized corrosion mechanisms like pitting and chloride stress corrosion cracking (SCC). For instance, austenitic stainless steels that are generally resistant to chloride SCC at ambient temperatures can become highly susceptible when temperatures rise above about 60°C (140°F), especially if tensile stresses and sufficient chloride concentrations are present. The flow rate of the fluid within the pipe also plays a critical role. Very low flow rates or stagnant conditions can lead to the settling of suspended solids, deposit formation, and the creation of concentration cells or crevice-like conditions, all of which can promote localized corrosion. Conversely, extremely high flow rates, especially if the fluid contains entrained abrasive solid particles (like sand or catalyst fines), can lead to erosion-corrosion. This mechanism involves the mechanical removal or damage of the passive film by the abrasive action of the flowing fluid, continuously exposing fresh, active metal to the corrosive environment, leading to accelerated metal loss.
We worked with an equipment integrator whose end-client, a large power generation facility, was experiencing issues with their Type 316L stainless steel cooling water intake pipes. The water source, a brackish river estuary, had a moderate silt and sand content, particularly during certain seasons. In areas of high turbulence and fluid velocity, such as at pipe bends, reducers, and near pump impellers, they observed a characteristic pattern of wear combined with corrosion, indicative of erosion-corrosion. While stainless steel generally has good erosion resistance compared to carbon steel, the constant impingement of abrasive particles was sufficiently severe to compromise the passive layer, allowing corrosion to proceed at an accelerated rate. The solution involved a multi-pronged approach: design modifications to streamline flow and reduce turbulence in critical areas, evaluation of more erosion-resistant materials (such as duplex stainless steels or even certain nickel alloys known for better performance in abrasive slurries), and improved filtration upstream to reduce the particulate load. Data from organizations like the Electric Power Research Institute (EPRI) often contains valuable insights and case studies on material performance under such specific power plant operating conditions.
Mechanical damage sustained during shipping, handling, installation, or even in-service can also create nucleation sites for corrosion. Dents, scratches, gouges, or arc strikes disrupt the protective passive layer. If these damaged areas are not properly repaired (e.g., by grinding smooth and re-passivating) and if the service environment is sufficiently aggressive, corrosion can preferentially initiate at these points. Furthermore, as discussed in the context of SCC, applied or residual tensile stresses are a critical ingredient for this failure mode. If pipes are improperly supported leading to excessive bending stresses, subjected to significant vibration that induces cyclic stresses, or if they retain high residual stresses from cold working (e.g., U-bending) or welding without adequate stress relief, then the risk of SCC becomes significantly elevated if the specific corrosive environment (e.g., hot chlorides for austenitic stainless steels) is also present. We always emphasize to our target clients—manufacturing companies setting up process lines, engineering contractors overseeing large installations, and distributors supplying materials for various projects—the paramount importance of proper handling protocols, adherence to installation best practices (including alignment and support), and stress management considerations in piping system design and assembly to maintain the inherent corrosion resistance of the material and prevent premature, unexpected failures.
Causative Factor Category | Specific Cause Examples | Impact on Stainless Steel | MFY's Typical Client Concern/Example |
---|---|---|---|
Environmental Aggressors | Chlorides (seawater, industrial fluids, food salts), Acids (H2SO4, HCl), Alkalis, High Temperatures | Breakdown of passive layer, pitting, crevice corrosion, SCC, general corrosion | Food processor in SE Asia (chlorides in sauces/cleaners); Chemical plant in Russia (mixed acid streams); Desalination plant in Middle East (hot brine) |
Material Condition | Sensitization (high carbon + heat 450-850°C), Surface roughness/contamination (free iron), Inclusions | Intergranular corrosion, localized corrosion initiation at defects/contaminants | Engineering contractor in India (sensitized welds in standard 304); Need for clean fabrication practices to avoid free iron from carbon steel tools |
Operational/Mechanical | Stagnant or high-velocity/turbulent flow, Abrasive particles, Applied/Residual Stress, Physical damage (dents, scratches) | Deposit/crevice corrosion, erosion-corrosion, SCC, localized attack at damage sites | Power plant (erosion-corrosion in cooling water pipes with silt); Petrochemical plant (SCC due to combined heat, chlorides, and operational stress) |
Chlorides break passive layerTrue
Chloride ions are the most aggressive environmental factor that locally destroys stainless steel's protective chromium oxide layer.
304L resists all acidsFalse
Type 304L stainless steel is vulnerable to strong reducing acids like hydrochloric acid, despite its general corrosion resistance.
How does corrosion impact the functionality and longevity of stainless steel pipes?
Corrosion in stainless steel pipes isn't just a cosmetic issue; it silently and progressively degrades system integrity. This degradation can lead to a cascade of problems, including leaks, reduced flow efficiency, structural failures, and costly operational shutdowns. Understanding these far-reaching impacts underscores the vital need for proactive and comprehensive corrosion management strategies.
Corrosion significantly impacts stainless steel pipes by reducing wall thickness, leading to leaks or catastrophic bursts, and decreasing overall structural integrity. It can also cause blockages from corrosion products, contaminate process fluids, and ultimately shorten the pipe's operational lifespan, necessitating premature and costly replacement.
The consequences of corrosion extend far beyond the immediate sight of rust (which on stainless steel might appear as reddish-brown stains if iron contamination is present, or more subtle discoloration) or a minor leak. At MFY, we deal with global clients across a vast spectrum of sectors – from precision manufacturing companies to large-scale engineering and construction contractors – and the stories often share a common thread: an underestimation of corrosion's potential impact frequently leads to significant, and often entirely preventable, operational and financial setbacks. Imagine a critical pipeline in a chemical processing plant; a corrosion-induced failure there doesn't just mean the cost of replacing a section of pipe. It translates into emergency shutdown procedures, substantial lost production revenue, potential safety hazards for personnel, and the risk of environmental contamination with associated regulatory fines and reputational damage. The ripple effects can be immense and felt throughout the business. For our distributor and trader partners, supplying a pipe that fails prematurely due to corrosion can severely damage their hard-earned reputation and lead to complex and costly warranty claims. Even for less critical applications, the cumulative cost of repeated repairs, maintenance interventions, and eventual replacements due to ongoing corrosion issues can become a major drain on resources and operational budgets. Therefore, appreciating the full spectrum of how corrosion undermines both the immediate functionality and the long-term longevity of stainless steel pipes is crucial for making informed decisions about material selection, system design, and ongoing maintenance protocols. It's an investment in reliability, safety, and peace of mind.
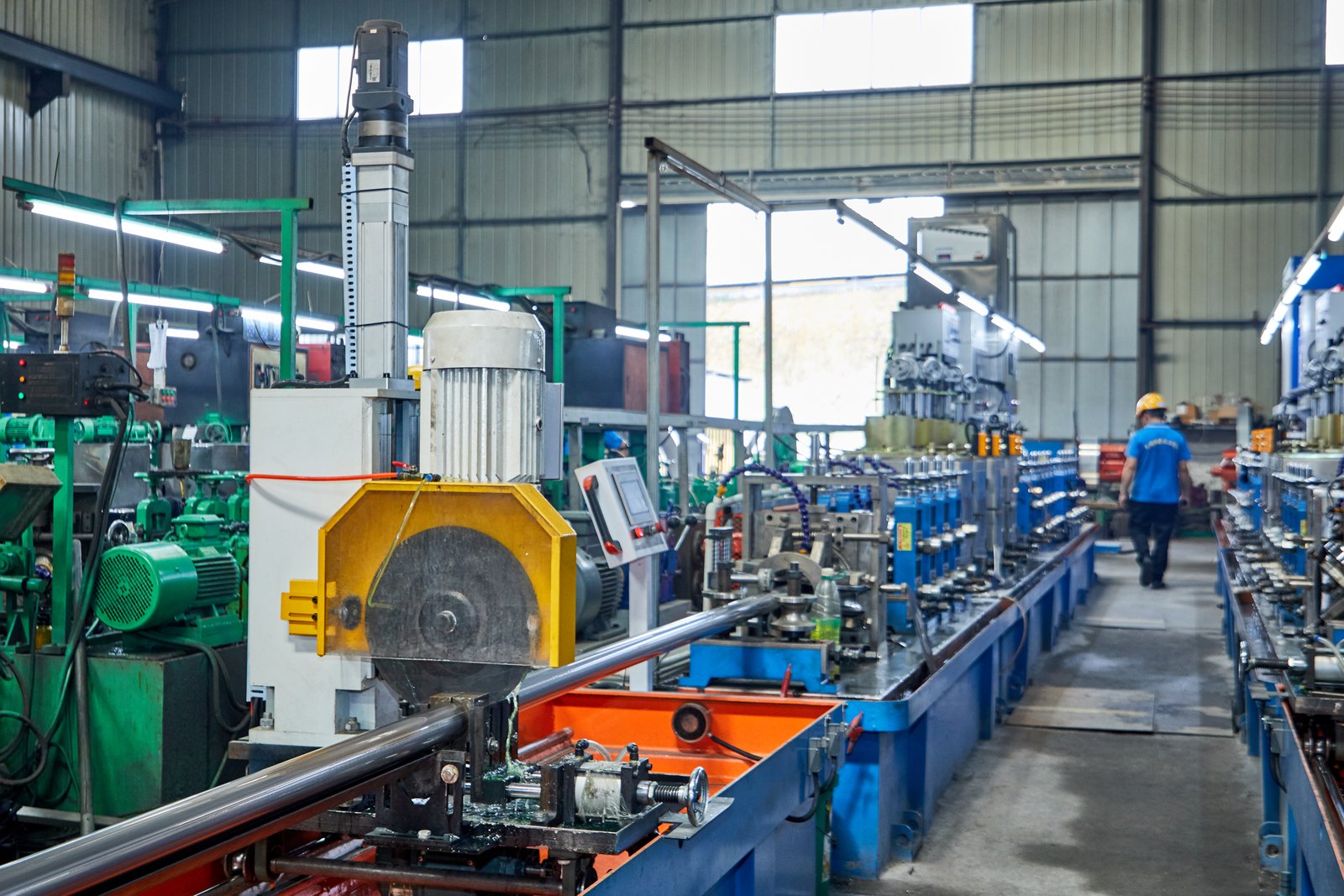
The degradation of stainless steel pipes due to corrosion is a multifaceted problem, affecting systems in ways that are both obvious and subtle. From my experience at MFY, working with clients across diverse industries and challenging environments like those in India, Southeast Asia, and the Middle East, the impacts are consistently significant. We've seen manufacturing companies struggle with product contamination due to corroded pipes, engineering contractors face project delays and cost overruns from unexpected failures, and distributors manage the fallout from supplying materials that didn't meet longevity expectations in a specific service. It’s not just about a hole in a pipe; it's about the safety of personnel, the integrity of the product, the efficiency of the operation, and the overall economic viability of the asset. The following discussion will explore these impacts in three key areas: the direct compromise of structural integrity leading to leaks, the reduction in operational efficiency and potential for disruptions, and ultimately, the shortening of service life and increase in overall lifecycle costs. Understanding these consequences is paramount for anyone involved in the design, operation, or maintenance of stainless steel piping systems.
Compromised Structural Integrity and Leakage
The most direct and perhaps most obvious impact of corrosion on stainless steel pipes is the physical loss of metal, which progressively thins the pipe wall. Whether this occurs as uniform general corrosion slowly reducing the overall thickness across a large area, or as highly localized attacks like pitting or crevice corrosion6 creating deep, narrow penetrations, the end result is a structurally weakened pipe. This reduction in effective wall thickness directly compromises the pipe's pressure-containing capability. Industry codes and standards, such as ASME B31.3 for process piping7 or API standards for oil and gas pipelines, mandate minimum required wall thicknesses calculated based on design pressure, operating temperature, material allowable stress, and any corrosion allowances. As corrosion proceeds and the actual wall thickness diminishes, it can eventually fall below this critical minimum, leading to a high risk of rupture, bursting, or catastrophic failure under normal or upset operational pressures.
I recall a particularly illustrative case with an engineering contractor who was responsible for a large water treatment facility. They had specified and installed a standard grade of austenitic stainless steel pipe for a line carrying moderately aggressive treated water, which, unknown to them initially, had fluctuating chloride levels and occasional pH drops. Over several years of operation, undetected pitting corrosion had significantly thinned the pipe wall in multiple localized areas. One day, a pit penetrated completely through the wall, leading to a substantial leak. The ensuing water damage to adjacent sensitive electronic equipment and the emergency shutdown required for immediate repairs and subsequent inspection of the entire line cost the facility significantly more—several orders of magnitude more—than if they had initially invested in a more corrosion-resistant grade like 316L or duplex stainless steel, or had implemented a more rigorous water chemistry monitoring and corrosion inspection program. According to a landmark study by NACE International (now AMPP) on the costs of corrosion in the U.S., and similar studies in other industrialized nations, corrosion costs hundreds of billions of dollars annually, with failures in piping systems being a major contributing factor across nearly all industrial sectors. This just highlights the enormous economic scale of the problem we are dealing with.
For many of MFY's clients, particularly manufacturing companies in the food, beverage, pharmaceutical, or semiconductor industries, such leaks have consequences beyond just structural failure and fluid loss; they can lead to critical product contamination. Even a microscopic pinhole leak in a stainless steel pipe carrying a high-purity product, a food ingredient, or a pharmaceutical compound can allow the ingress of external contaminants (bacteria, process fluids from an outer jacket, cleaning agents) or the egress of the valuable product itself. This creates a severe hygiene hazard, can lead to batch spoilage, product recalls, loss of consumer confidence, and significant brand damage. In these highly sensitive industries, MFY often emphasizes that the incremental cost of selecting a higher-grade stainless steel pipe, perhaps one with an electropolished internal surface finish for enhanced cleanability and corrosion resistance, is often a very small price to pay when compared to the potentially catastrophic financial and reputational costs of a single contamination event. Thus, structural integrity in these contexts is not just about pressure containment; it's intrinsically linked to product purity, safety, and quality assurance.
Reduced Efficiency and Operational Disruptions
Corrosion doesn't just cause pipes to leak or burst; it can also significantly impair the operational efficiency and reliability of the entire piping system and connected equipment. The accumulation of corrosion products (such as rust scale if iron contamination is present, or other metallic oxides and salts) on the internal surfaces of pipes leads to increased surface roughness. This increased roughness, in turn, results in higher frictional losses as fluids flow through the system. According to fluid dynamics principles (e.g., the Darcy-Weisbach equation8), the friction factor is directly related to relative roughness. Therefore, for extensive piping networks, this can translate into noticeably higher energy consumption by pumps to maintain the required flow rates, leading to increased operational costs over the lifespan of the system.
Consider a scenario we encountered with a client who manages a large district cooling system for an industrial complex in a humid Southeast Asian country. Their stainless steel pipes, after several years of service carrying treated cooling water which still had some scaling tendencies and microbial activity, had developed significant internal tuberculation (nodules or mounds of corrosion product and biomass). This not only effectively reduced the internal diameter of the pipes but also dramatically increased the internal surface roughness. They observed a gradual but persistent decrease in flow rates to end-users and a corresponding increase in pump energy usage as the system tried to compensate. A study published in the Journal of Pipeline Systems Engineering and Practice often discusses how even a modest increase in internal pipe roughness can have a substantial impact on hydraulic efficiency and pumping costs. In this client's case, the operational cost increase attributed to lost efficiency was substantial enough to warrant a major pipe cleaning operation using chemical and mechanical methods and, in some severely affected sections, complete replacement.
Furthermore, dislodged corrosion products or scale can travel downstream and cause blockages or malfunctions in sensitive equipment connected to the piping system. Valves (especially control valves with fine tolerances), heat exchanger tubes (leading to reduced heat transfer efficiency and potential hot spots), spray nozzles, small-bore instrumentation lines, and filters are all susceptible to fouling or clogging by particulate matter originating from corroded pipe surfaces. This can lead to process upsets, inconsistent product quality, equipment malfunction requiring unplanned shutdowns for cleaning or repair, and increased maintenance frequency. For instance, an equipment integrator using stainless steel pipes for a sophisticated hydraulic control system might find that fine corrosion particles, perhaps from a section of pipe that was inadvertently contaminated during fabrication, are causing premature wear of seals and clogging of precision servo valves, leading to erratic system performance and costly component replacements. The impact here is a clear reduction in system reliability and an increase in both direct maintenance costs and indirect costs associated with lost production or compromised performance. At MFY, we consistently stress to our clients that maintaining a clean and smooth internal pipe surface through appropriate initial material selection, proper fabrication and cleaning, and effective water treatment (if applicable) is key to ensuring sustained operational efficiency and minimizing these disruptive impacts.
Shortened Service Life and Increased Lifecycle Costs
Ultimately, unchecked or poorly managed corrosion significantly shortens the effective service life of stainless steel pipes and associated equipment. Pipes that might have been designed and expected to last for 20, 30, or even more years could fail in a fraction of that time if the chosen material is not genuinely suitable for the actual service environment, if fabrication quality is poor, or if maintenance and inspection are neglected. This premature failure necessitates early replacement, leading to unplanned and often substantial capital expenditure. The true cost of such a replacement isn't just the material cost of the new pipe; it encompasses a wide range of associated expenses, including the labor for removing the old pipe and installing the new one, potential system redesign if upgrades are needed, procurement and installation of new fittings or supports, the cost of any specialized equipment required for the replacement (e.g., cranes, scaffolding), and, critically, the often very significant costs associated with the production downtime incurred during the entire repair or replacement process.
A comprehensive report by NACE International (now AMPP) consistently highlights that a very significant portion of maintenance budgets in many key industries (e.g., oil and gas, chemical processing, power generation, pulp and paper) is allocated specifically to dealing with corrosion-related issues, including inspection, prevention, and repair. For example, in the global oil and gas industry, pipeline integrity management, a large and critical part of which involves sophisticated corrosion monitoring, control, and repair strategies, represents a multi-billion dollar annual expense. When we at MFY work with clients on large capital projects, especially those with long intended design lives, such as new infrastructure developments in India or major industrial facilities in the Middle East, we strongly encourage the adoption of a lifecycle cost analysis (LCCA) approach to material selection. An LCCA considers not just the initial procurement and installation cost of the piping system, but also all anticipated future costs, including inspection, maintenance, repair, potential replacement costs, and the economic impact of any associated downtime over the entire projected life of the system. Very often, a more corrosion-resistant (and therefore often initially more expensive) stainless steel grade, or a system incorporating better design features for corrosion control, proves to be significantly more economical in the long run when all these lifecycle factors are considered.
The table below illustrates a simplified conceptual comparison. Imagine two stainless steel pipe options being considered for a moderately corrosive chemical process environment. Option A is a standard stainless steel grade that is cheaper initially but has a shorter expected lifespan in this specific service due to a higher anticipated corrosion rate. Option B is a higher-alloyed, more corrosion-resistant stainless steel grade that has a higher upfront material cost but is expected to last significantly longer with lower maintenance needs. Over a 30-year project design life, Option B, despite its higher initial investment, could well result in substantially lower total lifecycle costs due to fewer (or no) required replacements, less frequent and less intensive inspection, and significantly reduced production losses from corrosion-related downtime. This kind of holistic, long-term financial perspective helps our target clients—be they manufacturing companies aiming for operational excellence, engineering contractors delivering turn-key projects, or distributors advising their customers on optimal material choices—make more informed, value-driven decisions that balance upfront investment with overall operational reliability and long-term cost-effectiveness.
Feature | Option A (e.g., Standard Grade SS like 304L) | Option B (e.g., Higher Alloy SS like Duplex 2205 or 316L) |
---|---|---|
Initial Material Cost | Lower | Higher (e.g., 1.5x - 2.5x of Option A) |
Expected Lifespan in Service | 8-12 years | 25-30+ years |
Estimated Corrosion Rate | 0.1 - 0.2 mm/year (localized or general) | <0.02 - 0.05 mm/year (localized or general) |
Number of Replacements (30yr) | 2-3 | 0-1 (potentially none for 30 years) |
Associated Downtime Costs | High (for 2-3 full replacement cycles) | Minimal to Low (for potential minor repairs only) |
Inspection/Maintenance Freq. | Higher / More Intensive | Lower / Less Intensive |
Estimated Lifecycle Cost | Significantly Higher | Potentially Lower |
Corrosion reduces pipe wall thicknessTrue
Corrosion physically removes metal from pipe walls, leading to thinning that can compromise structural integrity and pressure containment.
Corrosion only causes visible rustFalse
Corrosion in stainless steel often occurs as subtle pitting or crevice corrosion that may not be immediately visible, while still causing significant damage.
What solutions can be employed to enhance corrosion resistance in stainless steel pipes?
Standard stainless steel grades may not always suffice in particularly aggressive or challenging environments, risking premature pipe failure. This oversight in material selection or system design can lead to unexpected corrosion, disruptive system downtime, and escalating maintenance costs. Employing a range of targeted solutions can significantly enhance corrosion resistance, ensuring pipe longevity and operational reliability.
To enhance corrosion resistance in stainless steel pipes, key solutions include selecting appropriate higher-alloyed grades (e.g., with increased Cr, Mo, N), applying suitable protective coatings or linings, utilizing cathodic or anodic protection where applicable, controlling the operational environment (e.g., inhibitors, deaeration, pH control), and implementing proper design practices to avoid crevices and stress concentrators.
Simply acknowledging the ever-present threat of corrosion isn't enough; as engineers, operators, and suppliers, we need actionable, effective strategies to combat it robustly. At MFY, our extensive experience across diverse global markets – from the demanding industrial landscapes of India, with its varied climatic and process conditions, to the rapidly developing infrastructure projects in Southeast Asia, often facing tropical humidity and marine influences – has unequivocally shown that a multi-faceted and tailored approach9 to enhancing corrosion resistance yields the best and most sustainable results. It's not always about defaulting to the most expensive, exotic alloy; sometimes, intelligent design modifications, careful control of the operating environment, or the strategic application of protective technologies can make a profound difference at a more manageable cost. For our manufacturing clients, ensuring the longevity and integrity of their process piping is absolutely critical for maintaining uninterrupted production schedules and product quality. For the engineering and construction contractors we partner with, delivering durable and reliable installations is paramount to their professional reputation and project success. And for our valued distributors, offering products with clearly demonstrable resistance to common and specific corrosive challenges adds significant value to their portfolio and strengthens customer trust. The available solutions span a wide spectrum, from fundamental innovations in material science and alloying to practical engineering principles and advanced electrochemical techniques. By thoroughly exploring these various avenues, we can collaboratively tailor a corrosion mitigation strategy that is both technically effective and economically viable for specific applications, moving decisively beyond a simplistic, one-size-fits-all mentality.
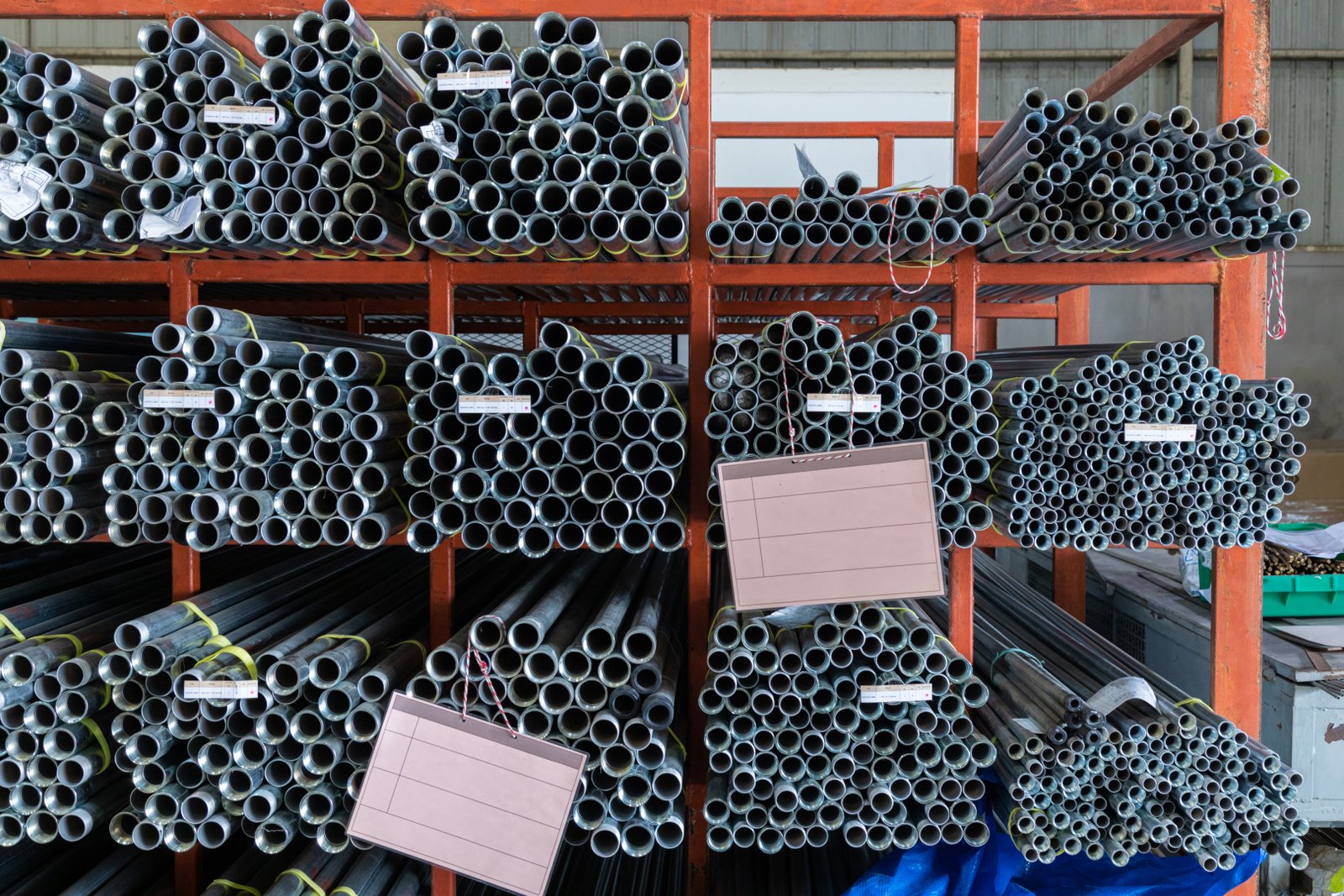
Enhancing the corrosion resistance of stainless steel pipes is a proactive endeavor, requiring a combination of informed choices and strategic interventions. It begins with the fundamental decision of material selection but extends into how the system is designed, fabricated, and operated. From my role at MFY, I've seen that the most successful outcomes arise when these elements are considered holistically. For example, a client in the Middle East dealing with high-salinity seawater for cooling systems might benefit from a combination of a duplex stainless steel (advanced material selection) and a carefully designed intake screening system to minimize abrasive particles (environmental control/design). Similarly, a manufacturing company using aggressive cleaning chemicals might opt for a highly resistant alloy or, in some cases, a specialized lining for their stainless steel pipes. The goal is always to create a robust defense against the specific corrosive threats anticipated in the application. Let's explore some of the primary categories of solutions that can be deployed to bolster the resilience of your stainless steel piping systems, ensuring they deliver the performance and lifespan expected. This exploration will cover advancements in materials, the use of barriers, and methods to modify the corrosivity of the environment itself.
Advanced Material Selection and Alloying
The first, and often most impactful, line of defense against corrosion in stainless steel piping systems is the judicious selection of the right stainless steel grade specifically suited for the anticipated service environment. The term "stainless steel" encompasses a vast family of alloys, and their corrosion resistance characteristics vary significantly based on their precise chemical composition. Key alloying elements that govern corrosion resistance include chromium (Cr), molybdenum (Mo), nickel (Ni), and nitrogen (N). Chromium is the primary element responsible for forming the passive, self-repairing chromium oxide (Cr2O3) layer that gives stainless steel its characteristic resistance. Generally, increasing the chromium content (typically from 10.5% up to 27% or more) improves resistance to general corrosion and high-temperature oxidation. Molybdenum is particularly effective in enhancing resistance to localized corrosion mechanisms like pitting and crevice corrosion, especially in environments containing chlorides; additions typically range from 2-3% in grades like 316L up to 6-7% in super austenitic grades. Nickel primarily serves to stabilize the austenitic microstructure, enhancing formability and toughness, and also contributes to resistance in certain reducing acid environments and against stress corrosion cracking. Nitrogen, when added to austenitic and particularly duplex stainless steels, acts as an austenite stabilizer, increases strength, and significantly improves resistance to pitting and crevice corrosion, working synergistically with molybdenum.
As a major supplier of stainless steel products, MFY frequently guides clients through this critical material selection process. For instance, while Type 304L (UNS S30403, typically ~18% Cr, 8-10% Ni) is an excellent workhorse alloy suitable for many mildly corrosive environments such as atmospheric exposure, fresh water, and food product contact (where chlorides are low), it would be wholly inadequate if a manufacturing company in a coastal region of the Middle East intended to use it for handling raw seawater or concentrated brine solutions. In such a scenario, our recommendation would typically start with Type 316L (UNS S31603, ~17% Cr, 10-12% Ni, 2-3% Mo) as a minimum baseline, or more robustly, duplex stainless steels like Grade 2205 (UNS S32205, ~22% Cr, 5% Ni, 3% Mo, 0.15% N). The Pitting Resistance Equivalent Number (PREN = %Cr + 3.3x%Mo + 16x%N for austenitic/duplex) is an invaluable empirical metric used here. For reliable long-term performance in seawater applications, a PREN value greater than 35 is often desired, and for more critical or warmer seawater applications, PREN > 40 (achieved by super duplex or 6% Mo super austenitic grades) is commonly specified. For example, extensive data from producers like Outokumpu or Sandvik shows that a 6% Moly super austenitic grade like 254 SMO® (UNS S31254, PREN ~43) performs exceptionally well in heavily chlorinated seawater cooling systems where even 316L (PREN ~25) would suffer severe pitting and crevice corrosion within a short period.
The choice of an advanced alloy isn't solely dictated by pitting resistance. For applications requiring superior resistance to chloride stress corrosion cracking (SCC), to which standard 300-series austenitic grades are susceptible at elevated temperatures, ferritic stainless steels (like Type 444 or 446) or, more commonly, duplex stainless steels offer significantly better performance. If the environment involves strong reducing acids (e.g., sulfuric acid at intermediate concentrations), then nickel-based alloys (e.g., Alloy C-276, Alloy 20) or specialized high-nickel, high-molybdenum stainless steels might be the only viable metallic options. The key to successful material selection is a thorough and accurate characterization of all relevant process conditions – including detailed chemical composition of the fluid, concentration ranges, operating and upset temperatures, pressures, pH levels, velocity, and the presence of any abrasives or contaminants. MFY’s fully integrated supply chain and strong relationships with major mills enable us to source and provide a wide spectrum of these standard and specialized grades, ensuring our clients, from large engineering contractors to niche equipment integrators, receive the optimal material tailored to their specific and often demanding application needs.
Protective Coatings and Linings
In certain situations, either for overriding economic reasons where the cost of a highly alloyed stainless steel for the entire system is prohibitive, or when even the most advanced alloys might not offer sufficient resistance to exceptionally aggressive chemical attack or wear, the application of protective coatings or linings onto a more standard stainless steel substrate can be a highly effective and viable solution. Coatings function by creating a continuous physical barrier that isolates the stainless steel surface from direct contact with the corrosive environment. The range of available coatings is extensive and includes organic coatings (e.g., epoxies, polyurethanes, vinyl esters, fluoropolymers like PVDF or ECTFE, and fusion-bonded epoxies - FBE), inorganic coatings (e.g., ceramic coatings, glass coatings), and sometimes metallic coatings (though galvanizing, for example, is rarely used on stainless steel due to galvanic incompatibility issues). The long-term effectiveness and integrity of any coating system depend critically on meticulous surface preparation of the stainless steel substrate (to ensure cleanliness and achieve the required anchor profile for adhesion), precise application technique (following manufacturer recommendations for thickness, curing, etc.), and the inherent compatibility of the chosen coating material with all aspects of the service environment (including chemical exposure, temperature range, potential for abrasion or impact, and UV exposure if outdoors).
For example, an engineering contractor might be designing a large chemical waste treatment system where the bulk of the piping can be cost-effectively constructed from Type 316L stainless steel, but certain specific sections or vessels are anticipated to experience exposure to exceptionally aggressive chemical mixtures or high abrasive wear for which 316L is unsuitable. Instead of fabricating the entire system from an expensive superalloy or nickel alloy, applying a specialized chemically resistant coating (like a thick-film epoxy novolac or a fluoropolymer sheet lining) to the internal surfaces of only those critical sections could present a much more cost-effective engineered solution. We've seen numerous successful applications in the municipal and industrial wastewater treatment industries where high-build epoxy or polyurethane linings are applied to stainless steel pipes and tanks to provide long-term protection against a challenging combination of corrosive hydrogen sulfide (H2S) gas, acidic condensates, and abrasive solids. According to guidelines from organizations like SSPC (The Society for Protective Coatings) and NACE (now AMPP), achieving the specified level of surface cleanliness (e.g., SSPC-SP5 White Metal Blast) and surface profile (e.g., 2-4 mils) is absolutely crucial for optimal coating adhesion and long-term performance on stainless steel. A poorly adhered or damaged coating can, paradoxically, sometimes accelerate localized corrosion if it allows corrodents to become trapped between the coating and the substrate, potentially leading to issues like cathodic disbondment or severe under-film corrosion.
Linings, which are typically thicker and more robust than coatings, can also be employed to provide a high level of corrosion protection. These might include elastomeric linings like natural or synthetic rubber (excellent for abrasion and some chemical resistance), thermoplastic linings like PTFE (Teflon®), PFA, FEP, or PVDF (offering outstanding resistance to a very wide range of aggressive chemicals, even at high temperatures), or even glass lining (vitreous enamel) for extreme chemical inertness. For instance, PTFE-lined stainless steel pipes and fittings are commonly used in the pharmaceutical, semiconductor, and fine chemical industries for safely handling ultra-pure water, aggressive solvents, strong acids, and reactive intermediates where even high-nickel alloys might corrode or, equally importantly, cause unacceptable metallic ion contamination of the product. In such composite systems, the stainless steel outer pipe provides the necessary mechanical strength, pressure containment, and external corrosion resistance, while the inert internal liner provides the primary barrier against internal corrosion and product contamination. While extremely effective, lined pipes have their own set of design and operational considerations, such as potential damage to the liner during installation or due to excessive thermal cycling (due to differential thermal expansion between the liner and the steel), the integrity and design of flanged joints and nozzles to ensure a continuous protective barrier, and limitations on vacuum service for some liner types.
Environmental Control and Electrochemical Methods
Modifying the operational environment to render it less corrosive to the stainless steel pipes is another important and often highly effective strategy for enhancing corrosion resistance. This can be achieved through several distinct techniques. Chemical corrosion inhibitors can be added in small concentrations to the process stream or operating fluid to significantly reduce corrosion rates. Inhibitors function in various ways: some adsorb onto the metal surface to form a thin, protective film that acts as a barrier; others passivate the metal by promoting the formation of a more stable oxide layer; while some scavenge aggressive species (like dissolved oxygen or H2S) from the environment. For example, in closed-loop cooling water systems, which MFY often supplies pipes for in industrial facilities, specific inhibitor packages (often proprietary blends containing phosphonates, molybdates, or organic film-formers) are routinely used to protect stainless steel components (and other metals in the system) from general corrosion, pitting, and scaling. Deaeration, the physical or chemical removal of dissolved oxygen from water or other process fluids, can dramatically reduce corrosion rates in many systems, as oxygen is often a key cathodic reactant in the electrochemical corrosion process. This is particularly effective for carbon steel but can also benefit stainless steels by reducing the driving force for certain corrosion cells, especially under stagnant conditions.
Adjusting and controlling the pH of the process fluid within an optimal range can also be critical for maintaining the passivity of stainless steel. Stainless steels exhibit varying degrees of resistance depending on the pH of the solution. For instance, many common austenitic grades are susceptible to accelerated general corrosion or pitting in highly acidic (low pH) or, in some cases, highly alkaline (high pH) conditions, particularly if these are outside their established passive range for the given temperature and chemical composition. Maintaining the pH within a safe operating window, often near neutral or slightly alkaline for many water systems, through controlled addition of acids or alkalis, can significantly extend pipe life and prevent unexpected failures. We had a client, a large-scale manufacturing company with extensive process water recirculation, that was experiencing sporadic but troubling corrosion issues in their 316L stainless steel piping. An investigation revealed that their process led to periodic, uncontrolled pH drops into a more aggressive acidic range. By implementing a more robust automated pH monitoring and control system, they were able to stabilize the pH within the recommended range for 316L and significantly reduced their corrosion rates and maintenance interventions. Extensive research data and guidelines from organizations like AMPP (Association for Materials Protection and Performance) and specialized industry consortia provide comprehensive information on the effect of pH, temperature, and specific inhibitors on the corrosion behavior of various stainless steel alloys.
Electrochemical methods, primarily cathodic protection (CP) and, less commonly for stainless steels, anodic protection (AP), can also be employed to control corrosion. Cathodic protection involves lowering the electrochemical potential of the stainless steel structure to a point where the rate of corrosion is significantly reduced or stopped. This is achieved by connecting the pipe to a more active (sacrificial) anode material (e.g., zinc, aluminum, or magnesium anodes) or by using an impressed current cathodic protection (ICCP) system, which uses an external DC power source and inert anodes. While CP is very widely and successfully used for protecting buried or immersed carbon steel pipelines and structures, its application to stainless steels requires more careful consideration. Overprotection (driving the potential too negative) can lead to hydrogen evolution on the stainless steel surface, which can cause hydrogen embrittlement in some grades (especially martensitic or duplex stainless steels under high stress) or cathodic disbondment of any applied organic coatings. However, in specific situations, such as protecting stainless steel reinforcement in concrete in chloride-contaminated marine environments, or protecting stainless steel components in seawater where crevices might be unavoidable and Mo content is borderline, carefully designed and monitored CP systems can be beneficial. Anodic protection, in contrast, involves actively controlling the electrochemical potential of the stainless steel to maintain it firmly within its passive range, typically by using a potentiostat and inert cathodes. AP is a more specialized technique, generally used for protecting stainless steel tanks and vessels handling very aggressive bulk chemicals like concentrated sulfuric acid, where it can provide excellent corrosion control but requires sophisticated monitoring and control systems.
Solution Category | Specific Method | Mechanism of Action | Typical Application / MFY Client Relevance |
---|---|---|---|
Material Selection | Higher Cr, Mo, N grades (316L, Duplex SS 2205/2507, Super Austenitics like 254SMO/904L/AL-6XN) | Enhanced passive film stability, higher PREN, better SCC resistance | Seawater handling (Middle East clients), aggressive chemical processing (India), food/pharma (SE Asia needing high purity) |
Protective Coatings/Linings | Epoxy (FBE), Polyurethane, Fluoropolymer (PTFE, PVDF, ECTFE), Rubber lining, Glass lining | Physical barrier between steel and environment, chemical inertness | Wastewater pipes (epoxy on 304L/316L), aggressive chemical transport (PTFE-lined SS for equipment integrators), abrasion resistance (rubber lining in mining) |
Environmental Control | Chemical Inhibitors (filming, passivating, scavenging), Deaeration, pH adjustment (acid/alkali dosing) | Reduces aggressiveness of environment, stabilizes passive film, removes cathodic reactants | Closed-loop cooling systems for manufacturing plants, boiler feedwater treatment, process streams with pH fluctuations (chemical industry) |
Electrochemical Methods | Cathodic Protection (sacrificial anode or ICCP - careful application for SS), Anodic Protection | Shifts electrochemical potential to non-corroding (CP) or stable passive (AP) region | Specialized cases: SS in chloride-rich soil/water (CP with caution), concentrated H2SO4 storage tanks (AP for major chemical producers) |
Molybdenum enhances pitting resistanceTrue
Molybdenum (Mo) is a key alloying element that significantly improves stainless steel's resistance to localized pitting corrosion, especially in chloride-containing environments.
304L is suitable for seawater applicationsFalse
Type 304L stainless steel lacks sufficient molybdenum content and would suffer rapid pitting corrosion in seawater; 316L or duplex grades are required for marine environments.
What are the best practices for maintaining corrosion resistance in stainless steel pipes?
Even meticulously chosen and installed stainless steel pipes can succumb to corrosion if not properly maintained over their service life. Neglecting essential maintenance practices often leads to unexpected failures, costly emergency repairs, and significant operational disruptions, ultimately undermining your initial investment. Adopting a consistent regimen of best practices for maintenance is crucial for ensuring sustained corrosion resistance and maximizing the lifespan of your valuable piping assets.
Best practices for maintaining corrosion resistance in stainless steel pipes include regular inspection and monitoring, prompt and appropriate cleaning to remove deposits and contaminants, avoiding contact with incompatible materials like carbon steel, ensuring correct fabrication and repair procedures are always followed, and periodic passivation treatments where necessary to restore or enhance the protective chromium oxide layer.
Selecting the right stainless steel pipe for the job and employing initial solutions to enhance its corrosion resistance are undoubtedly crucial first steps, but the journey to long-term reliability doesn't conclude there. Sustained high performance and asset integrity critically hinge on the implementation of a diligent and well-planned maintenance program. At MFY10, we consistently emphasize to all our diverse clients – from large-scale manufacturing companies operating complex facilities, to dynamic engineering contractors executing critical infrastructure projects, and to our valued distributors and traders supplying materials into various demanding applications – that maintenance should not be viewed as a mere operational expense, but rather as a vital investment in asset integrity, safety, and long-term profitability. I've personally witnessed numerous situations where perfectly good, appropriately specified stainless steel piping systems deteriorated prematurely and failed unexpectedly, simply due to a lack of a consistent and informed maintenance regimen. Over time, contaminants can accumulate on surfaces, minor damages or process upsets can go unnoticed and fester into serious corrosion sites, and the all-important protective passive layer can be compromised without deliberate care and attention. For industries operating in our key export markets like India, Southeast Asia, and the Middle East, where environmental conditions (e.g., high humidity, salinity, industrial pollutants, extreme temperatures) can often be particularly challenging, a proactive and robust maintenance strategy becomes even more critical. It's fundamentally about preserving and nurturing the "stain-less" quality of the steel throughout its entire intended service life. By systematically implementing a set of established best practices, businesses can significantly extend the longevity of their stainless steel piping systems, avoid costly surprises and unplanned outages, and ensure continuous, reliable, and safe operation.
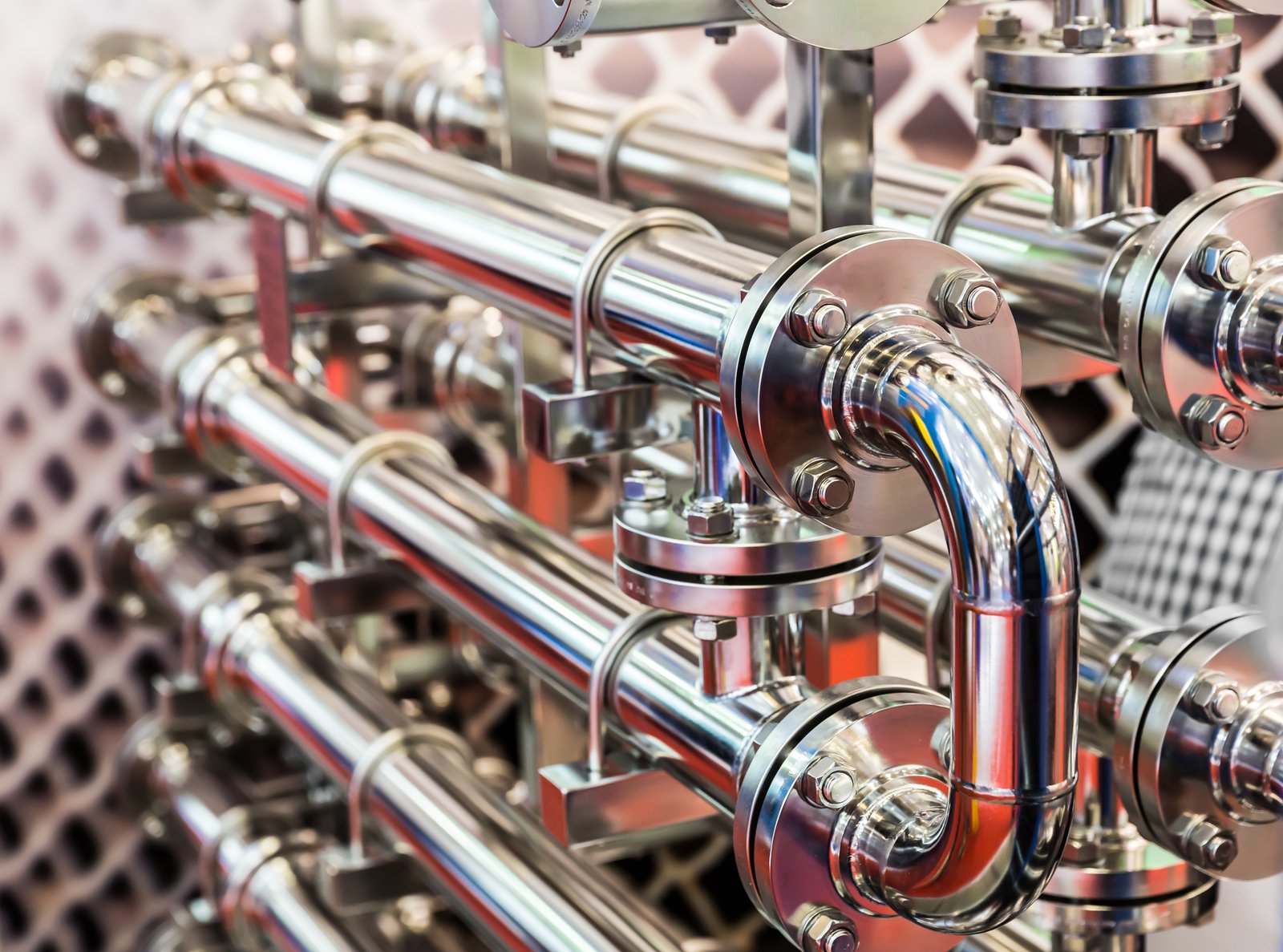
Maintaining the inherent corrosion resistance of stainless steel pipes is an ongoing commitment that pays dividends in reliability and longevity. It's about vigilance and adherence to procedures that protect the passive layer and address potential issues before they escalate. From my vantage point at MFY, I've seen that companies that integrate these best practices into their standard operating procedures experience fewer unexpected failures and lower overall lifecycle costs. Whether it’s a manufacturing company in India striving for consistent production, an engineering contractor in Southeast Asia ensuring the durability of a new facility, or a distributor in the Middle East advising clients on proper care, these principles are universally applicable. The following sections will detail key best practices, covering regular inspection and monitoring, essential cleaning and passivation techniques, and crucial considerations for fabrication, repair, and handling. These practices are not just theoretical guidelines; they are actionable steps that can be implemented to safeguard your stainless steel investments and ensure they perform as intended for years to come.
Regular Inspection and Monitoring
The absolute cornerstone of any effective and proactive maintenance program for stainless steel piping systems is a schedule of regular, systematic inspection and diligent monitoring. This proactive approach allows for the early detection of potential corrosion initiation or other forms of degradation well before they escalate into significant problems that could lead to leaks, failures, or operational disruptions. Inspection methods can range from relatively simple but essential visual examinations by trained personnel to the deployment of more sophisticated non-destructive testing (NDT) techniques for quantitative assessment. Visual inspections should be conducted routinely, focusing on tell-tale signs such as any unusual discoloration of the pipe surface, the appearance of rust staining (which on stainless steel often indicates external contamination from carbon steel or iron-bearing water, or severe underlying corrosion), evidence of pitting (small, localized holes), the presence of scale buildup or tenacious deposits, and any signs of weeping or leakage, particularly at critical locations like welds, flanged joints, areas under pipe clamps or supports (potential crevice sites), and sections of pipe prone to stagnant conditions or fluid traps.
For many of our clients, particularly those in larger manufacturing or process industries like chemical plants or refineries, we at MFY often recommend the development and implementation of a formal Risk-Based Inspection (RBI) plan. This data-driven approach, often guided by standards like API 580/581, helps to prioritize inspection efforts and resources on those sections of the piping system that are deemed most critical to safety and operation, or have the highest calculated likelihood of corrosion based on process fluid corrosivity, material of construction, operating conditions (temperature, pressure), and historical performance data from similar units. When more detailed assessment is required, various NDT methods can be employed. Ultrasonic testing (UT), including conventional thickness gauging and advanced techniques like phased array UT (PAUT), can be used to accurately measure wall thickness and detect internal or external metal loss due to general or localized corrosion. Liquid penetrant testing (PT) is effective for revealing surface-breaking defects such as cracks, pits, or porosity. Radiographic testing (RT) can be used to identify internal flaws, volumetric corrosion, or weld defects. For instance, a major petrochemical plant that MFY supplies with specialized alloy pipes might use long-range guided wave ultrasonic testing (GWUT) for initial screening of long, insulated or buried pipelines to identify areas of potential concern, followed by localized, more detailed UT and other NDT methods for precise characterization and fitness-for-service assessment in those suspect areas. Organizations like the American Petroleum Institute (API), particularly through its standard API 570 ("Piping Inspection Code: In-service Inspection, Rating, Repair, and Alteration of Piping Systems"), provide comprehensive and widely adopted guidelines for inspection frequencies, applicable techniques, and acceptance criteria.
In addition to physical inspection, ongoing monitoring of key process parameters and environmental conditions can provide valuable early warnings of changing corrosivity. This can involve routine analysis of process fluid chemistry to detect unexpected changes in corrosive species (e.g., sudden increases in chloride levels, significant pH deviations, buildup of sulfides) or for the presence of dissolved corrosion products (e.g., elevated iron, chromium, or nickel content in the fluid, which can indicate active corrosion upstream). In some highly critical or aggressively corrosive systems, corrosion coupons (small, pre-weighed specimens of the same material as the pipe, exposed to the process fluid for a defined period) or sophisticated online corrosion monitoring probes (e.g., electrical resistance (ER) probes, linear polarization resistance (LPR) probes, or electrochemical noise (ECN) sensors) can be installed. These devices can provide real-time or periodic quantitative data on actual corrosion rates occurring within the system. This proactive and data-rich approach allows plant operators and maintenance engineers to make timely adjustments to process conditions (e.g., inhibitor dosage, pH control), or to modify maintenance schedules and inspection frequencies before significant material degradation occurs. For example, if continuous monitoring reveals an unexpected spike in chloride concentration in a cooling water system, an operator can immediately investigate and take corrective action to identify and eliminate the source of contamination, thereby preventing potential pitting damage to stainless steel heat exchangers and piping.
Proper Cleaning and Passivation
Keeping stainless steel surfaces scrupulously clean is absolutely vital for maintaining their inherent corrosion resistance over the long term. Any type of deposit or fouling on the surface – whether it's process residues, mineral scale from hard water, biofilms from microbial activity, atmospheric dirt and grime, or even just settled dust in a corrosive industrial atmosphere – can create localized conditions conducive to corrosion. These deposits can act as crevice-formers, trap moisture and aggressive corrodents (like chlorides) against the pipe surface, or create differential aeration cells, all of which can lead to the breakdown of the passive film and initiate localized corrosion mechanisms like pitting or crevice corrosion. Therefore, a program of regular and appropriate cleaning is essential to remove these potentially harmful deposits and allow the passive chromium oxide layer to remain fully effective in protecting the underlying steel. The specific cleaning method, the type of cleaning agents used, and the frequency of cleaning will depend heavily on the nature of the application, the type of fouling encountered, the grade of stainless steel, and any regulatory requirements (e.g., in food or pharmaceutical industries).
For industries like food and beverage processing, pharmaceuticals, or biotechnology, where hygiene and prevention of contamination are paramount, highly regimented cleaning-in-place (CIP) and sterilization-in-place (SIP) systems are commonly used. These automated systems typically involve circulating a sequence of cleaning solutions (e.g., alkaline detergents to remove organic soils, acid cleaners to remove mineral scale, followed by sanitizers like peracetic acid or hot water/steam) through the piping and equipment. It is absolutely crucial that all cleaning agents used are fully compatible with the specific grade of stainless steel being cleaned and with any elastomeric seals or gaskets in the system. Thorough rinsing procedures, usually with high-purity water, must be diligently followed after each chemical cleaning step to ensure complete removal of all chemical residues, as leftover cleaning agents (especially those containing chlorides, like sodium hypochlorite if misused) can themselves become a source of corrosion. MFY often advises its clients in these sensitive industries to carefully select and validate their cleaning chemicals and procedures in consultation with chemical suppliers and industry guidelines. A very common and detrimental mistake, often made by untrained personnel, is the use of ordinary steel wool, carbon steel brushes, or abrasive pads containing iron for cleaning stainless steel surfaces. These tools can embed microscopic iron particles into the stainless steel surface, which will subsequently rust, causing unsightly staining and, more seriously, acting as initiation sites for localized galvanic corrosion. Only tools made from stainless steel (of a compatible or higher grade), nylon, or other non-metallic materials should ever be used for cleaning stainless steel.
Passivation is a specific chemical treatment, typically involving the use of an oxidizing acid solution like nitric acid (as per ASTM A967 or AMS 2700) or, increasingly for environmental and safety reasons, citric acid formulations, to remove any free iron and other surface contaminants left over from fabrication or handling, and more importantly, to chemically enhance and thicken the natural chromium-rich passive layer on the stainless steel surface. While stainless steel inherently passivates (forms its protective oxide layer) spontaneously in the presence of oxygen (from air or aerated water), chemical passivation provides a more uniform, robust, and contaminant-free passive film, optimizing the material's corrosion resistance. Passivation is often specified and performed as a final step after fabrication processes like welding, grinding, machining, or pickling (acid cleaning to remove weld scale/tint). It can also be beneficial as a periodic maintenance step if there's reason to believe the passive layer has been damaged, contaminated, or depleted over time due to harsh service conditions or aggressive cleaning. Standards like ASTM A380 ("Standard Practice for Cleaning, Descaling, and Passivation of Stainless Steel Parts, Equipment, and Systems") provide detailed guidance on best practices for these critical surface conditioning treatments. At MFY, we ensure that our own processed stainless steel products, such as cold-rolled sheets or plates that might be used for subsequent pipe manufacturing, undergo appropriate cleaning and, where specified, passivation treatments to deliver optimal corrosion resistance to our customers from the very start.
Best Practices in Fabrication, Repair, and Handling
The process of maintaining corrosion resistance effectively begins from the moment the stainless steel pipes and components are first fabricated and installed, and these best practices must be diligently continued through any subsequent repair or modification work. During all stages of fabrication, it is absolutely crucial to prevent any contamination of the stainless steel with carbon steel or other dissimilar metals that could cause galvanic corrosion or embed iron particles. This requires strict adherence to good workshop practices, such as maintaining dedicated tools (grinders, brushes, clamps, etc.) exclusively for stainless steel work, establishing segregated fabrication areas physically separated from carbon steel work, and using appropriate handling equipment (e.g., nylon slings, padded supports) to prevent surface damage and contamination. Any embedded iron particles, whether from grinding sparks from nearby carbon steel work, contact with carbon steel tools or workbenches, or handling with rusty chains, can become potent initiation sites for localized galvanic corrosion, appearing as rust spots that can eventually lead to pitting of the stainless steel. Weld quality is another paramount consideration. Proper welding procedures (developed and qualified according to standards like ASME Section IX or ISO 15614), use of qualified welders, selection of appropriate filler metals (usually matching or slightly overalloyed compared to the base metal), and achieving good weld profiles (smooth, free from excessive undercut, overlap, porosity, or sharp crevices) are all essential for ensuring the long-term integrity and corrosion resistance of welded joints. Post-weld cleaning to completely remove all weld tint (the heat-induced oxide scale, which is less protective than the original passive film) and any weld spatter is also critically important, often achieved through mechanical means (stainless steel wire brushing, grit blasting with clean abrasives) followed by chemical pickling and passivation.
When repairs to stainless steel piping become necessary, they must be carried out with the same high level of attention to detail and adherence to best practices as the original fabrication. This includes meticulous planning, using correct and compatible grades of filler material, employing appropriate welding techniques designed to minimize heat input and avoid sensitization (especially for standard carbon austenitic grades that haven't been solution annealed post-weld), and conducting thorough post-repair cleaning, inspection, and passivation. For instance, if a section of Type 304 pipe requires weld repair, using a Type 308L (low carbon) filler metal is common practice. If there's a significant risk of sensitization in the base metal HAZ due to the repair heat cycle, specialized low heat input welding procedures should be employed, or consideration might be given to using a stabilized filler metal or performing a localized post-weld solution anneal if practical (though this is rare for field repairs). We frequently consult with our engineering contractor clients on best practices for on-site welding and repair in diverse and often challenging field environments, such as those encountered in our key export markets across Asia and the Middle East, to ensure that any repair work does not inadvertently compromise the long-term integrity or corrosion resistance of the overall system. Non-destructive testing (NDT) of repair welds is often required to verify their quality.
Proper handling, storage, and transportation practices also play a surprisingly significant, though often underestimated, role in preserving the corrosion resistance of stainless steel pipes right up to the point of installation and commissioning. Stainless steel pipes should ideally be stored in a clean, dry, well-ventilated indoor environment, or if outdoor storage is unavoidable, they should be kept off the ground on non-metallic supports, covered with waterproof tarpaulins (allowing for air circulation to prevent condensation), and sloped to allow for drainage. During transport and on-site handling, extreme care must be taken to prevent mechanical damage such as scratches, dents, gouges, or bending, as these can disrupt the passive film and create stress risers. Using appropriate lifting equipment, such as wide fabric or nylon slings, padded spreader bars, and avoiding dragging pipes across rough or contaminated surfaces, is essential. Even something as simple as ensuring that protective end caps remain securely in place on pipe ends during storage and transport can prevent the ingress of moisture, dirt, and other contaminants that could initiate corrosion from the inside. These seemingly small details, when consistently applied, contribute significantly to ensuring that the stainless steel piping system starts its service life in optimal condition and maintains its design corrosion performance.
Maintenance Practice | Key Actions | Why It's Important | MFY's Client Application Example |
---|---|---|---|
Inspection & Monitoring | Visual checks (discoloration, deposits, leaks), NDT (UT for thickness, PT for cracks), RBI plans, corrosion coupons/probes, process fluid analysis | Early detection of issues, prevent catastrophic failures, optimize maintenance spend | Petrochemical plant in India using RBI and GWUT/PAUT for pipeline integrity; Food processor in SE Asia regularly monitoring CIP fluid chemistry & pipe internals |
Cleaning & Passivation | Regular removal of process/biofilm/scale deposits, use of compatible cleaning agents (avoiding harsh chlorides), chemical passivation (nitric/citric acid) post-fabrication/repair or periodically | Prevents crevice corrosion under deposits, removes contaminants (e.g. free iron), restores/enhances passive layer for optimal resistance | Food/pharma CIP/SIP systems; Post-fabrication passivation for new installations by engineering contractors; Routine cleaning of heat exchanger tubes. |
Fabrication & Repair Best Practices | Dedicated SS tools/areas, avoid carbon steel contamination, proper welding procedures (qualified welders, correct fillers, low heat input), thorough post-weld cleaning/pickling/passivation, correct repair materials & techniques | Prevents galvanic corrosion from Fe contamination, ensures weld integrity & HAZ resistance, avoids sensitization, maintains original design performance | Engineering contractor ensuring clean fabrication protocols on-site for a project in the Middle East; Manufacturing company using certified procedures for weld repairs to process equipment. |
Passivation enhances corrosion resistanceTrue
Passivation treatments chemically enhance the chromium oxide layer on stainless steel, improving its protective qualities against corrosion.
Carbon steel tools are safe for cleaning stainlessFalse
Carbon steel tools can embed iron particles into stainless steel surfaces, leading to rust stains and potential galvanic corrosion initiation sites.
Conclusion
Corrosion resistance in stainless steel pipes is maximized by informed material selection, understanding environmental aggressors, robust design, and diligent maintenance. Proactive strategies ensure longevity, operational efficiency, and safety, safeguarding your valuable assets and ensuring reliable performance across diverse industrial applications.
-
Discover the global economic impact of corrosion and its significance in maintenance planning ↩
-
Learn why Type 316L offers better corrosion resistance and where it's advantageous ↩
-
Understand benefits of 2205 duplex stainless steel in stress corrosion environments ↩
-
Explore how stabilization elements prevent sensitization and enhance [^5]: Learn about corrosion effects of salt exposure on Type 304 stainless steel pipes near coastal areas ↩
-
Discover how chlorides compromise austenitic stainless steel's corrosion resistance in various settings ↩
-
Learn about unique corrosion types that affect pipe integrity ↩
-
Understand the standards for piping systems and their requirements ↩
-
Understand how this equation affects fluid flow in pipes ↩
-
Understand the advantages of combining methods for optimal corrosion protection. ↩
-
Discover MFY's approach to stainless steel corrosion resistance maintenance ↩
Have Questions or Need More Information?
Get in touch with us for personalized assistance and expert advice.