Low-Carbon Stainless Steel: How Green Melting Affects Pipe Quality
The global push for sustainability is creating immense pressure on industrial supply chains. You're likely facing demands for greener materials, but this brings a critical worry: does "low-carbon" mean sacrificing the performance and reliability you depend on? By understanding the reality of modern green steel production, you can confidently meet sustainability goals without compromising quality.
Green melting primarily affects pipe quality by ensuring metallurgical equivalence through advanced processes like the Electric Arc Furnace (EAF). This method, centered on recycled content and clean energy, produces low-carbon stainless steel that meets or exceeds all traditional quality benchmarks for purity, strength, and corrosion resistance.
This shift towards sustainable manufacturing is not about accepting a lesser product; it's about embracing a smarter, more efficient process. The technology behind "green melting" has matured, allowing us to produce steel that is both environmentally responsible and fully compliant with the stringent ASTM and ASME standards1 your projects demand. For my clients, from E&C contractors in the Middle East to equipment integrators in India, this is a game-changer.
As we navigate this transition at MFY, our focus is on demystifying the process and providing concrete proof of performance. It’s a journey from perception to reality. The perception is that "recycled" is a synonym for "impure" or "weak." The reality, backed by rigorous testing and comprehensive Mill Test Certificates (MTCs), is that low-carbon stainless steel is indistinguishable from its traditionally-made counterpart in every performance metric that matters. This article will explore the science and data, showing how green melting is not a compromise but a competitive advantage.
What defines low-carbon stainless steel in the context of environmental sustainability?
Does the term "low-carbon steel" leave you confused? Many people mistake it for the metallurgical carbon content (like in 304L), causing them to miss the bigger picture of environmental impact. The solution is to redefine the term based on its total lifecycle emissions, not just its chemical composition.
In the context of environmental sustainability, low-carbon stainless steel is defined not by the carbon content in the alloy itself, but by the significantly lower carbon dioxide (CO₂) emissions generated during its entire production lifecycle, from raw material sourcing to the final product.
This distinction is the key to making informed, sustainable procurement decisions. For instance, two pipes—one made via the traditional Blast Furnace (BF-BOF) route and one via a modern Electric Arc Furnace (EAF)—can have the exact same grade (e.g., TP316L) and identical metallurgical properties, but their carbon footprints can be worlds apart. As a company with a mission to innovate within the stainless steel supply chain, we at MFY are committed to helping our clients understand this crucial difference. It empowers them to meet both their technical specifications and their corporate sustainability targets, a dual objective that is becoming the new standard for competitive advantage in global markets.
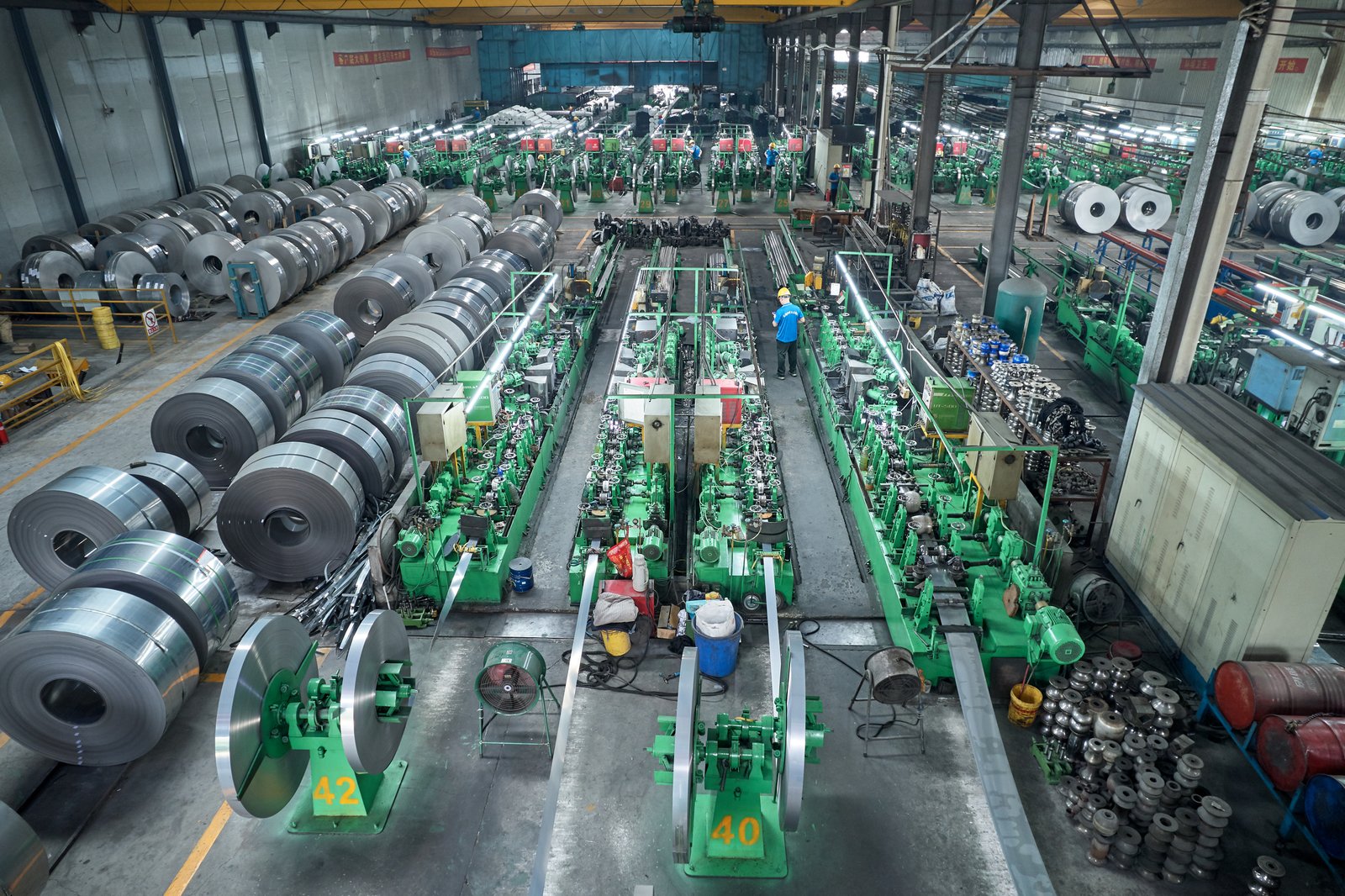
I remember a conversation with a distributor in Southeast Asia who was fielding more and more requests for "green" materials from his manufacturing clients. He was concerned that providing a "low-carbon" product would require him to stock an entirely new set of SKUs and that performance might be an issue. We walked him through the concept of lifecycle emissions. We showed him how our stainless steel pipes, produced using the EAF method, carried the same ASTM A312 certification as any other pipe on the market. Their chemical and mechanical properties were identical. The only difference was the process, which generated drastically fewer emissions. By focusing on the production path's carbon footprint, he could confidently offer our standard, high-quality pipes as a low-carbon solution. This shifted his perspective from seeing sustainability as a product problem to seeing it as a process solution, simplifying his inventory and strengthening his sales proposition.
Defining "Low-Carbon" by Production Path
The most significant factor in a steel product's carbon footprint is its initial production method. The traditional route involves a Blast Furnace and Basic Oxygen Furnace (BF-BOF), which relies on raw materials like iron ore and coking coal. This process is energy-intensive and inherently releases large amounts of CO₂, with industry averages often cited at over 2 tons of CO₂ for every ton of steel produced. This is the high-carbon baseline against which greener alternatives are measured.
The primary low-carbon alternative is the Electric Arc Furnace (EAF). This method uses high-power electric arcs to melt steel, with the primary feedstock being recycled steel scrap rather than raw iron ore. Because it bypasses the chemical reduction of iron ore with coke, its direct emissions are dramatically lower. Data consistently shows that the EAF process emits a fraction of the CO₂ compared to the BF-BOF route, often less than 0.5 tons of CO₂ per ton of steel. Therefore, when we speak of "low-carbon" stainless steel, we are primarily referring to steel produced via the EAF pathway.
This distinction is vital for procurement and engineering teams. A project specification might simply call for "SS316L Pipe," but a sustainability-focused addendum might require that it be sourced from a low-emission production process. This is where suppliers like MFY, with our roots in an integrated and modern supply chain, can provide the necessary documentation and traceability to prove that our materials meet these advanced environmental criteria without altering the fundamental performance characteristics of the steel itself.
The Role of Recycled Content
The use of scrap is central to the low-carbon definition. Stainless steel is 100% recyclable without any degradation of its properties. Every ton of recycled stainless steel scrap used in an EAF avoids the need for mining approximately 1.5 tons of iron ore and 0.5 tons of coal. This circularity is the engine of the low-carbon steel economy. The global stainless steel industry already has a high recycled content, but the EAF process maximizes this benefit.
It's a common misconception that "recycled" implies lower quality. In reality, the opposite is true for stainless steel. The collected scrap—a mix of end-of-life products and manufacturing offcuts—is carefully sorted, analyzed, and blended. The EAF process then refines this material, removing impurities and allowing for precise alloying adjustments to meet the exact chemical specifications of the target grade. The result is a new batch of steel that is metallurgically identical to one made from virgin materials.
For our clients, this means they can benefit from the environmental advantages of a circular economy without taking on any technical risk. When we provide a Mill Test Certificate for a pipe made from low-carbon, EAF-produced steel, it certifies the same chromium and nickel content, the same low carbon levels (e.g., <0.03% for an 'L' grade), and the same mechanical properties as any other pipe. The high recycled content is a process benefit, not a product compromise.
Lifecycle Assessment (LCA) as the Gold Standard
To truly quantify the "greenness" of a material, the industry is increasingly turning to a formal methodology known as Lifecycle Assessment (LCA). An LCA provides a comprehensive, cradle-to-gate or cradle-to-grave analysis of a product's total environmental impact. It accounts for all inputs (energy, water, raw materials) and outputs (emissions, waste) at every stage, from raw material extraction and manufacturing to transportation, use, and end-of-life recycling.
When an LCA is performed on stainless steel, the difference between production paths becomes starkly clear. The BF-BOF route shows a high impact in the initial stages due to mining and smelting emissions. The EAF route shows a significantly lower impact in these early stages, with its main energy input being electricity. If that electricity is sourced from renewables (solar, wind, hydro), the overall carbon footprint can approach near-zero levels for Scope 2 emissions.
As global clients, especially large E&C contractors and multinational manufacturers, adopt more sophisticated sustainability reporting, the demand for products with favorable LCA data will grow. This is where forward-thinking suppliers must be prepared. At MFY, we are aligning our processes and data collection with LCA principles, ensuring we can provide our clients with the transparent, verifiable environmental performance data they need to build the resilient and responsible supply chains of the future.
EAF produces low-carbon steelTrue
Electric Arc Furnace (EAF) uses recycled scrap and clean energy to produce steel with significantly lower CO₂ emissions compared to traditional methods.
Recycled steel is lower qualityFalse
Recycled stainless steel undergoes rigorous refining in EAFs, resulting in material that meets identical metallurgical specifications as virgin steel.
How does the green melting process work for stainless steel production?
The concept of "green melting" might sound like complex, unproven science, creating uncertainty about its reliability. This can make you hesitant to adopt materials from such a process. The solution lies in understanding that green melting is simply the proven Electric Arc Furnace (EAF) technology powered by clean energy.
The green melting process for stainless steel primarily uses an Electric Arc Furnace (EAF) to melt high-purity recycled steel scrap. Its "green" credentials come from this high use of scrap, which avoids mining, and by powering the furnace with renewable energy sources, drastically reducing the carbon footprint.
This process is not experimental; it's a mature, globally adopted technology that now accounts for a significant portion of the world's stainless steel production. I’ve seen the evolution firsthand through our supply network at MFY. Our partner mills have invested heavily in state-of-the-art EAFs and, increasingly, in dedicated renewable energy infrastructure. This isn't just for environmental reasons; it’s about efficiency, quality control, and long-term cost stability. By embracing this technology, we can offer our clients a product that is consistent, high-quality, and aligned with modern environmental standards.
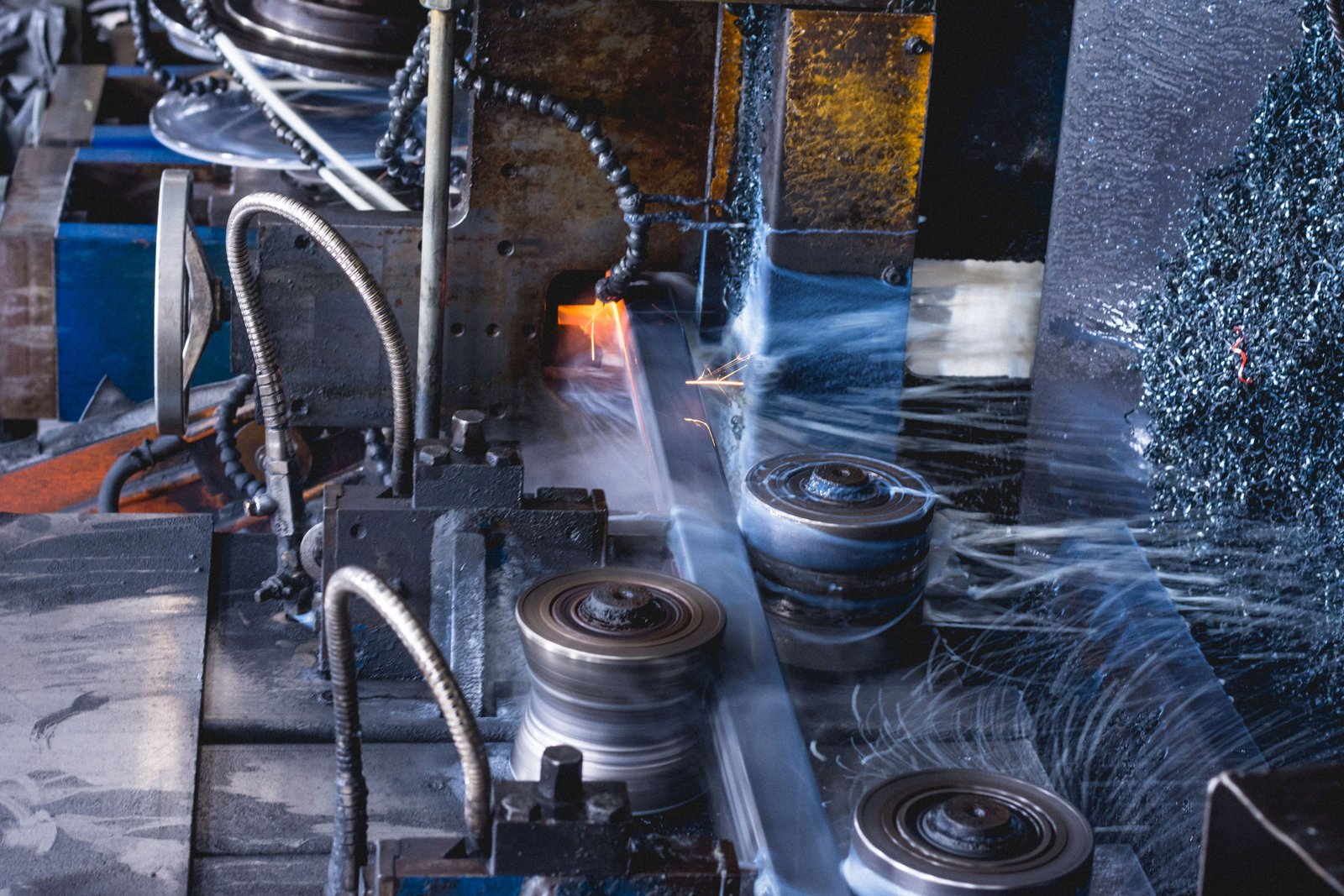
Consider a recent project with a major equipment integrator in the Middle East. They were building water treatment skids for a large municipal project that had stringent "green procurement" mandates. They needed stainless steel pipes that not only met the technical specs for corrosion resistance but also had a verifiably low carbon footprint. We were able to meet their needs precisely because our supply chain is rooted in the EAF process. We provided documentation tracing the material back to a specific production facility that powers its EAF operations partially with its own large-scale solar farm. This tangible link between the melting process and a renewable energy source gave the client the proof they needed. It was a clear demonstration that "green melting" isn't an abstract marketing term; it's a practical, verifiable production method that delivers both quality and sustainability, helping our client win the bid and deliver a future-forward project.
The Electric Arc Furnace (EAF) at its Core
The Electric Arc Furnace is the heart of low-carbon steelmaking. Unlike a blast furnace, which uses a continuous, high-volume chemical process, an EAF operates in batches. The process begins by loading a carefully selected charge of recycled stainless steel scrap into the furnace. Large graphite electrodes are then lowered into the furnace, and an immense electrical current is passed through them, creating a powerful arc. This arc generates intense heat, with temperatures reaching over 3,000°C (5,400°F), rapidly melting the scrap metal into a molten bath.
Once the scrap is melted, the refining process begins. Oxygen is injected to remove excess carbon, and other elements like silicon and manganese are oxidized and removed as slag. At this stage, precise amounts of ferroalloys, such as ferrochrome and ferronickel, are added to the molten bath to bring the steel's chemistry to the exact specification of the desired grade, for example, 316L or Duplex 22052. This high degree of control is a key advantage of the EAF process.
Because the heat source is electricity, the EAF offers operational flexibility that a blast furnace cannot. It can be started and stopped relatively easily, allowing for more agile production that can respond to market demand. For a company like MFY, which prides itself on agility and rapid export delivery, having EAF-based suppliers is a strategic advantage. It allows us to secure material for our pipe and tube manufacturing more efficiently, ensuring a stable and responsive supply chain for our global clients.
The Critical Role of Scrap Steel Quality
The success of the EAF process is fundamentally dependent on the quality of the incoming raw material: the steel scrap. This is not simply a matter of dumping any available scrap metal into the furnace. A sophisticated system of sourcing, sorting, and analysis is required to ensure the final product meets stringent quality standards. The scrap is categorized based on its origin and alloy content. For example, scrap from known sources like industrial off-cuts from a 316L manufacturing process is highly valued for its purity.
Advanced analytical techniques, such as X-ray fluorescence (XRF) spectroscopy3, are used to analyze the chemical composition of the scrap before it is even charged into the furnace. This allows the furnace operators to create a precise "recipe" for each batch, blending different types of scrap to achieve a target chemistry. This meticulous management of the scrap stream is essential for controlling the level of tramp elements—undesirable residual elements like copper, tin, or lead—which could negatively impact the final steel's mechanical properties or weldability.
This is where an integrated supply chain demonstrates its value. At MFY, we work closely with our raw material suppliers who have invested in cutting-edge scrap processing technology. This ensures that the feedstock for our steel is of the highest possible purity. This upstream quality control is the first and most important step in guaranteeing that the final pipe we deliver to a construction contractor or a distributor will perform flawlessly in its intended application.
Powering the Process: The Renewable Energy Factor
The final, and arguably most important, component of "green" melting is the source of the electricity that powers the EAF. While using an EAF already slashes emissions by utilizing scrap, the carbon footprint of the electricity consumed (known as Scope 2 emissions) is a major part of the remaining environmental impact. A standard EAF powered by a coal-fired electrical grid will still have a notable carbon footprint. The truly "green" process is achieved when the EAF is powered by renewable energy.
Leading steelmakers are making massive investments in this area. This includes building dedicated solar and wind farms adjacent to their mills or signing long-term Power Purchase Agreements (PPAs) with renewable energy providers. By running their furnaces on clean electricity, they can reduce their Scope 2 emissions to nearly zero. This creates a virtuous cycle: the process uses recycled material (reducing Scope 3 emissions from raw material extraction) and is powered by clean energy (reducing Scope 2 emissions), resulting in one of the lowest possible carbon footprints for new steel.
This transition is a key part of our vision at MFY to drive the global expansion of a sustainable stainless steel supply chain. We actively seek out and partner with producers who are leaders in this renewable transition. It allows us to offer our clients in markets like the Middle East and Southeast Asia—regions with growing interest in sustainable infrastructure—a product that is not just high-quality but also a testament to the future of environmentally responsible manufacturing.
EAF uses recycled scrapTrue
The Electric Arc Furnace process primarily melts high-purity recycled steel scrap, reducing the need for mining new materials.
EAF requires coal powerFalse
While EAFs can use grid electricity, the green melting process specifically uses renewable energy sources like solar or wind power.
What are the quality implications of using low-carbon stainless steel in pipe manufacturing?
You've been asked to source low-carbon steel, but your biggest fear is that it will fail to meet your project's stringent quality standards. This concern over performance can cause project delays and stakeholder friction. The solution is to rely on the data and certifications which prove its equivalence.
When produced to standard specifications like ASTM standards for low-carbon stainless steel, the quality implications of using low-carbon stainless steel are non-existent. The final product is metallurgically identical to its high-emission counterpart, exhibiting the same corrosion resistance, tensile strength, weldability, and surface finish.
This is a critical point that I emphasize in every discussion with clients, from engineering contractors to traders. The "low-carbon" designation refers to the process, not a deficiency in the product. The EAF process is designed to refine and purify recycled materials to create a clean, homogenous melt that is then cast and rolled just like any other steel. The result is a pipe that doesn't just look the same; it performs the same, and we have the MTCs to prove it.
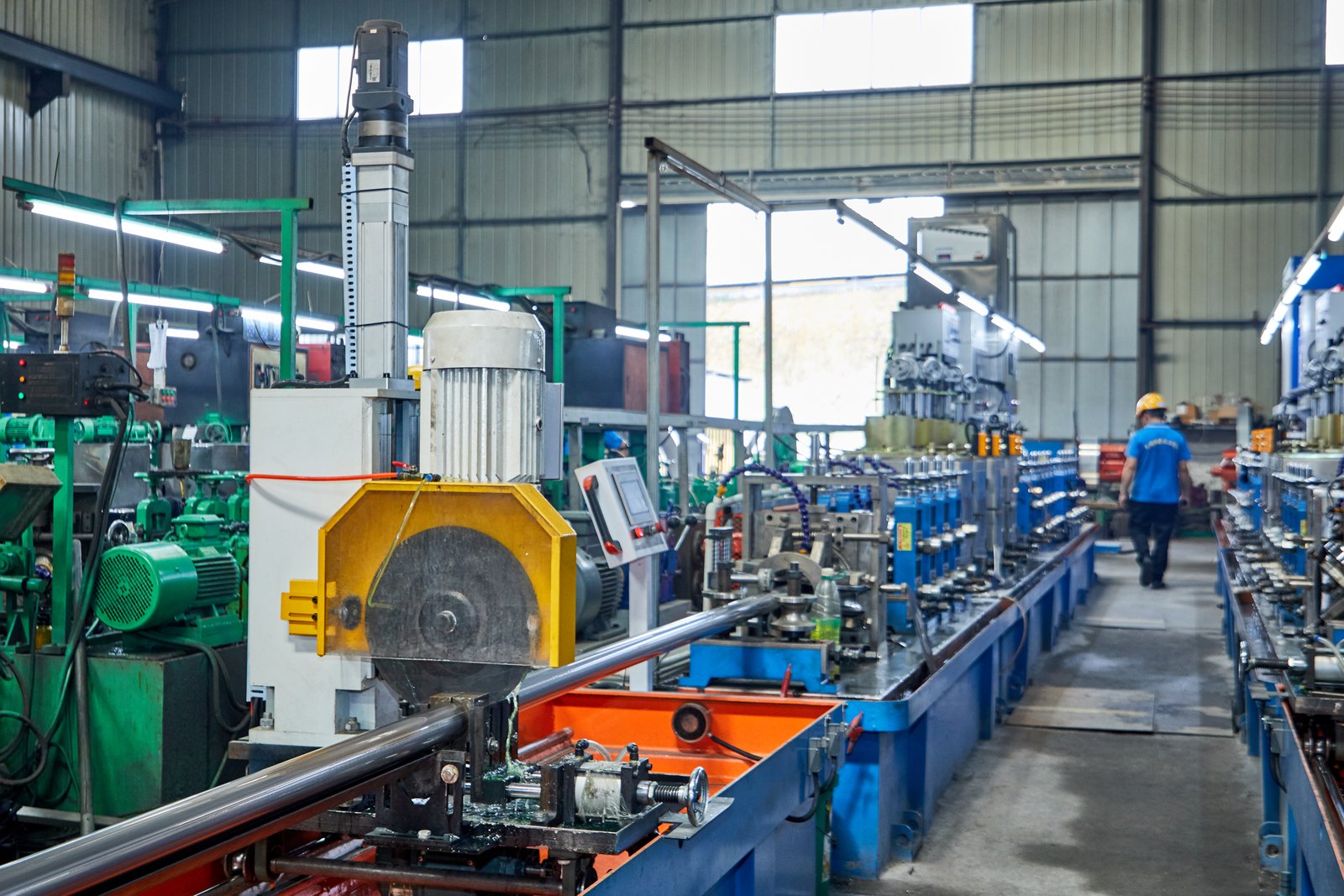
I can point to a specific case with a large manufacturing client in Russia who was building a new chemical processing line. Their engineering team was rightly conservative and had deep experience with traditionally produced stainless steel. They were skeptical about our proposal to use our EAF-sourced low-carbon pipes, fearing issues with weld integrity and corrosion resistance under their aggressive chemical environment. Instead of just debating the point, we provided them with sample pipes and a comprehensive data package. This included not only the standard MTCs but also supplementary corrosion test results (per ASTM G48) and detailed microstructural analysis. They conducted their own in-house welding trials and validation tests. The results confirmed what we already knew: the pipes performed identically to the material they had used for decades. This evidence-based approach completely removed their hesitation, and they have since become a strong advocate for using sustainable materials, proving that seeing is believing.
Metallurgical Equivalence and Compliance
The primary concern for any engineer or end-user is whether the material meets the established industry standards. Low-carbon stainless steel produced via the EAF route is designed from the ground up to meet the exact same specifications, such as those from ASTM International4 or EN standards. The final chemical composition, including the critical percentages of chromium, nickel, molybdenum, and, importantly, carbon, is precisely controlled to fall within the specified ranges for the grade. For example, a 316L pipe must have <0.03% carbon, regardless of whether it started as iron ore or recycled scrap.
The mechanical properties are also identical. The manufacturing process, including casting, rolling, and annealing, is what determines the final grain structure and mechanical strength of the steel. These processes are the same for EAF-produced steel as they are for BF-BOF steel. Therefore, the resulting pipe will have the same specified minimum yield strength, tensile strength, and elongation properties.
This equivalence is not a matter of opinion; it is a verifiable fact confirmed by the Mill Test Certificate (MTC) that accompanies every batch of pipe. This document is the legal and technical guarantee that the product you are receiving complies with every requirement of the ordered standard. For a distributor or contractor, this means there is no change required in their design specifications, welding procedures, or quality assurance protocols when switching to a low-carbon option.
Scrutinizing Purity and Trace Elements
A valid technical question that arises with any recycled material is the control of unwanted "tramp" or trace elements. These are residual elements, like copper, tin, or arsenic, that are not part of the standard alloy specification and which, in sufficient quantities, could potentially affect properties like corrosion resistance or hot workability. This is where the sophistication of the modern EAF process becomes evident.
Steelmakers using the EAF process have a multi-stage approach to purity. First, as discussed, is rigorous scrap management. High-quality, known-source scrap is segregated and used for demanding applications. Second, the EAF refining process itself is highly effective at removing many impurities. Through controlled oxidation and the use of specialized slag chemistry, unwanted elements are drawn out of the molten steel.
ly, advanced secondary refining processes like Argon Oxygen Decarburization (AOD) or Vacuum Oxygen Decarburization (VOD) are almost universally used after the EAF for stainless steel production. These steps further refine the molten steel, allowing for extremely precise chemistry control and the removal of dissolved gases and impurities to very low levels. The result is a "clean" steel that is often of higher purity than what might be produced via a less refined process. The table below illustrates the final certified properties are what matter, and they are identical.
Property | ASTM A312 TP316L Specification | Typical Result (Low-Carbon EAF) | Typical Result (Traditional BF-BOF) |
---|---|---|---|
Carbon (C) | 0.035% max | 0.025% | 0.026% |
Chromium (Cr) | 16.0 - 18.0% | 16.8% | 16.9% |
Nickel (Ni) | 10.0 - 14.0% | 10.2% | 10.3% |
Tensile Strength | 70 ksi (485 MPa) min | 81 ksi (560 MPa) | 82 ksi (565 MPa) |
Yield Strength | 25 ksi (170 MPa) min | 38 ksi (260 MPa) | 39 ksi (270 MPa) |
Performance in Application: Corrosion and Mechanical Properties
The ultimate test of quality is performance in the field. Here, decades of use and countless laboratory tests have confirmed that EAF-produced stainless steel performs identically to conventionally produced steel. The corrosion resistance of a stainless steel alloy is determined by its chemical composition—primarily its chromium, molybdenum, and nickel content—and its passive surface layer. Since the chemistry is controlled to the same specification, the corrosion performance is the same. Whether it's resisting pitting and crevice corrosion in a chloride-rich environment or general corrosion in an acidic one, the performance is a function of the grade, not the production route.
Similarly, the material's mechanical behavior, including its strength, ductility, toughness, and fatigue life, is a result of its chemical composition and its thermomechanical processing (hot rolling, cold rolling, annealing). These processes are standard across the industry and are applied to achieve the properties required by the governing ASTM or EN standard.
This is why, as a supplier, we can confidently stand behind the quality of our low-carbon stainless steel pipes. We know that when an engineering contractor specifies our pipe for a high-pressure, corrosive service in a chemical plant, or when an equipment integrator uses our tubes in a hygienic food processing system, the material will perform exactly as expected. The move to low-carbon steel is a change in environmental responsibility, not a change in material reliability.
Low-carbon steel meets ASTM standardsTrue
Low-carbon stainless steel is produced to meet the same ASTM specifications as traditional steel, ensuring identical performance.
EAF steel has lower corrosion resistanceFalse
Corrosion resistance depends on chemical composition, not production method. EAF-produced steel has the same corrosion resistance as traditional steel when meeting the same grade specifications.
How can manufacturers optimize the production process for better pipe quality using low-carbon stainless steel?
Even with high-quality raw material, you face the challenge of consistently producing top-tier pipes. Inconsistent processes can lead to defects and waste, undermining the benefits of using premium low-carbon steel. The solution lies in optimizing the manufacturing process through technology and supply chain integration.
Manufacturers can optimize pipe quality by integrating advanced scrap sorting and management, implementing real-time process control with digital twinning in the EAF, and fostering deep collaboration with both upstream raw material suppliers and downstream clients to ensure end-to-end quality assurance.
This holistic approach moves beyond simply melting and forming steel; it creates a digitally connected and responsive manufacturing ecosystem. At MFY, our identity as a company integrating production, sales, and digital innovation is built on this very principle. We don’t just see ourselves as pipe makers; we are supply chain architects. By leveraging data and technology from the scrap yard to the final delivery, we can enhance consistency, improve efficiency, and guarantee that the superior quality of the low-carbon steel is preserved and expressed in the final product.
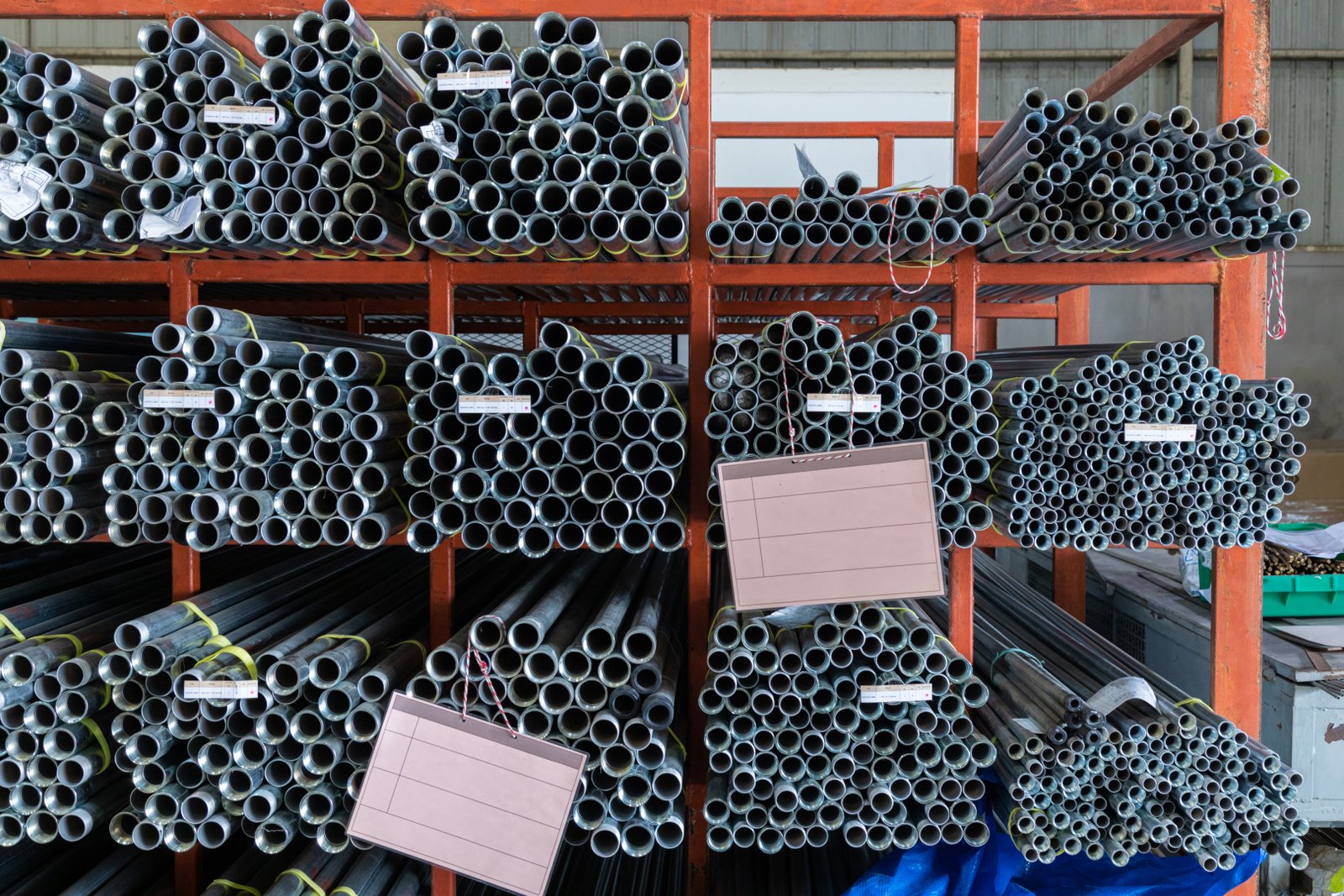
I often point to our work with a large-scale construction contractor who was building a series of facilities with very high-quality specifications. Their primary concern was consistency across multiple batches of pipe delivered over a period of months. They needed to ensure that the weldability and formability of the pipes remained identical from the first shipment to the last to avoid costly adjustments to their automated fabrication equipment. We were able to guarantee this consistency by providing them with a more detailed level of process data than they were used to. We shared data from the steel mill demonstrating the tight control over the chemistry in the EAF and our own pipe mill's process parameters for forming and annealing. This transparency, enabled by our digitally integrated system, gave them unprecedented confidence in the material's stability. It transformed the conversation from a simple transactional one to a collaborative partnership focused on optimizing their production outcomes.
Advanced Scrap Sorting and Management Systems
The optimization of pipe quality begins long before the steel is melted. It starts with the meticulous management of the primary input: recycled scrap. Leading producers are moving beyond basic scrap segregation and are implementing highly automated systems. These can include advanced sensors, robotics, and AI-powered image analysis to sort scrap with incredible speed and accuracy. This ensures that the chemical composition of the material entering the EAF is known and controlled to a very high degree.
By creating a "high-purity" scrap stream, free from contaminants like copper, lead, or excessive non-metallic inclusions, the steelmaker can run the EAF more efficiently. It reduces the amount of refining time needed, lowers energy consumption, and minimizes the risk of tramp elements ending up in the final product. A cleaner input directly translates to a cleaner, higher-quality output.
For a pipe manufacturer like MFY, sourcing our billets from steelmakers who employ these advanced scrap management systems is a critical first step. It provides us with a superior raw material that is inherently more consistent. This consistency in the feedstock makes it significantly easier for our own tube mills to produce pipes with uniform mechanical properties and excellent surface finish, batch after batch. It is a foundational element of quality control.
Process Control and Digital Twinning in the EAF
The next frontier of optimization lies inside the steel mill itself, through the use of advanced process control and digital innovation. Modern EAFs are equipped with a vast array of sensors that monitor everything in real-time: temperature, chemical composition, electrode consumption, energy input, and slag chemistry. This data is fed into sophisticated process control models. These models can predict how the melt will behave and suggest precise adjustments to maintain optimal conditions.
Taking this a step further, some producers are developing a "digital twin" of their furnace. This is a highly complex virtual model that mirrors the physical EAF in real-time. Operators can use the digital twin to run simulations, testing the effect of changing a parameter (like adding a specific alloy) in the virtual environment before doing it in the real world. This allows for unparalleled precision, minimizing errors, reducing waste, and ensuring the final chemistry hits the exact center of the specification window every single time.
This level of digital control is a key part of what makes modern green steel so reliable. It replaces reactive adjustments with predictive, data-driven control. As a company that has "digital innovation" in its DNA, we at MFY see this as a crucial evolution. It allows our suppliers to provide us with steel that is not just compliant, but consistently exceptional, which is a quality we pass directly on to our clients in the form of highly reliable pipes and tubes.
Collaboration Across the Supply Chain
ly, true optimization cannot happen in a silo. It requires deep, transparent collaboration across the entire supply chain. This starts with the steelmaker working closely with scrap suppliers to improve sorting and quality. It then extends to the relationship between the steelmaker and the pipe manufacturer. By sharing data and maintaining open lines of communication, we can better align our processes. For example, if we know the precise and consistent chemistry of the steel billets we are receiving, we can fine-tune our own welding and annealing parameters to achieve optimal results.
This collaboration must also extend downstream to the end-user. By understanding the specific application challenges of our clients—whether it's an E&C contractor facing a unique welding requirement or a manufacturing company needing a specific surface finish for hygienic reasons—we can provide valuable feedback to our partner mills. This creates a continuous improvement loop, where feedback from the final application informs the initial melting process.
This is the essence of MFY's business model. We are not just a link in the chain; we are the hub that connects the various spokes. Our role as an integrator—combining production, trade, and digital services—allows us to facilitate this kind of end-to-end collaboration. It's how we ensure that the promise of high-quality, low-carbon stainless steel is fully realized in the final products that our clients depend on.
Scrap sorting improves EAF efficiencyTrue
Advanced scrap sorting reduces contaminants, leading to cleaner steel output and more efficient melting processes.
Digital twins replace physical EAF testingFalse
Digital twins simulate EAF parameters but don't eliminate the need for physical furnace operations and testing.
What recommendations can be made to promote the use of low-carbon stainless steel in the industry?
Despite its proven quality, the adoption of low-carbon stainless steel faces inertia from old habits and a lack of market incentives. This slows down the industry's progress towards crucial sustainability goals. A multi-faceted strategy is needed to overcome this resistance and accelerate the transition.
To promote the use of low-carbon stainless steel, the industry needs a combination of clear standardization and green certifications, policy incentives that create market pull, and proactive education and partnership between suppliers and clients to build trust and demonstrate value beyond emissions.
This is not a challenge that can be solved by one company alone; it requires a concerted effort. As a key player in the global stainless steel trade, we at MFY see it as our responsibility to be a catalyst for this change. We are actively working not just to produce and sell these materials, but to champion the standards, provide the education, and build the partnerships that will make low-carbon steel the new global benchmark for quality and responsibility.
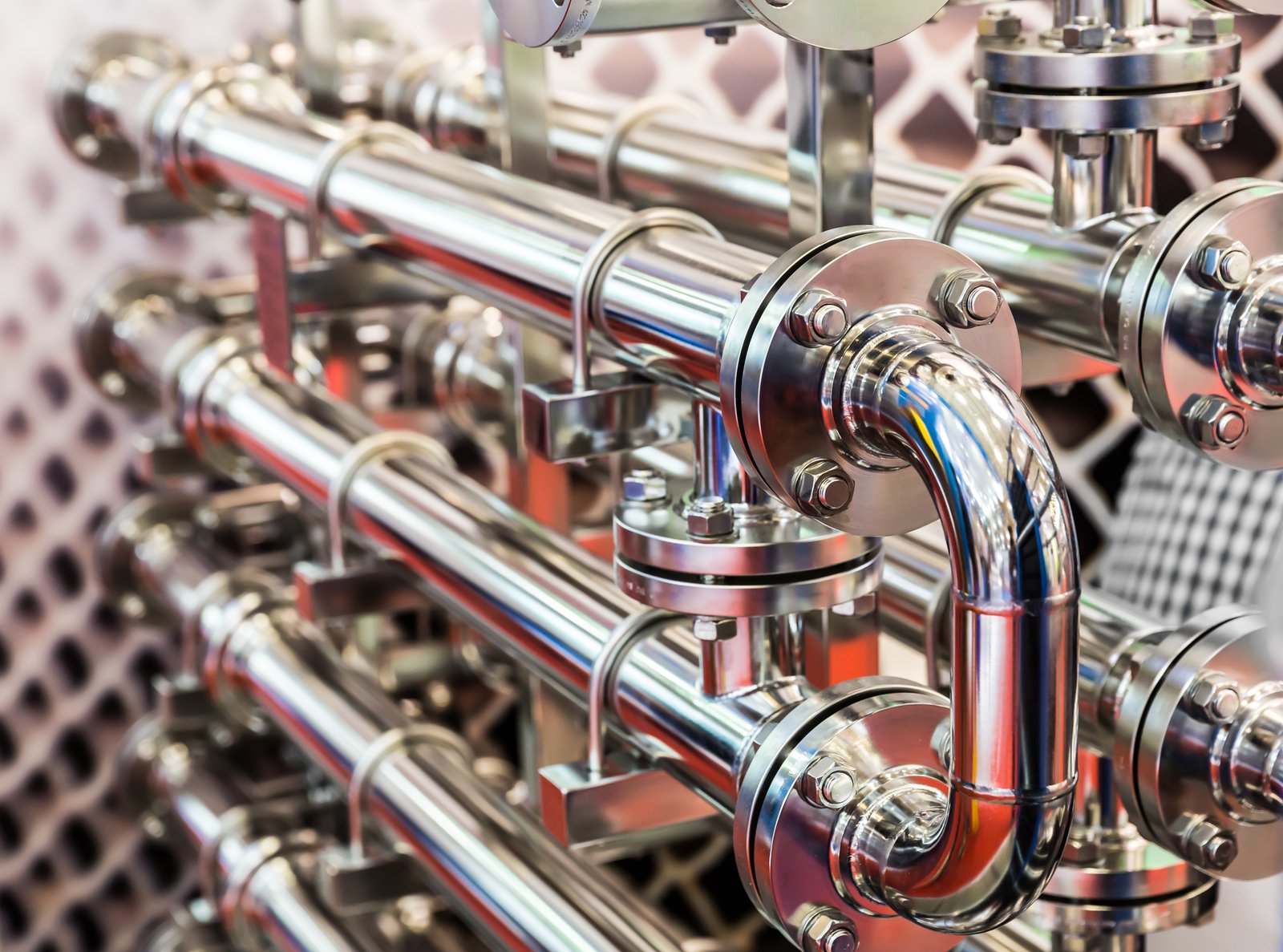
Driving change requires leadership and education. Last year, we organized a webinar for our key distributors and some of their largest clients across India and Southeast Asia. The topic was "The Business Case for Sustainable Steel." We didn't just talk about CO₂. We presented case studies, like the one with our Russian client, proving the material's quality. We showed how specifying low-carbon steel could help them win bids on government-funded infrastructure projects with green mandates. We also demonstrated how our agile supply chain could deliver these materials without project delays. The feedback was overwhelmingly positive. One distributor noted that the session gave his sales team the confidence and the technical arguments they needed to proactively talk about sustainability with their customers. This is the kind of proactive engagement that moves the market forward—transforming a compliance obligation into a commercial opportunity.
Standardization and Green Certification
One of the largest barriers to adoption is ambiguity. Terms like "green," "sustainable," or "low-carbon" can be vague and lead to greenwashing. The industry urgently needs clear, internationally recognized standards and certification programs. This would create a level playing field and give procurers a reliable way to compare different materials. These standards should be based on a full Lifecycle Assessment (LCA) methodology, providing a transparent score or rating for a product's carbon footprint (covering Scope 1, 2, and 3 emissions).
Organizations like ISO5 are developing standards in this area, but adoption needs to be accelerated. Governments and major industry bodies should endorse and promote a single, robust certification system. Once such a system is in place, a supplier like MFY could deliver a pipe with a standard MTC and an accompanying "Green Certificate," which would transparently state its embedded carbon value.
This would be a powerful tool for our clients. An E&C contractor could easily prove to their project owner that they have met the sustainability requirements. A manufacturer could use the certification to enhance the environmental credentials of their own final product. Clear certification removes uncertainty and turns sustainability into a tangible, marketable asset.
Incentivizing Demand: The Role of End-Users and Policy
While supply-side innovation is crucial, demand is the most powerful driver of change. This demand can be stimulated through both public policy and private sector leadership. Governments can play a huge role by implementing green public procurement policies, mandating that taxpayer-funded infrastructure projects use materials with a certified low-carbon footprint. This single measure would create a massive and stable market for sustainable steel. Carbon tariffs or border adjustments can also level the playing field, ensuring that low-carbon domestic producers are not at a disadvantage against high-carbon imports.
Simultaneously, large private end-users—in sectors like automotive, construction, and consumer goods—can set their own ambitious procurement targets. When a major global brand commits to using only low-carbon steel in its products by a certain year, it sends a powerful signal down the entire supply chain.
As a supplier, our role is to make it easy for clients to respond to these incentives. By maintaining a robust supply of high-quality, certified low-carbon pipes and providing the necessary documentation, we empower our clients to bid for these green projects and meet the demands of their most forward-thinking customers. We become not just a supplier, but an enabler of their growth in a new, sustainable economy.
Supplier-Client Education and Partnership
Ultimately, overcoming inertia requires building trust, which is achieved through education and partnership. Many clients are simply unaware of the quality and reliability of EAF-produced steel or do not understand how to navigate the new landscape of green specifications. Proactive suppliers must take on the role of educators and advisors. This goes far beyond a sales pitch.
It involves sharing technical data, hosting workshops, and providing clear, honest information about both the benefits and the production processes of low-carbon materials. It means working collaboratively with a client’s engineering team to ensure they are comfortable with the material's performance characteristics and have all the documentation they need for their internal quality assurance and external reporting. At MFY, this aligns perfectly with our core values of agility and continuous evolution.
By investing in these partnerships, we build deep, long-lasting relationships. Our clients come to see us as a trusted advisor who can help them navigate the complexities of the global market and gain a competitive edge. This collaborative approach is the most effective way to accelerate the adoption of low-carbon stainless steel, creating a win-win scenario where our clients succeed, our business grows, and we collectively contribute to a more sustainable industrial future.
Low-carbon steel needs standardizationTrue
Clear international standards prevent greenwashing and enable reliable comparison of materials' carbon footprints.
Demand alone drives steel adoptionFalse
While demand is crucial, supplier education and policy incentives are equally important for widespread adoption.
Conclusion
The shift to low-carbon stainless steel is not a compromise on quality but an embrace of superior, cleaner technology. Through the proven EAF process, we can deliver pipes that meet every technical standard while drastically reducing environmental impact, building the resilient and responsible supply chains of tomorrow.
-
Ensure compliance with international standards for stainless steel in industrial projects ↩
-
Learn about the distinct properties and uses of these steel grades ↩
-
Explore XRF's role in ensuring steel purity and quality ↩
-
Learn how ASTM standards govern stainless steel manufacturing to meet industry specifications ↩
-
Understand ISO’s role in developing sustainable standards for stainless steel. ↩
Have Questions or Need More Information?
Get in touch with us for personalized assistance and expert advice.