ASTM A312 vs EN 10217: Key Differences Buyers Should Know
Are you navigating the complex world of stainless steel pipe procurement and finding yourself stuck between ASTM A312 and EN 10217? This confusion can lead to incorrect specifications and costly project setbacks. Making the wrong choice could result in non-compliance, operational failures, or budget overruns.
ASTM A312 is the primary American standard for austenitic stainless steel pipe for high-temperature and general corrosive service. In contrast, EN 10217, specifically EN 10217-7, is the harmonized European standard for welded stainless steel tubes intended for pressure purposes, aligning with the EU's Pressure Equipment Directive.
Choosing the right standard is more than a box-ticking exercise; it's a critical decision that impacts your project's safety, longevity, and regulatory compliance. The differences, though sometimes subtle, have significant implications for engineering design, fabrication, and long-term performance. As someone who has guided countless clients through this decision-making process, I want to demystify these standards for you.
In my years as Global Business Director at MFY, I’ve seen firsthand how a seemingly small mismatch in standards can create significant hurdles for international projects. For instance, a client in the engineering and construction sector was developing a facility intended for the European market but was more familiar with American ASTM standards. Procuring materials based solely on their usual specifications could have led to a complete rejection by European regulatory bodies. This highlights a crucial reality: understanding the DNA of each standard is not just technical diligence—it's a fundamental risk management strategy. This guide will move beyond simple definitions, delving into the practical consequences of your choice and equipping you with the knowledge to select the right stainless steel pipe with confidence, ensuring your supply chain is both efficient and resilient.
What are the main specifications of ASTM A312 and EN 10217?
Feeling overwhelmed by the technical jargon in material specifications? You might assume that stainless steel pipe standards are largely interchangeable, a mistake that can easily lead to procuring materials that are unsuitable for your project's specific regulatory and engineering environment, causing significant delays and compliance issues.
ASTM A312 covers seamless, straight-seam welded, and heavily cold-worked welded austenitic stainless steel pipe for high-temperature and corrosive service. EN 10217-7 specifically applies to welded austenitic and ferritic-austenitic stainless steel tubes for pressure purposes, with testing conditions aligned with European regulations like the PED.
To make an informed decision, it's essential to look beyond the surface and understand the foundational philosophy behind each standard. ASTM (American Society for Testing and Materials) standards are dominant in North America and often referenced globally in industries like oil and gas, which have strong U.S. engineering influences. They are developed by industry consensus and focus heavily on material properties and testing methods suitable for specific applications. On the other hand, the EN (European Norms) standards represent a harmonized system across the European Union, designed to eliminate trade barriers and ensure consistent safety and performance, particularly for equipment under pressure. EN 10217-7 is a prime example, being intrinsically linked to the legal requirements of the Pressure Equipment Directive (2014/68/EU). For a buyer in India or Southeast Asia working on a project for a European end-user, simply providing a pipe with similar chemical composition to an ASTM grade is not enough; it must meet the specific testing, certification, and traceability requirements mandated by the EN standard to be legally compliant. This distinction between a market-driven consensus standard and a regulation-driven harmonized standard is the most critical initial concept to grasp.
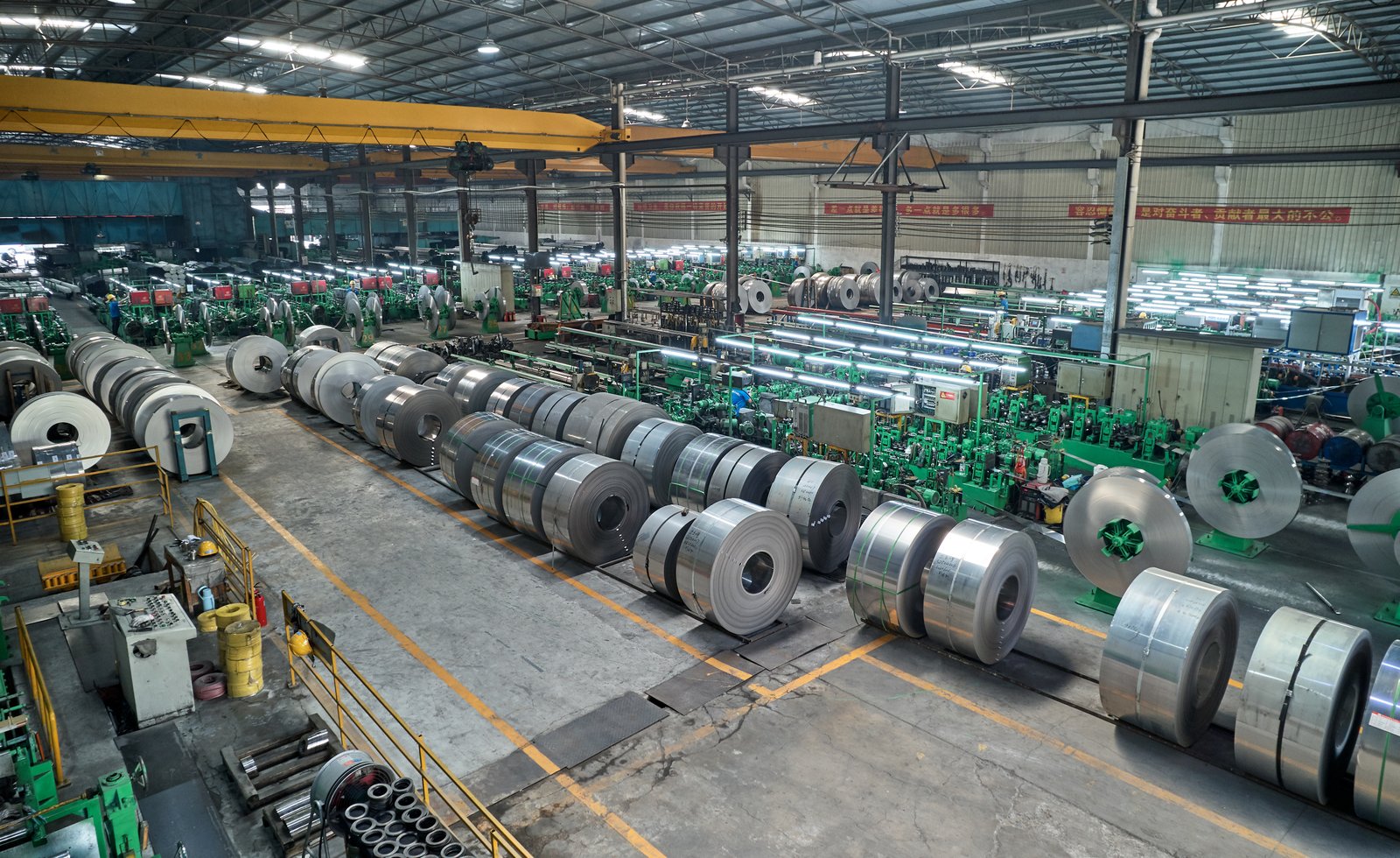
My team at MFY recently worked with a distributor in the Middle East who primarily stocked ASTM-specified materials. They received a large inquiry for a water treatment facility being built by a German contractor. The contractor's specifications clearly called for tubes compliant with EN 10217-7. While the distributor could offer a chemically equivalent grade under ASTM A312, they couldn't provide the required EN 10204 3.1 inspection certificate or the testing procedures mandated by the European standard. This forced them to outsource the request, losing the sale and highlighting a gap in their inventory strategy. This scenario underscores the importance of understanding the fundamental specifications, which dictate not just the physical product but the entire ecosystem of compliance and documentation surrounding it.
The American Standard: ASTM A312's Application-Centric Approach
The ASTM A312 standard is a cornerstone for industries like petrochemical, chemical processing, and power generation, particularly in regions that follow ASME (American Society of Mechanical Engineers) codes for design and construction, such as the ASME B31.3 for process piping. Its scope is broad, covering seamless and welded pipes intended for service in demanding environments characterized by high temperatures and corrosive media. The standard places a strong emphasis on ensuring the material can withstand these harsh conditions. Common grades specified under A312 include TP304/304L and TP316/316L, which have become benchmark materials for corrosion resistance.
The manufacturing and testing requirements within ASTM A312 are prescribed to validate this performance. For example, it mandates specific heat treatment procedures, such as solution annealing, to ensure the steel's microstructure is optimized for corrosion resistance and mechanical strength. Furthermore, it requires a series of tests, including a hydrostatic test to check for leaks and mechanical tests (tensile and flattening) to verify strength and ductility. For a manufacturing company building a new chemical reactor skid for export to the United States, specifying ASTM A312 pipe is non-negotiable, as it ensures seamless integration with the prevailing engineering and safety codes in that market.
This focus on application is what drives the standard's evolution. It is designed by and for the industries it serves, ensuring that the specifications remain practical and relevant to real-world challenges. When we supply A312 pipes, the Mill Test Certificate (MTC) provides a detailed record of the chemical analysis and mechanical test results, offering complete traceability and assurance that every length of pipe meets the stringent requirements for its intended high-stakes application.
The European Norm: EN 10217's Regulatory Harmonization
EN 10217 is not a single document but a series of standards for welded steel tubes for pressure purposes. The part relevant to our discussion is EN 10217-7: Stainless steel tubes. Its primary purpose is to provide one of the means of conforming to the Essential Safety Requirements (ESRs) of the EU's Pressure Equipment Directive (PED). This regulatory linkage is its most defining characteristic. If a piece of pressure equipment—be it a boiler, heat exchanger, or piping system—is to be sold and operated within the European Economic Area, it must bear the CE marking, and using materials compliant with harmonized standards like EN 10217-7 is the most direct path to achieving this.
The standard specifies technical delivery conditions for welded tubes made from a range of austenitic and austenitic-ferritic (duplex) stainless steels. The grade nomenclature is different; for example, the European equivalent of ASTM TP316L is 1.4404. EN 10217-7 outlines two test categories (TC1 and TC2), offering different levels of inspection and testing, which allows buyers to select the appropriate level of assurance for their application. This is a key difference from the more one-size-fits-all testing approach of A312.
Let's consider an equipment integrator building a pasteurization system for a dairy in France. This system operates under pressure and falls squarely under the PED. The integrator must use tubes certified to EN 10217-7 and be able to present the corresponding EN 10204 3.1 certificate, which is an inspection certificate issued by the manufacturer's authorized representative, independent of the production department. This level of mandatory third-party-verified documentation is a hallmark of the European system, designed to ensure a uniform level of safety across all member states. It's a system built on regulatory compliance first and foremost.
Comparative Overview: Scope and Manufacturing Focus
The fundamental difference in philosophy between ASTM A312 and EN 10217-7 directly influences their scope and how they treat manufacturing methods. While both aim to deliver reliable stainless steel tubes, their priorities and prescribed methodologies diverge, which is a critical point for global buyers sourcing materials for diverse projects. A construction contractor in Southeast Asia, for instance, might be bidding on two separate projects simultaneously: an American-designed LNG terminal and a European-funded infrastructure project. Understanding these differences is key to quoting accurately and delivering compliant materials for both.
ASTM A312 broadly covers seamless, straight-seam welded, and heavily cold-worked (HCW) welded pipe. The inclusion of seamless and HCW pipe makes it versatile for applications demanding high material integrity and a smooth internal finish. The EN 10217-7 standard, however, is exclusively for welded tubes for pressure applications. Seamless stainless pressure tubes are covered under a different standard, EN 10216-5. This separation is typical of the highly structured and specific nature of European Norms.
To illustrate these differences clearly, consider the following comparison:
Feature | ASTM A312 | EN 10217-7 |
---|---|---|
Primary Jurisdiction | United States / ASME-influenced regions | European Union / PED-regulated markets |
Core Philosophy | Industry consensus, application-driven | Regulatory harmonization (PED), safety-driven |
Product Scope | Seamless and Welded Pipe | Welded Tube Only |
Primary Application | High-temperature and general corrosive service | Pressure purposes |
Testing | Standardized testing (e.g., hydrostatic, tensile) | Two Test Categories (TC1, TC2) for varying risk |
Certification | Mill Test Certificate (MTC) to the standard | Inspection Certificate (e.g., EN 10204 3.1) required for PED |
For a distributor, this has clear implications. Stocking "dual-certified" pipe might seem like a solution, but one must ensure the material genuinely meets all the requirements of both standards, including the specific testing and documentation protocols. Often, a pipe manufactured to ASTM A312 will not have undergone the specific non-destructive testing (NDT) options or documentation trail required for EN 10217-7, making it non-compliant for a European pressure application despite having identical dimensions and chemical makeup.
ASTM A312 covers seamless pipesTrue
ASTM A312 includes specifications for both seamless and welded austenitic stainless steel pipes, making it more versatile for various applications.
EN 10217-7 applies to seamless tubesFalse
EN 10217-7 specifically applies only to welded stainless steel tubes; seamless tubes are covered under EN 10216-5.
How do the mechanical properties differ between ASTM A312 and EN 10217?
Are you assuming that equivalent steel grades like 316L and 1.4404 have identical mechanical properties regardless of the standard? This common oversight can lead to critical design miscalculations, as subtle differences in required strength and ductility can impact the safety and performance of your equipment.
While chemically similar, comparable grades under ASTM A312 and EN 10217-7 can have slightly different minimum requirements for mechanical properties. These variations are most notable in yield strength, tensile strength, and elongation values, directly affecting engineering calculations and material behavior under stress.
These seemingly minor discrepancies in minimum specified values are not accidental; they reflect the different safety factors and design philosophies embedded in the American (ASME) and European (PED) engineering codes. For an engineer designing a pressurized system, the minimum yield strength is a critical variable used to calculate the required wall thickness of a pipe. Using the value from the wrong standard could result in a pipe that is either over-engineered and costly or, more dangerously, under-engineered and unsafe. For example, some EN standards provide specified proof strength values at elevated temperatures, a level of detail not always present in ASTM standards but essential for designing equipment that operates above ambient temperatures. As we delve deeper, you'll see how these nuances in the data sheet translate into real-world consequences for fabrication, safety, and operational reliability, reinforcing the need for meticulous specification review.
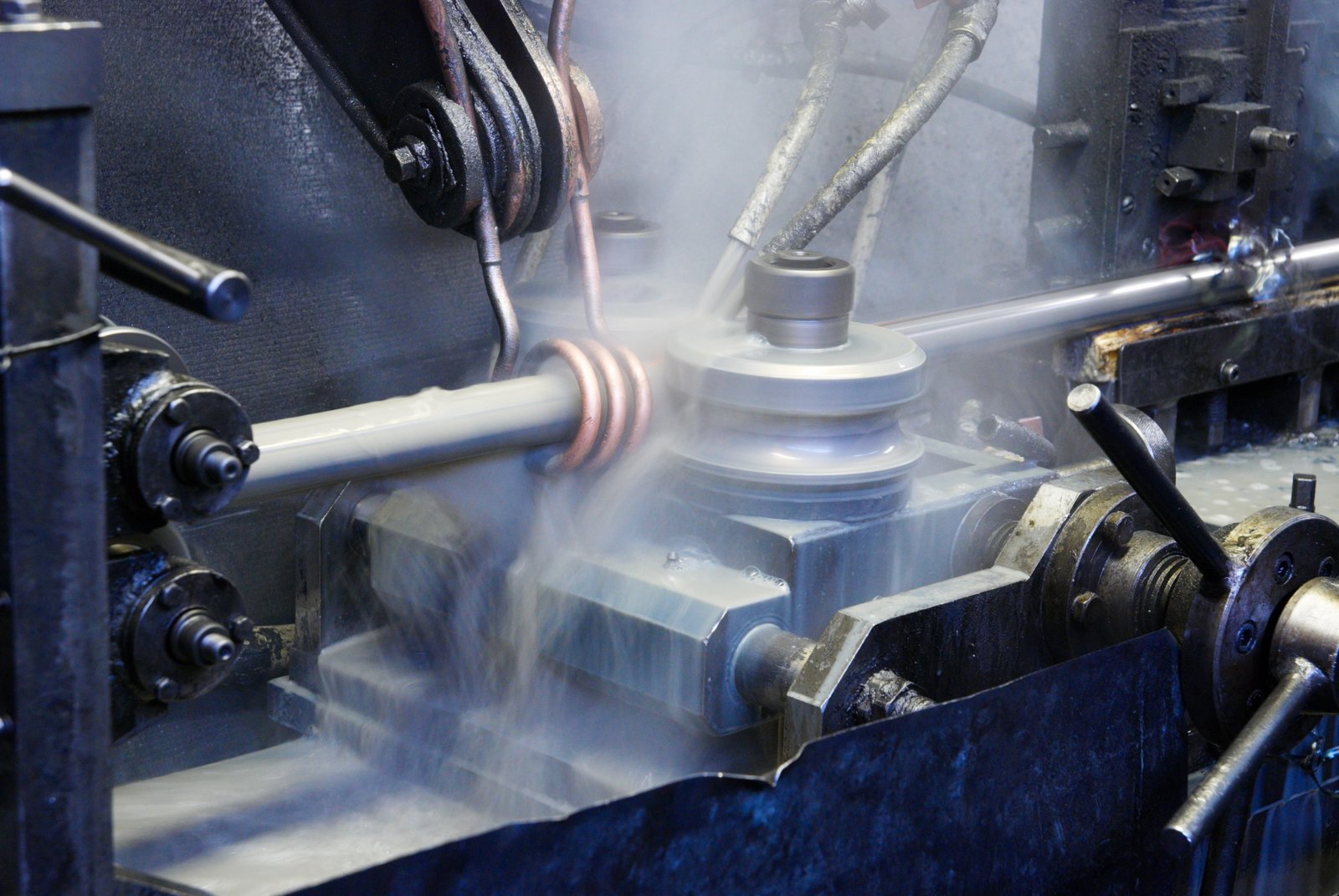
I recall a case involving one of our clients, an equipment integrator specializing in custom heat exchangers. They were building a unit for a Canadian facility that, due to the end-client's parent company, needed to follow European design principles. The integrator's engineers were accustomed to using the minimum tensile strength values from ASTM A312 in their calculations. When they reviewed the EN 10217-7 specifications for grade 1.4404, they noticed the minimum tensile strength requirement was slightly lower in a specific range compared to its ASTM TP316L counterpart, but the proof strength (yield strength) at the design temperature was more clearly defined. This forced a recalculation of the tube wall thickness and a revision of their design. It was a valuable lesson: the standards are not just names on a certificate; they are integrated systems of data that must be respected in their entirety to ensure engineering integrity.
Tensile and Yield Strength: A Tale of Two Philosophies
The most critical mechanical properties for any pressure-retaining component are its yield strength (the stress at which it begins to deform permanently) and its tensile strength (the maximum stress it can withstand before fracturing). While grades like TP304 (ASTM) and 1.4301 (EN) are often considered interchangeable due to their near-identical chemical composition, their specified minimum strength values can differ. For example, for a standard 2-inch welded pipe, ASTM A312 TP304 requires a minimum tensile strength of 515 MPa (75 ksi) and a minimum yield strength of 205 MPa (30 ksi).
In contrast, for the equivalent grade 1.4301 under EN 10217-7, the minimum tensile strength is typically specified at 500-700 MPa, and the minimum 0.2% proof strength (equivalent to yield strength) is 190 MPa at room temperature. The European standard often goes a step further by providing guaranteed minimum proof strength values at elevated temperatures (e.g., 128 MPa at 300°C for 1.4301). This is invaluable for designers of pressure vessels and boilers, as it removes the guesswork involved in derating material strength at high temperatures. The ASME code provides its own temperature-based stress tables, but the EN approach integrates this data directly into the material standard itself.
This difference reflects a philosophical divergence. The ASTM/ASME system provides a baseline at ambient temperature and relies on the overarching design code (like ASME B31.3) to provide the complex formulas and factors for various conditions. The EN system, driven by the PED, aims to build more of this critical performance data directly into the harmonized material standard. For a manufacturer building equipment for diverse global markets, this means their engineering team must be fluent in both systems to ensure every product is compliant and safely designed according to the rules of its destination market.
Elongation and Ductility: Implications for Fabrication
Elongation, expressed as a percentage, measures a material's ductility—its ability to be stretched or bent without breaking. This property is paramount during fabrication processes like bending, flanging, or expanding tube ends. A pipe with higher elongation can undergo more severe deformation before failing, which is crucial for creating complex piping geometries. Both ASTM A312 and EN 10217-7 specify minimum elongation values, but how they are measured and what they require can differ.
ASTM A312 typically specifies a minimum elongation of 35% on a 2-inch (or 50mm) gauge length. EN 10217-7, on the other hand, often specifies two values, one for the longitudinal direction and one for the transverse direction, and the requirement can vary. For grade 1.4404 (TP316L), the minimum longitudinal elongation is 40%, while the transverse value is 30%. This distinction is important because the manufacturing process for welded pipe can result in different properties along and across the weld seam.
Consider a construction contractor fabricating a complex piping system for a pharmaceutical plant, which requires numerous tight-radius bends. A pipe with superior and more consistent elongation properties will be easier to work with, reducing the risk of cracking during the bending process and minimizing material waste. I once spoke with a fabrication shop manager who had to reject a batch of pipes because they consistently failed during 90-degree bending. The root cause was traced back to material that barely met the minimum elongation requirement; while technically compliant, it lacked the practical ductility needed for their specific process. This is why at MFY, we emphasize understanding not just the minimum specification1 but the typical performance of our products, ensuring our clients receive materials that are not just compliant but also highly workable.
Hardness and Toughness Considerations
Hardness is a measure of a material's resistance to localized plastic deformation, such as a scratch or indentation. While not always a primary design parameter for pipes, it is an important indicator of both wear resistance and the material's overall condition after manufacturing and heat treatment. An unusually high hardness value in an austenitic stainless steel, for example, could indicate improper heat treatment or excessive cold working, which might in turn increase its susceptibility to certain types of corrosion, like stress corrosion cracking (SCC).
Neither ASTM A312 nor EN 10217-7 typically impose mandatory hardness limits for standard austenitic grades unless specified by the purchaser as a supplementary requirement. However, the acceptable ranges can be found in related standards and are generally understood by manufacturers. For instance, a Rockwell B hardness of 90-95 is typical for annealed TP304/TP316. The key is consistency. A batch of pipes with widely varying hardness values suggests inconsistent manufacturing processes, which should be a red flag for any buyer.
Toughness, the ability of a material to absorb energy and deform without fracturing (especially at low temperatures), is another critical consideration, particularly for applications in colder climates like Russia or for cryogenic processing. While standard tensile tests provide some insight, specific impact tests (like the Charpy V-notch test) are required to quantify toughness. These are not standard requirements in either A312 or EN 10217-7 for austenitic steels (which are inherently tough at low temperatures) but can be specified as a supplementary requirement (S2 in ASTM) if the application demands it. For our clients in the LNG industry, specifying supplementary toughness testing2 is standard practice to ensure the material's integrity at cryogenic temperatures.
EN standards specify proof strength at temperatureTrue
EN 10217-7 provides guaranteed minimum proof strength values at elevated temperatures, unlike ASTM which relies on separate design codes.
ASTM and EN elongation tests are identicalFalse
EN standards often specify separate longitudinal/transverse elongation values, while ASTM typically uses a single gauge length measurement.
What are the implications of these differences for various applications?
You've chosen a stainless steel pipe that meets the chemical and mechanical needs, but is it the right standard for your specific application? Selecting a pipe based on material properties alone, without considering the regulatory and operational context, can lead to project rejection, operational hazards, or premature failure.
The choice between ASTM A312 and EN 10217 standards has profound implications. It dictates regulatory compliance (ASME vs. PED), determines suitability for specific pressures and temperatures, affects interchangeability with other components, and ultimately impacts the project's safety, budget, and timeline.
The "best" standard does not exist in a vacuum; it is defined by the demands of the application. For a high-pressure steam line in a power plant built to ASME codes, ASTM A312 is the natural choice. For a hydraulic system on a machine destined for sale in Germany, EN 10217-7 is legally required. Beyond these clear-cut cases, the nuances become critical. In the food and beverage industry, while both standards might be technically acceptable, one may have more stringent or relevant specifications regarding surface finish and cleanability. In structural applications, the focus might shift to dimensional tolerances and aesthetic consistency. As we explore specific industry scenarios, it will become clear that aligning the standard with the application's unique ecosystem—from legal frameworks to physical stresses—is the key to a successful outcome.
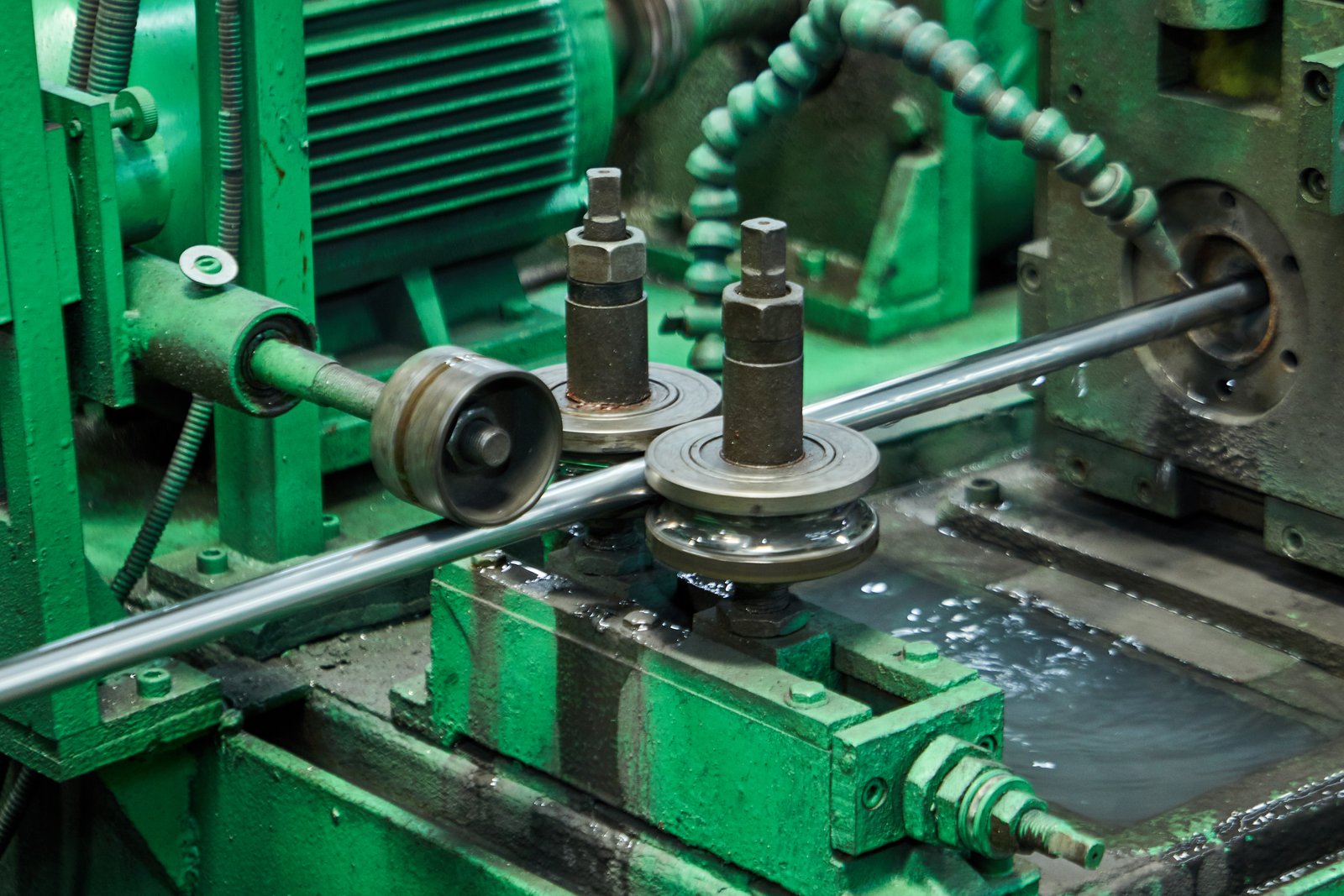
Let's look at a practical example from our experience at MFY in standard selection3. We supplied stainless steel tubes to a multinational manufacturer of industrial compressors. Their engineering was done in the USA (favoring ASTM), but they had a large assembly plant in Poland (operating under EU regulations). For years, they struggled with a dual-sourcing strategy, trying to match ASTM-specified materials with the requirements of the PED for their European-assembled units. This created constant friction in their supply chain. We worked with them to analyze their portfolio and recommended a streamlined approach: for units destined for ASME markets, they would strictly use ASTM A312; for CE-marked units, they would use EN 10217-7. We helped them manage the inventory for both, ensuring clear segregation and documentation. This simple strategic shift, based on understanding the application's end-market, eliminated compliance risks and simplified their procurement process significantly.
Pressure Applications: The ASME vs. PED Divide
This is the most critical and least flexible area of application. The choice of standard is not a preference but a mandate dictated by the governing design code and legal jurisdiction. In North America, the Middle East, and many parts of Asia, process piping is designed according to the ASME B31 series of codes. ASME B31.3 for Process Piping, for instance, explicitly lists ASTM A312 as an approved material specification. The allowable stresses, design formulas, and welding procedures are all built around the data and philosophy of ASTM standards. Using an EN-specified pipe in an ASME system would require a complex and costly recertification process, if it's even permitted by the client.
Conversely, any pressure-bearing equipment or system intended for sale and operation within the European Union must comply with the Pressure Equipment Directive (PED 2014/68/EU). The most straightforward way to demonstrate compliance is by using materials from harmonized EN standards, like EN 10217-7. The CE mark on a final product is a declaration that it meets all relevant directives, and using non-EN materials creates a significant burden of proof on the manufacturer to demonstrate an equivalent level of safety.
I recall a case with an engineering contractor in India building modular skids for a global chemical company. One skid was destined for a plant in Texas, the other for a plant in the Netherlands. Although the skids were functionally identical, the bill of materials was completely different. The Texas skid required ASTM A312 pipes with MTRs detailing compliance with ASME standards. The Netherlands skid required EN 10217-7 tubes with EN 10204 3.1 certificates to satisfy the PED. It’s a perfect illustration of how geography and regulation, not just engineering function, dictate material selection.
Structural and Architectural Applications
When stainless steel pipe is used for structural or architectural purposes—such as railings, building facades, or support frames—the stringent requirements of pressure directives do not apply. This provides greater flexibility in choosing between ASTM and EN standards. The decision here often shifts from regulatory compliance to other factors like aesthetic finish, dimensional tolerances, and cost-effectiveness. Both standards offer the common austenitic grades that provide excellent corrosion resistance and a clean look, which are desirable in architectural design.
However, there can still be subtle differences. For example, standards may have slightly different tolerances on straightness or outside diameter, which could be important for applications requiring precise alignment of many components. Furthermore, the specification for surface finish might be described differently. An architect might specify a "No. 4 finish," which is common terminology in the ASTM system. An equivalent finish exists under EN standards (e.g., a 2K finish), but a supplier needs to understand how to translate these requirements.
I worked with a construction contractor on a large public transit station in Southeast Asia where the design specified extensive use of stainless steel tubing for canopies and handrails. The original design was from a European firm and referenced EN standards. However, due to local availability and familiarity, the contractor preferred to source ASTM-compliant material. In this case, because it was a non-pressure application, the switch was possible. Our role at MFY was to provide a detailed comparison of the relevant EN and ASTM grades, demonstrating that the chemical composition, mechanical properties, and, crucially, the dimensional tolerances of our ASTM A312 pipes were a perfect match for the project's structural and aesthetic requirements, satisfying both the contractor and the original designer.
Food & Beverage and Pharmaceutical Industries
In hygienic applications, the primary concern is preventing microbial contamination. The material must be non-reactive, corrosion-resistant, and, most importantly, have a smooth, cleanable surface. Both ASTM A312 and EN 10217-7 can be used as a basis for procuring pipes for these industries, but they are often supplemented by more specific standards like ASTM A270 for sanitary tubing or various European hygiene standards. The key properties of interest are the internal surface roughness (Ra value) and the absence of surface defects like pits or crevices where bacteria can harbor.
The choice between the base standards can still matter. For example, a project might specify a particular heat treatment or require that the welded pipe be heavily cold-worked (as allowed in A312) to achieve a superior internal finish. The EN standard's structured approach, with its different test categories, might also be appealing to a quality manager who wants to specify a higher level of non-destructive testing on the weld seam to ensure its integrity, even if the system is not under high pressure.
We have a long-standing client that manufactures dairy processing equipment. They produce identical systems for the US and German markets. For their FDA-regulated U.S. products, they procure pipe specified to ASTM A270 (which often uses A312 as a base). For their German products, they must meet the requirements of the European Hygienic Engineering & Design Group (EHEDG), and they typically specify EN 10217-7 tubes with an additional specification for a very low surface roughness. While the base steel (e.g., 1.4404/316L) is the same, the bundle of specifications, testing, and certifications around it is tailored to the specific regulatory landscape of the final application.
ASTM A312 is required for ASME systemsTrue
ASME B31.3 explicitly lists ASTM A312 as an approved material specification for process piping in North America and other regions following ASME codes.
EN 10217-7 can freely replace ASTM A312False
Using EN-specified pipe in an ASME system would require complex recertification as the standards have different testing philosophies and compliance requirements.
How should buyers assess which standard to choose for their project?
Faced with two robust standards, how do you make the final call without second-guessing your decision? The complexity of technical data, regulatory requirements, and commercial factors can be paralyzing, leading to indecision or, worse, a choice based on incomplete information that could jeopardize your project.
Buyers should first establish the project's non-negotiable regulatory framework and governing codes. Next, meticulously analyze the technical service requirements (pressure, temperature, media). Finally, evaluate commercial and supply chain factors like cost, supplier availability, and lead times to make a holistic, risk-informed decision.
This assessment is not a simple linear process but a multi-faceted evaluation. It begins with the question, "What are the rules I must follow?" This is about legal and contractual obligations. Only after that can you move to the engineering question, "What is the best material for the job?" And finally, you address the commercial reality: "What is the most viable way to source this material?" By breaking the decision down into these three distinct but interconnected stages—Regulation, Engineering, and Commerce4—you can move from a state of confusion to one of structured clarity. This systematic approach transforms a daunting task into a manageable process, ensuring all critical bases are covered before a purchase order is ever issued.
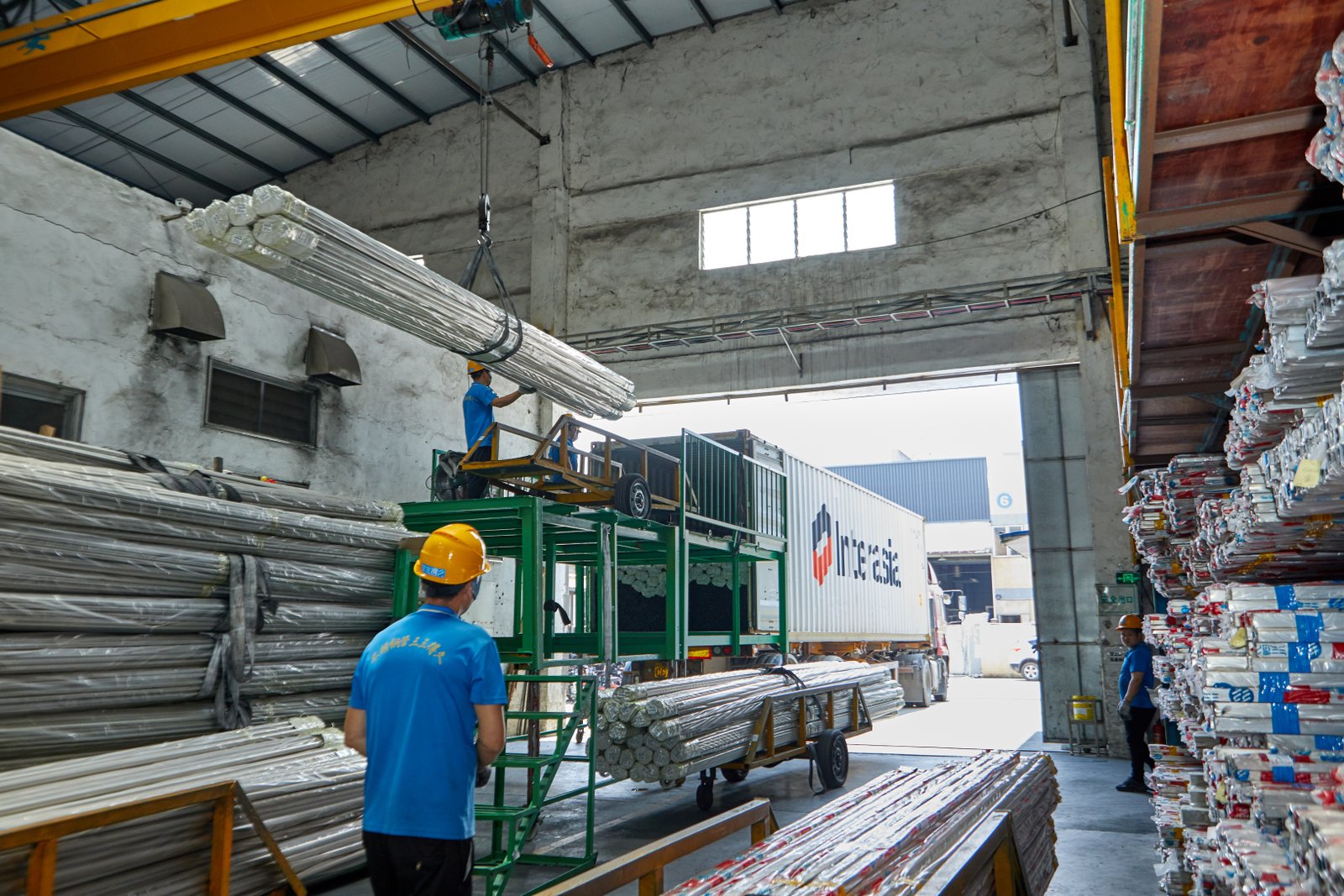
This three-stage assessment became my standard advice after a difficult experience with a new client, an engineering and construction contractor working on their first international project. They were building a water desalination plant in a country that historically used British standards but was now seeing more investment from American firms. The client was caught in the middle, receiving conflicting advice. They were leaning toward ASTM A3125 due to a slightly lower material cost. I urged them to pause and apply the three-stage approach. First, we confirmed the project's contractual documents and found that while the engineering was influenced by U.S. practices, the ultimate safety case had to be approved by a body that recognized EN standards. This single finding (Stage 1) made the choice clear, overriding the initial cost consideration. They chose EN 10217-7, and while the initial pipe cost was marginally higher, they avoided what would have been months of delays and costly battles over regulatory approval.
Step 1: Deconstruct Project Requirements and Governing Codes
This is the foundational, non-negotiable step. Before you even look at a data sheet, you must become a detective and investigate the project's legal and contractual landscape. The single most important question is: What is the geographic location of the project, and what are the legally binding codes and standards for that region? For pressure applications, this immediately points you toward either the ASME code family or the European PED. There is typically no room for compromise here. A mismatch results in non-compliance, which can mean the equipment is illegal to operate.
Start by reviewing the main project contract, the engineering specifications, and the purchase order requirements. Look for explicit references to standards like ASME B31.3, PED 2014/68/EU, or other national standards. Don't be afraid to ask for clarification. As a supplier, I would much rather have a client ask me to help them interpret a specification than receive a purchase order for the wrong material. It saves time, money, and reputation for everyone involved.
In my experience, this is where most costly errors are prevented. I once had a new buyer from a manufacturing company send an RFQ for a large quantity of ASTM A312 pipe. It seemed straightforward. However, based on their company name, I knew they had a strong presence in Europe. I took the initiative to call and ask if this material was for a CE-marked product. There was a long pause on the phone. It turned out the RFQ was prepared by a junior engineer based on an old project template. The new project was indeed for their European factory and absolutely required EN 10217-7. That one phone call saved them from ordering thousands of meters of unusable pipe.
Step 2: Analyze Technical and Performance Needs
Once the regulatory framework is established, you can move on to the engineering analysis. Here, you match the material's properties to the physical and chemical demands of the service environment. This involves a detailed review of the process conditions and asking a series of critical technical questions. A simple checklist can help guide this process, but the analysis should be thorough.
First, consider the operational pressure and temperature. Are you dealing with low-pressure fluid, or high-pressure steam? Will the pipe operate at ambient temperature, high temperatures, or in cryogenic conditions? As discussed, EN standards often provide explicit proof strength values at elevated temperatures, which can simplify design for high-temperature service. Next, analyze the media flowing through the pipe. Is it corrosive? Is it a hygienic product? This will guide your grade selection (e.g., 304L vs. 316L vs. a duplex grade) and any special requirements for surface finish or corrosion testing.
Finally, think about the fabrication and installation process. Will the pipe undergo significant bending or forming? If so, paying close attention to the specified elongation values is critical. Will there be extensive welding? Ensuring you have a grade with controlled carbon content (like the "L" grades) is vital to prevent post-weld corrosion. This stage is about ensuring the pipe will not just be compliant, but will perform reliably and safely for its entire design life. It’s the dialogue between the process engineer, the materials engineer, and the procurement manager.
Step 3: Evaluate Commercial and Supply Chain Factors
With the regulatory and technical requirements defined, the final step is to assess the commercial and logistical realities. This is where procurement strategy comes to the forefront. The key factors to consider are cost, availability, and supplier capability. While EN- and ASTM-compliant pipes made from the same grade of steel will have a similar base material cost, the final price can be affected by the different testing and certification requirements. The extensive documentation required for EN 10204 3.1 certification, for example, can add a small premium compared to a standard ASTM MTC.
Availability and lead times are hugely important. Depending on your region, one standard may be more commonly stocked by local distributors than the other. Sourcing the less common standard might involve longer lead times and higher shipping costs. This is where a supplier with a robust global network like MFY provides a distinct advantage. We manufacture and stock pipes to both standards, and our integrated supply chain allows us to provide competitive lead times for clients in our key markets across Asia, the Middle East, and Russia, regardless of the standard they require.
Finally, evaluate your supplier's expertise. Can they do more than just provide a price? Do they understand the nuances between the standards? Can they review your specifications and spot potential conflicts? A knowledgeable supplier acts as a risk mitigation partner. They can provide advice on market conditions, help you understand the certification documents, and ensure that what you order is exactly what your project needs. Choosing a supplier is not just a transaction; it's an investment in a successful project outcome.
Regulatory framework is non-negotiableTrue
The geographic location and legally binding codes must be identified first, as they dictate the permissible standards.
Cost is the primary deciding factorFalse
While cost is important, regulatory compliance and technical suitability must be prioritized over initial material cost.
What recommendations can help buyers make informed purchasing decisions?
You've done the research, but the final moment of placing a purchase order still feels daunting. How can you be absolutely certain that the product arriving at your facility will be fully compliant and fit for purpose? The fear of a documentation error or subtle quality issue causing delays is very real.
Always insist on a comprehensive Mill Test Certificate (MTC) that explicitly states compliance with the full standard designation. Partner with suppliers who demonstrate deep technical expertise in both ASTM and EN standards and who can act as consultants, not just order-takers.
The ultimate goal is to eliminate ambiguity and create a transparent, traceable procurement process. This is achieved through two key actions: demanding rigorous, standard-compliant documentation for every item you purchase, and cultivating relationships with suppliers who are willing to invest their expertise in your success. An MTC is your proof of compliance; a knowledgeable supplier is your guide to ensuring you've requested the right compliance in the first place. These two elements work together to transform a potentially risky purchase into a confident, value-driven investment, safeguarding your project against the common pitfalls of international sourcing.
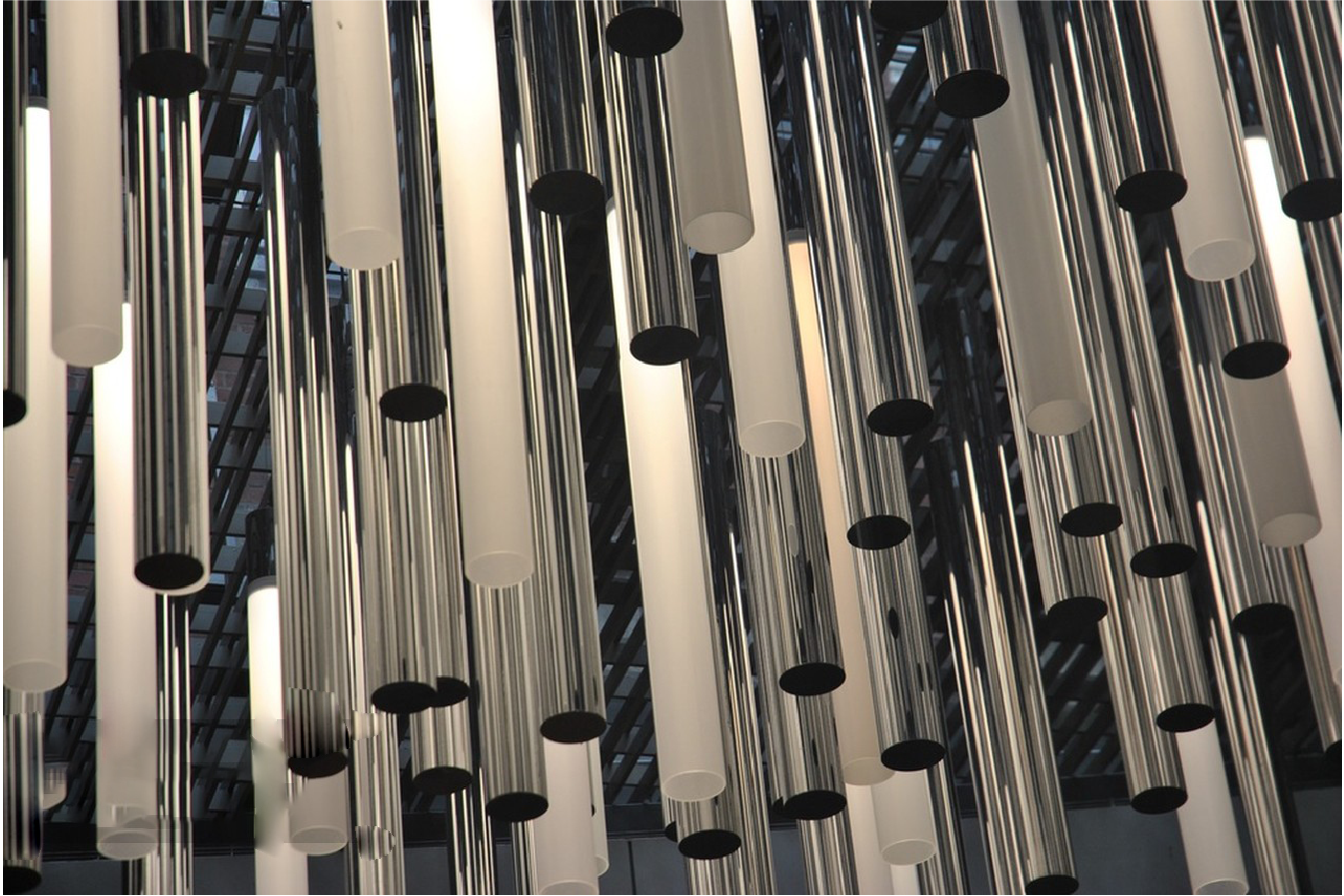
This philosophy is at the core of how we operate at MFY. A few years ago, a construction contractor for a major infrastructure project in Southeast Asia approached us. They needed a large volume of stainless steel pipe and had offers from several suppliers. One offer was significantly cheaper, but when we advised the client to ask for a sample MTC, the document was vague, referencing only the steel grade but not the full ASTM A312 standard or the results of mandatory tests like hydrostatic testing. We explained that this certificate would be rejected by any serious project inspector. By providing them with a sample of our own detailed MTC, which clearly showed every required test result against the A312 specification, we demonstrated the difference between "cheap pipe" and "compliant pipe." They chose to partner with us, and during the project, our clear documentation passed every quality audit without issue. This is the tangible value of diligence.
The Power of the Mill Test Certificate (MTC)
The Mill Test Certificate (MTC), also known as a Mill Test Report (MTR) or an inspection certificate, is the single most important document you will receive with your pipe order. It is the material's birth certificate, providing a complete and traceable record of its properties, directly from the manufacturer. It is your ultimate proof that the material meets the standard you specified. However, not all MTCs are created equal. A robust and trustworthy MTC must be meticulously reviewed.
For an order under ASTM A312, the MTC should clearly state "ASTM A312" and the specific grade (e.g., TP316L). It must include a detailed chemical analysis, showing the percentage of each element and confirming it falls within the required range. It must also list the results of the mechanical tests: tensile strength, yield strength, and elongation, again confirming they meet the minimum requirements. ly, it should confirm that other required tests, such as the hydrostatic test, have been successfully completed.
For an order under EN 10217-7 intended for a pressure application in the EU, you should expect an "Inspection Certificate 3.1" according to the EN 10204 standard. This is more than just a report; it's a formal declaration of compliance issued by the manufacturer’s authorized inspection representative who is independent of the production department. It contains similar information to the ASTM MTC (chemical analysis, mechanical properties) but is structured to meet the specific requirements of the PED. Verifying that you have the correct type of certificate (e.g., 3.1 vs. 2.2) is just as important as verifying the technical data within it.
Leveraging Supplier Expertise: Beyond the Transaction
Your relationship with your supplier should not be purely transactional. In a global market with complex standards, a truly valuable supplier acts as a partner and a technical resource. Their expertise can be one of your most effective risk management tools. An experienced supplier can help you navigate the very challenges this article has outlined, providing clarity where there is confusion.
When evaluating suppliers, ask them questions that test their knowledge. Ask them to explain the difference between the certification requirements of ASTM and EN standards. Present them with a hypothetical scenario: "If I'm building a PED-compliant heat exchanger, what documentation do I need?" A knowledgeable supplier will be able to answer confidently and accurately. They should be able to review your technical specifications and identify potential conflicts or ambiguities before they become problems.
At MFY, we train our sales and technical support teams to be consultants. Our mission is to help clients build resilient supply chains, and that begins with making informed procurement decisions. We see it as our responsibility to ensure that when a client like an equipment integrator or a construction contractor orders from us, they are getting a product that is not only high-quality but is also the correct product for their specific application and regulatory environment. This proactive, partnership-based approach builds trust and prevents the costly errors that can arise from a simple lack of information.
Considering Dual-Certified Materials
In the marketplace, you will often find pipes that are advertised as "dual-certified" to both ASTM and EN standards. For distributors and large manufacturers who serve diverse markets, these products can seem like an ideal solution, offering flexibility and simplifying inventory management. A pipe that can be sold to a project in Texas or a project in Germany seems to offer the best of both worlds. However, buyers must approach this with a healthy dose of professional skepticism and diligence.
The key to dual certification is ensuring the pipe truly meets the strictest requirements of both standards. It's not enough for the chemical and mechanical properties to overlap. The pipe must have undergone all the mandatory tests and be accompanied by documentation that is compliant with both systems. For example, did the pipe undergo the specific NDT regimen required by EN 10217-7's Test Category 2, even if it wasn't required by the base ASTM A312 standard? Can the supplier provide both a standard MTC acceptable in the US and a formal EN 10204 3.1 certificate for Europe?
Dual certification is a smart choice when the documentation is robust and the traceability is impeccable. It can be particularly useful for global distributors who need to serve a wide range of customer requests from a single stock. However, for an end-user with a specific project, it is often safer and clearer to specify a single standard. This eliminates any ambiguity and ensures a direct and unbroken chain of compliance from the mill to the final installation.
MTC proves complianceTrue
A proper Mill Test Certificate provides verifiable evidence that materials meet specified standards.
Cheaper is always betterFalse
Lower cost often indicates compromised quality or missing documentation that could cause project failures.
Conclusion
Choosing between ASTM A312 and EN 10217 is not about identifying a superior standard, but about selecting the appropriate one. Your decision must be driven by regulatory mandates, rigorous engineering analysis, and practical supply chain considerations to ensure project compliance, safety, and success.
-
Discover MFY's approach to ensuring high-quality and workable stainless steel products. ↩
-
Understand the importance of toughness testing in ensuring material integrity at cryogenic temperatures. ↩
-
Discover MFY's role in resolving multinational compliance challenges ↩
-
Gain clarity on structured decision-making in project management ↩
-
Understand ASTM A312's role and advantages in material selection ↩
Have Questions or Need More Information?
Get in touch with us for personalized assistance and expert advice.