CE-PED Certification for Pressure Equipment: Pipe Supplier Checklist
Struggling to navigate the complex requirements of the European market for pressure equipment? Sourcing components like stainless steel pipes without the proper CE-PED certification can lead to blocked shipments, project delays, and significant legal liabilities, putting your entire European operation at risk.
CE-PED (Pressure Equipment Directive 2014/68/EU) certification is a mandatory legal requirement for any pressure equipment and components, including pipes, sold within the European Economic Area. It signifies that the product meets the EU's stringent essential safety requirements for design, manufacturing, and testing.
As the Global Business Director for MFY, I’ve seen firsthand how crucial this certification is for our clients. It’s not just a rubber stamp; it's a testament to a manufacturer's commitment to safety, quality, and global standards. This guide demystifies the process, showing what it takes for a supplier like us to earn and maintain this mark of excellence.
This checklist is more than a procedural guide; it's a look behind the curtain at the rigorous systems that separate world-class suppliers from the rest. The journey to CE-PED certification is a demanding one, requiring deep investment in quality management, material traceability, and manufacturing discipline. It forces a supplier to elevate every aspect of their operation, from raw material procurement to final inspection. For our clients—the engineering contractors, distributors, and manufacturers who build critical systems—understanding this process is vital. It provides the assurance that the components you integrate into your projects are not just compliant on paper, but are the product of a culture of quality, ensuring safety and reliability for the end-user.
What is the importance of CE-PED certification for pressure equipment?
Are you concerned about market access and legal compliance when sourcing pipes for European projects? Using non-certified components is not an option; it can halt your projects, lead to hefty fines, and damage your reputation, effectively shutting you out of a lucrative market.
CE-PED certification is paramount as it serves as a legal passport for pressure equipment entering the European market. It confirms adherence to essential safety requirements, mitigates liability for all stakeholders, and acts as a clear differentiator of quality and reliability in a competitive global landscape.
The true weight of this certification often becomes clear only when it’s missing. I recall working with a new client, an equipment integrator in Italy, who had previously sourced pipes from a non-certified supplier to save on costs. A random inspection by local authorities on their finished product—a skid-mounted pumping system—flagged the non-compliant pipes. The entire batch of systems was impounded, leading to a six-month delay and severe contractual penalties. When they switched to MFY, the first thing they asked for was our complete CE-PED documentation. For them, our certification wasn't just a document; it was a guarantee against catastrophic business disruption. It proves that a supplier has invested in the necessary systems to meet the highest safety benchmarks, providing peace of mind that goes far beyond the material itself. It’s a fundamental requirement for any serious player in the European market.
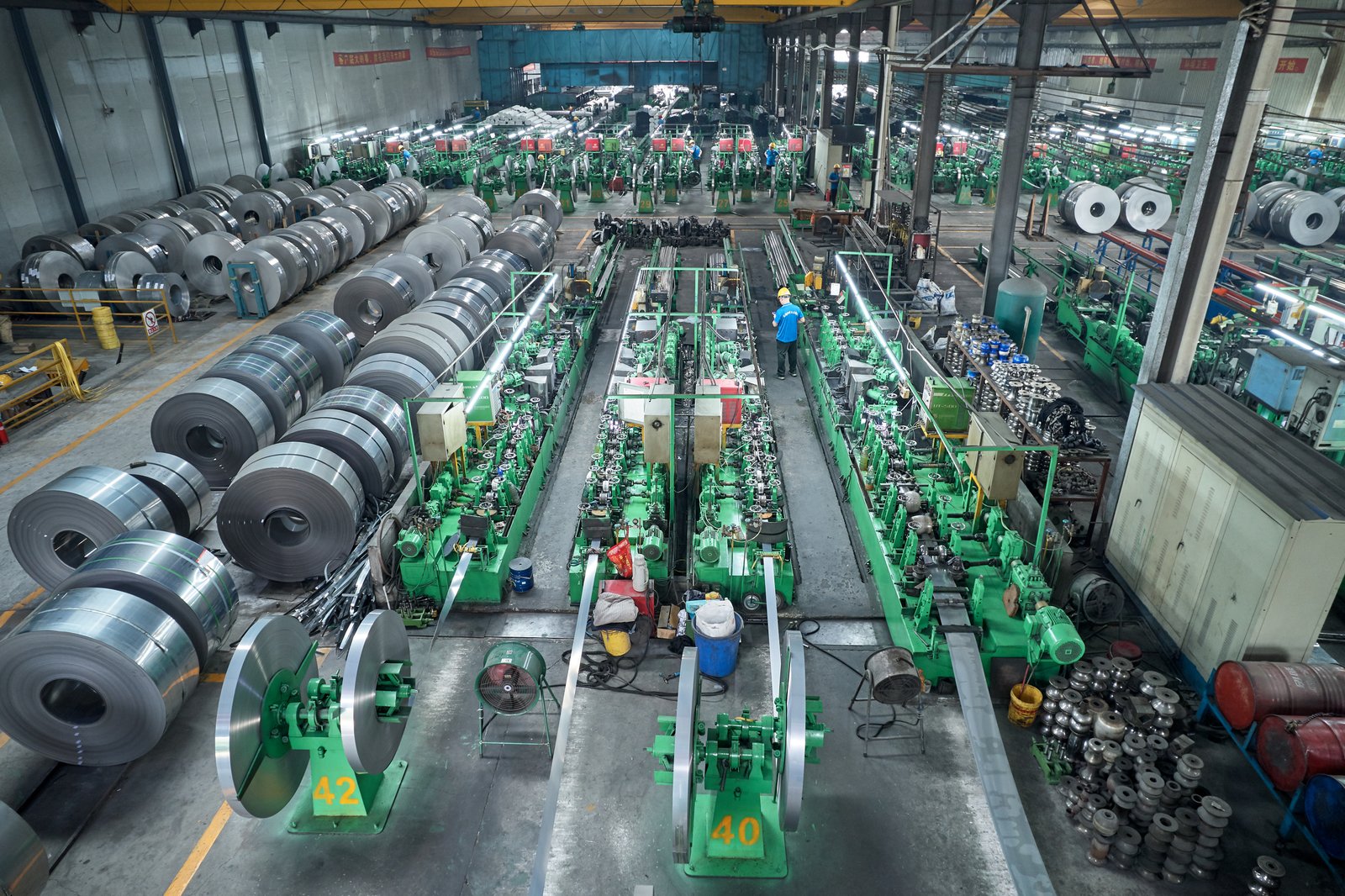
The importance of the CE marking under the Pressure Equipment Directive (PED) 2014/68/EU, cannot be overstated for any manufacturer or supplier in the pressure equipment supply chain. It is far more than a simple trade compliance issue; it is a foundational pillar of safety, quality assurance, and market strategy. For a pipe supplier like MFY, achieving and maintaining this certification is a strategic imperative that directly impacts our ability to serve our target clients in Europe and other regions that recognize CE standards. The directive's primary goal is to ensure the free movement of products within the European Economic Area (EEA) by harmonizing national laws regarding the safety of pressure equipment. This harmonization means that once a product like a stainless steel pipe is certified, it can be sold anywhere in the EEA without needing further national approvals. However, the process to affix that CE mark is intensive, demanding a complete alignment of a company's design, manufacturing, and quality processes with the Essential Safety Requirements (ESRs) laid out in the directive. For our clients, whether they are engineering contractors building a chemical plant or distributors supplying local markets, our CE-PED certification is their assurance that the components we provide will not become a point of failure, either legally or mechanically.
Unlocking Market Access to the European Union
The most immediate and tangible importance of CE-PED certification is that it grants legal market access to the entire European Economic Area, a market of over 450 million consumers. Without the CE mark, it is illegal to place pressure equipment or relevant components on the market in any of the member states. This acts as a hard barrier to entry. For MFY, a company with a mission for global expansion, this is not optional; it's the price of admission. Our certification allows our stainless steel pipes to flow seamlessly into projects across Europe, from a power plant in Germany to a pharmaceutical facility in Ireland.
This "passport" function simplifies the supply chain immensely for our clients. An engineering & construction contractor working on a multi-country project doesn't need to worry about different national regulations for the pipes they source from us. Our single CE-PED certification covers them across the board. I remember a discussion with a large French distributor who was consolidating their supplier list. A key criterion was mandatory CE-PED certification for all pressure components. They explained that managing suppliers with varying national certifications had become a logistical nightmare. By partnering with a fully certified supplier like MFY, they streamlined their compliance process, reduced their administrative burden, and minimized their risk of importing non-compliant goods.
The certification is not just for direct export to the EU. Many of our clients in the Middle East and Southeast Asia are equipment integrators who build systems destined for the European market. They rely on us to provide compliant components so that their final assembled product can be easily certified. In this way, our certification becomes a critical enabler for our clients' own export ambitions.
Ensuring Product Safety and Mitigating Liability
At its core, the PED is a safety directive. Its Essential Safety Requirements (ESRs) are designed to prevent the risks associated with pressurized systems, such as explosions or leaks of hazardous substances. The certification process forces a manufacturer to rigorously analyze and control these risks. This involves everything from verifying the chemical and mechanical properties of raw materials to ensuring the integrity of welds and conducting appropriate non-destructive testing (NDT). By adhering to these requirements, we are not just complying with a law; we are manufacturing a safer product.
This has profound implications for liability. In the event of an equipment failure, investigators will scrutinize the entire supply chain. If a component is found to be non-compliant, the liability can fall on the equipment manufacturer, the installer, the distributor, and the component supplier. Having a valid CE-PED certification, supported by robust technical documentation and a certified quality management system, provides a powerful legal defense. It demonstrates that the supplier has exercised due diligence and followed established best practices to ensure safety.
For our target clients, this is a critical shield. When an engineering contractor specifies MFY's CE-PED certified pipes, they are not only getting a quality product but also incorporating a documented chain of conformity into their project records. This protects their firm, their clients, and the public from the consequences of component failure, making the choice of a certified supplier a fundamental part of their risk management strategy.
Building Brand Trust and Competitive Advantage
In a crowded global market, CE-PED certification is a powerful differentiator. It is an internationally recognized symbol of quality, safety, and reliability. For a Chinese company like MFY, it is an unambiguous statement that our products meet the same high standards as any European manufacturer. This helps to overcome any outdated perceptions about the quality of products from different regions and builds immense trust with discerning clients. It demonstrates a long-term commitment to the market and a willingness to invest in the processes necessary to be a world-class supplier.
This trust becomes a tangible competitive advantage. When a distributor or contractor is evaluating suppliers, the presence of CE-PED certification often moves a supplier to the top of the list. It simplifies their procurement process and gives them confidence in the product's performance. We've seen this play out many times. A potential client will compare us to a local or regional supplier with a lower price point but no certification. The conversation shifts from price to risk. The small saving on the initial purchase is quickly outweighed by the potential costs of non-compliance, project delays, and liability.
Ultimately, the certification becomes part of our brand identity. MFY's vision is to be a leading international trade and service brand. We cannot achieve this without embracing the highest international standards. Our CE-PED certification is a core part of that vision, signaling to the world that we are a reliable, high-quality partner for the most demanding applications.
CE-PED is mandatory for EU marketTrue
CE-PED certification is legally required for all pressure equipment sold in the European Economic Area, as stated in Directive 2014/68/EU.
CE-PED only covers product designFalse
CE-PED certification encompasses the entire manufacturing process including material selection, production, testing, and quality management systems.
How can pipe suppliers prepare for CE-PED certification?
Embarking on the CE-PED certification journey feels daunting, doesn't it? The sheer volume of technical, procedural, and quality management requirements can seem overwhelming, leaving many suppliers unsure where to even begin and fearful of making costly mistakes in the process.
Preparation begins with a thorough gap analysis to understand existing non-conformities with the directive. This is followed by establishing a dedicated internal team, investing in comprehensive training on PED requirements, and systematically upgrading quality management and documentation systems to meet the stringent standards.
From my own experience guiding MFY through this rigorous process, the most crucial first step was acknowledging that this is not an overnight task but a deep, organizational transformation. It's not about "passing a test," but about embedding a new culture of quality. We started by bringing in an external consultant to conduct a no-holds-barred gap analysis. The results were sobering, revealing gaps not just in our documentation but in how we tracked materials and managed production deviations. This honest assessment was our true starting point. It allowed us to create a realistic roadmap, allocate the necessary resources, and get buy-in from every department, from procurement to the factory floor. This foundational work is what turns a complex challenge into a manageable project and is essential for any supplier serious about achieving certification.
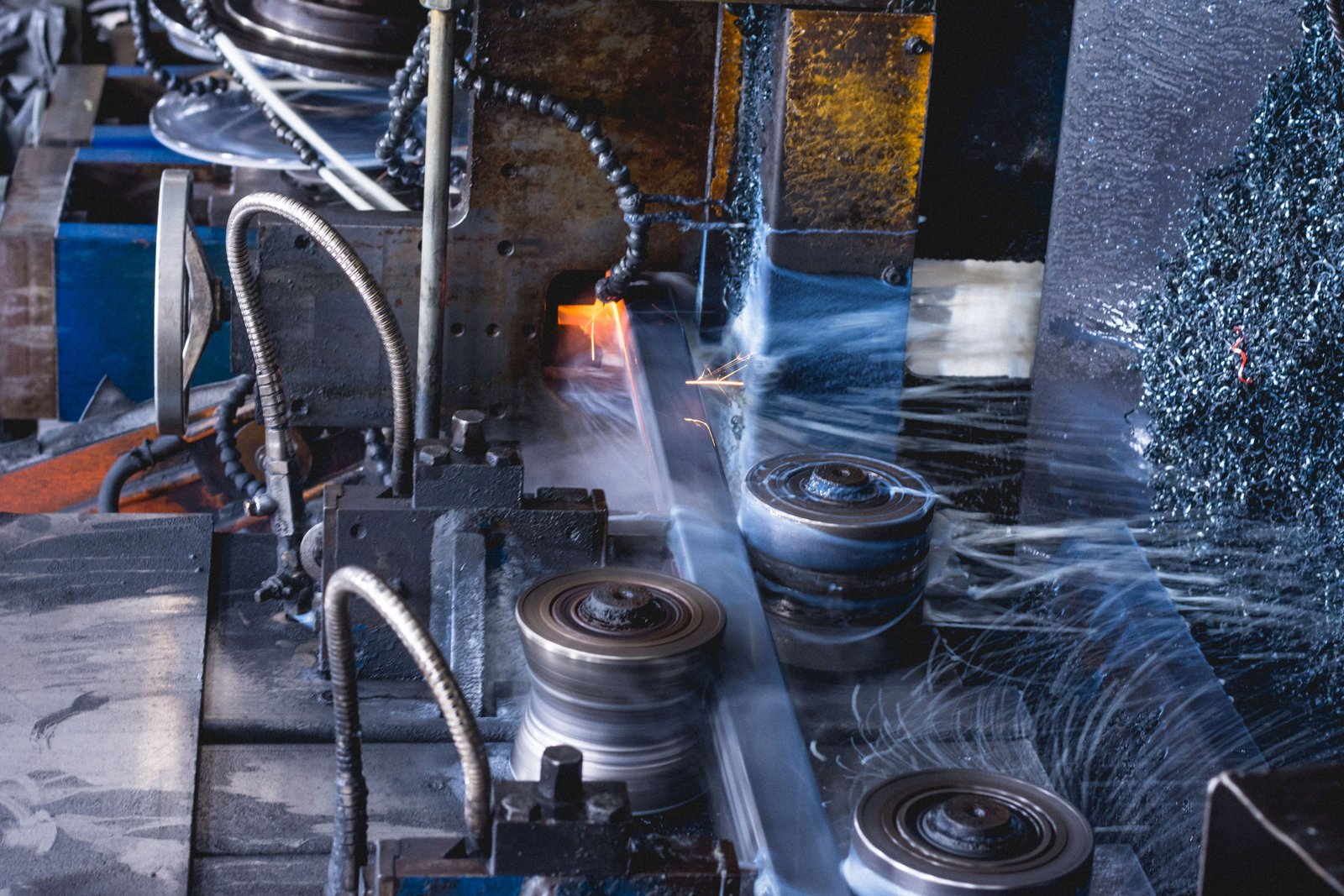
Preparing for CE-PED certification is a systematic and resource-intensive undertaking that requires a long-term strategic commitment from the highest levels of management. It is not merely a quality control exercise but a comprehensive overhaul of a company's design, manufacturing, and documentation processes to align with the legal requirements of the European Union. For a pipe supplier, whose products are often fundamental components in larger pressure systems, the scrutiny is particularly intense. The preparation process must be methodical, transparent, and thorough, as any gaps will inevitably be discovered during the conformity assessment by the Notified Body1. At MFY, our journey to certification was a multi-year project that touched every aspect of our operations. It involved significant investment in personnel, training, and technology. Based on our experience, a successful preparation strategy can be broken down into several key phases, starting long before the official application is ever submitted. The goal is to build a robust system of compliance from the ground up, ensuring that the requirements of the directive are not just met, but are ingrained in the company's daily operations. This proactive approach is far more effective than trying to retrospectively apply fixes to a flawed system.
Conducting a Comprehensive Gap Analysis
The first and most critical step in preparing for CE-PED certification is to conduct a detailed gap analysis. This involves a meticulous comparison of the company's current practices against every applicable requirement in the Pressure Equipment Directive. This analysis should be led by a knowledgeable individual or team and should cover everything from design controls and material sourcing to manufacturing processes, welding procedures, testing methods, and technical documentation. A supplier cannot fix what they don't know is broken. An honest and critical self-assessment is essential. For example, during our initial gap analysis at MFY, we identified that our existing material traceability system, while robust for our own purposes, did not fully meet the PED's specific requirement for transferring markings, which demands a documented and audited procedure to ensure the identity of a material is never lost, from the original steel mill certificate to the final pipe.
This analysis should result in a detailed report outlining all areas of non-conformity, categorized by risk and level of effort required to remediate. This document becomes the master plan for the certification project. It is often highly beneficial to engage an external consultant or a Notified Body for a preliminary audit. Their impartial, expert perspective can identify gaps that internal teams might overlook due to familiarity with existing processes. This initial investment can save a tremendous amount of time and money by ensuring the preparation efforts are focused on the right areas from the very beginning.
Establishing a Dedicated Cross-Functional Team
Achieving CE-PED certification cannot be the responsibility of a single person or department. It requires a collaborative, cross-functional effort. A dedicated project team should be established, comprising members from key departments including Quality Assurance, Production, Engineering, Procurement, and Sales. This team acts as the engine of the certification project, responsible for implementing the changes identified in the gap analysis. The team should have a clear mandate from senior management, a defined project charter, and the authority to enact necessary changes across departmental lines.
At MFY, our PED task force met weekly to track progress against our project plan. The production manager was responsible for implementing new welding procedure specifications (WPS), the procurement manager was tasked with upgrading our supplier audit process for raw material providers, and the quality manager oversaw the complete rewrite of our quality manual and technical documentation. This collaborative approach ensures that all facets of the directive are addressed in an integrated manner. For instance, the engineering team cannot develop PED-compliant designs without understanding the production team's capabilities for testing, and the procurement team must understand the material certificate requirements (e.g., EN 10204 3.1) needed by the quality team. This synergy is vital for building a compliant system that is not only effective but also efficient and sustainable.
Investing in Training and Competency Development
The Pressure Equipment Directive is a complex technical and legal document. It is unreasonable to expect that existing staff will instinctively understand its nuances. A significant investment in training is therefore non-negotiable. This training must be tailored to different roles within the organization. For example, welders and NDT operators require specific training and qualification according to harmonized European standards. Quality and engineering personnel need in-depth training on the directive's requirements for risk assessment (hazard analysis), conformity assessment modules, and the compilation of the Technical File. Even the sales and marketing team needs to be trained on the scope and limitations of the certification so they can communicate accurately with clients.
We found this investment to be one of the most impactful. We brought in specialists to train our NDT personnel to be certified according to ISO 9712, a requirement for certain conformity modules. We also sent our lead quality engineers to advanced seminars on the PED. This not only provided them with the necessary knowledge but also empowered them to become internal champions for the new processes. A well-trained workforce is more likely to understand the "why" behind the new rules, leading to better adoption and fewer errors. This competency development is not a one-time event; it must be an ongoing process to keep up with changes in the standards and to train new employees, ensuring the culture of compliance is maintained over the long term.
Gap analysis is the first stepTrue
A thorough gap analysis is essential to identify existing non-conformities with PED requirements before starting the certification process.
Certification is a quick processFalse
CE-PED certification requires a long-term strategic commitment and organizational transformation, not just a quick test.
What are the key requirements for achieving CE-PED certification?
You're ready to pursue certification, but the specific requirements feel like a dense, impenetrable code. What exactly do you need to have in place? The fear of missing a critical piece of documentation or failing a key audit can cause significant anxiety and delay.
The key requirements include compiling a detailed Technical File with risk assessments, implementing a robust Quality Management System (QMS) compliant with the directive, ensuring full material traceability from source to final product, and successfully passing a conformity assessment by a Notified Body.
In my experience, the single most challenging yet crucial requirement is material traceability2. For a pipe supplier, this is the backbone of our certification. We must be able to prove, with auditable records, the exact origin and properties of the steel used in every single pipe marked with the CE logo. I remember an audit by our Notified Body where they randomly selected a pipe from our inventory and asked for its complete history. Within minutes, we had to produce the original mill certificate (EN 10204 3.1), our internal inspection reports, and the production records linking it to a specific batch. This level of granular control is non-negotiable and requires an incredibly disciplined system. It's the ultimate proof that you're not just making promises about quality, but that you have the system to back it up.
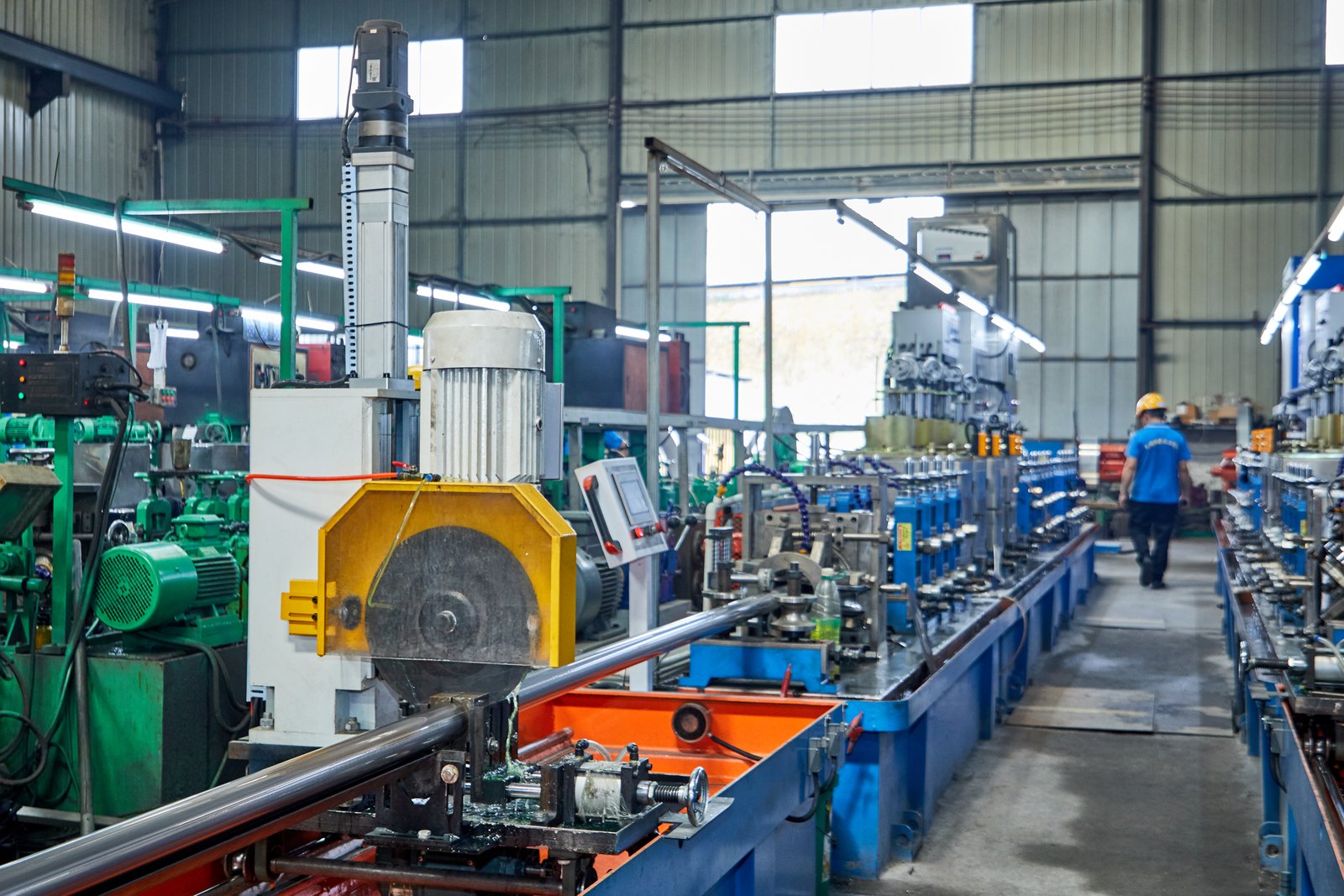
Achieving CE-PED certification requires fulfilling a series of stringent, interconnected requirements that are legally mandated by the directive. These are not optional guidelines; they are Essential Safety Requirements (ESRs) and procedural obligations that a manufacturer must demonstrably meet. The entire framework is designed to ensure that products placed on the European market are safe and fit for purpose. For a pipe supplier like MFY, these requirements translate into specific, actionable systems and documents that must be developed, implemented, and rigorously maintained. The process culminates in a conformity assessment, where an independent, EU-appointed Notified Body3 audits the supplier against these requirements. The Notified Body acts as an impartial referee, and their approval is necessary to legally affix the CE mark for most categories of pressure equipment. Successfully navigating this process depends on a deep understanding of and adherence to three core pillars: comprehensive technical documentation, a robust quality management system, and an unbroken chain of material conformity. Failing in any one of these areas will result in the failure of the entire certification effort.
Technical Documentation and Risk Assessment
The foundation of any CE-PED submission is the Technical File (also known as the Technical Documentation). This is a comprehensive dossier that contains all the evidence to prove that the product complies with the directive. It is a living document that must be kept for at least 10 years after the product is placed on the market. A critical component of the Technical File is the hazard analysis or risk assessment. The manufacturer must identify all potential hazards associated with the pipe under pressure (e.g., material failure, weld failure, over-pressurization) and demonstrate how the design and manufacturing processes mitigate these risks to an acceptable level.
The file must also include detailed design calculations, drawings, material specifications, manufacturing procedures (especially for welding, which requires qualified welders and approved Welding Procedure Specifications - WPS), reports of examinations and tests carried out (like hydrostatic testing or non-destructive testing - NDT), and instructions for the user. For MFY, this meant standardizing our production travelers and inspection reports to capture all the data required by the directive, ensuring that for any given pipe, we have a complete documentary record of its creation and verification. This meticulous record-keeping is the primary evidence examined by the Notified Body during an audit.
Quality Management System (QMS) Implementation
A supplier cannot achieve reliable compliance without a systematic approach to quality. The PED requires manufacturers to operate under a suitable Quality Management System (QMS). While full ISO 9001 certification is not always mandatory, the chosen conformity assessment module often requires a QMS that is audited and approved by a Notified Body. For example, Modules D/D1, H, and H1 all require a comprehensive QMS focused on production, final inspection, and testing. This system must define procedures for everything from contract review and document control to the calibration of measuring equipment and the handling of non-conforming products.
At MFY, we chose to pursue certification under Module H, which is a full quality assurance system. This required us to integrate the PED's specific requirements into our existing ISO 9001 framework. We had to create new procedures for tasks like the "particular appraisal of materials," a PED requirement that goes beyond standard material inspection. The QMS is the engine that drives continuous compliance. It ensures that processes are consistent, results are repeatable, and that there is a formal system for identifying and correcting any deviations. The Notified Body's audit of the QMS is incredibly thorough, as they need assurance that the supplier can consistently produce compliant products, not just a single "golden sample."
Material Traceability and Conformity Assessment
For a component manufacturer like a pipe supplier, material is everything. The PED places enormous emphasis on using the correct materials and being able to prove it. This means full traceability is a non-negotiable requirement. The supplier must have a bulletproof system for tracking materials from the original source (the steel mill) all the way to the finished pipe. The most common requirement is for materials to be certified with an inspection certificate EN 10204 Type 3.1. This certificate is issued by the mill and declares that the material complies with the order's specifications, including its chemical composition and mechanical properties, based on specific tests.
Our system at MFY involves assigning a unique heat number to each batch of raw material and tracking that number through every stage of production. When a pipe is cut, the markings must be carefully transferred to each piece according to a documented procedure. This ensures that even the smallest off-cut can be traced back to its source certificate. This traceability is essential for the conformity assessment process, which is the final step where a manufacturer selects a "module" to demonstrate compliance. The modules vary in their level of Notified Body involvement, depending on the risk category of the equipment.
Module | Description | QMS Requirement | Notified Body Involvement |
---|---|---|---|
A | Internal Production Control | No | None (for Category I only) |
B | EU-Type Examination (Design) | No | Reviews Technical File and type sample |
D | Production Quality Assurance | Yes (Audited) | Approves and surveils QMS |
F | Product Verification | No | Verifies and tests every product or batch |
H | Full Quality Assurance | Yes (Audited) | Approves and surveils comprehensive QMS |
H1 | Full QA with Design Examination | Yes (Audited) | As Module H, plus design review/testing |
For our stainless steel pipes, which fall into higher categories, a combination like B+D or a comprehensive module like H is typically required. Choosing the right module and successfully passing its assessment is the final gate to earning the right to affix the CE mark.
Material traceability is mandatory for CE-PEDTrue
The PED requires full traceability of materials from source to final product, verified by EN 10204 3.1 certificates.
ISO 9001 certification is required for PEDFalse
While a QMS is required, full ISO 9001 certification isn't mandatory - PED has its own QMS requirements that may differ.
What steps should pipe suppliers take to ensure compliance with CE-PED standards?
Knowing the requirements is one thing, but how do you actually implement them effectively? The path to compliance is filled with potential pitfalls, from choosing the wrong Notified Body4 to failing to properly document critical processes, leading to wasted time and effort.
To ensure compliance, suppliers must engage a Notified Body early for guidance, implement a meticulous material traceability system from receiving to dispatch, standardize all production and testing protocols according to harmonized standards, and maintain exhaustive, auditable records for every step of the process.
The most critical step we took at MFY was to treat compliance not as a project with an end date, but as a new, permanent way of operating. It’s about building the system and then living by it every day. For example, we didn't just write a procedure for material marking transfer; we automated it by linking it to our ERP system. When a pipe is designated for a PED order, the system automatically flags it and requires specific quality checks and documentation at each workstation. This removed the chance of human error and made compliance the default path, not an extra step. This proactive, system-based approach is the only way to guarantee consistent adherence to the standards and to be "audit-ready" at all times.
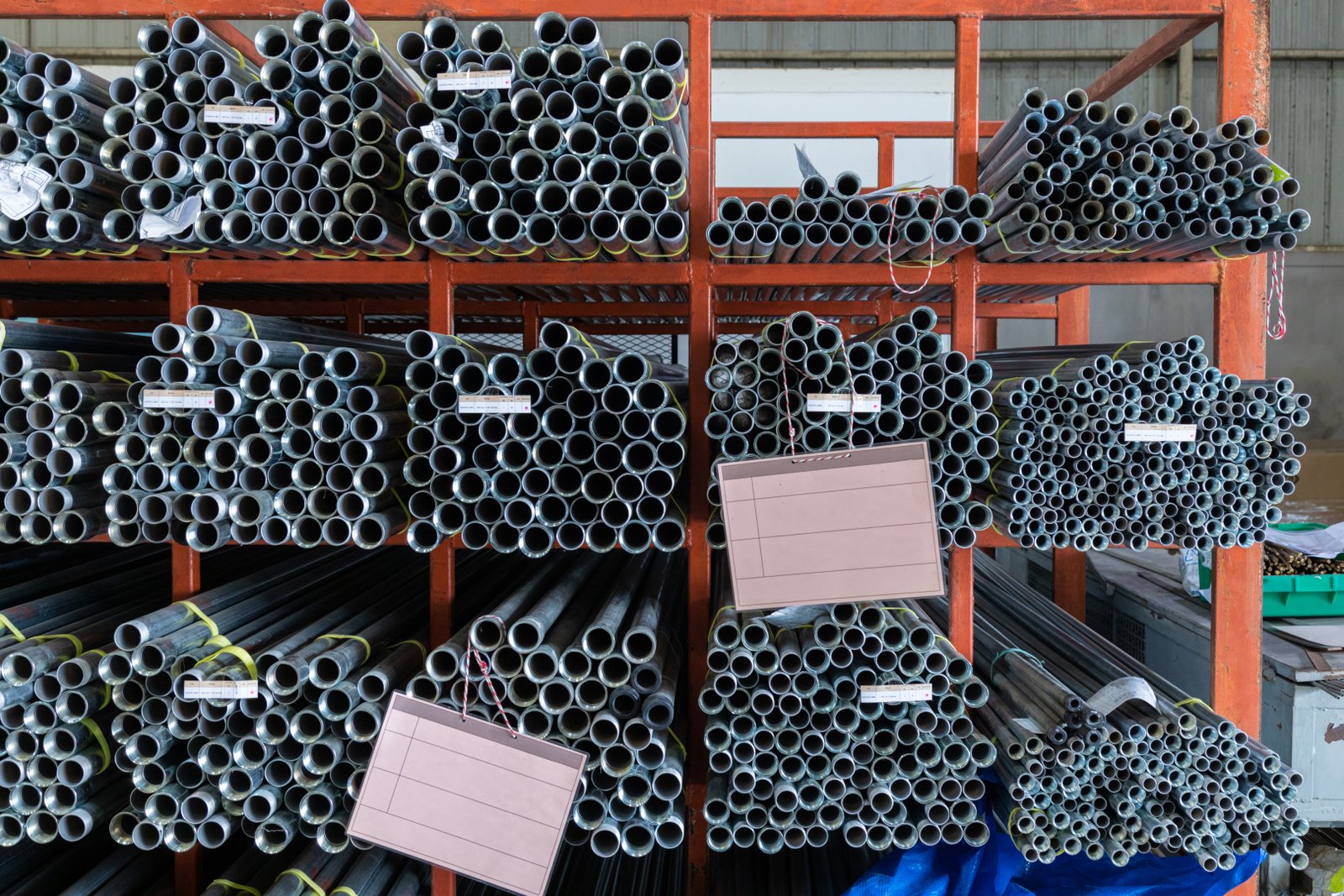
Ensuring ongoing compliance with CE-PED standards is a dynamic and continuous process, not a one-time achievement. A pipe supplier cannot simply pass an audit, receive a certificate, and then revert to old habits. The directive and the Notified Bodies require a sustained demonstration of conformity. This means embedding the principles of the PED into the very fabric of the organization's culture and daily operations. The steps taken to achieve initial certification must be solidified into robust, repeatable processes that are followed without fail. The goal is to create a state of perpetual "audit-readiness," where an unannounced visit from a Notified Body would be a routine event, not a cause for panic. At MFY, we view compliance as a core business function, akin to financial accounting or workplace safety. It requires clear procedures, designated responsibilities, regular verification, and a commitment to continuous improvement. For our clients, this sustained compliance is their assurance that the quality and safety of the pipes they receive today will be the same as the ones they receive years from now.
Engaging with a Notified Body Early and Collaboratively
One of the most effective steps a supplier can take is to move from a transactional relationship with their Notified Body to a collaborative one. Instead of viewing the Notified Body as a final examiner, it is wise to engage them early in the preparation phase. While they cannot act as consultants (to maintain impartiality), they can provide invaluable clarification on the interpretation of the directive's requirements and give feedback on proposed compliance strategies. This early engagement helps to prevent costly missteps. A supplier might spend months developing a new testing procedure only to find during the formal audit that it doesn't meet the Notified Body's interpretation of a specific harmonized standard.
We adopted this approach by scheduling preliminary meetings with our chosen Notified Body to review our certification roadmap. We discussed our proposed conformity assessment module, our plans for qualifying our welding procedures, and our approach to the hazard analysis. This dialogue provided us with greater clarity and confidence that our efforts were pointed in the right direction. It helped to demystify the process and build a professional, transparent relationship. This partnership is crucial, as the Notified Body will be a long-term partner, returning for regular surveillance audits to ensure the quality system remains effective.
Implementing a Rigorous Material Traceability System
For a pipe supplier, the entire compliance structure rests on the integrity of the material. Therefore, implementing a bulletproof traceability system is arguably the single most important practical step. This system must create an unbroken, auditable link from the certified raw material to the final shipped product. This goes beyond simple inventory management. It requires specific procedures for every stage. Upon receiving raw materials, the EN 10204 3.1 certificate must be verified and digitally linked to the physical material's heat number. During production, any cutting or processing that separates the material must be accompanied by a documented "marking transfer" procedure to ensure the identity is maintained.
At MFY, we invested in a barcoding system integrated with our ERP. Every coil of steel, every bundle of pipes, and eventually every individual pipe for a PED order has a unique identifier that links back to its complete history. This system tracks who handled the material, which machine it was processed on, and what tests were performed. When a Notified Body auditor walks onto our factory floor and points to a pipe, we can scan it and instantly bring up its entire pedigree. This level of granular control is the only way to provide the objective evidence required to satisfy the directive's stringent material requirements.
Standardizing Production and Testing Protocols
Consistency is the bedrock of quality. To ensure compliance, all production and testing processes critical to safety must be standardized and validated according to recognized harmonized standards5. This is particularly crucial for "special processes" like welding. All welding must be performed according to qualified Welding Procedure Specifications (WPS), and the welders themselves must hold current qualifications (welder performance qualifications - WPQ). These are not internal company standards; they must be developed and tested according to European standards like EN ISO 15614 (for WPS) and EN ISO 9606 (for welders).
Similarly, all testing procedures—from hydrostatic pressure tests to non-destructive testing (NDT) like radiographic or ultrasonic examination—must be formalized into detailed, written protocols. These protocols must specify the equipment to be used, the calibration requirements for that equipment, the step-by-step method, and the acceptance criteria. At MFY, every test is documented on a formal report that becomes part of the pipe's permanent Technical File. This standardization removes ambiguity and operator discretion, ensuring that every pipe is manufactured and verified in precisely the same way, guaranteeing a consistent level of safety and quality that meets the PED's expectations.
CE-PED compliance requires ongoing effortTrue
The article emphasizes that compliance is not a one-time achievement but a continuous process embedded in daily operations.
Notified Bodies can act as consultantsFalse
The article clarifies that while Notified Bodies provide guidance, they cannot act as consultants to maintain impartiality.
How can pipe suppliers maintain their CE-PED certification over time?
You've earned your CE-PED certification, a massive achievement. But now the real work begins. How do you prevent compliance from slipping over time? The risk of standards dropping or documentation lapsing can jeopardize the certification you worked so hard to obtain.
Maintaining CE-PED certification requires a commitment to continuous vigilance. This includes conducting regular internal audits, actively monitoring for changes in regulations and standards, providing ongoing employee training, and fostering a deep-rooted organizational culture where quality and compliance are paramount.
From my perspective at MFY, maintaining certification is about perpetual motion. It’s a cycle of review, learning, and improvement. We have a dedicated regulatory affairs manager whose primary job is to track updates from the European Commission6 and standards bodies. Every six months, our internal audit team, which is independent of production, conducts a full "mock audit" as if they were the Notified Body. This proactive approach ensures we catch any potential issues long before our official surveillance audit. It's this relentless self-scrutiny that gives our clients confidence, as it proves our commitment is not just to a certificate on the wall, but to the daily practice of excellence it represents.
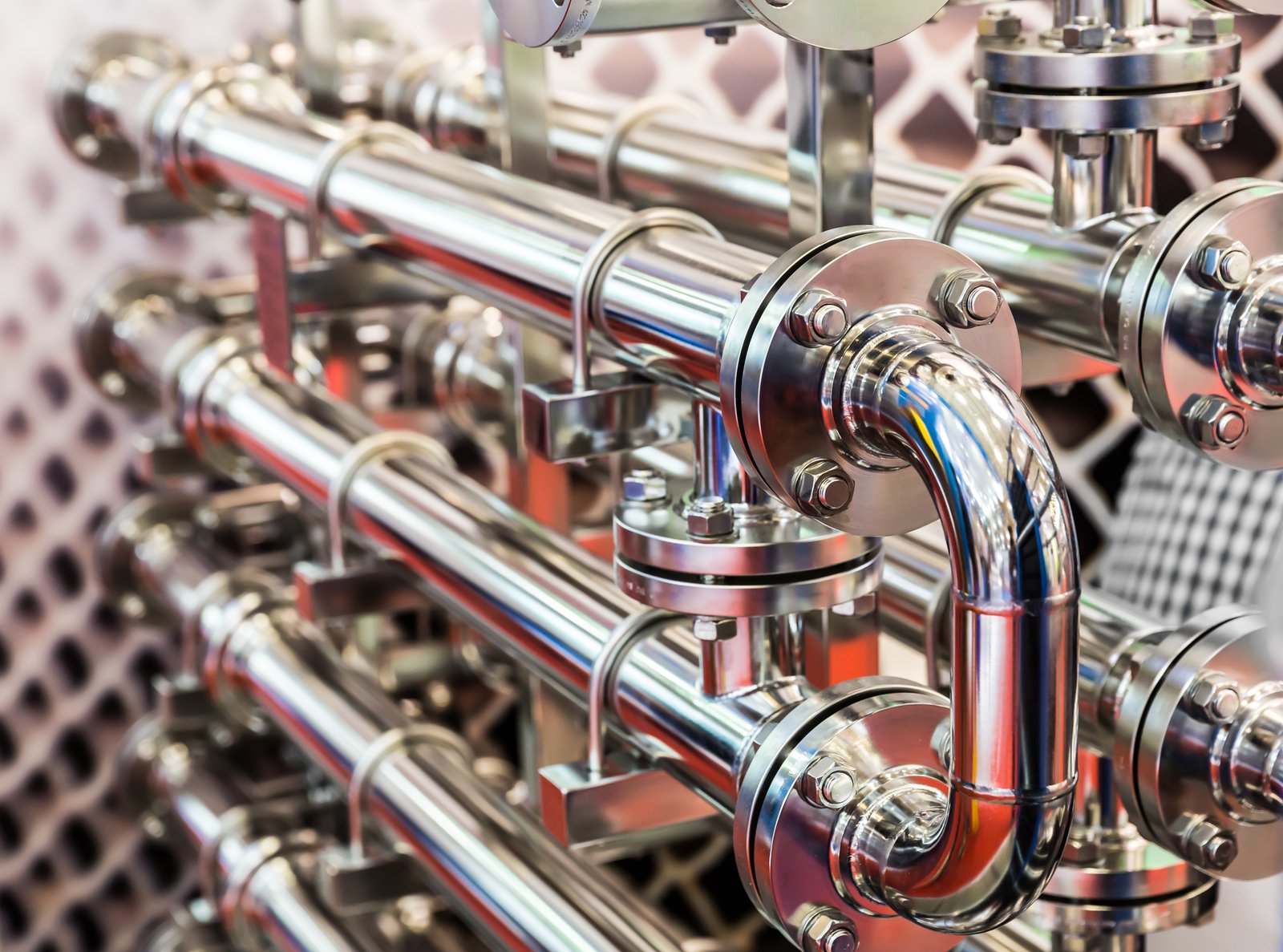
Maintaining CE-PED certification is a continuous and active process, fundamentally different from the project-based approach of achieving it initially. The certificate issued by a Notified Body is not a permanent license; it is a conditional approval that is subject to regular surveillance and renewal. The supplier must continually demonstrate that the Quality Management System (QMS) remains effective and that the products consistently meet the Essential Safety Requirements (ESRs) of the directive. A failure to do so can result in the suspension or withdrawal of the certification, which would be catastrophic for a supplier serving the European market. Therefore, the focus must shift from implementation to sustenance. At MFY, we treat our CE-PED certification as a living entity that requires constant care and attention. This involves building a robust framework for continuous improvement and vigilance, ensuring that the high standards achieved during the initial audit become the permanent benchmark for all our operations. This commitment is essential to providing our clients with the unwavering assurance of safety and compliance they expect from a premier supplier.
Conducting Regular Internal Audits and Management Reviews
The cornerstone of maintaining compliance is a rigorous internal audit program. A supplier cannot rely solely on the Notified Body's periodic surveillance audits to identify problems. A dedicated, trained team of internal auditors should regularly assess all aspects of the PED-compliant QMS. These audits should be just as thorough as the external ones, checking for adherence to procedures, the quality of documentation, the integrity of material traceability, and the proper execution of tests7. The findings from these audits—both conformities and non-conformities—must be formally documented and reported directly to senior management.
Following the audits, a formal Management Review meeting should be held at planned intervals. This is a requirement of most quality systems, including those under the PED. In this meeting, top management must review the performance of the QMS, including the results of internal and external audits, customer feedback, process performance, and any non-conformities. The outcome of this review should be documented decisions and actions aimed at improving the system's effectiveness. This high-level oversight ensures that compliance remains a strategic priority and that the necessary resources are allocated to address any emerging issues.
Continuous Monitoring of Regulatory Changes
The regulatory landscape is not static. The Pressure Equipment Directive itself can be amended, and more frequently, the "harmonized standards" that provide a presumption of conformity are updated, replaced, or withdrawn. A harmonized standard is a European standard (EN) that has been officially endorsed by the European Commission. Following these standards makes proving compliance easier. If a supplier builds their processes around a specific standard (e.g., for welding8 or material testing) and that standard is updated, the supplier must update their internal processes and documentation accordingly to maintain their state-of-the-art compliance.
Maintaining certification requires a proactive system for monitoring these changes. This can involve subscribing to services from standards bodies, participating in industry associations, or assigning a specific person or department with the responsibility for regulatory intelligence. At MFY, our quality department is tasked with tracking the Official Journal of the European Union for any changes related to the PED and its associated standards. When a change is identified, a formal impact assessment is conducted to determine what changes are needed in our QMS, manufacturing processes, or Technical Files, ensuring we are never caught off guard by a regulatory shift.
Fostering a Culture of Quality and Compliance
Ultimately, procedures and audits can only go so far. Sustainable, long-term compliance is only possible when it is embedded in the company's culture. It must become "the way we do things here." This requires a top-down commitment from management that is demonstrated through actions, not just words. It involves investing in continuous training for all employees, from the welder on the floor to the engineer in the design office, so they understand their specific role in maintaining safety and compliance. It means empowering employees to raise quality concerns without fear of reprisal and celebrating successes in quality performance.
We work to foster this culture by making CE-PED compliance a visible part of our daily work. We hold regular "toolbox talks" on the factory floor about specific safety requirements. We link performance bonuses for production managers to key quality metrics like the internal audit pass rate and the reduction of non-conformities. When every employee understands that the CE mark on a pipe is a personal promise of quality and safety that they helped to create, the system becomes self-sustaining. This cultural foundation is the most powerful tool for maintaining certification, as it turns every employee into a guardian of the company's commitment to excellence.
CE-PED requires continuous complianceTrue
The certification is conditional and requires ongoing surveillance audits and QMS maintenance, unlike one-time achievements.
Internal audits are optional for PEDFalse
Regular internal audits are mandatory to proactively identify issues before Notified Body surveillance audits.
Conclusion
Ultimately, CE-PED certification is a non-negotiable benchmark of quality, safety, and market readiness. For pipe suppliers, the path involves rigorous preparation, meticulous documentation, and a deep, ongoing commitment to a culture of compliance that ensures long-term success in the European market.
-
Understand the role of the Notified Body in ensuring CE-PED compliance ↩
-
Learn about steps to maintain material traceability for CE-PED certification ↩
-
Understand the importance of Notified Bodies in CE-PED certification process ↩
-
Learn how Notified Bodies assist in CE-PED compliance and certification processes. ↩
-
Understand the specific harmonized standards required for processes under CE-PED compliance. ↩
-
Learn responsibilities of the European Commission regarding certification updates ↩
-
Discover detailed testing procedures in a PED-compliant QMS ↩
-
Understand impact of welding standard updates on certification ↩
Have Questions or Need More Information?
Get in touch with us for personalized assistance and expert advice.