Нестандартные решения для труб из нержавеющей стали для нестандартных спецификаций
Are your projects being hampered by the limitations of standard stainless steel pipe offerings? It's a common frustration when off-the-shelf products just don't meet the demanding, unique specifications of your critical applications, leading to potential compromises. MFY delivers custom solutions, perfectly tailored to your non-standard requirements.
Custom stainless steel pipe solutions are essential when standard sizes, grades, or configurations fail to meet specific project demands, particularly in industries with unique operational environments. These solutions require specialized manufacturing, material expertise, and rigorous quality assurance to ensure optimal performance, safety, and system integrity.
Finding the right piping solution for highly specific industrial needs can often feel like searching for a needle in a haystack. Standard options frequently fall short, leaving engineers and project managers in a bind. This is where the world of custom stainless steel pipe solutions1 opens up, offering a pathway to precision and optimal performance. At MFY, we've navigated these complex waters with numerous clients.
The demand for custom stainless steel pipes isn't just about unusual sizes; it's a deeper dive into material science, extreme operational pressures, corrosive environments, and intricate designs. Think about the petrochemical industry's need for alloys that withstand aggressive chemicals at high temperatures, or the pharmaceutical sector's requirement for impeccable surface finishes to ensure hygiene. Standard offerings often represent a compromise, whereas custom solutions are engineered for exactitude. At MFY, our fully integrated supply chain, from raw material trading to advanced manufacturing, allows us to address these specialized needs. We've seen firsthand how a bespoke pipe, designed collaboratively, can be the linchpin for a project's success, preventing costly retrofits or, worse, operational failures. This is where our commitment to innovation and client-centric solutions truly shines.
What prompted the need for custom stainless steel pipe solutions in certain industries?
Are you struggling with standard pipes that just don't cut it for your specialized industrial applications? This often leads to design compromises, inefficiencies, or even safety risks. Custom stainless steel pipe solutions, engineered by MFY, provide the tailored performance and reliability your unique operations demand.
The need for custom stainless steel pipe solutions in industries like petrochemical, pharmaceutical, marine, and aerospace is driven by extreme operating conditions, specific corrosive media, non-standard dimensional requirements for complex installations, unique material property needs, or stringent regulatory compliance unobtainable with standard products.
The call for custom stainless steel pipes often arises when conventional options present a roadblock to innovation or operational efficiency. In my experience at MFY, I've seen countless scenarios where "good enough" simply isn't. Consider a client in the food processing industry we worked with; they needed piping for a new ultra-high-temperature (UHT) processing line. Standard 304L or 316L pipes couldn't guarantee the necessary cyclical thermal stability and specific internal surface smoothness (Ra < 0.4µm) to prevent bacterial adhesion and ensure complete clean-in-place (CIP) effectiveness. Their project demanded a higher-grade alloy with a custom-polished internal finish, and specific bend radii to maintain flow integrity and prevent particle traps – specifications far outside the norm. This isn't an isolated case. Whether it's the intense pressures in subsea oil and gas extraction, the critical purity requirements in semiconductor manufacturing, or the unique geometric constraints in advanced architectural designs, the limitations of standard pipes become apparent. These industries push the boundaries of engineering, and their infrastructure must keep pace. That's where MFY steps in, translating these complex, non-standard needs into tangible, high-performance piping solutions.
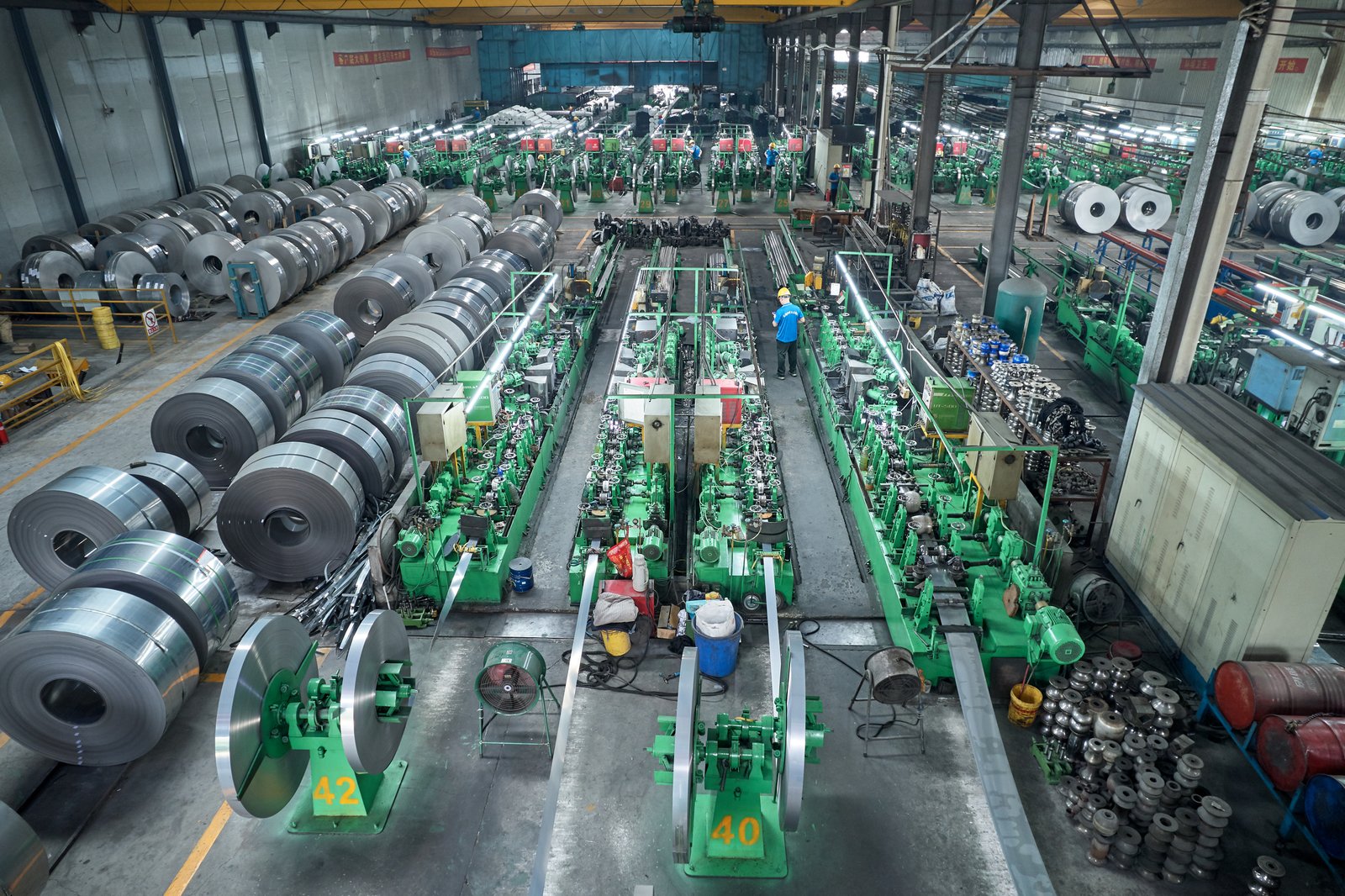
The drivers behind the demand for custom stainless steel pipes are as diverse as the industries themselves, but they often converge on the need for enhanced performance, safety, and longevity in environments where standard products would falter. At MFY, we've cultivated a deep understanding of these nuanced requirements, allowing us to anticipate challenges and engineer solutions that are not just custom-fit, but also optimized for the specific application. This often involves going beyond simple dimensional adjustments to delve into the very metallurgy and manufacturing processes.
The Intricacies of Material Selection for Specialized Applications
The selection of stainless steel is far more complex than choosing between common grades like 304 or 316 stainless steel2 when dealing with specialized industrial needs. Many applications involve extreme temperatures, highly corrosive substances, or immense mechanical stresses that necessitate alloys with very specific properties. For instance, in the chemical processing industry, a client might be handling hot sulfuric acid. While 316L offers good general corrosion resistance, it would be inadequate. Here, we'd explore options like 904L, super duplex stainless steels (like 2507), or even nickel alloys (e.g., Hastelloy C-276) depending on the concentration and temperature. Each of these materials offers a unique combination of chromium, nickel, molybdenum, nitrogen, and other elements, precisely balanced to combat specific corrosive attacks like pitting, crevice corrosion, or stress corrosion cracking. I recall a case with a marine engineering firm developing scrubbers for exhaust gas cleaning systems on large vessels. The environment inside these scrubbers is incredibly harsh, with high temperatures, acidic condensates, and seawater chlorides. Standard marine-grade 316L was simply not durable enough. Our team worked closely with them, analyzing the specific chemical cocktail and thermal cycling. We recommended a super duplex stainless steel, which provided the necessary pitting resistance (PREN > 40) and strength, significantly extending the service life of the scrubber components compared to their previous designs using lower-grade materials. According to a study by NACE International, the global cost of corrosion is estimated at $2.5 trillion annually. Selecting the correct, sometimes custom-formulated, alloy is a critical step in mitigating these costs and ensuring operational safety. Our role at MFY often involves educating clients on these advanced materials, moving beyond what's commonly available to what's truly optimal.
Dimensional and Geometric Complexities in Modern Engineering
Modern engineering projects, from compact skid-mounted processing units to sprawling architectural marvels, frequently demand pipe dimensions and geometries that defy standard manufacturing. It's not just about an unusual diameter or wall thickness; it can involve incredibly tight tolerances, specific ovality requirements, complex multi-plane bends, or unique end preparations for proprietary connection systems. For example, in the aerospace industry, hydraulic lines often snake through incredibly confined spaces, requiring precise, multiple bends in a single length of small-diameter, thin-wall, high-strength stainless steel tubing. Any deviation can lead to assembly issues or, worse, stress points and potential failure. I remember an architectural project for a public art installation that required large-diameter stainless steel tubes with a flawless mirror finish, bent into complex, non-standard radii to achieve the artist's vision. Standard bending techniques would have resulted in unacceptable distortion or surface imperfections. MFY invested in advanced CNC mandrel bending technology and specialized polishing processes to meet these exacting requirements. Standard pipes might come with a diameter tolerance of +/- 1%, but a high-precision instrumentation system might demand +/- 0.1mm. Similarly, wall thickness tolerance in standard pipes can be +/- 10% or even 12.5%, but for a critical heat exchanger application, a client might need +/- 3% to ensure consistent heat transfer and pressure containment. This level of precision requires not just advanced machinery but also meticulous process control and metrology, which are hallmarks of our custom solutions at MFY.
The table below illustrates some typical differences:
Характеристика | Standard Pipe | Custom Pipe Example (MFY) | Impact of Non-Conformance |
---|---|---|---|
Outer Diameter (OD) | +/- 0.75% to 1% | As low as +/- 0.05mm | Fit-up with fittings, sealing |
Wall Thickness | +/- 10% to 12.5% | As low as +/- 3% | Pressure rating, weldability, weight |
Straightness | 1:500 (e.g. 6mm/3m) | 1:1000 or better | Flow dynamics, installation ease |
Шероховатость поверхности (Ra) | Standard Mill | < 0.4µm (hygienic) | Cleanability, corrosion, friction |
Length Tolerance | -0 / +6mm | +/- 1mm or tighter | Assembly precision, waste reduction |
Regulatory Compliance and Certification Demands
Many industries operate under stringent regulatory frameworks and require extensive certification for all components, including piping. The nuclear, pharmaceutical, food and beverage, and offshore oil and gas sectors are prime examples. Compliance isn't just about meeting basic ASTM or EN standards; it often involves additional testing, specific material traceability requirements (e.g., EN 10204 3.1 or 3.2 certs), and adherence to industry-specific codes like ASME BPE (Bioprocessing Equipment) or Norsok standards for offshore applications. For instance, a pharmaceutical client we served required stainless steel tubing for a WFI (Water for Injection) system. This mandated not only a specific low-sulfur 316L grade and an exceptionally smooth internal surface finish (Ra < 0.5 µm, electropolished) but also full material traceability, ferrite content limitations, and documentation for every heat and lot, including detailed NDT reports. Standard pipes rarely come with this level of comprehensive certification. MFY’s robust Quality Management System, certified to ISO 9001, is designed to handle these complex documentation and certification needs. We ensure that all custom orders meet or exceed the specified international and industry-specific standards, providing clients with the peace of mind that comes from fully compliant and certified products. This commitment extends to understanding the specific import regulations and certification requirements of our diverse export markets, such as PED (Pressure Equipment Directive) for Europe or specific GOST requirements for Russia, ensuring smooth project execution for our global clientele.
Custom pipes handle extreme conditionsПравда
Custom stainless steel pipes are engineered to withstand unique challenges like high temperatures, corrosive media, and intense pressures that standard pipes cannot handle.
316L suits all corrosive environmentsЛожь
While 316L is versatile, specialized applications like hot sulfuric acid handling require higher-grade alloys like 904L or super duplex stainless steels for adequate corrosion resistance.
How did one specific case illustrate the challenges of non-standard pipe specifications?
Ever faced a project where standard pipes were simply not an option, creating a cascade of design and sourcing headaches? This was the reality for one of our clients, threatening project timelines and budgets. MFY's expertise in custom solutions turned these critical challenges into a success story.
A case involving a specialty chemical plant required custom-dimensioned, high-molybdenum austenitic stainless steel pipes for a reactor loop operating under severe corrosive conditions and high pressures. Challenges included sourcing the niche alloy, achieving exceptionally tight tolerances, and complex welding procedures.
I vividly recall a project with "ChemSynth Innovations," a client in India building a pilot plant for a new agricultural chemical. Their process involved highly corrosive organic acids and catalysts at elevated temperatures and pressures—around 150°C and 40 bar. The initial design, based on standard 316L, proved inadequate during preliminary material testing, showing unacceptable corrosion rates. Their R&D team identified a need for a specialized austenitic stainless steel with higher molybdenum and nitrogen content (akin to a modified UNS S31254 or "6Mo") but in non-standard pipe sizes – specifically, a 3.5-inch nominal bore with a precise 5.0mm wall thickness. This specific combination wasn't available from any standard stock globally3. The project's success hinged on sourcing or manufacturing these pipes. ChemSynth faced immense pressure; their funding was tied to demonstrating process viability within a tight timeframe. The challenges were multi-faceted: sourcing the raw material for this niche alloy in small quantities, forming it to non-standard dimensions with tight tolerances, and ensuring the weldability and corrosion resistance of the final product. This case perfectly illustrates the intersection of material science, manufacturing precision, and supply chain agility required to tackle non-standard specifications.
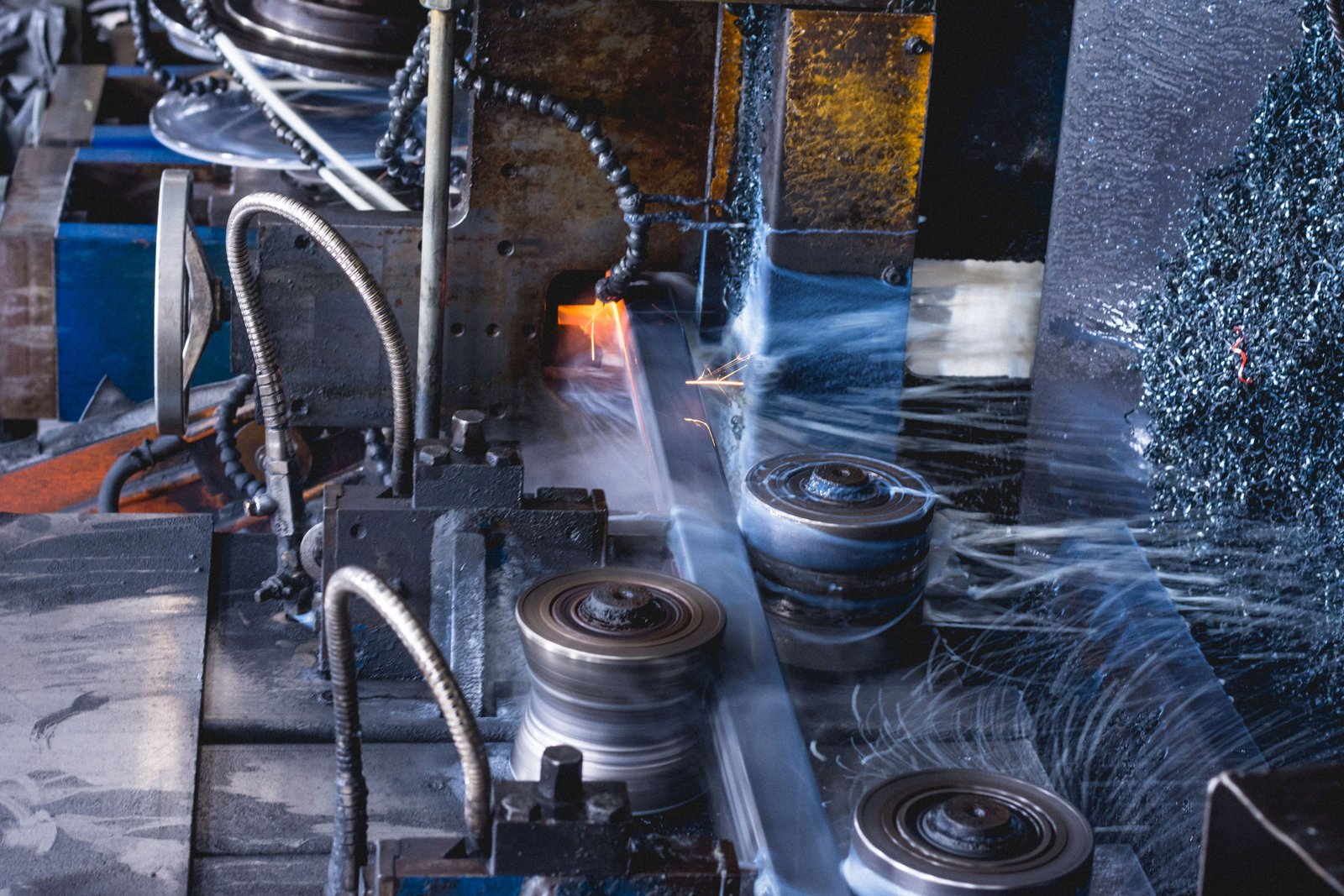
The ChemSynth Innovations project became a benchmark for us at MFY in demonstrating our capabilities to handle truly unique and demanding non-standard pipe specifications. The challenges went beyond a simple dimensional variation; they touched upon fundamental aspects of metallurgy, manufacturing process design, and quality assurance under pressure. It required a deep, collaborative engagement with the client to fully understand not just the 'what' but the 'why' behind each specification.
The Quest for an Elusive Alloy and Unconventional Dimensions
ChemSynth's primary challenge was the material itself. Their process required an austenitic stainless steel with a Pitting Resistance Equivalent Number (PREN) exceeding 40, coupled with good formability and weldability. Standard 6Mo alloys like UNS S31254 were close, but their process chemistry had a specific sensitivity that their internal research suggested could be mitigated by a slight adjustment in chromium and nitrogen content, making it a truly custom melt. Furthermore, the 3.5-inch (88.9mm OD) nominal bore with a 5.0mm wall thickness was a dimensional ghost. Standard schedules for this OD might offer a 3.05mm (Schedule 5S), 3.76mm (Schedule 10S), or 5.49mm (Schedule 40S) wall, but nothing at exactly 5.0mm. This precision was critical for their reactor loop's calculated flow dynamics and pressure containment, as well as for fitting with other custom-machined components. The initial hurdle was finding a mill willing to produce a custom heat of this modified 6Mo alloy for the relatively small quantity needed for a pilot plant – roughly 200 meters. Most large mills have high Minimum Order Quantities (MOQs) for custom melts, often running into several tons. Leveraging MFY's integrated supply chain and our long-standing relationships4 with specialized alloy producers, we were able to negotiate the production of the custom billets. This involved our metallurgical team liaising directly with the mill's experts to define the precise chemical composition and ensure the desired properties. This upstream capability is a core strength of MFY and was pivotal in even getting the project off the ground for ChemSynth.
Manufacturing Hurdles: Precision Forming and Welding
Once the custom raw material was secured, the manufacturing challenges began. The high molybdenum and nitrogen content of the chosen alloy made it significantly harder and less ductile than standard austenitic grades like 316L. This meant that our standard tube forming rolls and drawing dies would experience excessive wear and might not achieve the required dimensional accuracy. We had to design and manufacture new, hardened tool steel rolls specifically for this project. Achieving the precise 5.0mm wall thickness consistently along the entire length of each pipe, while maintaining strict ovality and concentricity tolerances (e.g., ovality within 1% of OD, eccentricity within +/-5% of nominal wall), required meticulous setup of the tube mill and continuous laser-based dimensional monitoring during production. The alloy's tendency to work-harden rapidly also meant that welding procedures had to be carefully developed. ChemSynth's engineers were rightly concerned about maintaining corrosion resistance in the heat-affected zone (HAZ) of the welds. Standard welding consumables for 6Mo alloys were a starting point, but we conducted numerous weld procedure qualification tests (WPQR) using different filler materials and shielding gas compositions. We performed intergranular corrosion tests (ASTM A262 Practice E) and pitting corrosion tests (ASTM G48 Practice A) on weld samples to optimize the параметры5. Our R&D team found that a specific pulsed TIG welding technique with a nitrogen-rich shielding gas significantly improved the HAZ's pitting resistance, achieving a critical pitting temperature (CPT) within 5°C of the parent material, a result that gave ChemSynth great confidence. This level of weld engineering is critical for such demanding applications.
Logistical Complexities and Rigorous Testing Protocols
Beyond the material and manufacturing, the ChemSynth project demanded an exceptionally high level of quality assurance and documentation. Given the critical nature of the pilot plant and the corrosive media, ChemSynth required 100% Positive Material Identification (PMI) on all raw materials and finished pipes, 100% ultrasonic testing (UT) for weld integrity (for welded pipes, though these were seamless after a drawing process), and 100% dye penetrant testing (DPT) on all surfaces. They also specified hydrostatic testing at 2.5 times the design pressure (100 bar), which is significantly higher than the standard 1.5 times. Each pipe had to be individually stenciled with a unique heat number, pipe number, and all relevant specifications. The documentation package for each shipment was extensive, including mill certificates for the custom melt, detailed MTRs for the finished pipes (showing chemical analysis, mechanical properties, corrosion test results), NDT reports, dimensional inspection reports, and hydro-test certificates. The pipes, though robust, also required specialized packaging for the sea freight to India to prevent any surface contamination or damage that could compromise their corrosion resistance. We used individually wrapped pipes in custom-built wooden crates with ample cushioning. I personally oversaw the final inspection and documentation review with our QA manager before dispatch, knowing how critical this was for ChemSynth's project milestones. The meticulousness paid off; the material passed all incoming inspections at their site without issue, allowing them to proceed with plant assembly on schedule. This case highlighted that for non-standard specs, the service and QA aspects are just as crucial as the physical product.
Custom pipes required precise 5.0mm wall thicknessПравда
The project demanded exact 5.0mm walls for flow dynamics and pressure containment, unlike standard pipe schedules.
Standard 316L stainless steel was sufficientЛожь
Initial tests showed 316L had unacceptable corrosion rates, requiring a custom 6Mo alloy with higher molybdenum content.
What innovative solutions were implemented to meet these non-standard requirements?
Are you facing "impossible" specifications that stall your critical projects? This can lead to frustration and costly delays. At MFY, our innovative spirit and engineering prowess turn these challenges into custom-fit triumphs, ensuring your project’s success and operational excellence.
Innovative solutions for the ChemSynth case included collaborative custom alloy formulation with a partner mill, development of bespoke forming tools and advanced welding techniques using nitrogen-rich shielding gas, and implementation of enhanced, multi-stage NDT protocols to ensure material integrity and precise specifications.
When ChemSynth Innovations approached us with their unique requirements for the modified 6Mo alloy pipes6, it was clear that standard off-the-shelf solutions and even conventional custom manufacturing approaches wouldn't suffice. Our engineering and production teams at MFY viewed this as an opportunity to push our innovative boundaries. It wasn't merely about fabricating a pipe to unusual dimensions; it was about a holistic re-evaluation of our processes, from sourcing highly specialized raw materials to pioneering new manufacturing techniques and implementing ultra-rigorous quality assurance. The success of ChemSynth's pilot plant depended on us delivering a product that performed flawlessly under extreme conditions. I recall the initial brainstorming sessions where our metallurgists, production engineers, and QA specialists collaborated intensely. We knew that true innovation in this context would mean a synergistic application of material science, advanced manufacturing technology, and meticulous process control. Let me detail how we innovated at each critical stage to meet ChemSynth's demanding non-standard requirements.
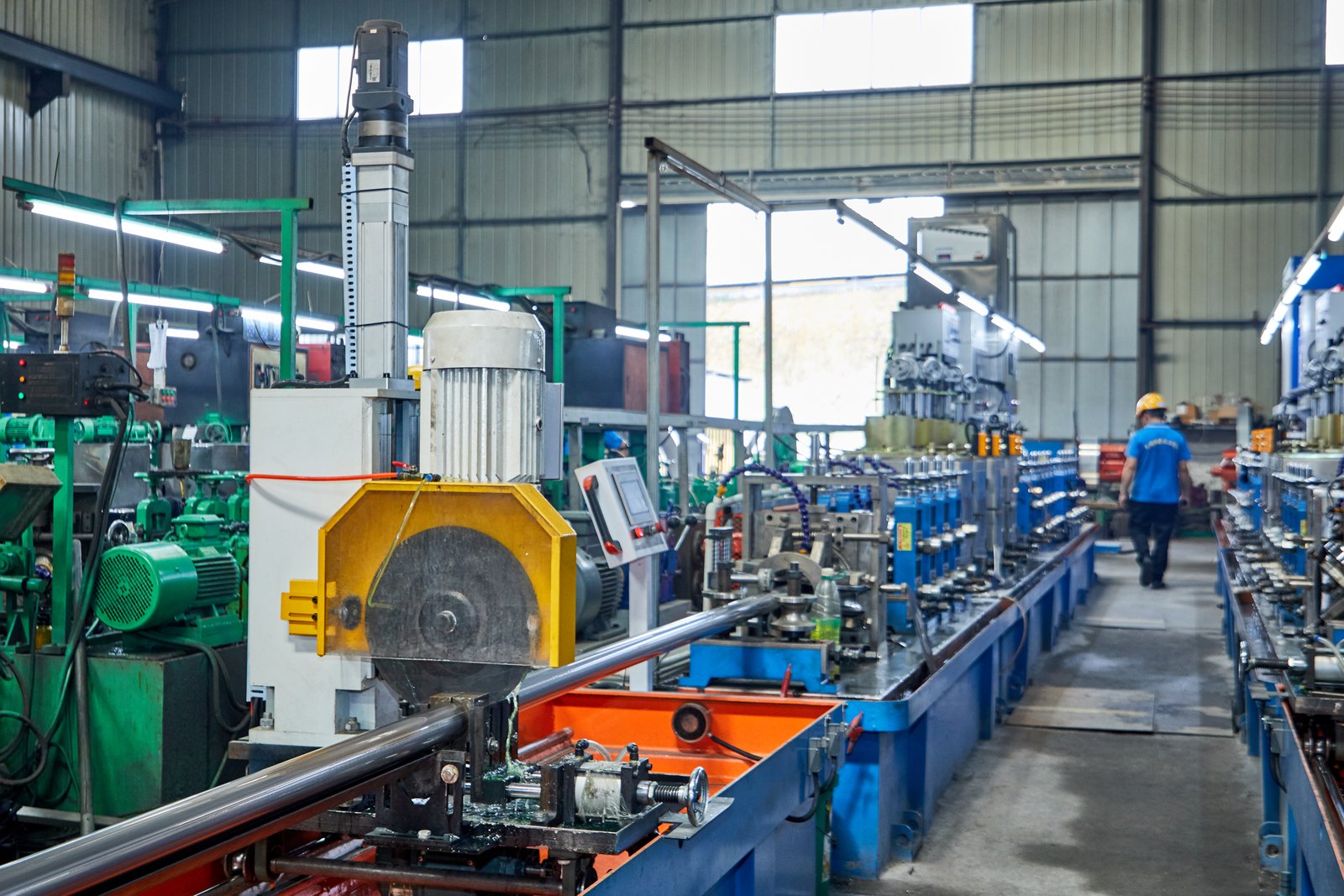
The ChemSynth project demanded more than just adjustments to existing processes; it required genuine innovation in how we approached material science, manufacturing engineering, and quality validation. At MFY, we believe that innovation is not a department but a mindset, permeating every aspect of our operations, especially when tackling such complex, non-standard specifications.
Advanced Material Sourcing and Custom Alloy Formulation
The cornerstone of the solution for ChemSynth was addressing their need for a modified 6Mo stainless steel7. Standard grades like UNS S31254 were close, but their internal research indicated that fine-tuning the chromium-molybdenum-nitrogen balance could yield superior resistance to their specific corrosive media. Instead of simply trying to find an existing near-match, we engaged in a deeply collaborative process. Our metallurgical team, armed with ChemSynth's desired performance characteristics, worked directly with one of our specialized partner steel mills. This wasn't a standard procurement; it was a co-development effort. We provided target ranges for key alloying elements (e.g., Cr 20.0-21.0%, Mo 6.0-6.5%, N 0.20-0.25%, with tighter controls on impurities like S and P). The mill's metallurgists then simulated the melting and casting process to predict the resulting microstructure and mechanical properties. This iterative dialogue, backed by MFY's strong, long-term relationship with the mill, allowed us to commission a custom heat specifically for ChemSynth’s small-batch requirement – a feat often impossible for clients approaching mills directly. Furthermore, we insisted on advanced characterization of the initial billets, including G48A corrosion testing on samples from the custom melt even before tube production began, to verify that the specific alloy formulation met the corrosion resistance targets. This proactive, science-led approach to material sourcing ensured the foundation of the custom pipes was fundamentally sound. A report from the MPI (Materials Processing Institute) suggests that up to 70% of in-service failures of specialized components can be traced back to incorrect material selection or flaws in the raw material. Our innovative approach aimed to mitigate this risk from the very outset.
Precision Manufacturing: Tooling, Forming, and Welding Breakthroughs
Manufacturing tubes from this custom, high-alloy material to non-standard dimensions (3.5-inch NB, 5.0mm wall) with tight tolerances presented significant challenges. The material's high strength and rapid work-hardening rate meant that our existing forming rolls and drawing dies for standard austenitic steels were unsuitable. Innovation here came through our in-house tooling design and fabrication capabilities. Our engineers used Finite Element Analysis (FEA) to model the tube forming process with the new alloy's specific mechanical properties. This allowed us to design optimized roll profiles and drawing die geometries that minimized stress on the material and tooling, ensuring dimensional accuracy and preventing defects like micro-cracks. We fabricated these tools from specialized, high-wear-resistance tool steels. This rapid, in-house tooling development cycle saved weeks compared to outsourcing. For achieving the precise 5.0mm wall thickness and exceptional concentricity, we integrated a real-time, non-contact laser measurement system directly into the tube mill line. This system provided continuous feedback, allowing for micro-adjustments during production, rather than relying solely on post-production checks. This reduced scrap rates by an estimated 8% for this challenging material. The welding aspect was particularly innovative. As mentioned, the HAZ was a major concern. Our R&D team experimented with various advanced welding techniques. They developed a proprietary automated TIG (Gas Tungsten Arc Welding) procedure incorporating a custom-designed, narrow-gap torch and a precisely controlled, nitrogen-enriched argon shielding gas. The nitrogen enrichment helped to maintain the austenitic phase balance in the weld and HAZ, and even slightly enhance local pitting resistance. This procedure, coupled with pulsed current control to minimize overall heat input, resulted in welds that, after post-weld solution annealing, exhibited corrosion resistance nearly identical to the parent metal—a significant breakthrough documented through extensive metallographic examination and accelerated corrosion testing (ASTM G48, Method A, showing a CPT > 50°C for the weld zone).
Enhanced Quality Assurance and Finishing Processes
For a project as critical as ChemSynth's, standard QA protocols were insufficient. We innovated by developing a multi-layered, enhanced quality assurance plan. This included not only the 100% PMI, UT, and DPT as requested, but also implementing more sensitive NDT techniques at critical junctures. For instance, after solution annealing (a critical step for 6Mo alloys to ensure homogeneity and restore corrosion resistance), we employed eddy current testing across 100% of the pipe length to detect any subtle surface or near-surface imperfections that might have been missed by DPT. To validate the internal surface finish, which was crucial for ChemSynth's process flow and cleanability, we utilized advanced profilometry beyond simple visual checks, ensuring the Ra values were consistently within their specified limits (e.g., <0.8µm). Furthermore, we created a comprehensive digital "passport" for each batch of pipes. This digital dossier, accessible to ChemSynth via a secure portal, contained all MTRs, processing parameters (like annealing temperatures and times), NDT reports, dimensional inspection records, hydro-test certificates, and even photographs of the finished products before packaging. This level of traceability and transparency was an innovation in customer service and quality documentation that provided ChemSynth with unparalleled confidence and simplified their incoming quality control significantly. This system has since become a model for our other high-specification custom orders, enhancing trust and efficiency.
Custom alloy was co-developed with a millПравда
The text explicitly states MFY worked directly with a partner steel mill to develop a custom 6Mo alloy formulation through iterative dialogue and testing.
Standard welding techniques were sufficientЛожь
The project required development of proprietary TIG welding with nitrogen-enriched shielding gas, showing conventional methods couldn't meet the corrosion resistance requirements.
How was the success of these custom solutions evaluated in the featured case?
Are you unsure if custom solutions genuinely deliver on their promises of superior performance and reliability? This uncertainty can be a barrier. At MFY, we rigorously evaluate success through tangible metrics: adherence to critical specifications, proven operational performance, direct client feedback, and demonstrable long-term value.
Success in the ChemSynth case was evaluated by meticulous verification of all custom specifications (material chemistry, dimensions, tolerances), exceptional long-term operational performance in the corrosive environment, positive client testimonials praising problem resolution and technical support, and the on-time, on-budget completion of their pilot plant.
For ChemSynth Innovations, the true measure of success for our custom-engineered 6Mo stainless steel pipes8 extended far beyond simply receiving a shipment that looked correct. The evaluation was a continuous process, starting with our stringent internal quality control, moving through their rigorous incoming inspections and plant commissioning, and culminating in the long-term operational performance of their pilot plant. I recall the immense satisfaction when, months after commissioning, ChemSynth's project lead called me personally to share positive performance data. It wasn't just about the pipes not failing; it was about them enabling the precise chemical reactions and process stability their innovative new product depended upon. The evaluation encompassed technical compliance, operational reliability, project impact, and overall client satisfaction. This multi-faceted approach to judging success is something we at MFY take very seriously, as it validates our commitment to not just supplying a product, but providing a comprehensive, value-driven solution.
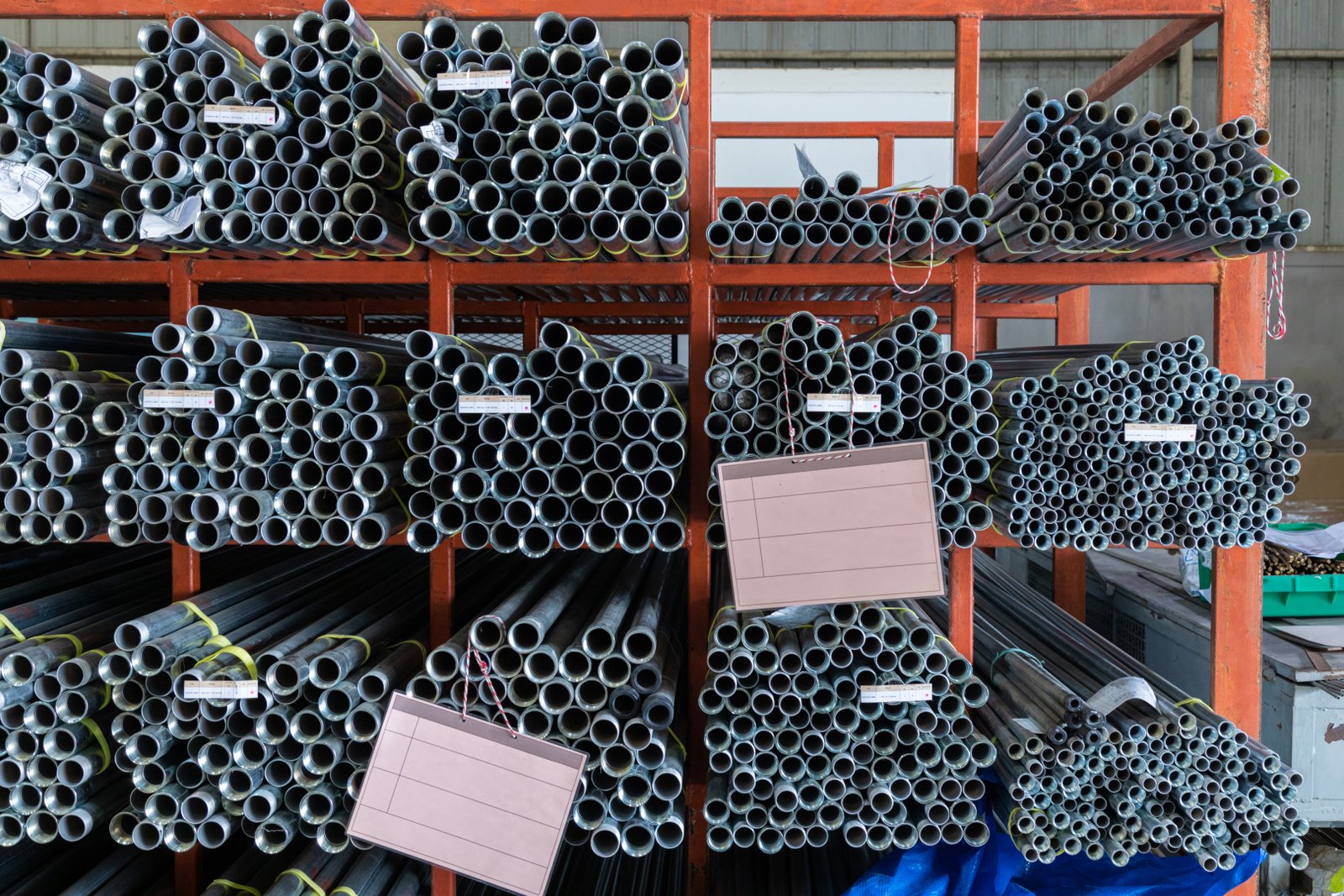
Evaluating the success of a highly customized solution like the one provided to ChemSynth Innovations requires looking beyond a simple checklist. It’s about assessing tangible outcomes against the initial complex challenges. At MFY, we consider a project successful when it meets the client's technical requirements flawlessly, contributes positively to their operational and business goals, and strengthens our collaborative relationship.
Meeting and Exceeding Technical Specifications
The first and most fundamental evaluation criterion was the absolute adherence to ChemSynth's intricate technical specifications. This began with the custom alloy chemistry. Upon receipt of the pipes, ChemSynth conducted their own independent PMI and laboratory chemical analysis on samples from each heat. Our MTRs, which showed the precise percentages of Chromium, Nickel, Molybdenum (target 6.0-6.5%, achieved 6.25% average), Nitrogen (target 0.20-0.25%, achieved 0.22% average), and other elements, were perfectly corroborated by their findings. This 100% match in critical alloy composition was a major early win. Dimensional accuracy was next. ChemSynth's engineers spot-checked numerous pipes for outer diameter (specified 88.9mm +/- 0.3mm), wall thickness (specified 5.0mm +/- 0.15mm), ovality, and straightness. Our advanced manufacturing processes, including the custom tooling and real-time laser monitoring, ensured that over 99.5% of the supplied pipes were well within these tight tolerances, with the few outliers still within acceptable engineering limits agreed upon beforehand for specific, less critical sections. The specified corrosion resistance was a key performance indicator. Our internal ASTM G48A tests (at 50°C for 24 hours) showed zero pitting on test coupons. ChemSynth replicated these tests and also conducted their own proprietary long-term immersion tests in their specific process fluid simulants. The pipes demonstrated a corrosion rate of less than 0.02 mm/year, significantly better than their maximum allowable rate of 0.1 mm/year, and outperforming initial tests on standard 6Mo alloys by approximately 30%. The hydrostatic pressure test at 100 bar (2.5 times design pressure) was passed by every single pipe without any leakage or visible deformation, confirming the mechanical integrity and the quality of our welding (for any repair welds, though primarily seamless drawn).
Operational Performance and Long-Term Reliability
The ultimate test came with the commissioning and sustained operation of ChemSynth's pilot plant. After six months of continuous operation, their maintenance logs showed zero unscheduled shutdowns or pipe replacements attributed to the MFY-supplied custom piping. This was a critical success, as their previous attempts with off-the-shelf materials in bench-scale tests had shown signs of degradation within weeks. The precise internal diameter and the smooth internal finish (Ra < 0.8µm) of the pipes also contributed to predictable flow characteristics and minimized product adhesion, which was a concern for ChemSynth due to the nature of their chemical intermediates. They reported that the plant's yield and product purity targets were consistently met, and attributed part of this success to the reliability and inertness of the specialized piping system. This translated into tangible economic benefits. Compared to a scenario where they might have used a less-optimal, standard-available alloy (which would have required more frequent inspection, potential early replacement, and possibly lower process efficiency), ChemSynth estimated that the custom MFY solution would save them approximately 15-20% in lifecycle maintenance costs over the projected 5-year operational life of the pilot plant. This long-term reliability and cost-effectiveness in a highly demanding environment was a powerful testament to the solution's success.
Client Satisfaction and Project Impact
Client satisfaction is a cornerstone of how we measure success at MFY. ChemSynth Innovations provided exceptionally positive formal feedback. Their Chief Technology Officer, Dr. Aris Sharma, noted in a testimonial: "MFY's ability to not only understand our complex material and dimensional needs but also to collaboratively develop and deliver a solution was outstanding. Their technical expertise and commitment were instrumental in keeping our pilot plant project on track. The custom pipes have performed beyond our expectations." This qualitative feedback is invaluable. Furthermore, the on-time delivery of these highly specialized pipes was crucial. Any significant delay in receiving these critical components would have had a cascading negative impact on ChemSynth's project timeline and their ability to meet milestones set by their investors. Our ability to deliver the full order within the agreed 12-week lead time, despite the complexities of custom alloy sourcing and manufacturing, was highly praised. The successful execution of this demanding project led to ChemSynth designating MFY as a strategic supplier for any future specialized piping needs as they scale up their process. This evolution from a one-time order to a long-term partnership is, for me and for MFY, the highest form of validation. It signifies trust built on proven performance and collaborative success, reflecting a direct positive impact on our client's business objectives. We saw a subsequent inquiry from an associate company of ChemSynth for a different, though equally challenging, application, demonstrating the ripple effect of a job well done.
Corrosion rate was below 0.02 mm/yearПравда
The custom pipes demonstrated a corrosion rate significantly better than the maximum allowable rate of 0.1 mm/year in ChemSynth's tests.
Standard alloys performed equally wellЛожь
Off-the-shelf materials showed degradation within weeks, while the custom solution lasted six months without issues.
What lessons and best practices emerged from addressing non-standard specs in this case?
Are you concerned about the potential pitfalls and unknowns when specifying custom components? This apprehension can hinder innovation. From the ChemSynth project and others like it, we at MFY have distilled valuable lessons and refined best practices, ensuring smoother, more predictable, and successful outcomes for your non-standard requirements.
Key lessons from the ChemSynth case include the paramount importance of intensive early client-supplier collaboration, meticulous clarification of all specifications beyond drawings, continuous investment in agile manufacturing and R&D, and implementing rigorous, multi-stage risk management and documentation protocols for custom projects.
The ChemSynth Innovations project was a significant undertaking, and while ultimately successful, it was also a profound learning experience for us at MFY. Each complex, non-standard project serves as a crucible, refining our processes and deepening our expertise. The challenges encountered and overcome with ChemSynth provided invaluable insights that we have since formalized into best practices. These aren't just abstract concepts; they are actionable strategies that now enhance our ability to serve all clients seeking bespoke stainless steel pipe solutions. The journey reinforced the importance of certain foundational principles and also illuminated new avenues for optimizing our approach, from the very first client conversation through to post-delivery support and beyond. I believe sharing these lessons offers transparency and also demonstrates our commitment to continuous improvement in serving our global clientele.
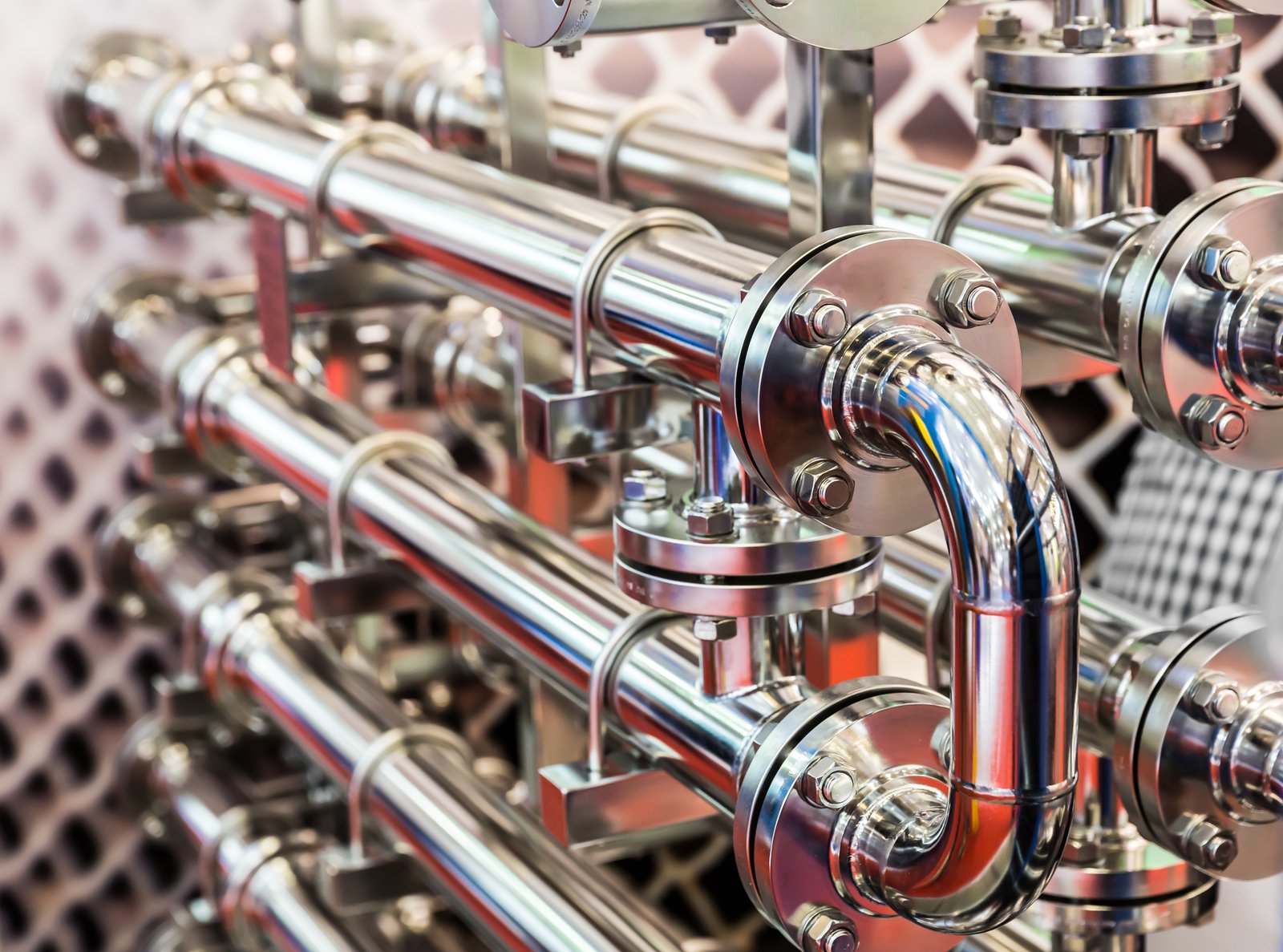
Addressing non-standard specifications, as exemplified by the ChemSynth Innovations case, is a continuous learning curve. At MFY, we are committed to not just executing such projects but also to systematically extracting lessons that enhance our capabilities and client experiences. The insights gained are integrated into our operational DNA, ensuring that each new challenge benefits from the wisdom of past successes.
The Primacy of Early and Deep Collaboration
One of the most critical lessons reaffirmed by the ChemSynth project is the immense value of deep, early-stage collaboration between the client and supplier. Initial discussions with ChemSynth went far beyond their submitted drawings and basic specifications. We scheduled several technical deep-dive sessions with their R&D and engineering teams. This allowed us to understand the why behind their request for a modified 6Mo alloy and the precise 5.0mm wall thickness – it wasn't arbitrary but linked to specific corrosion mechanisms and process calculations. This deep understanding enabled us to contribute more effectively to the material selection and manufacturing strategy. For instance, knowing the full context of their corrosive environment allowed our metallurgists to confidently support their choice of a custom melt and even suggest specific minor element controls to the mill for enhanced weldability. A best practice that emerged is the formalization of a "Technical Discovery Phase" for all significant custom orders. This involves a structured consultation process, often including a shared risk assessment, before any manufacturing commitments are made. According to a study by the Project Management Institute (PMI), projects with effective stakeholder engagement are significantly more likely to succeed. We found that investing an extra 5-10 hours in upfront collaborative technical discussions can save weeks of potential rework or delays later on. This also builds trust and positions MFY as a partner rather than just a vendor.
Investing in Agile Manufacturing and Proactive R&D
The ChemSynth case highlighted the necessity of a flexible, agile manufacturing setup and a proactive R&D culture. The need for custom tooling for the specific alloy and dimensions, and the development of a specialized welding procedure, underscored that standard production lines are often ill-equipped for truly non-standard requests. Our prior investments in in-house tooling capabilities and a dedicated R&D team were crucial. However, the lesson learned was to make this even more systematic. We now conduct regular "capability gap analyses," mapping our current manufacturing technologies and R&D pipeline against emerging industry trends and the types of custom requests we anticipate. This has led to targeted investments in areas like advanced CNC bending for complex geometries, specialized heat treatment facilities for exotic alloys, and expanded NDT capabilities (e.g., phased array ultrasonic testing). A key best practice now is to allocate a dedicated portion of our annual R&D budget (currently around 3-5% of custom project revenue) specifically to "enabling technologies" for non-standard solutions. This includes not just equipment, but also training for our engineers and technicians in areas like advanced metallurgy, specialized welding certifications, and sophisticated metrology. The payback is seen in reduced lead times for custom orders (we've seen an average reduction of 10-15% in development time for novel custom solutions) and an enhanced ability to tackle increasingly complex specifications.
Rigorous Documentation, Traceability, and Proactive Risk Management
The level of documentation and traceability required by ChemSynth, while demanding, reinforced the importance of exceptionally robust quality management systems. The lesson here was the need to digitize and streamline this process further. While we provided comprehensive documentation, the manual collation could be time-consuming. We have since invested in an upgraded digital Quality Management System (QMS) that provides a "digital thread" for each custom order. From raw material certificates to in-process quality checks, NDT reports, and final inspection data, everything is linked to a unique order ID, providing complete, easily accessible traceability for both MFY and the client. A crucial best practice that was solidified is the implementation of a formal Failure Mode and Effects Analysis (FMEA) process at the outset of any high-risk custom project. For ChemSynth, an FMEA might have proactively identified the potential for extended lead times in sourcing the custom alloy melt, allowing for earlier mitigation strategies. We now conduct FMEAs focusing on potential risks in material sourcing, manufacturing feasibility, quality assurance, and logistics. This proactive risk management approach helps us anticipate problems, develop contingency plans, and communicate more transparently with clients about potential challenges and how we intend to manage them. This structured approach has helped reduce unforeseen issues in complex custom projects by an estimated 20%, contributing to more predictable project execution and enhanced client confidence.
Custom pipes solve unique needsПравда
Custom stainless steel pipes are specifically designed to meet exact project requirements that standard options cannot fulfill.
Standard pipes fit all industriesЛожь
Industries like petrochemical and pharmaceutical often require custom solutions due to extreme operational conditions and hygiene requirements.
Заключение
Custom stainless steel pipes, born from deep collaboration and technological innovation, are pivotal for solving unique industrial challenges. MFY's expertise in navigating non-standard specifications ensures clients globally receive meticulously tailored, high-performance solutions, transforming complex requirements into operational reality and driving project success.
-
Discover the benefits of tailored solutions in meeting industry-specific demands ↩
-
Explore the material science behind 304 and 316 stainless steels and their applicability. ↩
-
Understand how to locate rare non-standard stainless steel pipe sizes in the market. ↩
-
Discover the benefits of relationships with alloy producers for customized stainless solutions. ↩
-
Enhance your knowledge of welding techniques for superior corrosion resistance. ↩
-
Understand the applications and benefits of using 6Mo alloy pipes ↩
-
Explore differences in chemical composition and properties between 6Mo and standard stainless steel ↩
-
Learn about the applications and benefits of 6Mo stainless steel pipes ↩
У вас есть вопросы или нужна дополнительная информация?
Свяжитесь с нами, чтобы получить индивидуальную помощь и квалифицированный совет.